Proceso avanzado de fundición a presión: clave para componentes de alta precisión
Descubra la precisión y versatilidad de la fundición a presión, una técnica de fabricación preferida que moldea metal fundido en piezas de alta calidad que se utilizan en diversas industrias. Este artículo destaca los procesos, beneficios y materiales asociados con la fundición a presión.
Entendiendo la fundición a presión
La fundición a presión representa una técnica de fabricación en la que se inyecta con fuerza metal fundido en un molde, creando componentes con formas meticulosas. Reconocida por su capacidad para producir diseños complejos con una precisión inigualable, la fundición a presión emerge como la opción preferida para las industrias que buscan una calidad de primer nivel en sus productos.
Ventajas de la fundición a presión
La prevalencia de la fundición a presión en diversas industrias se puede atribuir a una multitud de ventajas que aporta. Entre los beneficios fundamentales se encuentran:
- Alta precisión y exactitud dimensional:Permite la fabricación de componentes complejos con una precisión excepcional y tolerancias estrictas.
- Calidad de superficie superior:Genera superficies elegantes, minimizando la necesidad de procedimientos de acabado complementarios.
- Robustez y Longevidad: Produce componentes con atributos mecánicos elevados, ideales para aplicaciones con requisitos de rendimiento exigentes.
- Altas tasas de producción: Rápida producción de grandes cantidades debido a la rápida solidificación del metal fundido.
- Rentable para tiradas grandes: Rentable para la producción en masa una vez cubiertos los costos iniciales de herramientas y moldes.
- Opciones de aleación versátiles: Admite una amplia gama de aleaciones metálicas, lo que permite una selección de materiales personalizada.
- Reducción de residuos de materiales:La precisión minimiza el desperdicio de material, contribuyendo a beneficios ambientales y de costos.
- Consistencia y repetibilidad:Garantiza uniformidad y confiabilidad dentro de las tiradas de producción.
- Geometrías complejas: Adecuado para piezas intrincadas con formas y características complejas.
Tipos de fundición a presión
Los procesos de fundición a presión se clasifican principalmente en dos tipos: fundición a presión en cámara caliente y fundición a presión en cámara fría, que se distinguen por sus enfoques para fundir y transferir metal a la máquina de fundición a presión.
Fundición a presión en cámara caliente:
En la fundición a presión en cámara caliente, el sistema de inyección se sumerge en un baño de metal fundido. Este método se emplea comúnmente para aleaciones con puntos de fusión más bajos, como zinc, estaño y plomo. El mecanismo de inyección, o émbolo, se sumerge en metal fundido y, a medida que se retrae, el metal fundido ingresa a la cámara. Este proceso se caracteriza por su velocidad y es muy adecuado para componentes más pequeños que se benefician de tiempos de ciclo rápidos.
Fundición a presión en cámara fría:
La fundición a presión en cámara fría está diseñada para aleaciones con puntos de fusión más altos, incluidos aluminio, latón y magnesio. A diferencia de la fundición a presión en cámara caliente, el sistema de inyección en la fundición a presión en cámara fría es distinto del baño de metal fundido. El metal fundido se vierte en la cámara fría y luego se introduce en la cavidad del troquel bajo alta presión. Este método es particularmente ventajoso para piezas más grandes y complejas que requieren el uso de aleaciones de alto punto de fusión.
Fundición a presión frente a otros procesos de fundición
A continuación se muestra una comparación de la fundición a presión con otros procesos de fundición comunes:
Fundición a presión:
Ventajas: Alta precisión, acabado superficial superior, tiempos de ciclo más cortos, ideal para producción de gran volumen.
Contras: mayores costos de herramientas, opciones de aleaciones limitadas, menos flexibilidad para tiradas pequeñas.
Moldeo en arena:
Ventajas: Costos de herramientas más bajos, versátil para aleaciones y tamaños de piezas, adecuado para prototipos y producción de bajo volumen.
Desventajas: menor precisión, acabado superficial más rugoso, tiempos de ciclo más prolongados y mayor intensidad de mano de obra.
Ventajas: Excelente acabado superficial, buena precisión dimensional, adecuado para piezas complejas y detalladas.
Contras: tasas de producción más lentas, mayores costos de herramientas, menos rentable para la producción a gran escala.
