Tabla de contenido
Visión general
La forja de metales, uno entre muchos procesos industriales, es un procedimiento convencional pero esencial que da forma al metal aplicando fuerzas de compresión, lo que a su vez proporciona componentes fuertes y duraderos. Sin embargo, todavía quedan algunas dificultades como la elección del material, el consumo de energía y la precisión. Aunque el camino de la forja de metales está lleno de tendencias como materiales avanzados, digitalización, sostenibilidad y personalización, parece muy prometedor.
Entendiendo la forja de metales
La forja de metales es un proceso de fabricación que implica dar forma al metal utilizando fuerzas de compresión localizadas. Es uno de los procesos metalúrgicos más antiguos conocidos, que se remonta a miles de años, y sigue siendo vital en la fabricación moderna para producir piezas con alta resistencia e integridad.
Ventajas y desventajas de la forja de metales.
La forja de metales, el método de dar forma al metal mediante su compresión, tiene múltiples beneficios esenciales. En primer lugar, mejora el rendimiento del metal, como resistencia, tenacidad y ductilidad, al refinar la microestructura y cerrar los huecos durante el proceso. Las propiedades superiores de las piezas forjadas las convierten en la opción preferida para aplicaciones críticas que se encuentran en maquinaria aeroespacial, automotriz e industrial, donde la confiabilidad y el rendimiento con un mayor valor de deformación son importantes. Vale la pena mencionar que en la forja es más probable que las piezas tengan una mejor textura superficial y precisión dimensional en comparación con otras técnicas de fabricación, lo que resulta en una reducción de la operación secundaria y el desperdicio de material.
Además de los beneficios de la forja de metales, también existen algunos inconvenientes a considerar. La maquinaria pesada y que consume mucha energía, que caracteriza este proceso, genera altos costos iniciales de puesta en marcha y operación. El costo de producción de la forja será demasiado alto para la producción pequeña y para aquellas piezas que pueden fabricarse de manera similar mediante procesos adecuados y menos costosos. Además, la gama de formas que se pueden forjar de manera eficiente es algo menor en comparación con procesos como la fundición o la fabricación aditiva que hacen que la fabricación de configuraciones más complicadas sea más costosa y requiera más tiempo.
El impacto de la forja en las propiedades de los materiales metálicos
Mediante la acción de la forja, las características físicas de los metales como la resistencia, entre otras, mejoran mucho mediante la perfección de sus estructuras de grano y la eliminación de defectos internos. Este proceso impone una tensión de compresión sobre los granos metálicos, generalmente a temperaturas elevadas, lo que alinea los granos, lo que da como resultado un mejor rendimiento y resistencia a la tracción, y materiales que tienen una mayor resistencia a la deformación y el desgaste. Son particularmente útiles para industrias donde se requiere alta confiabilidad en condiciones extremas, como en la industria aeroespacial y automotriz. Aunque el forjado proporciona el rendimiento óptimo del material en algunos parámetros, como la resistencia al desgaste y la vida a la fatiga, su eficacia se basa en el material, el método de forjado y el tratamiento posterior.
Proceso típico de forja de metales
- Selección de materiales: Dependiendo de las propiedades que debe tener la pieza terminada, elija un metal o aleación apropiado para la fundición.
- Calefacción: Calentar el metal hasta su temperatura dúctil sin sobrecalentarlo; Se requieren diferentes temperaturas según el tipo de metal.
- Forjar: Calentar el metal y utilizar los métodos de golpeo o prensado, subdivididos en forjado con matriz abierta o con matriz cerrada.
- Perforación/recorte: Para forjado con matriz cerrada, recorte el exceso de material (rebaba) para cumplir con las medidas y la forma especificadas.
- Operaciones secundarias: Realizar procesos adicionales de tratamiento térmico, mecanizado y acabado de superficies para mejorar las propiedades mecánicas y la precisión.
- Inspección y prueba: Preservar el hecho de que los componentes tengan las especificaciones y estándares de calidad correctos mediante controles dimensionales, inspección de superficies y pruebas mecánicas.
En términos generales, a través de este procedimiento se mencionan los principales pasos que van desde el metal en bruto hasta componentes de alta calidad y perfectamente formados mediante la forja.
Tipos de métodos de forja de metales
La forja de metales consta de varios métodos de conformación que se eligen según las necesidades de fabricación de un producto final en particular. En el proceso de forja con matriz abierta, el metal se moldea entre matrices simples, apropiadas para piezas grandes o simples, mientras que el proceso de forja con matriz cerrada implica presionar metal en cavidades de molde para piezas de formas complejas, donde se requiere alta precisión. Se producen anillos rodantes sin costura para componentes como rodamientos y engranajes. Las técnicas basadas en la temperatura incluyen forjado en frío para mejorar la resistencia y precisión a temperatura ambiente, forjado en caliente para lograr un equilibrio entre la complejidad de las formas y la fuerza necesaria, y forjado en caliente para formas complejas con una deformación más fácil. El propósito de la forja de precisión, por otro lado, es producir componentes con un acabado mínimo donde se necesitan procesos altamente controlados para tener dimensiones precisas. El método de elección depende del tamaño, la complejidad y las características deseadas del componente final, que ilustran la característica multitarea de la forja en metal.
