الكشف عن دور التحكم الرقمي بالكمبيوتر (CNC) في التصنيع الدقيق للأجهزة الطبية
استكشف الدور المحوري لتقنية التحكم الرقمي بالحاسوب (CNC) في الصناعات الطبية والدوائية. تتناول هذه المدونة كيفية تعزيز التصنيع باستخدام الحاسب الآلي لإنتاج قطع طبية عالية الدقة، وتناقش كل شيء بدءًا من أنواع القطع الطبية الدقيقة وعمليات إنتاجها وصولًا إلى المواد المستخدمة ومزاياها. تعرّف على فوائد وتحديات استخدام التحكم الرقمي بالحاسوب (CNC) في تصنيع المكونات الطبية الأساسية، واكتشف لماذا تُعدّ شركة HDC Manufacturing شركة رائدة موثوقة في هذا المجال عالي التخصص.
أهمية التحكم الرقمي بالكمبيوتر في الصناعة الطبية والدوائية
في الصناعة الطبية، هناك حاجة إلى تصنيع العديد من الأجزاء والمكونات بسرعة وبشكل عاجل، حتى بكميات صغيرة لأنها تستخدم في المستشفيات والعيادات المختلفة وغيرها من فروع التخصصات الطبية المختلفة.
بدون التصنيع باستخدام الحاسب الآلي، فإن إنتاج الأجزاء والمكونات الطبية والدوائية والصيدلانية سيستغرق وقتًا أطول، كما أنها معرضة لخطر عدم الدقة.
فهم الأجزاء الطبية الدقيقة
الأجزاء الطبية الدقيقة هي أي أجزاء طبية أو دوائية أو صيدلانية، وحتى أجزاء فضائية، يجب أن تكون دقيقة ومتقنة إلى درجة أن تتمتع بمستويات تحمل شبه مثالية. ويتم إنتاج هذه الأجزاء الطبية الدقيقة باستخدام مطاحن دقيقة بدلاً من آلات CNC التقليدية أو المطاحن القياسية.
في حال كنت لا تعلم، فإن الطحن الدقيق باستخدام الحاسب الآلي هو عملية تستخدم للقيام بعمليات القطع والطرح المتطورة للغاية باستخدام مطحنة CNC أو أداة القطع من أجل تحقيق الشكل والشكل والقياس والزوايا التي يرغب بها العميل.
أنواع الأجزاء الطبية الدقيقة
تشير الأجزاء الطبية الدقيقة إلى العديد من المكونات المهمة للأجهزة الطبية المختلفة. تم تصميم هذه المكونات بعناية وفقًا لأعلى معايير الجودة والدقة، وتلبية متطلبات السلامة الخاصة بالمعدات الطبية. يتضمن ذلك، من بين الأدوات الجراحية الأخرى، الأجهزة القابلة للزرع مثل غرسات العظام والأوعية الدموية. كما أنها تشمل أيضًا الأجهزة الدقيقة وأجزاء معدات التنفس ومكونات معدات طب الأسنان والأطراف الاصطناعية والأجهزة التقويمية بالإضافة إلى أدوات المختبر والبحث.
تُصنع هذه الأجزاء عالية الدقة من مواد مثل الفولاذ المقاوم للصدأ والتيتانيوم والبلاستيك من خلال عمليات تصنيع دقيقة مثل التصنيع باستخدام الحاسب الآلي أو الطباعة ثلاثية الأبعاد أو القولبة بالحقن. ولضمان موثوقية وسلامة هذه المكونات في التطبيقات الطبية، فإنها تخضع لإجراءات صارمة لمراقبة الجودة بالإضافة إلى اختبارات التوافق الحيوي. تعد الأجزاء الطبية الدقيقة ضرورية في صناعة الرعاية الصحية، بدءًا من الغرسات المنقذة للحياة إلى أدوات التشخيص المتطورة المستخدمة لتوفير رعاية طبية عالية الجودة.
