- Maison
- Ressources
- Blog
- Techniques de moulage sous pression de précision
Processus avancé de moulage sous pression : clé des composants de haute précision
Découvrez la précision et la polyvalence du moulage sous pression, une technique de fabrication privilégiée qui transforme le métal en fusion en pièces de haute qualité utilisées dans diverses industries. Cet article met en évidence les processus, les avantages et les matériaux associés au moulage sous pression.
Comprendre le moulage sous pression
Le moulage sous pression représente une technique de fabrication dans laquelle du métal en fusion est injecté avec force dans un moule, créant ainsi des composants aux formes méticuleuses. Réputé pour sa capacité à produire des conceptions complexes avec une précision inégalée, le moulage sous pression apparaît comme l'option privilégiée pour les industries visant une qualité de pointe dans leurs résultats.
Avantages du moulage sous pression
La prévalence du moulage sous pression dans diverses industries peut être attribuée à une multitude d’avantages qu’elle apporte. Parmi les avantages essentiels figurent :
- Haute précision et précision dimensionnelle :Permet la fabrication de composants complexes avec une précision exceptionnelle et des tolérances strictes.
- Qualité de surface supérieure :Génère des surfaces élégantes, minimisant la nécessité de procédures de finition supplémentaires.
- Robustesse et Longévité : Produit des composants aux attributs mécaniques élevés, idéaux pour les applications ayant des exigences de performances exigeantes.
- Taux de production élevés : Production rapide de grandes quantités grâce à la solidification rapide du métal en fusion.
- Rentable pour les grandes séries : Rentable pour la production de masse une fois les coûts initiaux d’outillage et de moule couverts.
- Options d'alliage polyvalentes : Prend en charge une large gamme d’alliages métalliques, permettant une sélection de matériaux sur mesure.
- Réduction des déchets de matériaux :La précision minimise le gaspillage de matériaux, contribuant ainsi aux avantages environnementaux et financiers.
- Cohérence et répétabilité :Assure l’uniformité et la fiabilité des cycles de production.
- Géométries complexes : Convient aux pièces complexes aux formes et caractéristiques complexes.
Types de moulage sous pression
Les procédés de moulage sous pression sont principalement classés en deux types : le moulage sous pression en chambre chaude et le moulage sous pression en chambre froide, qui se distinguent par leurs approches de fusion et de transfert de métal dans la machine de moulage sous pression.
Moulage sous pression en chambre chaude :
Dans le moulage sous pression en chambre chaude, le système d’injection est immergé dans un bain de métal en fusion. Cette méthode est couramment utilisée pour les alliages ayant des points de fusion plus bas, tels que le zinc, l'étain et le plomb. Le mécanisme d'injection, ou piston, est immergé dans le métal en fusion et, à mesure qu'il se rétracte, le métal en fusion est aspiré dans la chambre. Ce processus se caractérise par sa rapidité et convient bien aux petits composants bénéficiant de temps de cycle rapides.
Moulage sous pression en chambre froide :
Le moulage sous pression en chambre froide est adapté aux alliages ayant des points de fusion plus élevés, notamment l'aluminium, le laiton et le magnésium. Contrairement au moulage sous pression en chambre chaude, le système d’injection dans le moulage sous pression en chambre froide est distinct du bain de métal en fusion. Le métal en fusion est versé dans la chambre froide puis refoulé dans la cavité de la filière sous haute pression. Cette méthode est particulièrement avantageuse pour les pièces plus grandes et plus complexes nécessitant l’utilisation d’alliages à point de fusion élevé.
Moulage sous pression par rapport aux autres processus de moulage
Voici une comparaison du moulage sous pression avec d'autres procédés de moulage courants :
Moulage sous pression :
Avantages : Haute précision, finition de surface supérieure, temps de cycle plus courts, idéal pour la production en grand volume.
Inconvénients : coûts d’outillage plus élevés, options d’alliage limitées, moins flexible pour les petites séries.
Moulage en sable:
Avantages : coûts d'outillage réduits, polyvalent pour les alliages et les tailles de pièces, adapté aux prototypes et à la production en faible volume.
Inconvénients : précision moindre, finition de surface plus rugueuse, temps de cycle plus longs, plus de main d'œuvre.
Avantages : Excellente finition de surface, bonne précision dimensionnelle, adapté aux pièces complexes et détaillées.
