Una comprensión integral del acero inoxidable: pasado, presente y futuro
Los orígenes y la historia del acero inoxidable: una cronología
- En 1794: El químico francés Louis Nicolas Vauquelin, mientras estudiaba el mineral de crocoita (cromato de plomo), produjo con éxito trióxido de cromo (CrO3) mezclando el mineral con ácido clorhídrico. En 1797 logró aislar el cromo metálico calentando este óxido en un horno de carbón. Por esto, se acredita a Vauquelin como el verdadero descubridor del elemento cromo.
- A principios del siglo XIX: Los científicos británicos James Stoddart, Michael Faraday y Robert Mallet observaron la resistencia de las aleaciones de cromo y hierro a los agentes oxidantes.
- 1821: Pierre Berthier descubrió la resistencia a la corrosión de las aleaciones de cromo y hierro ante ciertos ácidos y sugirió su uso en la fabricación de cubiertos.
- Década de 1840: Los fabricantes de acero en Sheffield, Inglaterra, y Krupp en Alemania producían acero al cromo, y este último lo utilizaba para fabricar cañones en la década de 1850.
- 1869: J. Baur, de la Chrome Steel Works de Brooklyn, produjo por primera vez en los Estados Unidos acero que contenía cromo para la construcción de puentes y en 1869 obtuvo una patente estadounidense para el acero al cromo. Posteriormente, el científico británico John T. Woods y John Clark reconoció la importancia del contenido de cromo para la resistencia a la corrosión de las aleaciones de cromo, señalando que el contenido de cromo debe estar dentro de 5-30%.
- Finales de la década de 1890: químico alemán Hans Goldschmidt desarrolló un proceso aluminotérmico (termita) para producir cromo libre de carbono.
- 1904 ~ 1911:Algunos investigadores, en particular León Guillet de Francia, prepararon aleaciones que hoy se consideran acero inoxidable.
- 1911: Philip Monnartz informó sobre la relación entre el contenido de cromo y la resistencia a la corrosión.
- 1912: Los ingenieros de Krupp, Benno Strauss y Eduard Maurer, patentaron el acero inoxidable austenítico (conocido hoy como 18/8 o AISI tipo 304).
- 1912: Mientras buscamos una aleación resistente a la corrosión para cañones de armas, Harry Brearley en Sheffield, Inglaterra, descubrió lo que hoy se conoce como acero inoxidable martensítico AISI tipo 420.
- 1915: El descubrimiento de Harry Brearley fue anunciado en The New York Times. Posteriormente colaboró con Haynes y, con un grupo de inversores, fundó la American Stainless Steel Corporation en Pittsburgh, Pensilvania.
Composición elemental del acero inoxidable: la clave para prevenir la oxidación
El acero inoxidable se compone principalmente de hierro, cromo, níquel, molibdeno, vanadio y otros elementos de aleación comunes. El hierro generalmente constituye alrededor de 70% a 80% de acero inoxidable, lo que proporciona la resistencia estructural necesaria. El cromo es crucial para la resistencia a la oxidación del acero inoxidable; Se requiere al menos 10,5% de cromo para que el acero se considere inoxidable, ya que es esencial para formar una capa densa y estable de óxido de cromo en la superficie. Esta capa es muy estable e impermeable, impidiendo eficazmente la penetración de oxígeno y humedad cuando se expone al aire o al agua, mejorando significativamente la resistencia a la corrosión del acero.
El contenido de níquel suele estar entre 8% y 10%, lo que mejora la resistencia a la corrosión, la conformabilidad y la resistencia del acero inoxidable y ayuda a mantener las cualidades no magnéticas del acero inoxidable austenítico a bajas temperaturas. El contenido típico de molibdeno varía de 2% a 3%, lo que mejora la resistencia a la corrosión por picaduras y grietas, lo que es particularmente beneficioso en condiciones cloradas. Elementos como el vanadio y el titanio suelen estar presentes en cantidades muy bajas, que normalmente no superan los 0,51 TP3T. Fortalecen el acero inoxidable formando carburos finos, como el carburo de vanadio (VC) y el carburo de titanio (TiC), que estabilizan la estructura y mejoran la dureza y la resistencia. Estos carburos son de vital importancia para mejorar el rendimiento general del acero inoxidable debido a su alta dureza y resistencia al desgaste. Al ajustar cuidadosamente las proporciones de estos elementos, el acero inoxidable puede funcionar de manera óptima en una variedad de entornos hostiles.