تقنيات التصنيع المستخدمة في إنتاج الأجزاء الطبية الدقيقة
تستخدم صناعة المكونات الطبية الدقيقة عمليات تشغيل مختلفة لتحقيق التسامحات المطلوبة وتلبية متطلبات الجودة الصارمة للغاية. تتضمن التقنيات ذات الصلة التصنيع باستخدام الحاسب الآلي، وأتمتة الطحن، والتحويل والحفر؛ والتصنيع على الطريقة السويسرية للتفاصيل الدقيقة والحساسة؛ والتفريغ الكهربائي الذي يستخدم شرارة كهربائية على مواد مثل التيتانيوم أو الفولاذ المقاوم للصدأ. يتم استخدام القطع واللحام بالليزر لتشكيل المواد ذات التأثير الحراري المنخفض بينما يسمح الطحن بتشطيبات سطحية واضحة للأجزاء مثل الأدوات الجراحية يتم نشر تقنية EDM السلكية والتصنيع بالكهرباء الكيميائية للأشكال الهندسية المعقدة التي يصعب تصنيعها بالطرق التقليدية. علاوة على ذلك، تلبي الطباعة ثلاثية الأبعاد وقوالب الحقن احتياجات مخصصة للمكونات الطبية المصنوعة من البلاستيك الحراري في حين تعمل تقنيات التصنيع الدقيقة على تطوير أجزاء صغيرة باهتة.
يتم اختيار مثل هذه التقنيات التصنيعية مع الأخذ بعين الاعتبار الاحتياجات الخاصة للأجزاء الطبية الدقيقة والتي قد تشمل خصائص المواد والتسامحات والتعقيد الأبعادي والكمية المراد إنتاجها. وتضمن هذه التقنيات مجتمعة تصنيعًا موثوقًا به للمكونات الطبية عالية الجودة والتي تعد ضرورية لتطبيقات الرعاية الصحية.
عملية إنتاج الأجزاء الطبية الدقيقة
غالبًا ما تتضمن عملية تصنيع الأجزاء الطبية الدقيقة استخدام مطحنة CNC عالية الدقة، وهي لا تختلف كثيرًا عن طريقة تصنيعها وتنفيذها باستخدام المطاحن CNC التقليدية. لمساعدتك، إليك لمحة موجزة عن كيفية تصنيعها، وشرحًا سريعًا وسهلًا لخطوات تصنيع الأجزاء الطبية الدقيقة.
- يتم الحصول على المواد وتوريدها من قبل الشركة المصنعة / المورد.
- بعد ذلك، يجب برمجة الماكينة التي سيتم استخدامها على البرنامج أو النمط المحدد المطلوب لإنشاء الجزء الدقيق.
- بعد ذلك، سيتم تحميل المواد على آلة CNC الدقيقة.
- يجب إجراء طريقة أو عملية تجريبية للاختبار لمعرفة ما إذا كانت تحتوي على البرنامج أو النمط المضمن.
- عندما تظهر نتائج إيجابية ودقيقة، تبدأ عملية الطحن الدقيق.
ملحوظة: عادةً، في نهاية تصنيع الأجزاء الطبية الدقيقة، يقوم مُقيِّم أو خبير بفحص دقيق لجودة الأجزاء والمكونات المُنتَجة للتأكد من توافقها مع مستوى التسامح المُحدَّد. وإلا، فسيتم إجراء تعديلات طفيفة على المكونات المُنتَجة.