Inconvénients : taux de production plus lents, coûts d’outillage plus élevés, moins rentable pour une production à grande échelle.
Coulée par gravité :
Avantages : Coûts d’outillage inférieurs, adaptés à divers alliages, adaptés à la production de volumes moyens à élevés.
Inconvénients : Des cadences de production plus lentes, moins de précision que le moulage sous pression, peuvent nécessiter une finition supplémentaire.
Coulée centrifuge :
Avantages : Convient aux pièces cylindriques, bonnes propriétés métallurgiques, permet d'obtenir une structure dense.
Inconvénients : limité à des géométries spécifiques, temps de cycle plus longs, moins précis que le moulage sous pression.
Le choix entre le moulage sous pression et d'autres procédés de moulage dépend des exigences spécifiques de l'application, notamment des propriétés des matériaux, de la complexité des pièces, du volume de production et des contraintes budgétaires. Chaque méthode a ses atouts et ses limites, ce qui les rend adaptées à différents scénarios de fabrication.
Matériaux utilisés dans le moulage sous pression
Le moulage sous pression est un procédé polyvalent qui peut s'adapter à divers matériaux, mais certains alliages sont plus couramment utilisés en raison de leurs propriétés spécifiques et de leur adéquation au processus de moulage sous pression. Les matériaux les plus courants pour le moulage sous pression comprennent :
Alliages d'aluminium :
Largement utilisé pour sa faible densité, son rapport résistance/poids élevé, sa résistance à la corrosion et sa conductivité thermique.
Alliages courants : A380, A383, A360, ADC12.
Alliages de zinc :
Populaire pour les composants plus petits, offrant une haute précision, d'excellentes propriétés de moulage et une bonne finition de surface.
Alliages courants : Zamak 3, Zamak 5, Zamak 7.
Alliages de magnésium :
Utilisé pour les composants légers nécessitant une résistance élevée, avec des avantages tels qu'une faible densité et une bonne usinabilité.
Alliages courants : AZ91D, AM60B.
Alliages de cuivre
Appliqué en moulage sous pression pour une excellente conductivité et résistance à la corrosion.
Alliages courants : C87500, C95800.
Alliages de plomb et d’étain :
Utilisé dans des applications spécifiques où de faibles points de fusion sont avantageux.
Les exemples incluent les alliages Pb-Sn (plomb-étain).
Processus de moulage sous pression expliqué
Voici un aperçu du processus de moulage sous pression :
- Préparation du moule :Commencez avec un moule usiné avec précision, composé de moitiés fixes et mobiles en acier trempé.
- Serrage : Rassemblez et serrez solidement les moitiés du moule pour maintenir leur position pendant la coulée.
- Injection de métal en fusion : Chauffer du métal en fusion (alliages d’aluminium, de zinc ou de magnésium) dans un four. Injectez le métal en fusion dans la cavité du moule sous haute pression.
- Solidification: Solidifiez rapidement le métal en fusion dans le moule pour prendre sa forme. Contrôlez le temps de refroidissement pour les propriétés souhaitées.
- Ouverture du moule :Ouvrez les moitiés du moule et éjectez la pièce moulée dans la forme de pièce souhaitée.
- Découpage et finition : Coupez l'excédent de matière (flash) et terminez la pièce, en ajoutant des fonctionnalités si nécessaire.
- Récupération et recyclage :Recyclez les excédents de matériaux et les carottes de coulée pour plus de durabilité et d’efficacité.
Post-traitement pour les pièces moulées sous pression
Une fois le processus de moulage sous pression terminé, des étapes de post-traitement supplémentaires sont fréquemment entreprises pour répondre à des exigences particulières, améliorer la qualité du produit final et garantir son alignement avec les spécifications souhaitées. Les étapes de post-traitement des pièces moulées sous pression peuvent inclure :
- Découpage et ébavurage :Retirez l'excès de matériau (« flash ») et lissez les bords rugueux créés pendant le processus de coulée.
- Usinage: Effectuer des fraisage, perçage ou taraudage pour des dimensions précises ou pour créer des fonctionnalités spécifiques.
- Finition des surfaces :Améliorez l'apparence et la résistance à la corrosion grâce à des méthodes telles que le grenaillage, la finition vibratoire ou la galvanoplastie.