Análisis en profundidad del acero inoxidable 304 más utilizado: composición y propiedades
Acero inoxidable 304 Es uno de los aceros inoxidables austeníticos más versátiles y utilizados, conocido por su excelente resistencia a la corrosión y formabilidad.
Composición del acero inoxidable 304:
% | 304 | 304L | 304H |
C | 0.0 – 0.07 | 0.0 – 0.03 | 0.04 – 0.08 |
Minnesota | 0.0 – 2.0 | 0.0 – 2.00 | 0.0 – 2.0 |
Si | 0.0 – 1.00 | 0.0 – 1.00 | 0.0 – 1.0 |
PAGS | 0.0 – 0.05 | 0.0 – 0.05 | 0.0 – 0.04 |
S | 0.0 – 0.03 | 0.0 – 0.02 | 0.0 – 0.02 |
cr | 17.50 – 19.50 | 17.50 – 19.50 | 17.00 – 19.00 |
Ni | 8.00 – 10.50 | 8.00 – 10.50 | 8.00 – 11.00 |
Fe | Balance | Balance | Balance |
norte | 0.0-0.11 | 0.0-0.11 | 0.0 – 0.10 |
Propiedades del acero inoxidable 304
Calificación | 304 |
Resistencia a la tracción (MPa) | 500 – 700 |
Estrés de prueba (MPa) | 190 |
Elongación A50 mm | 45 min % |
Dureza Brinell | 215 máx. HB |
Propiedad | Valor |
Densidad | 8,00 g/cm3 |
Punto de fusion | 1450°C |
Módulo de elasticidad | 193 GPa |
Resistividad electrica | 0,72 x 10-6 Ω.m |
Conductividad térmica | 16,2 W/mK |
Expansión térmica | 17,2 x 10-6/K |
Perspectiva microscópica: el mecanismo de prevención de la oxidación del acero inoxidable
La corrosión del metal se refiere al daño causado por los efectos combinados de factores químicos, físicos, mecánicos o biológicos en su entorno. La corrosión atmosférica, que es el deterioro de materiales o estructuras metálicas debido a reacciones químicas o electroquímicas en condiciones atmosféricas, es el tipo de corrosión más común. A nivel mundial, se utilizan más de 60% de acero en condiciones atmosféricas, incluidas vigas de acero, rieles, diversos equipos mecánicos y vehículos. La pérdida de metal debido a la corrosión atmosférica normalmente representa más del 50% del daño total por corrosión.
En la corrosión de metales estándar, el hierro pierde electrones (se oxida) y se transforma en iones de hierro, que luego reaccionan con el agua para formar óxidos férricos hidratados (óxido).
En el acero inoxidable, que contiene un alto contenido de cromo, el cromo reacciona con el oxígeno del medio ambiente (ya sea aire o agua) para formar una capa delgada y estable de óxido de cromo sobre la superficie del metal. Esta capa de óxido de cromo es increíblemente delgada pero muy adherente, lo que previene eficazmente la migración de electrones necesaria para la oxidación del hierro y aísla físicamente el hierro de los oxidantes ambientales.
Si la capa de óxido se daña mecánicamente o se rompe químicamente temporalmente, el cromo del acero inoxidable puede regenerar espontáneamente la película de óxido y volver a pasivar la superficie. Esta característica de autocuración es crucial en entornos donde el metal está frecuentemente sujeto a desgaste o exposición química severa.
La composición de la aleación del acero inoxidable generalmente incluye níquel y molibdeno, que mejoran la estabilidad de la película de óxido, particularmente en ambientes que contienen cloruro (como áreas costeras o condiciones de sal deshielo), lo que reduce el riesgo de corrosión por picaduras y grietas. La estabilidad de la capa de óxido se mantiene incluso en condiciones ácidas o altamente oxidantes, lo que hace que el acero inoxidable sea adecuado para una amplia gama de condiciones atmosféricas.
Limitaciones del acero inoxidable: ¿cuándo se corroe?
