ملخص
HDC stands as an adept provider of personalized metal components, boasting over a decade of mastery in tailoring metal solutions. Armed with sophisticated production facilities, encompassing 4-axis and 5-axis machining centers, as well as cutting-edge inspection tools like the coordinate measuring machine, HDC extends a diverse array of machining options, ranging from التصنيع باستخدام الحاسب الآلي, صب, تشكيل، و القطع بالليزر، ل ختم المعادن.
Immerse yourself in the intricacies of 6060 Aluminum Machining on our dedicated page, where we elucidate the diverse parameters and applications of this highly versatile material. Celebrated for its outstanding weldability, corrosion resistance, and flawless finishing attributes, 6060 Aluminum emerges as the favored choice in industries valuing precision and reliability. HDC excels in 6060 Aluminum machining, harnessing advanced technology and extensive experience to yield superior outcomes. Our steadfast commitment to quality and precision establishes HDC as the ideal collaborator for all your personalized metal component requirements.
Embark on an exploration of the HDC advantage – a convergence where innovation seamlessly melds with craftsmanship. Our proficiency in 6060 Aluminum machining assures bespoke solutions, perfectly attuned to your specifications and industry imperatives.
محتويات
- ملخص
- What Are the Series of Aluminum Alloys?
- Aluminum Alloys Are Classified Into Series Based on What Criteria?
- How Many Types of Aluminum Alloys Are There Today?
- The Invention Time and Place of Aluminum 6060
- What Are the Benefits of Aluminum 6060?
- The Price of Aluminum 6060
- Chemical Composition of Aluminum 6060
- The Influence of Various Elemental Compositions on the Properties of Aluminum 6060
- Mechanical properties of Aluminum 6060
- Physical Properties of Aluminum 6060
- Equivalent materials of Aluminum 6060
- The Main Application Fields of Aluminum 6060
What Are the Series of Aluminum Alloys?
Aluminum alloys are categorized into several series, each with distinct properties and applications:Aluminum alloys are categorized into several series, each with distinct properties and applications:
- 1xxx series: These alloys, almost pure aluminum, cannot withstand heat treatment. They have generally been used for the anti-corrosion and electrical conductivity.
- 2xxx series: These alloys are known for their superior strength and copper that being their main alloying element. They are typical in aviation industries.
- 3xxx series: This type of alloys predominantly have manganese and are not heat treatable. Good formability and corrosion resistance are the main features of this category.
- 4xxx series: These type alloys which contain silicon as the main alloying element are usually used as weld metal filler metal.
- 5xxx series: Magnesium is the main alloying element in the range of alloys presented in this series. They are very good at protecting themselves from corrosion especially in salt water.
- 6xxx series: These alloys mainly comprise of magnesium and silicon as the principal alloying elements. Heat treatable and often used in architectural and structural applications like the ones in buildings or bridges because they have good formability and weldability.
- 7xxx series: Regarded as having the most strength in them, these alloys have zinc as the main alloying element. They are extensively used in aviation and major structural systems.
- 8xxx series: These alloys are generally applied for specific purposes and the main ingredient frequently being lithium.
All the series come up with the wide spectrum of alloys designed impressively for diverse performance parameters in a variety of industrial applications.
Aluminum Alloys Are Classified Into Series Based on What Criteria?
Aluminum alloys are stratified into the series based on the elements present in the metal’s chemical composition, primary among them. The criteria for classification include:The criteria for classification include:
- Alloying Elements: The intermediate components of the alloy, namely, copper, magnesium, silicon, zinc, manganese, and lithium, dictate the attributes and qualities of the alloy.
- Properties and Applications: Alloy types each have specific parameters which make them suitable for specific uses. For example, it is possible to have an alloy in magnesium (5xxx series) that gives great resistance to corrosion and one in copper (2xxx series) that gives high strength.
- Heat Treatability: Some series, such as 6xxx and 7xxx chains, are heat- treatable and therefore are able to achieve additional strength and other mechanical characteristics through various heat treatment processes.
