Copper is one of the most widely used metals in human history. Long before the industrial revolution, copper and its alloys provided a vital source of metal to humans for various day-to-day activities. Over time, humans learned to use Copper and Copper Alloys in different ways to fulfill their needs. With research and development, humans have overcome a number of shortcomings that were not identified earlier.
Nowadays, copper is extensively used in a number of industries including construction, electricity and power generation, electronics industry, and in making artificial jewelry. In this article, we will try and explore the various commercially available copper alloys and discuss the main properties of a few of the most common types.
Copper Alloys and Their Types
Like all other metallic alloys, copper alloys also base on the addition of different elements and metals to enhance the properties of copper. These materials usually include zinc, tin, nickel, silver, and aluminum. The quantities to be added to the copper also vary from 45% to 95% depending on the intended final copper alloy material required. In order to understand the properties of copper alloys, it’s important to have a look at the intrinsic properties of copper metal itself.
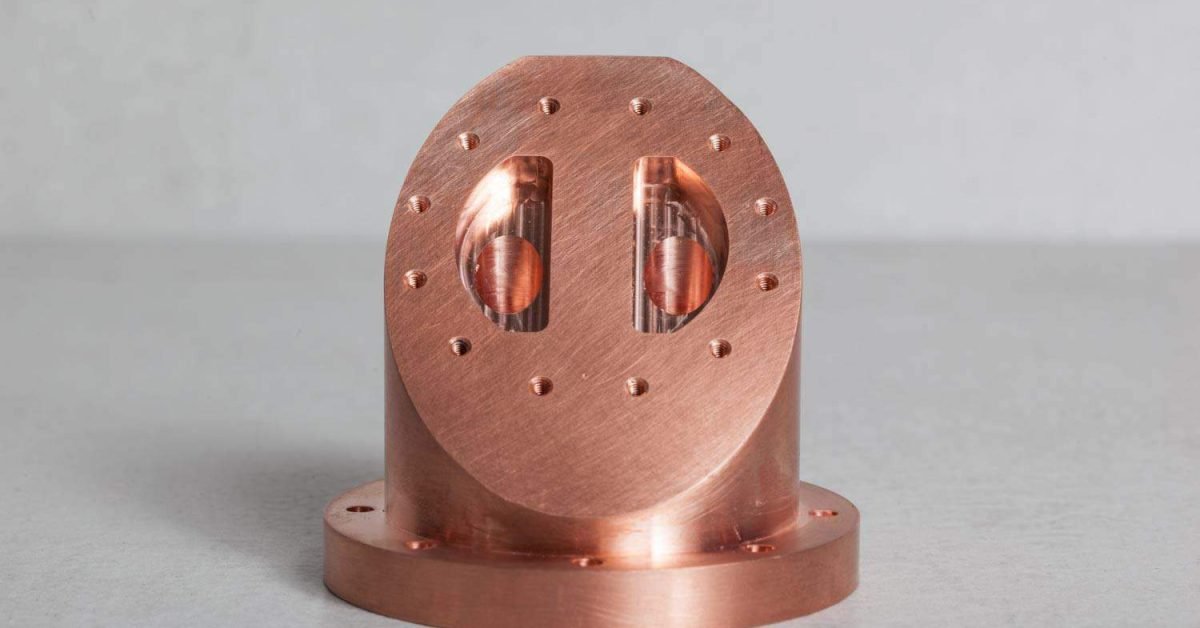
Properties of Copper
Copper displays a number of different physical and chemical properties as follows:
- الموصلية الكهربائية: Copper has a high conductivity and therefore is ideal for applications including wires, conducting elements, etc.
- الموصلية الحرارية: Due to the metallic composition, copper has a high thermal conductivity which makes it an ideal choice for cookware, heat exchange jackets, and other applications where heat has to be transferred.
- Ductility and Malleability: Copper can be easily stretched into wires and rolled into sheets without breaking. This makes Copper an ideal choice for wires and other manufacturing applications.
- Alloying Ability: Copper can form alloys with various metals as we have discussed in this article.
- Visually Appealing: Copper is visually appealing and is an ideal choice of use in the jewelry industry.
Common Types of Copper Alloys
1. نحاس (Copper and Zinc Alloy)
Brass is perhaps one of the most commonly used alloy of copper and zinc. Due to its appealing appearance, it is popular for making decorative applications. High corrosion resistance in brass makes it one of the best choices for plumbing fixtures, decorative items, valves, and marine applications. Various compositions exist of copper and zinc alloys based on the composition of copper and zinc in the final mix.