- Cloruros: Los cloruros, especialmente a altas temperaturas, pueden comprometer la capa de pasivación del acero inoxidable, provocando corrosión localizada y picaduras. Esto se ve comúnmente en ambientes marinos y con las sales de deshielo utilizadas en las carreteras durante el invierno.
- Ácidos fuertes: Si bien el acero inoxidable puede resistir la corrosión de ácidos débiles, los ácidos fuertes como el ácido sulfúrico y clorhídrico pueden penetrar rápidamente su capa de pasivación, provocando una corrosión significativa.
- Oxidantes fuertes: Los oxidantes fuertes como los peróxidos y ciertos ácidos (por ejemplo, ácido nítrico) pueden acelerar el proceso de corrosión en el acero inoxidable.
- Ambientes bajos en oxígeno: En ambientes con suministro insuficiente de oxígeno, como suelo y lodos, la capa de pasivación de acero inoxidable no puede regenerarse eficazmente, lo que aumenta el riesgo de corrosión.
- Condiciones de alta temperatura: A altas temperaturas, la capa de pasivación del acero inoxidable puede agrietarse o volverse inestable, acelerando el proceso de corrosión, particularmente en presencia de sustancias corrosivas.
- Estres mecanico: El agrietamiento por corrosión bajo tensión puede ocurrir cuando el acero inoxidable se somete a esfuerzos de tracción y ambientes corrosivos simultáneamente, especialmente en presencia de cloruros.
- Actividad microbiana: En algunos casos, los procesos metabólicos de microorganismos (como las bacterias) pueden producir sustancias corrosivas. Este fenómeno, conocido como corrosión microbiológicamente inducida (MIC), puede provocar la formación de biopelículas en la superficie del acero inoxidable, favoreciendo la corrosión.
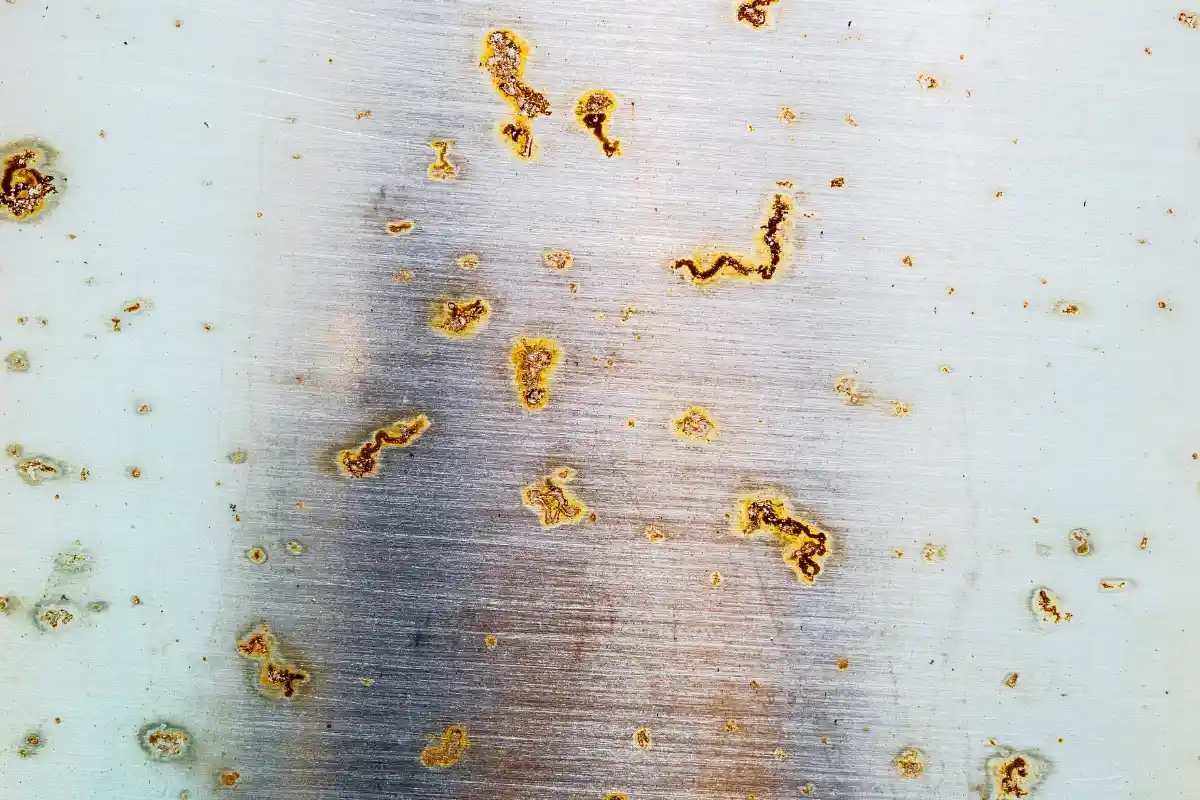
Estándares de acero inoxidable: clasificación de acero inoxidable
Existen varios estándares principales de clasificación de acero inoxidable en todo el mundo, establecidos por diferentes organizaciones de estandarización para satisfacer las necesidades de diversas aplicaciones industriales y comerciales.