Fundición por gravedad:
Ventajas: Costos de herramientas más bajos, adecuado para diversas aleaciones, bueno para producción de volumen medio a alto.
Desventajas: tasas de producción más lentas, menos precisión que la fundición a presión y pueden requerir acabados adicionales.
Fundición centrífuga:
Ventajas: Adecuado para piezas cilíndricas, buenas propiedades metalúrgicas, puede lograr una estructura densa.
Contras: Limitado a geometrías específicas, tiempos de ciclo más largos, menos preciso que la fundición a presión.
La elección entre fundición a presión y otros procesos de fundición depende de los requisitos específicos de la aplicación, incluidas las propiedades del material, la complejidad de las piezas, el volumen de producción y las restricciones presupuestarias. Cada método tiene sus ventajas y limitaciones, lo que los hace adecuados para diferentes escenarios de fabricación.
Materiales utilizados en la fundición a presión
La fundición a presión es un proceso versátil que puede adaptarse a varios materiales, pero ciertas aleaciones se usan más comúnmente debido a sus propiedades específicas y su idoneidad para el proceso de fundición a presión. Los materiales más comunes para la fundición a presión incluyen:
Aleaciones de aluminio:
Ampliamente utilizado por su baja densidad, alta relación resistencia-peso, resistencia a la corrosión y conductividad térmica.
Aleaciones comunes: A380, A383, A360, ADC12.
Aleaciones de zinc:
Popular para componentes más pequeños, ya que ofrece alta precisión, excelentes propiedades de fundición y buen acabado superficial.
Aleaciones comunes: Zamak 3, Zamak 5, Zamak 7.
Aleaciones de magnesio:
Se utiliza para componentes livianos que requieren alta resistencia, con ventajas como baja densidad y buena maquinabilidad.
Aleaciones comunes: AZ91D, AM60B.
Aleaciones de cobre
Aplicado en fundición a presión para una excelente conductividad y resistencia a la corrosión.
Aleaciones comunes: C87500, C95800.
Aleaciones de plomo y estaño:
Se utiliza en aplicaciones específicas donde los puntos de fusión bajos son ventajosos.
Los ejemplos incluyen aleaciones de Pb-Sn (plomo-estaño).
Explicación del proceso de fundición a presión
Aquí hay una descripción general del proceso de fundición a presión:
- Preparación del molde:Comience con un molde mecanizado con precisión, que consta de mitades fijas y móviles hechas de acero endurecido.
- Reprimición: Junte y sujete de forma segura las mitades del molde para mantener su posición durante la fundición.
- Inyección de Metal Fundido: Calentar metal fundido (aleaciones de aluminio, zinc o magnesio) en un horno. Inyecte el metal fundido en la cavidad del molde a alta presión.
- Solidificación: Solidifique rápidamente el metal fundido dentro del molde para que tome su forma. Controle el tiempo de enfriamiento para obtener las propiedades deseadas.
- Abriendo el molde:Abra las mitades del molde, expulsando la pieza fundida con la forma deseada.
- Recorte y acabado: Recorte el exceso de material (rebaba) y termine la pieza, agregando características si es necesario.
- Recuperación y Reciclaje:Recicle el exceso de material y bebederos para lograr sostenibilidad y eficiencia.
Postproceso para piezas de fundición a presión
Una vez finalizado el proceso de fundición a presión, con frecuencia se llevan a cabo pasos de posprocesamiento adicionales para cumplir requisitos particulares, mejorar la calidad del producto final y garantizar su alineación con las especificaciones deseadas. Los pasos de posprocesamiento para piezas de fundición a presión pueden incluir:
- Recorte y Desbarbado:Retire el exceso de material (“rebaba”) y alise los bordes ásperos creados durante el proceso de fundición.
- Mecanizado: Realizar adicionales molienda, taladrar o roscar para obtener dimensiones precisas o crear características específicas.
- Acabado de superficies:Mejore la apariencia y la resistencia a la corrosión mediante métodos como granallado, acabado vibratorio o galvanoplastia.
- Tratamiento térmico:Mejorar propiedades mecánicas como resistencia y dureza mediante procesos de tratamiento térmico.