2. Bronze (Alloy of Copper and Tin)
Bronze is made from a mixture of Copper and Tin with Tin usually making 12% of the final composition of the product. Due to the addition of Tin, Copper becomes more resistant to corrosion and is able to withstand the onslaught of seawater. Therefore, bronze is ideal for utility in the marine industry and other areas that have a high risk of corrosion.
3. Copper-Nickel Alloy
Copper-Nickel alloys are composed of Nickel in the quantity of 10-30%, while the major composition consists of Copper. Like other copper alloys, this alloy serves as a wonderful option to fight corrosion. Due to the addition of Nickel, the alloy has an improved strength-to-weight ratio. This enables the copper alloy to be used in applications that are exposed to high pressure and physical wear and tear.
4. Silver-Copper Alloy
In the Silver-Copper Alloy, Silver is mixed in traces with the copper to make it a wonderful alloy for electricity conduction. Inherently, silver and copper both display properties of high conductivity on their own. However, when the two elements are mixed together, they display even stronger properties for conduction. The Silver-Copper Alloy is an ideal choice for electrical wires where low resistance is the purpose.
5. Copper Aluminum Alloy (Aluminum Bronze)
Copper-Aluminum Alloy or Aluminum Bronze comprises 4-12% of aluminum mixed with copper. The percentages of mixing vary based on the intended purpose of the final product. Since Aluminum and Copper display high resistance to corrosion as individual elements, their alloy also displays high performance in this area.
Since Aluminum has a high strength-to-weight ratio, its alloy with copper also displays the same property. Therefore, the Copper Aluminum Alloy is ideal for use in the manufacturing of gears, cogs, and other applications. Due to its lightweight, it is an ideal choice for aerospace applications.
6. Copper Iron Alloy
Iron is present in trace amounts in Copper-Iron Alloy. The small amount of Iron works best at enhancing the strength of the alloy. Due to the addition of Iron, the alloy has a higher strength and becomes ideal for use in the manufacturing industry. Particularly, the alloy is good at bearing weights and loads of higher strength with durability. Due to its properties, copper-iron alloy is used in high-stress environments.
7. Gold-Copper Alloy
Slight traces of Copper are mixed with Gold to make the Gold-Copper Alloy. Gold is majorly used for jewelry manufacturing, however, the addition of copper to Gold makes it more resistant to corrosion and long-lasting. As a result, Gold-Copper alloy preserves the beauty of the jewelry without impacting its aesthetics. Occasionally, the Gold-Copper Alloy is also used in decorative arts-work, electronic connectors, etc.
8. Copper Titanium Alloy
Copper and Titanium make a vital alloy that has excellent strength and hardness. Despite the high strength, the alloy does not lose its electrical and thermal conductivity. Since Titanium is a wonderful metal providing aesthetic appeal to the equipment and protecting it against corrosion, when mixed with Copper, it gives a very vital alloy. These alloys are usually used in automotive and aerospace industries.
9. Copper Steel Alloy
Copper-Steel alloys offer a range of benefits for the manufacturing industry. Ideal benefits include, but are not limited to, the building of bridges and transport infrastructure like roads, development of structural designs, etc. Steel itself allows for the strength that copper lacks. On the other hand, copper provides the protection against corrosion and rust that steel often lacks.