- Estándares de Estados Unidos (AISI/ASTM): AISI (Instituto Americano del Hierro y el Acero) y ASTM (Sociedad Estadounidense de Pruebas y Materiales) son clasificaciones comunes de acero inoxidable que incluyen la serie 300 (como 304, 316), la serie 400 y más. Estos estándares se utilizan ampliamente en los Estados Unidos y en todo el mundo.
- Normas europeas (EN/ISO): ES Las normas (norma europea) son emitidas por el Comité Europeo de Normalización y cubren diversos aspectos del acero inoxidable, como 1.4301 para 304, 1.4401 para 316, etc. Además, YO ASI (Organización Internacional de Normalización) también publica normas de acero inoxidable de gran influencia.
- Normas alemanas (DIN): Las normas industriales alemanas (DIN) son muy conocidas a nivel internacional, especialmente en los sectores de ingeniería y fabricación en Europa y Asia.
- Estándares japoneses (JIS): JIS (Estándares industriales japoneses) son particularmente populares en Asia, especialmente en las industrias de fabricación de automóviles y electrónica.
- Estándares británicos (BS): Los estándares británicos (BS) son desarrollados por la British Standards Institution. Aunque su impacto global directo puede no ser tan extenso como el de ASTM o EN, todavía mantienen una relevancia significativa en el Reino Unido y muchos países de la Commonwealth.
- Estándares chinos (GB): Los Estándares Nacionales (GB) de China se utilizan con frecuencia en productos fabricados y exportados desde China, y a menudo se alinean con los estándares internacionales y hacen referencia a ellos.
A continuación se muestran algunas comparaciones de grados de acero inoxidable según diferentes normas:
China (GB) | ruso (GOST) | americano(ASTM) | Alemán (DIN) | YO ASI |
1Cr17Mn6Ni5N | – | 201 | X12CrMnNiN 17-7-5 | A-2 |
1Cr18Mn8Ni5N | 12KH17G9AH4 | 202 | X12CrMnNiN 18-9-5 | A-3 |
1Cr17Ni7 | – | 301 | – | 14 |
1Cr18Ni9 | 12KH18H9 | 302 | DIN17440-96 X12CrNi18-9 | 12 |
Y1Cr18Ni9 | – | 303 | X12CrNiS18-9 | 17 |
0Cr18Ni9 | 08KH18H10 | 304 | X5CrNi18-10 | 11 |
00Cr19Ni11 | 03KH18H11 | 304L | X2CrNi19-11 | 10 |
1Cr18Ni12 | 12KH18H12T | 305 | X4CrNi18-12 | 13 |
0Cr17Ni12Mo2 | 08KH17H13M2T | 316 | X5CrNiMo17-12-2 | 20/20a |
0Cr18Ni12Mo2Ti | 08KH17H13M2T | 316Ti S31635 | X6CrNiMoTi17-12-2 | 21 |
00Cr17Ni14Mo2 | 03KH17H14M2 | 316L | X2CrNiMo18-14-3 | 19/19a |
0Cr19Ni13Mo3 | 08KH17H15M3T | 317 | X5CrNiMo17-13-3 | – |
1Cr18Ni9Ti | 12KH18H10T | 321 | X6CrNitI18-10 | 11 |
0Cr18Ni10Ti | 08KH18H10T | 321 | X6CrNiTi18-10 | 15 |
0Cr18Ni11Nb | 08KH18H12B | 347 | X6CrNiNb18-10 | 16 |
0Cr13Al | – | 405 | X6CrAl13 | 5 |
1Cr17 | 12KH17 | 430 | X6Cr17 | 8 |
1Cr12 | 403 | X6Cr13 | 3 | |
1Cr13 | 12KH13 | 410 | X12Cr13 | 3 |
0Cr13Ae | 405 | X6Cr13 | 1 | |
2Cr13 | 20KH13 | 420 | X20Cr13 | 4 |
3Cr13 | 30KH13 | 420 | X30Cr13 | 5 |
1Cr17Ni2 | 14KH17H2 | 431 | X17CrNi16-2 | 96 |
Métodos de prueba de acero inoxidable
- Pruebas magnéticas: La mayoría de los aceros inoxidables, especialmente los austeníticos como 304 y 316, no son magnéticos en condiciones normales. Probar con un imán para ver si el material es atraído puede indicar preliminarmente si se trata de acero inoxidable austenítico. Este método es sencillo y rápido, adecuado para una rápida identificación in situ. Sin embargo, cabe señalar que el trabajo en frío puede inducir una ligera estructura martensítica en algunos aceros inoxidables, provocando un magnetismo leve.