- Formability and Weldability: The ability to form and weld the alloy is affected by the addition of some alloying elements. It is one of the most important properties which relates to manufacturing.
Through the categorization of the aluminum alloy into different series based on these criteria, the work of the engineers, designers, and manufacturers is made easier by allowing them to select the most suitable alloy for their particular applications and performance requirements.
How Many Types of Aluminum Alloys Are There Today?
These days there is plenty of aluminum alloys available categorized in series by the main alloying elements which they consist. It is the series which range from 1xxx to 8xxx, and with each offering properties that are unique and suited for certain applications. However, it is difficult to provide the exact number considering the fact that the demand for aluminium alloys continue to rise as a result of constant development. The material is in use today in industries ranging from aerospace, automotive, construction, packaging, and electronics.
The Invention Time and Place of Aluminum 6060
Aluminum alloy 6061 was invented in 1935 by Alcoa (the Aluminum Company of America) in the United States. It was developed as a heat-treatable alloy with excellent mechanical properties, making it suitable for a wide range of applications in various industries.
What Are the Benefits of Aluminum 6060?
The 6061 aluminum alloy is a quantity of strength, machinability, corrosion resistance, weldability, and heat treatability, all of which enable it to be used in a variety of areas. First developed by Alcoa in 1935, it has super strength-to-weight ratio, meaning it is suitable in aircraft, automotive, and marine structural components. Its machining versatility makes it possible to produce intricate details and tolerances and it also provides resistance to corrosion in outdoor environments. This characteristic is useful also for easiness of welding and heat treatability which allows increase in flexibility of the fabrication processes, thus expanding the applications range between various consumer goods and industrial sectors.
The Price of Aluminum 6060
The price of aluminum alloy 6060 can change due to factors like market demand, which raw materials are available, what the production costs are, and geopolitical events that affect the overall global aluminum market. By March 2022, aluminum alloy 6060 price varied between $2,200 and $2,500 per metric ton. However, prices also go up and down then it is important to check the trends before determining the market price. Also prices may depend on such aluminum 6060 form as extrusions, sheets, or plates and on suppliers location and pricing policy.
التركيب الكيميائي للألمنيوم 6060
6060 aluminum, with good corrosion resistance, is widely used in the decorative industry, such as doors and windows, metal structures, interior design, metal frames, screws, and pipes, have an excellent anodizing response.