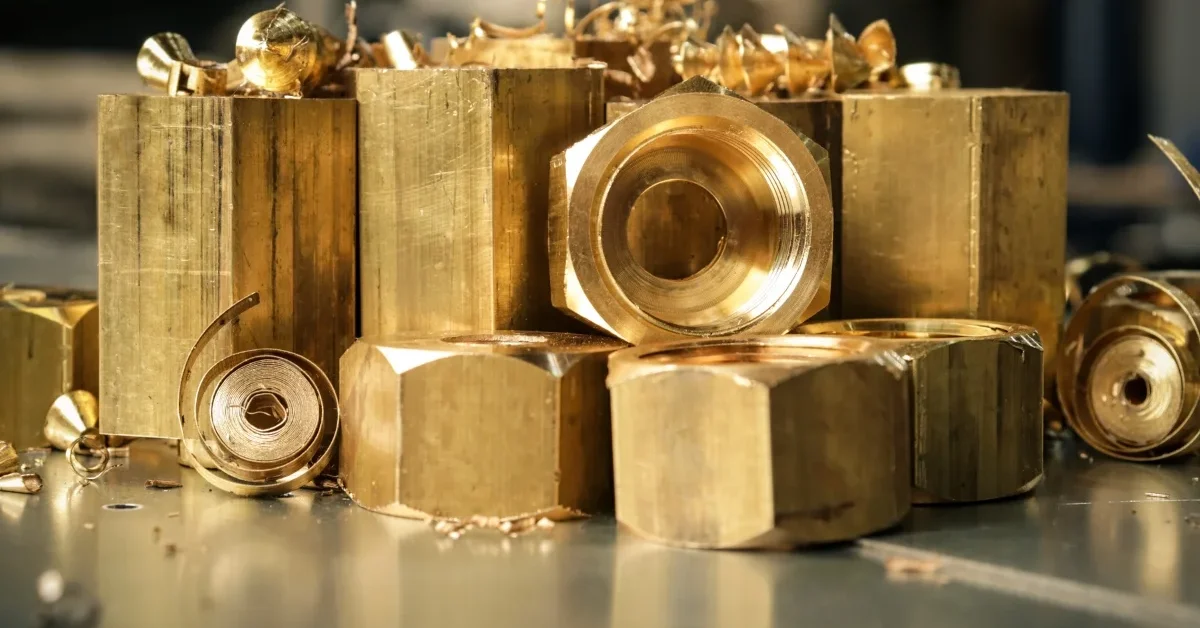
Industrial Applications of Copper Alloys
Although we have discussed the major applications of Copper Alloys while explaining the composition of the alloys, here is a brief description of major applications of the copper alloys in major industries:
- Plumbing Applications: Copper Alloyshave a lot of applications in the plumbing industry. As a result, Brass and Bronze are ideal choices when it comes to manufacturing valves, pipes, fittings, and other applications where water/moisture exposure is high.
- Electrical Wires and Electronics: Copper and its alloysare known for their low resistance and high conductivity. Therefore, copper alloys like silver-copper are ideal for making connectors, wires, and switches that allow for efficient operation of electrical systems.
- صناعة السيارات: Copper Alloyslike Copper-Nickel, Aluminum Bronze, etc., are ideal choices for making the heat exchangers in cars and vehicles. Due to the high thermal conductivity, these alloys serve as ideal choices for the automotive industry. Similarly, these alloys are used in heavy-duty components like gears and cogs that have to undergo stress during their lifetime.
- Marine and Aerospace: Marine and Aerospace are critical industries that require reliable material like Copper Alloys to perform well under high-pressure and corrosion-exposed environments. As such, bronze and copper-nickel are ideal to fend off the corrosion caused by seawater and brine. This makes it ideal for manufacturing propellers of sea ships, submarine parts, underwater pipes, etc. Similarly, the copper-titanium and aluminum bronze offer a high strength-to-weight ratio, making it ideal for choices and applications where weight is a concern. This makes such equipment ideal for uses in the aerospace and marine industry.
- Jewelry and Decorative Parts: Gold-Copperand Brass have been long used in the manufacturing of decorative equipment and arts-work. Also, the alloys make it more resistant to corrosion without affecting the aesthetics of the alloy.
Pros and Cons of Using Copper Alloys
الايجابيات | سلبيات |
High corrosion resistance | Can be costly depending on the alloy composition |
Excellent conductivity | Requires proper alloy selection for specific applications |
Recyclable and sustainable | Certain alloys may tarnish over time |
Versatile and durable | Fluctuations in copper price can affect cost |

Conclusion: Copper Alloys
Copper and its alloys are central to a variety of industries, offering unparalleled versatility in material performance. From the copper-zinc alloy known as brass to the alloy of copper and tin known as bronze, each type of copper alloy has unique properties that make it ideal for specialized uses. Copper alloys continue to play a crucial role in technological advancements and design innovations, proving that, even after thousands of years, copper remains one of humanity’s most valuable materials.
Whether you’re working in engineering, construction, or jewelry design, understanding the different copper alloy materials and their applications can help you make informed decisions that leverage these remarkable materials to their fullest potential.
اكتشف المزيد مع منشورات مدونتنا.
المشاركات الاخيرة
اكتشف المزيد عن منتجاتنا.
المنتجات ذات الصلة
اقتباس فوري!