- Inspeccion de calidad: Asegúrese de que las piezas fundidas cumplan con las tolerancias y los estándares de calidad especificados mediante controles dimensionales, inspecciones visuales y pruebas no destructivas.
- Asamblea:Une, suelda o fija piezas fundidas a presión con otros componentes para crear productos terminados.
- Revestimiento o pintura de superficies: Aplique revestimientos o pintura para darle color, textura o protección adicional contra factores ambientales.
Aplicaciones de la fundición a presión
- Electrónica de consumo: Carcasas y componentes estructurales para smartphones, portátiles, cámaras y equipos de audio.
- Accesorios:Partes de lavadoras, refrigeradores y hornos, artefactos de iluminación y portalámparas.
- Automotor:Componentes del motor, carcasas de transmisión y piezas del sistema de frenos.
- Equipo industrial:Cajas de cambios, carcasas de bombas y componentes de válvulas.
- Aeroespacial:Componentes de aeronaves, incluidas piezas de motores.
- Militar y Defensa:sistemas de armas y piezas de vehículos
- Artículos deportivos:componentes de bicicletas y palos de golf
- Telecomunicaciones
- Equipo medico
- Muebles
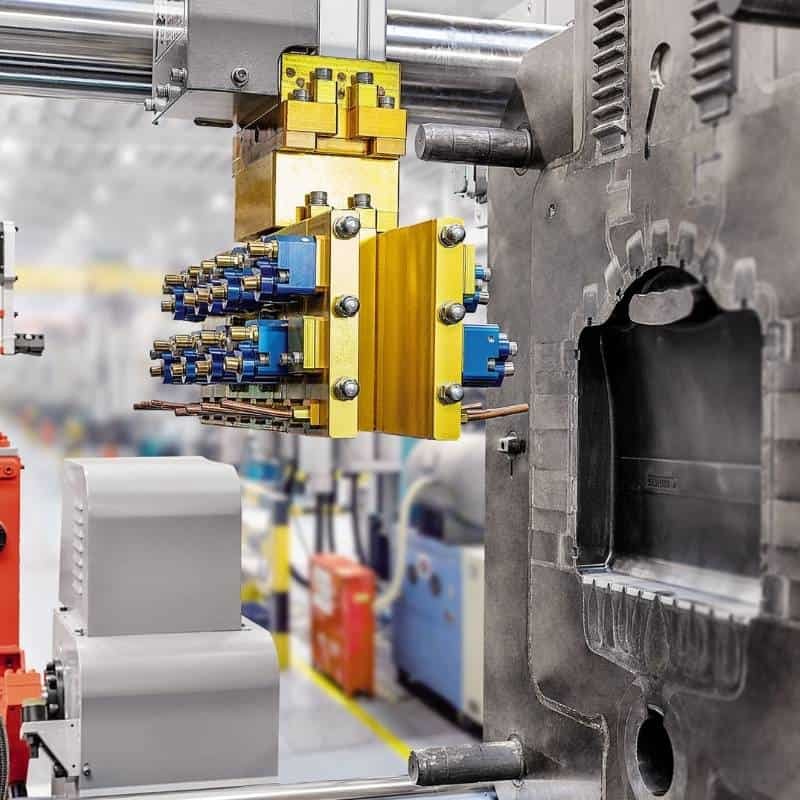
Innovaciones en tecnología de fundición a presión
En los últimos años, la tecnología de fundición a presión ha experimentado varias innovaciones destinadas a mejorar la eficiencia, la precisión, la sostenibilidad y ampliar la gama de aplicaciones. Algunas innovaciones notables en la tecnología de fundición a presión:
- Avances en la fundición a presión de alta presión (HPDC): Las mejoras continuas en las máquinas, mayores presiones de inyección, ciclos más rápidos y sistemas de control avanzados mejoran la eficiencia.
- Fundición a presión de pared delgada: Las innovaciones en herramientas y control de procesos permiten la producción de componentes de paredes más delgadas, cruciales para la reducción de peso en aplicaciones automotrices y aeroespaciales.
- Fundición a presión asistida por vacío:Reduce la porosidad al eliminar los gases antes de la solidificación, lo que mejora las propiedades mecánicas y el acabado superficial.
- Fundición a presión semisólida:Utiliza metal parcialmente solidificado para mejorar las propiedades mecánicas, especialmente beneficioso para aplicaciones que requieren resistencia y precisión.