المواد المستخدمة في الأجزاء الطبية الدقيقة
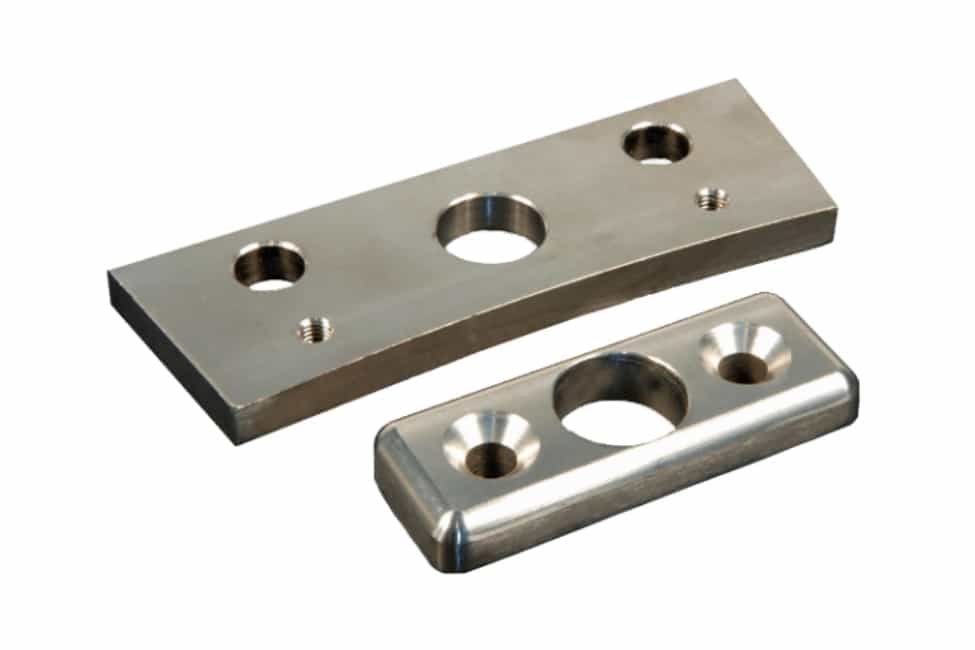
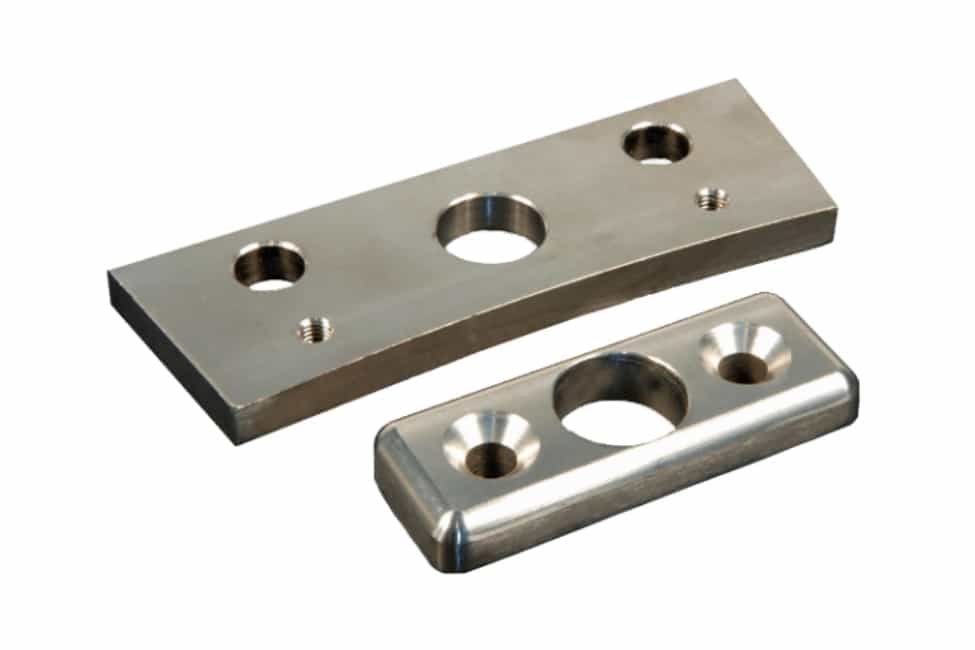
- أنواع مختلفة من السبائك
- الفولاذ المقاوم للصدأ
- الفولاذ الدقيق
- التيتانيوم
- نحاس
- سبائك متخصصة
- بولي فينيل كلوريد
- الأسيتال
- نظرة خاطفة
- نايلون
- مادة البولي تترافلورو إيثيلين
- مادة البولي ميثيل ميثا أكريلات
- و المزيد الكثير!
إيجابيات وسلبيات الأجزاء الطبية الدقيقة


- لا يتطلب أدوات ثابتة
- لا توجد قيود على الحجم
- آلات CNC مرنة وقابلة للحمل
- تتمتع آلات CNC بتسامحات محددة
- تكاليف أولية أعلى من المعتاد
- عملية التصنيع المعقدة والمعقدة
- مراقبة الجودة سيئة أو رديئة
المعادن مقابل البلاستيك في الأجزاء الطبية الدقيقة
والآن، بالنسبة لبعض الآلات والمعدات، فإن المعادن هي الأكثر استحسانًا بسبب موصليتها الحرارية وقوتها ومتانتها، بالإضافة إلى خصائصها الكهرومغناطيسية أيضًا.