- Traitement thermique:Améliorez les propriétés mécaniques telles que la résistance et la dureté grâce à des processus de traitement thermique.
- Contrôle de la qualité: Assurez-vous que les pièces moulées sous pression respectent les tolérances et les normes de qualité spécifiées grâce à des contrôles dimensionnels, des inspections visuelles et des tests non destructifs.
- Assemblée:Joignez, soudez ou fixez des pièces moulées sous pression avec d'autres composants pour créer des produits finis.
- Revêtement ou peinture de surface : Appliquez des revêtements ou de la peinture pour obtenir de la couleur, de la texture ou une protection supplémentaire contre les facteurs environnementaux.
Applications du moulage sous pression
- Electronique grand public : Boîtiers et composants structurels pour smartphones, ordinateurs portables, appareils photo et équipements audio
- Appareils électroménagers:Pièces de machines à laver, réfrigérateurs et fours, luminaires et boîtiers de lampes
- Automobile:Composants de moteur, carters de transmission et pièces du système de freinage
- Équipement industriel:Boîtes de vitesses, corps de pompe et composants de vannes
- Aérospatial:Composants d'aéronefs, y compris les pièces de moteur
- Militaire et Défense :systèmes d'armes et pièces de véhicules
- Articles de sport:composants de vélo et clubs de golf
- Télécommunications
- Équipement médical
- Meubles
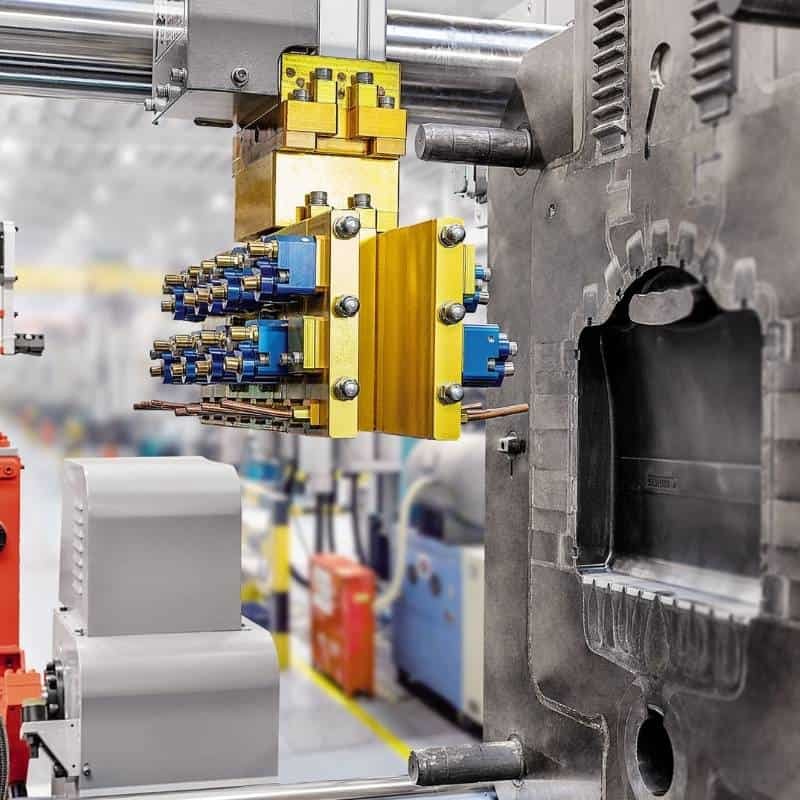
Innovations dans la technologie de moulage sous pression
Ces dernières années, la technologie du moulage sous pression a connu diverses innovations visant à améliorer l’efficacité, la précision, la durabilité et à élargir la gamme d’applications. Quelques innovations notables dans la technologie du moulage sous pression :
- Avancées du moulage sous pression haute pression (HPDC) : Des améliorations continues des machines, des pressions d'injection plus élevées, des cycles plus rapides et des systèmes de contrôle avancés améliorent l'efficacité.
- Moulage sous pression à paroi mince : Les innovations en matière d'outillage et de contrôle des processus permettent la production de composants à parois plus fines, essentiels à la réduction de poids dans les applications automobiles et aérospatiales.
- Coulée sous pression assistée sous vide :Réduit la porosité en éliminant les gaz avant solidification, ce qui améliore les propriétés mécaniques et la finition de surface.