- Pruebas de reactivos: Esto implica el uso de reactivos químicos específicos que reaccionan con iones metálicos en acero inoxidable para observar cambios de color para la identificación de componentes. Por ejemplo, las pruebas de iones de hierro se vuelven azules, los reactivos específicos de níquel reaccionan para mostrarse de rosa a rojo y los reactivos específicos de cromo se vuelven de amarillo a verde al reaccionar. Este método es de bajo costo, fácil de operar y adecuado para aplicaciones rápidas de campo.
- Pruebas de espectrómetro: Los espectrómetros analizan las longitudes de onda específicas de la luz emitida o absorbida por un material para determinar con precisión su composición química. Por ejemplo, el uso del analizador XRF portátil de Olympus para probar el acero inoxidable identifica con precisión elementos como hierro, cromo y níquel. Esta tecnología es adecuada para aplicaciones de alta precisión que requieren un análisis compositivo detallado.
Es importante señalar que los métodos de prueba anteriores sólo pueden analizar la composición de la superficie del metal. Para productos de acero inoxidable más gruesos o sólidos, estos métodos no son capaces de detectar con precisión la composición interna. Por lo tanto, la mejor estrategia para evitar la compra de materiales o productos de acero inoxidable falsificados es elegir proveedores confiables que brinden certificaciones de materiales.
Ventajas y desafíos del acero inoxidable
El acero inoxidable es conocido por su excepcional resistencia a la corrosión, alta resistencia y atractivo estético, lo que lo hace adecuado para una variedad de aplicaciones, desde diseños arquitectónicos hasta equipos industriales. También ofrece una excelente resistencia al calor y es reciclable 100%, lo que se alinea bien con las prácticas sostenibles.
A pesar de sus beneficios, el acero inoxidable puede tener un costo prohibitivo, especialmente para proyectos a gran escala, y su alta resistencia a menudo requiere herramientas y técnicas de mecanizado especializadas. Además, su mala conductividad térmica y susceptibilidad al agrietamiento por corrosión bajo tensión en entornos específicos, como los que contienen cloruros, pueden limitar su uso en determinadas aplicaciones.
Cómo se combinan varios elementos para formar acero inoxidable

- Fusión y aleación: La producción de acero inoxidable comienza con el proceso de fusión. Las materias primas suelen incluir acero procedente de la fundición de minerales utilizado directamente para la producción de acero inoxidable, acero inoxidable reciclado y ferroaleaciones como el ferroníquel. Estos materiales se calientan en un horno eléctrico hasta que se funden a altas temperaturas, durante lo cual se añaden elementos de aleación como cromo y níquel para garantizar que el acero fundido alcance la composición química especificada.
- Eliminar el exceso de carbono: Por lo general, se utiliza un horno de descarburación de argón y oxígeno (AOD) para soplar oxígeno en el acero fundido bajo una presión atmosférica estándar y al mismo tiempo inyectar gases inertes (Ar, N2). Este proceso refina y descarbura ajustando la relación argón/oxígeno, reduciendo la presión parcial de CO, bajando así el contenido de carbono a un nivel muy bajo y evitando la oxidación del cromo en el acero.