Diferentes materiales utilizados en la forja de metales.
La forja de metales implica el uso de diferentes materiales que se eligen por sus propiedades únicas que son responsables de una amplia gama de opciones de aplicación.
- Aceros al carbono Son apreciados por su equilibrio entre resistencia y plasticidad, lo que los convierte en una solución económica para muchas aplicaciones.
- Aceros aleados tienen beneficios adicionales como mayor dureza y tenacidad adecuadas para necesidades de alto rendimiento.
- Aceros inoxidables Ofrecen resistencia a la corrosión y son los más adecuados para su uso en ambientes corrosivos.
- Aleaciones de aluminio tienen la ventaja de ser livianos y resistentes a la corrosión, lo que se adapta a las industrias aeroespacial y automotriz.
- Aleaciones de titanio, famosos por su brillante relación resistencia-peso, son adecuados para las industrias aeroespacial, médica y automotriz de alto rendimiento.
- Aleaciones de cobre, incluidos el latón y el bronce, son bien conocidos por su excelente conductividad y resistencia a la corrosión. Se utilizan en componentes eléctricos y de plomería.
- Aleaciones de níquel exhiben propiedades excepcionales de resistencia al calor y a la corrosión que son críticas para las aplicaciones de fabricación química y de ingeniería aeroespacial.
- Aleaciones de magnesio, al ser el metal estructural más ligero, se utilizan cuando es necesario reducir peso.
Seleccionar el material adecuado es un paso fundamental que se ve afectado por las propiedades esperadas, como la resistencia, la ductilidad y la resistencia a las condiciones ambientales.
Tipos de procesos de postratamiento de productos forjados
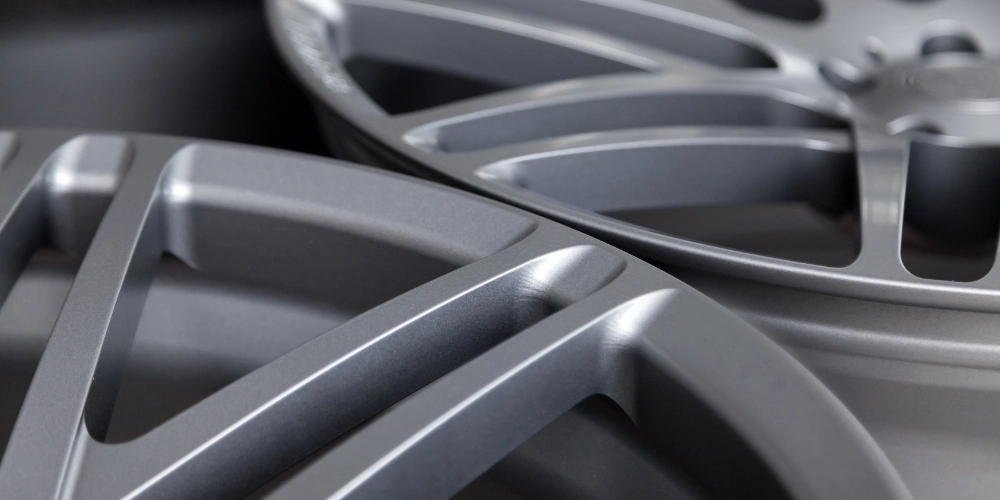
El impacto del tratamiento térmico en los productos forjados
El tratamiento térmico es indispensable porque el rendimiento y la vida útil de los productos forjados mejoran mediante la modificación de la microestructura mediante calor y enfriamiento con un control preciso del proceso. Mediante este tratamiento, el material gana resistencia a la tracción, dureza y tenacidad, siendo al mismo tiempo más dúctil y maleable, volviéndose así más fácil de trabajar y menos propenso a fallar. Destaca el relieve, lo que conlleva una menor aparición de deformaciones y defectos en la estructura. A continuación, el tratamiento térmico puede mejorar la resistencia a la corrosión y las propiedades de desgaste del material y puede personalizarse para adaptarse a los requisitos de necesidades particulares. A través del proceso de refinamiento de la microestructura, el tratamiento térmico garantiza el desgaste, el desgaste y la integridad estructural de los componentes necesarios para la aplicación específica.