- Moulage sous pression semi-solide :Utilise du métal partiellement solidifié pour améliorer les propriétés mécaniques, particulièrement bénéfique pour les applications nécessitant résistance et précision.
- Matériaux de matrice avancés : Les aciers à outils et les revêtements haute performance améliorent la durabilité des matrices, réduisant ainsi la maintenance et les temps d'arrêt.
- Matériaux et alliages avancés : Les recherches en cours permettront d'introduire des alliages aux propriétés améliorées pour répondre aux besoins changeants de l'industrie.
- Surveillance et contrôle en temps réel : L'intégration de capteurs et de systèmes de surveillance optimise le moulage sous pression en garantissant une qualité constante des pièces grâce à un contrôle en temps réel.
- Impression 3D pour l'outillage de matrice : Exploration de impression en 3D pour les moules complexes et complexes, offrant des solutions rentables pour la production d'outillage.
- Logiciel de simulation : La simulation avancée prédit l'écoulement du métal en fusion, identifie les défauts et simule le cycle de fabrication, réduisant ainsi le besoin de prototypes physiques.
- Développement d'alliages : Les recherches en cours introduisent de nouveaux matériaux dotés de propriétés améliorées, notamment une résistance, une résistance à la chaleur et une recyclabilité améliorées.
- Améliorations de l’efficacité énergétique : Les innovations dans les technologies de fours économes en énergie et les pratiques durables contribuent à réduire l’impact environnemental du moulage sous pression.
- Robotique et automatisation :L'utilisation accrue de la robotique améliore l'efficacité, réduit les coûts de main-d'œuvre et améliore la sécurité dans les tâches telles que l'extraction, le découpage et le contrôle qualité des pièces.
- Personnalisation et production en petits lots :Évoluer pour s’adapter à des processus de production plus flexibles et agiles afin de répondre aux demandes croissantes de personnalisation.
Ces innovations contribuent collectivement à faire du moulage sous pression un processus de fabrication plus polyvalent, précis et durable. À mesure que la technologie continue de progresser, de nouveaux développements devraient façonner l’avenir du moulage sous pression dans diverses industries.
Impact environnemental du moulage sous pression
Le processus de moulage sous pression, comme tout processus de fabrication industrielle, a des implications environnementales. Si le moulage sous pression offre des avantages en termes d’efficacité et d’utilisation des matériaux, il s’accompagne également de certaines considérations environnementales. Il est important de noter que les progrès technologiques et les pratiques industrielles, ainsi que les cadres réglementaires, contribuent à réduire l'impact environnemental du moulage sous pression. De nombreuses installations de moulage sous pression s'efforcent activement d'adopter des pratiques plus durables, telles que l'utilisation d'équipements économes en énergie, la mise en œuvre de programmes de recyclage et le respect des normes et certifications environnementales. Voici quelques aspects de l’impact environnemental du moulage sous pression :
- Consommation d'énergie: La fusion du métal lors du moulage sous pression nécessite une énergie considérable, influencée par des facteurs tels que le type d'alliage et l'efficacité de l'équipement.
- Émissions :Le fonctionnement des fours peut émettre des polluants contribuant à la pollution de l'air, mais les installations modernes utilisent des technologies pour minimiser les émissions et respecter les réglementations.
- Utilisation de l'eau : Le moulage sous pression implique une certaine consommation d'eau pour le refroidissement, ce qui nécessite une gestion responsable pour éviter tout impact sur l'environnement.
- La production de déchets:Le moulage sous pression génère des déchets, notamment des excès de matériaux et des pièces rejetées.
- Utilisation de produits chimiques : Des lubrifiants et des agents de démoulage sont utilisés dans le moulage sous pression, et leur choix et leur manipulation peuvent avoir un impact sur l'environnement s'ils ne sont pas gérés correctement.
- Recyclabilité : Les matériaux moulés sous pression, tels que l'aluminium et le zinc, sont hautement recyclables, favorisant une économie circulaire et réduisant l'impact environnemental.
Conseils pour un moulage sous pression de qualité
Garantir la qualité du processus de moulage sous pression est essentiel pour produire des composants fiables et précis. En intégrant les conseils ci-dessous, les fabricants peuvent améliorer la qualité de leurs pièces moulées sous pression, réduire les défauts et optimiser l'efficacité globale de la production :
- Conception optimale des outils : Investissez dans des outils de moulage sous pression bien conçus pour obtenir une géométrie précise des pièces, réduire les défauts et garantir un refroidissement et une ventilation uniformes.