لذا، إذا كنت بحاجة إلى الاختيار بين البلاستيك والمعادن، فحاول أن تأخذ في الاعتبار الاستخدام أو النتيجة النهائية التي تبحث عنها.
مصنع قطع الغيار الطبية الدقيقة الذي يمكنك الوثوق به تمامًا
على الرغم من أننا لسنا أطباء، إلا أن فريق المهندسين والمتخصصين لدينا هنا في HDC Manufacturing يدركون تمامًا مخاطر التصنيع والإنتاج غير الصحيح للأجزاء والمكونات والملحقات الطبية.
تلتزم شركة HDC Manufacturing بإنتاج أجزاء طبية دقيقة عالية الجودة دون دفع سعر باهظ عادةً.
في الواقع، أنتج خبراؤنا آلاف القطع الطبية الدقيقة من الألومنيوم والنحاس والمعادن غير القياسية، بالإضافة إلى مكونات بلاستيكية تُضاف إلى المعدات. خلال مسيرتنا في هذا المجال، لم نُخيب آمال عملائنا قط، بل كان العكس هو الصحيح دائمًا.
إذا كنت بحاجة إلى مصنع قطع غيار طبية دقيقة موثوق به، فإن HDC Manufacturing ستكون دائمًا في خدمتك. إلى جانب توفيرنا لقطع الغيار الطبية الدقيقة، نحن أيضًا الأفضل في خدمات القطع بالليزر، وتصنيع الصفائح المعدنية، بالإضافة إلى إنتاج... دراجة نارية CNC, السيارات، و أجزاء الدراجة، أيضاً!
تواصل معنا اليوم واحصل على تقدير سعر مجاني لجميع طلباتك قبل الغد. تمتع بالراحة التامة مع قطع الغيار الطبية الدقيقة، دون القلق بشأن مكان العثور عليها بعد الآن!
إرشادات حول قطع الغيار الطبية الدقيقة المخصصة من الشركات المصنعة
بهذا الترتيب عند البحث عن أجزاء طبية دقيقة مصنوعة حسب الطلب من الشركات المصنعة، قم أولاً بتحديد متطلباتك وتحديد الموردين المؤهلين الحاصلين على الاعتمادات المناسبة فقط ثم اطلب عرض أسعار تنافسي. تقييم المقترحات بسبب التكلفة ومدة التنفيذ بالإضافة إلى أداء الشركة المصنعة. تنفيذ ضمان الجودة، واتباع معايير الصناعة وتعزيز التواصل الواضح بين الأفراد المشاركين في المشروع. ينبغي أن يؤخذ في الاعتبار إنشاء النماذج الأولية للتحقق من صحتها، ويجب ضمان الامتثال التنظيمي. تحديد العقود؛ وإجراء عمليات تفتيش الجودة في وقت التسليم، وتقديم ردود الفعل من أجل التحسين المستمر إلى جانب السجلات الرائعة للوثائق التي سيتم استخدامها في التدقيق. وباستخدام هذا النهج المنظم، فإنه يضمن أن يتم الحصول على أجزاء طبية دقيقة عالية الجودة بناءً على المواصفات والمعايير التنظيمية.
خاتمة
في المجال الطبي، هناك حاجة إلى مثل هذه الأجزاء الدقيقة لزيادة دقة التعامل بشكل كبير والتي تتضمن تقنيات معينة تستخدم في التصنيع باستخدام الحاسب الآلي والتصنيع بالتفريغ الكهربائي. تتطلب هذه العناصر والمكونات الأساسية للأجهزة والغرسات ضوابط صارمة فيما يتعلق بالمسائل التنظيمية. في عملية الشراء، من المهم اختيار المواد والموردين المناسبين الذين يتوافقون مع معايير الجودة العالية. إن إنشاء نموذج أكثر تنظيماً، مع التواصل والتوثيق الدقيق، يتيح المشاريع التعاونية الناجحة فضلاً عن توافر مكونات الجودة لتسليمها إلى المستشفيات.