- Materiales avanzados para troqueles: Los aceros y recubrimientos para herramientas de alto rendimiento mejoran la durabilidad de los troqueles, lo que reduce el mantenimiento y el tiempo de inactividad.
- Materiales y aleaciones avanzados: Las investigaciones en curso introducirán aleaciones con propiedades mejoradas para satisfacer las necesidades cambiantes de la industria.
- Monitoreo y control en tiempo real: La integración de sensores y sistemas de monitoreo optimiza la fundición a presión al garantizar una calidad constante de las piezas a través del control en tiempo real.
- Impresión 3D para herramientas de troquelado: Exploración de Impresión 3d para moldes intrincados y complejos, ofreciendo soluciones rentables para la producción de herramientas.
- Software de simulación: La simulación avanzada predice el flujo de metal fundido, identifica defectos y simula el ciclo de fabricación, lo que reduce la necesidad de prototipos físicos.
- Desarrollo de aleaciones: Las investigaciones en curso introducen nuevos materiales con propiedades mejoradas, incluida una mayor resistencia, resistencia al calor y reciclabilidad.
- Mejoras en la eficiencia energética: Las innovaciones en tecnologías de hornos energéticamente eficientes y prácticas sostenibles contribuyen a reducir el impacto ambiental de la fundición a presión.
- Robótica y Automatización:Un mayor uso de la robótica mejora la eficiencia, reduce los costos laborales y mejora la seguridad en tareas como la extracción de piezas, el recorte y el control de calidad.
- Personalización y producción en pequeños lotes:Evolucionando para dar cabida a procesos de producción más flexibles y ágiles para satisfacer las crecientes demandas de personalización.
Estas innovaciones contribuyen colectivamente a hacer de la fundición a presión un proceso de fabricación más versátil, preciso y sostenible. A medida que la tecnología continúa avanzando, se espera que nuevos desarrollos den forma al futuro de la fundición a presión en diversas industrias.
Impacto ambiental de la fundición a presión
El proceso de fundición a presión, como cualquier proceso de fabricación industrial, tiene implicaciones medioambientales. Si bien la fundición a presión ofrece ventajas en términos de eficiencia y utilización de materiales, también conlleva ciertas consideraciones medioambientales. Es importante señalar que los avances en la tecnología y las prácticas industriales, así como los marcos regulatorios, contribuyen a reducir el impacto ambiental de la fundición a presión. Muchas instalaciones de fundición a presión trabajan activamente para adoptar prácticas más sostenibles, como el uso de equipos energéticamente eficientes, la implementación de programas de reciclaje y el cumplimiento de estándares y certificaciones ambientales. A continuación se detallan algunos aspectos del impacto ambiental de la fundición a presión:
- Consumo de energía: Fundir metal en la fundición a presión requiere una energía sustancial, influenciada por factores como el tipo de aleación y la eficiencia del equipo.
- Emisiones:Las operaciones de los hornos pueden emitir contaminantes que contribuyen a la contaminación del aire, pero las instalaciones modernas emplean tecnologías para minimizar las emisiones y cumplir con las regulaciones.
- El consumo de agua: La fundición a presión implica cierto uso de agua para refrigeración, lo que requiere una gestión responsable para evitar el impacto ambiental.
- Generacion de residuos:La fundición a presión genera residuos, incluido exceso de material y piezas rechazadas.
- Uso químico: En la fundición a presión se utilizan lubricantes y agentes desmoldantes, y su elección y manipulación pueden afectar al medio ambiente si no se gestionan adecuadamente.
- Reciclabilidad: Los materiales de fundición a presión, como el aluminio y el zinc, son altamente reciclables, lo que respalda una economía circular y reduce el impacto ambiental.
Consejos para una fundición a presión de calidad
Garantizar la calidad en el proceso de fundición a presión es esencial para producir componentes fiables y precisos. Al incorporar los siguientes consejos, los fabricantes pueden mejorar la calidad de sus piezas de fundición, reducir los defectos y optimizar la eficiencia general de la producción:
- Diseño óptimo de herramientas: Invierta en herramientas de fundición a presión bien diseñadas para lograr una geometría de pieza precisa, reducir defectos y garantizar una refrigeración y ventilación uniformes.