- Sélection des matériaux : Choisissez des alliages basés sur les propriétés mécaniques, la résistance à la corrosion et la conductivité thermique.
- Entretien et lubrification des moules : Inspectez et entretenez régulièrement les moules pour éviter l’usure. Appliquez des lubrifiants de matrice appropriés pour réduire la friction, faciliter le démoulage des pièces et contribuer à la longévité du moule.
- Optimisation du processus: Ajustez les paramètres de processus pour la pression d’injection, la température et la durée du cycle afin d’optimiser la qualité des pièces et l’efficacité de la production.
- Surveillance en temps réel:Mettez en œuvre des systèmes de surveillance pour suivre les paramètres clés du processus, en identifiant les problèmes rapidement et en évitant les pièces défectueuses.
- Contrôles de qualité :Effectuer des contrôles réguliers, y compris des inspections dimensionnelles, des évaluations visuelles et des méthodes de test, pour respecter les tolérances et les normes de qualité spécifiées.
- Système de portail optimisé : Concevez un système de déclenchement efficace pour un flux de métal contrôlé, minimisant les turbulences et réduisant le risque de défauts.
- Formation et développement des compétences : Fournir une formation appropriée aux opérateurs afin de maintenir une qualité constante grâce à un personnel qualifié et compétent.
Pièces moulées sous pression personnalisées
Si vous souhaitez obtenir des pièces moulées sous pression personnalisées auprès des fabricants, voici quelques étapes et considérations pour vous guider tout au long du processus :
- Précisez vos besoins :Définissez clairement vos besoins, y compris le matériau, les dimensions, l'état de surface, la quantité et toute caractéristique ou tolérance spécifique.
- Fabricants de recherche :Identifiez des fabricants de moulage sous pression réputés possédant une expérience et des certifications pertinentes dans les alliages et processus souhaités.
- Demander des devis : soumettez une demande de devis (RFQ) détaillée aux fabricants choisis, en fournissant les détails du projet pour des devis précis.
- Évaluer les devis : Examinez les devis en tenant compte du coût, des délais de livraison, des mesures d'assurance qualité et des services supplémentaires.
- Évaluer les capacités : Évaluez les capacités, l’expérience et les antécédents de chaque fabricant dans la production de composants similaires.
- Assurance qualité:Renseignez-vous sur les processus d’assurance qualité et les certifications pour garantir la conformité aux normes de l’industrie.
- Visitez les installations (si possible) : Envisagez de visiter les installations de fabrication pour évaluer par vous-même les équipements, les processus et les capacités globales.
- Communication: Établissez une communication claire, discutez des exigences, des défis potentiels et assurez une compréhension mutuelle.
- Prototypage :Demandez des prototypes ou des échantillons pour évaluer la qualité et effectuer des ajustements avant la production à grande échelle.
- Négocier les conditions : Négociez les conditions, notamment les prix, les délais de livraison, les conditions de paiement et d’autres aspects contractuels.
- Accord contractuel:Formalisez l’accord avec un contrat, documentant les spécifications, les calendriers de livraison et les normes de qualité.
- Suivi de la production : Restez engagé tout au long de la production et recevez des mises à jour régulières pour résoudre rapidement tout problème.
- Contrôle de la qualité:Effectuer des inspections de qualité approfondies à la réception des pièces, y compris des contrôles dimensionnels et des évaluations visuelles.
- Commentaires et amélioration : Fournir des commentaires aux fabricants pour améliorer les collaborations futures et l’amélioration continue.
En suivant ces étapes et en maintenant une communication ouverte avec le fabricant choisi, vous pouvez augmenter vos chances de recevoir des pièces moulées sous pression personnalisées de haute qualité qui répondent à vos exigences spécifiques.
Conclusion
Le moulage sous pression constitue la pierre angulaire de la fabrication moderne, offrant précision, efficacité et durabilité. Son impact se répercute dans tous les secteurs, façonnant les produits sur lesquels nous comptons quotidiennement. À mesure que la technologie progresse, les capacités du moulage sous pression évolueront également, garantissant ainsi sa pertinence continue dans le paysage en constante évolution de la fabrication de précision.