- Fundición: Después de acondicionarlo y agitarlo, el acero fundido se vierte en moldes para solidificarse en losas o lingotes.
- Laminación en frío y en caliente:
- Empezando por las losas, que se calientan y luego se procesan mediante laminadores de desbaste y acabado para formar tiras de acero.
- La banda de acero caliente se enfría a una temperatura preestablecida en un flujo laminar y luego se enrolla mediante una bobinadora.
- La bobina enfriada tiene una superficie oxidada, que se elimina mediante recocido y decapado.
- Algunos productos laminados en caliente se utilizan directamente, mientras que otros se transforman en productos laminados en frío.
- La laminación en frío implica el uso de productos laminados en caliente con un espesor de 3,0 a 5,5 mm, que luego se laminan utilizando equipos de laminación en frío.
- Después del laminado en frío, el acero inoxidable se recoce para eliminar el endurecimiento causado por el laminado.
- El decapado elimina la capa de óxido formada durante el recocido y realiza un tratamiento de pasivación para mejorar la resistencia a la corrosión de la placa de acero.
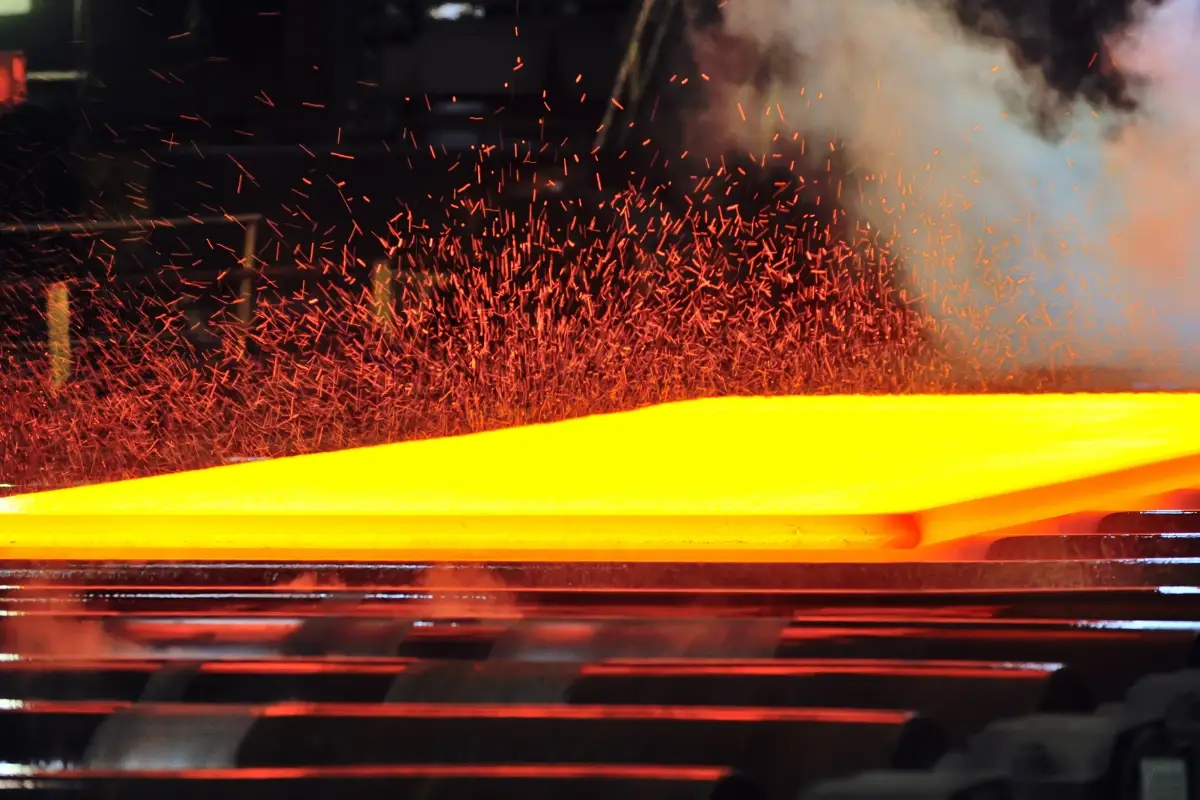
Desarrollo innovador de aleaciones de acero inoxidable
Innovando en aleaciones de acero inoxidable mediante el ajuste de la proporción elemental
El rendimiento de las aleaciones de acero inoxidable se puede optimizar e innovar ajustando las proporciones de los elementos en su composición química. Al aumentar o disminuir el contenido de elementos clave como cromo, níquel, molibdeno y titanio, se pueden realizar cambios significativos en las propiedades mecánicas, la resistencia a la corrosión y la estabilidad térmica del acero inoxidable. Por ejemplo, aumentar el contenido de cromo mejora la resistencia a la oxidación y la resistencia a la corrosión; agregar más níquel mejora la resistencia al impacto a baja temperatura y la tenacidad general; y para aplicaciones en entornos de alta temperatura, podría ser necesario aumentar el contenido de molibdeno.