- Selección de materiales: Elija aleaciones basadas en propiedades mecánicas, resistencia a la corrosión y conductividad térmica.
- Mantenimiento y lubricación de moldes: Inspeccione y mantenga periódicamente los moldes para evitar el desgaste. Aplique lubricantes de troquel adecuados para reducir la fricción, facilitar la liberación de piezas y contribuir a la longevidad del molde.
- Optimización de procesos: Ajuste los parámetros del proceso para la presión de inyección, la temperatura y el tiempo del ciclo para optimizar la calidad de las piezas y la eficiencia de la producción.
- Monitoreo en tiempo real:Implemente sistemas de monitoreo para rastrear parámetros clave del proceso, identificar problemas tempranamente y prevenir piezas defectuosas.
- Controles de control de calidad:Realice controles periódicos, incluidas inspecciones dimensionales, evaluaciones visuales y métodos de prueba, para cumplir con las tolerancias y los estándares de calidad especificados.
- Sistema de entrada optimizado: Diseñe un sistema de compuertas eficiente para controlar el flujo de metal, minimizando la turbulencia y reduciendo el riesgo de defectos.
- Capacitación y desarrollo de habilidades: Proporcionar capacitación adecuada a los operadores para mantener una calidad constante a través de personal capacitado y con conocimientos.
Piezas de fundición a presión personalizadas
Si está buscando obtener piezas de fundición a presión personalizadas de los fabricantes, aquí hay algunos pasos y consideraciones que lo guiarán a través del proceso:
- Especifique sus requisitos:Defina claramente sus necesidades, incluido el material, las dimensiones, el acabado de la superficie, la cantidad y cualquier característica o tolerancia específica.
- Fabricantes de investigación:Identifique fabricantes de fundición a presión acreditados con experiencia y certificaciones relevantes en las aleaciones y procesos que desee.
- Solicitar cotizaciones: envíe una solicitud de cotización (RFQ) detallada a los fabricantes elegidos, proporcionando detalles específicos del proyecto para obtener cotizaciones precisas.
- Evaluar cotizaciones: Revise las cotizaciones considerando costos, plazos de entrega, medidas de garantía de calidad y servicios adicionales.
- Evaluar capacidades: Evalúe las capacidades, la experiencia y el historial de cada fabricante en la producción de componentes similares.
- Seguro de calidad:Infórmese sobre los procesos de aseguramiento de la calidad y las certificaciones para garantizar el cumplimiento de los estándares de la industria.
- Visite las instalaciones (si es posible): Considere visitar las instalaciones de fabricación para evaluar de primera mano los equipos, los procesos y las capacidades generales.
- Comunicación: Establezca una comunicación clara, discuta los requisitos, los desafíos potenciales y garantice el entendimiento mutuo.
- Creación de prototipos:Solicite prototipos o muestras para evaluar la calidad y realizar ajustes antes de la producción a gran escala.
- Negociar términos: Negociar términos, incluidos precios, plazos de entrega, condiciones de pago y otros aspectos contractuales.
- Acuerdo contractual:Formalizar el acuerdo con un contrato, documentando especificaciones, cronogramas de entrega y estándares de calidad.
- Seguimiento de la producción: Manténgase involucrado durante toda la producción y reciba actualizaciones periódicas para solucionar cualquier problema con prontitud.
- Inspeccion de calidad:Realice inspecciones de calidad exhaustivas al recibir las piezas, incluidas comprobaciones dimensionales y evaluaciones visuales.
- Comentarios y mejoras: Proporcionar comentarios a los fabricantes para mejorar futuras colaboraciones y la mejora continua.
Si sigue estos pasos y mantiene una comunicación abierta con el fabricante elegido, puede mejorar la probabilidad de recibir piezas de fundición a presión personalizadas de alta calidad que cumplan con sus requisitos específicos.
Conclusión
La fundición a presión es una piedra angular de la fabricación moderna y ofrece precisión, eficiencia y durabilidad. Su impacto repercute en todas las industrias y da forma a los productos de los que dependemos a diario. A medida que avanza la tecnología, también lo harán las capacidades de la fundición a presión, lo que garantiza su continua relevancia en el panorama en constante evolución de la fabricación de precisión.