La precisión que puede lograr la forja de metales
Generalmente se aplican forjado de precisión y matriz cerrada para lograr una mayor precisión posicional y requisitos de mecanizado minimizados. La forja con matriz cerrada es perfecta para fabricar piezas con detalles intrincados y tolerancias iguales a ±0,3 mm. Por otro lado, la forja con matriz abierta, aunque es menos precisa, aún puede crear formas más grandes y simples con una precisión razonable. Por ejemplo, el tipo de material utilizado y los tratamientos posteriores al procesamiento, como el mecanizado y el rectificado, que mejoran las dimensiones y las propiedades de la superficie, influyen en el nivel de precisión. Las mejoras tecnológicas, como prensas controladas por computadora y mejores materiales para troqueles, son algunas de las herramientas que se utilizan para mejorar la precisión del proceso de forjado. Por lo tanto, al utilizar estas herramientas, los componentes pueden ser consistentes y precisos. Esta característica la confiere la forja de metales porque tiene la capacidad de fabricar componentes resistentes y precisos que se utilizan ampliamente en muchas industrias.
Comparación entre forja de metales y otras técnicas de procesamiento de metales
La forja de metales, así como otras operaciones de trabajo de metales como fundición, mecanizado, fabricación, extrusión y pulvimetalurgia, son propias y todas tienen sus propias ventajas y aplicaciones. El proceso de forja consiste en formar piezas metálicas utilizando altas temperaturas y fuerza de compresión. Las formas producidas son fuertes, dúctiles y pueden resistir bien la fatiga. Si bien la fundición desarrolla formas complejas, tiene menor resistencia mecánica y defectos. El mecanizado puede proporcionar una precisión real, pero no puede mejorar las cualidades de los materiales tanto como lo hace la forja. Por otro lado, la fabricación es fiable para crear estructuras muy grandes pero debilita las uniones. La extrusión es buena en cuanto a forma recta y eficiencia; sin embargo, puede no tener las mismas propiedades mecánicas que la forja, y la metalurgia de polvos puede formar formas complejas pero puede sufrir de porosidad. La selección del proceso depende de propiedades como dimensiones, forma, carga mecánica y restricciones de costos.
Desafíos enfrentados en la forja de metales
La forja de metales, que se caracteriza por sus ventajas, tiene sus desafíos que los fabricantes deben tener en cuenta para que la producción sea exitosa. La selección de una calidad de material consistente, así como el control de calidad en cada paso, monitoreando las temperaturas durante todo el proceso y previniendo defectos, usando y manteniendo matrices y herramientas para formas complejas, optimizando el consumo de energía y el impacto ambiental y logrando precisión y consistencia en las operaciones de forjado. En este proceso se incluyen el control de calidad y la inspección de componentes forjados. Además de las operaciones posteriores a la forja, garantizar la seguridad de la mano de obra calificada y gestionar la cadena de suministro. Además, la solución del problema incluye innovación tecnológica, optimización de procesos, desarrollo de fuerza laboral capacitada y gestión de la cadena de suministro para garantizar el suministro de productos de calidad adecuada en muchos campos.
Tendencias futuras de la forja de metales
La forja de metales del futuro experimentará una evolución y la siguiente tendencia será el impulsor clave. Los materiales más recientes, como diferentes aleaciones y alternativas ligeras como el titanio, se utilizarán cada vez más para satisfacer las necesidades de todos los componentes de alto rendimiento. Los desarrollos de la digitalización y la Industria 4.0 aportarán eficacia y calidad gracias al monitoreo en tiempo real, el mantenimiento predictivo y los programas de producción bajo demanda. Una integración simultánea en vivo de las tecnologías de fabricación aditiva con el proceso de forjado tradicional hará posibles enfoques híbridos y, como resultado, se podrán producir formas complejas con menos desperdicio y tiempos de entrega más cortos. Sin embargo, existe una preocupación creciente con respecto a la sostenibilidad que debe abordarse mediante la introducción de procesos ecológicos y campañas de reciclaje que se esfuercen por reducir el efecto adverso sobre el medio ambiente.
Por otro lado, esta tendencia a la personalización también exige un sistema de fabricación mucho más flexible y eficiente que pueda producir lotes pequeños y/o piezas personalizadas a un coste competitivo. Las instalaciones de producción de forja inteligentes estarán equipadas con sensores, análisis de datos y gemelos digitales para maximizar la eficiencia del proceso, detectar fallas en los equipos y mejorar la tasa de producción. La mayor globalización hace que la resiliencia de la cadena de suministro sea vital, lo que a su vez crea asociaciones estratégicas y estrategias de abastecimiento diversificadas, así como herramientas digitales, como las de gestión de la cadena de suministro, que ayudan a reducir al mínimo los riesgos derivados de las interrupciones de la cadena de suministro. Abarcar estas tendencias permitirá a los talleres de forja mantener el ritmo de la competencia y de las necesidades cambiantes de los clientes, así como de las innovaciones de la industria.
Conclusión
La forja de metales, como base de la fabricación, también proporciona una indudable capacidad de resistencia y confiabilidad a los componentes en diferentes industrias. A pesar de los problemas, los avances en materiales, tecnología y sostenibilidad ofrecen esperanzas de un camino brillante. La adopción de estas tendencias continuará en la industria de la forja de metales, a la altura de las necesidades siempre cambiantes del sector manufacturero moderno.