العنصر الكيميائي | % الحاضر |
المنغنيز (Mn) | 0.0 – 0.10 |
الحديد (Fe) | 0.10 – 0.30 |
المغنيسيوم (ملغ) | 0.35 – 0.50 |
السيليكون (Si) | 0.30 – 0.60 |
النحاس (Cu) | 0.0 – 0.10 |
الزنك (Zn) | 0.0 – 0.15 |
التيتانيوم (Ti) | 0.0 – 0.10 |
الكروم (Cr) | 0.0 – 0.05 |
أخرى (كل منها) | 0.0 – 0.05 |
أخرون (المجموع) | 0.0 – 0.15 |
الألومنيوم | 97.9 – 99.3 |
The Influence of Various Elemental Compositions on the Properties of Aluminum 6060
Mechanical properties of الألومنيوم 6060
كثافة [كجم/م³] | مدى الذوبان [° مئوية] | كهربائي الموصلية [ملي ثانية/م] | حراري الموصلية [و/م ك] | معامل التمدد الحراري 10-6/ك | معامل مرونة [ج ب س] |
2700 | 585-650 | 28-34 | 200-220 | 23.4 | ~70 |
الخصائص الفيزيائية لـ الألومنيوم 6060
Alloy designation and condition | 6060-O | 6060-T1 | 6060-T4 | 6060-T5 | 6060-T6 |
Density, g/cm³ | 2.7 | 2,7 | 2,7 | 2,7 | 2,7 |
Electric conductivity (% IACS) | - | 49,5 | 48 | 54 | 54 |
Specific electrical resistance (m/Wmm2) | - | 35 | 36 | 32 | 32 |
Thermal conductivity, W/m·K | - | 195 | 187 | 209 | 209 |
Specific heat capacity (kJ/kg·K) | 898 | 898 | 898 | 898 | 898 |
Liquidus temperature (°C) | 655 | 655 | 655 | 655 | 655 |
Solidus temperature (°C) | 610 | 610 | 610 | 610 | 610 |
Linear coefficient thermal expansion (CTE), 10-6/K | 23,4 | 23,4 | 23,4 | 23,4 | 23,4 |
Poisson’s number, ν | 0,33 | 0,33 | 0,33 | 0,33 | 0,33 |
Equivalent materials of الألومنيوم 6060
European | معيار | EN 573-3 |
Numeric (Chemical Symbols) | EN AW-6060 (AlMgSi) | |
الألمانية | معيار | DIN 1725-1; DIN EN 573-3 |
Designation (material number) | AlMgSi0,5 (3.3206); EN AW-6060 (AlMgSi) | |
نحن | معيار | ASTM B221 |
AA (UNS) | 6060 (UNS A96060) | |
Australian | معيار | AS 2848.1, AS/NZS 1734, AS/NZS 1865, AS/NZS 1866 |
Aluminium | 6060 | |
ايزو | معيار | ايزو 209 |
الألومنيوم | AW-6060 | |
Japanese | معيار | JIS H4000; JIS H4040 |
الألومنيوم | 6060 | |
Chinese | معيار | GB/T 3190; |
الألومنيوم | 6060 |
The Main Application Fields of Aluminum 6060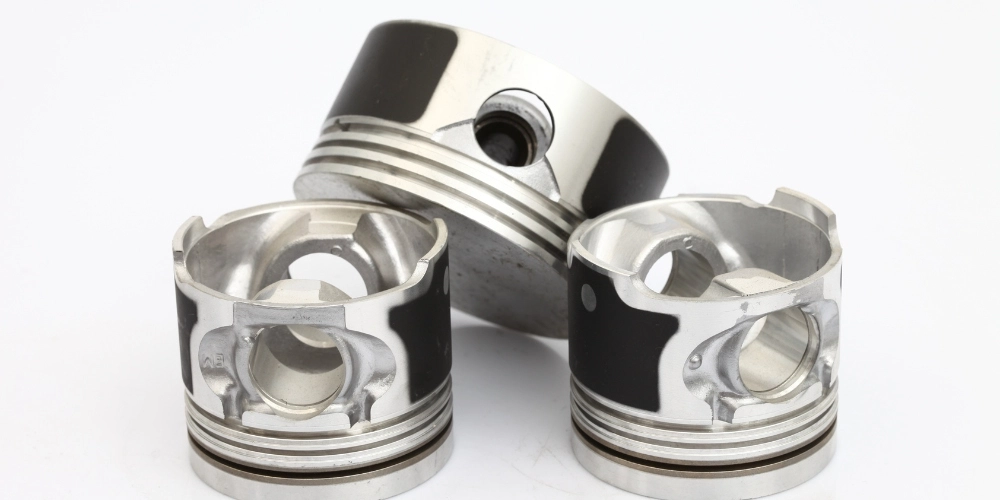
Alloy 6060 aluminum alloy is widely used in many different industries owing to its high versatility. It is used in construction of window frames and other building elements because of its strength and resistance to corrosion, and in cars it lightens body panels and the chassis parts, ensuring safety does not compromise fuel efficiency. This conductivity and low corrosion rate are the reason why it is so used in electronics. Also, its beauty and durability make it very much demanded in consumer goods like furniture, appliances and others. Another important application of this metal is industrial, where it is employed for its strength, machinability, and corrosion resistance, which allows for its wide use in automobiles, aerospace, rail components, and other manufacturing parts.