- Maison
- Ressources
- Blog
- Comparaison de l'aluminium 5052 et de l'aluminium 6061
Aluminum grades come in various grades, however, Aluminium 5052 et Aluminium 6061 are two of the most popular alloys in the market. Both alloys offer unique benefits and are widely used across various industries. This article provides a detailed comparison of 5052 aluminum and 6061 aluminum, covering their composition, mechanical properties, and real-world applications.
What is 5052 Aluminum?

5052 aluminum is a non-heat-treatable alloy primarily composed of aluminum, magnesium (2.2-2.8%), and chromium (0.15-0.35%). Known for its excellent corrosion resistance, especially in marine environments, it is a widely-used material in industries that demand durability and resistance to harsh elements. Its high strength and good weldability make it ideal for applications like fuel tanks, pressure vessels, and outdoor structures.
Key Properties of 5052 Aluminum:
- Résistance à la corrosion: Exceptional, particularly in saltwater and chemical environments.
- Soudabilité: Excellent, with minimal risk of cracks or defects.
- Force: Moderate, with tensile strength ranging from 31,000 to 38,000 psi.
- Formabilité: Excellent, making it ideal for complex shapes and deep draws.
- Non-Magnetic and Non-Heat-Treatable: Relies on cold working for strength enhancements.
What is 6061 Aluminum?

6061 aluminum is a versatile, heat-treatable alloy composed primarily of aluminum, magnesium (0.8-1.2%), and silicon (0.4-0.8%), with additional elements like copper and chromium. It is renowned for its balance of strength, corrosion resistance, and machinability, making it a popular choice for structural components, aerospace parts, and transportation equipment.
Key Properties of 6061 Aluminum:
- Résistance à la corrosion: Good, though not as strong as 5052 in marine environments.
- Force: High, with tensile strength ranging from 38,000 to 42,000 psi.
- Usinabilité: Excellent, suitable for precision machining.
- Aptitude au traitement thermique: Can be hardened through heat treatment for enhanced mechanical properties.
- Soudabilité: Good, though heat treatment after welding may be required to restore strength.
5052 Aluminum vs. 6061 Aluminum: A Side-by-Side Comparison
If you want to properly understand the comparison between the Aluminum 5052 and 6061 grades, then here is a summarized table:
Propriété | Aluminium 5052 | 6061 Aluminium |
Résistance à la corrosion | Superior, especially in saltwater and marine environments | Good, suitable for most environments |
Force | Moderate (31,000–38,000 psi) | High (38,000–42,000 psi) |
28,000 psi | 35,000 psi | |
Résistance à la traction | 31,000–38,000 psi | 38,000–42,000 psi |
Elongation (%) | 12–20% | 8–10% |
Hardness (Brinell) | 60 | 95 |
2.68 g/cm³ | 2.70 g/cm³ | |
Soudabilité | Excellent | Good, may require post-weld heat treatment |
Usinabilité | Fair | Excellent |
Formabilité | Excellent | Modéré |
Aptitude au traitement thermique | Non-heat-treatable | Heat-treatable |
Applications | Marine parts, tanks, pressure vessels, automotive panels | Structural components, aerospace, transportation |
Coût | Generally lower | Slightly higher |
Applications de l'aluminium 5052
5052 aluminum excels in environments that demand high corrosion resistance, particularly those exposed to saltwater or chemicals. Its excellent formability and weldability make it a popular choice for:
- Applications marines: Ship hulls, fuel tanks, and boat components.
- Industrie automobile: Body panels, fuel tanks, and truck trailers.
- Pressure Vessels: Storage tanks and chemical containers.
- Architectural Use: Roofing, siding, and decorative panels.
- Équipement industriel: Conveyor belts, enclosures, and piping systems.
Applications de l'aluminium 6061
6061 aluminum is known for its strength, machinability, and versatility, making it the go-to material for structural and precision applications. Common uses include:
- Composants aérospatiaux: Aircraft wings, fuselage parts, and landing gear.
- Applications structurelles: Frames, bridges, and trusses.
- Transport: Automotive parts, railroad cars, and bicycles.
- Machined Parts: Precision tools, jigs, and fixtures.
- Équipement sportif: High-performance bicycles, climbing gear, and baseball bats.
How to Choose Between 5052 Aluminum and 6061 Aluminum?
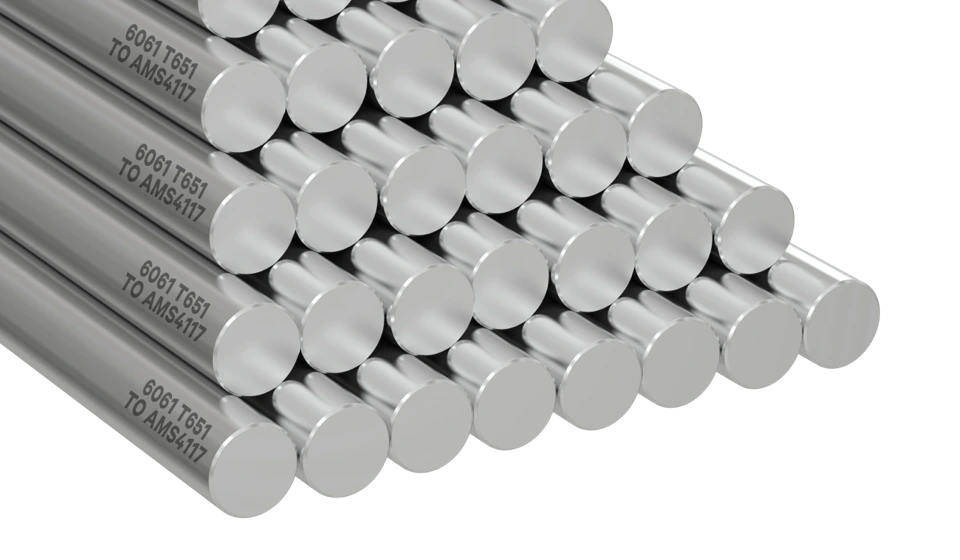
Choosing the right aluminum alloy depends on the specific requirements of your project. Here’s a quick guide:
Choose 5052 Aluminum If:
- You need superior corrosion resistance, particularly in marine or chemical environments.
- Formability is a priority for creating complex shapes or deep draws.
- Welding is critical, and you want minimal risk of cracks.
- Cost is a significant factor, as 5052 is generally more affordable.
Choose 6061 Aluminum If:
- Strength and rigidity are critical for structural integrity.
- Machinability is important for creating precision parts.
- Your project involves aerospace or transportation components.
- Heat treatment is necessary to achieve specific mechanical properties.
Conclusion
The decision between 5052 aluminum and 6061 aluminum ultimately depends on the specific demands of your project. 5052 aluminum excels in environments requiring corrosion resistance, formability, and affordability, while 6061 aluminum offers superior strength, machinability, and heat treatability for structural and precision applications. By understanding the differences in their properties and applications, you can confidently select the right alloy to meet your needs.
Whether you’re designing marine equipment, structural components, or aerospace parts, both 5052 and 6061 aluminum provide dependable solutions for various industrial applications.
Découvrez-en davantage avec nos articles de blog.
Messages récents
Découvrez-en plus sur nos produits.
Produits connexes
Devis instantané !