Esta puesta a punto de elementos no sólo aborda necesidades industriales específicas sino que también conduce a la creación de nuevos tipos de acero inoxidable diseñados para aplicaciones específicas.
Ejemplo: acero inoxidable utilizado en la nave espacial de Musk
SpaceX de Elon Musk ha adoptado una innovadora aleación de acero inoxidable (acero inoxidable 30X) para su proyecto Starship. SpaceX afirma que el acero inoxidable 30X es un nuevo tipo de acero inoxidable de la serie 300 diseñado específicamente para Starship, que ofrece una mayor tenacidad a bajas temperaturas en comparación con el acero inoxidable 304L tradicional, al tiempo que mantiene la resistencia y la estabilidad a altas temperaturas.
La innovadora aplicación de SpaceX no sólo demuestra el potencial de ajustar las composiciones químicas para optimizar las propiedades del acero inoxidable, sino que también resalta la importancia de los materiales avanzados en la industria aeroespacial moderna. Gracias a estos avances, el desarrollo de aleaciones de acero inoxidable está ampliando gradualmente los límites de los materiales industriales, ofreciendo más posibilidades para aplicaciones en condiciones extremas.
Tecnologías de fabricación avanzadas: la dirección futura del acero inoxidable
Técnicas de fusión de alta eficiencia y ahorro de energía:
La producción moderna de acero inoxidable utiliza hornos de arco eléctrico (EAF) y hornos de inducción equipados con sistemas de control avanzados. Estas tecnologías mejoran la precisión de la fusión, mejoran la pureza de los materiales y reducen el consumo de energía y el impacto ambiental.
Avances en técnicas de refinación y eliminación de impurezas:
Las tecnologías de descarburación con oxígeno argón (AOD) y descarburación con oxígeno al vacío (VOD) eliminan eficazmente las impurezas del acero inoxidable, optimizan su composición química y mejoran sus propiedades mecánicas y su resistencia a la corrosión.
Control preciso de las fases microestructurales:
Al controlar las velocidades de enfriamiento y las temperaturas de recocido durante el tratamiento térmico, se puede ajustar la proporción de austenita a ferrita para lograr propiedades mecánicas y resistencia a la corrosión óptimas.
Tecnología de colada continua:
La colada continua transforma la producción de acero inoxidable al automatizar la fundición de acero fundido en palanquillas y desbastes. Este método mejora el rendimiento, reduce el consumo de energía y garantiza la consistencia del producto, minimizando los defectos asociados con la fundición de lingotes tradicional.
Impresión láser 3D y otras tecnologías de fabricación aditiva:
La fabricación aditiva, incluida la fusión selectiva por láser (SLM) y la fusión por haz de electrones (EBM), permite la producción de componentes complejos de acero inoxidable con propiedades personalizadas.
Estas secciones describen las técnicas y tecnologías innovadoras que están dando forma al futuro de la producción de acero inoxidable, centrándose en la sostenibilidad, la eficiencia y las propiedades avanzadas de los materiales.
Conclusión
La utilización de acero inoxidable ha aumentado notablemente la eficiencia industrial y ha prolongado la vida útil de los productos, lo que también ha producido efectos medioambientales positivos. Debido a su reciclabilidad, el acero inoxidable ayuda a reducir los residuos industriales y la demanda de materias primas, apoyando prácticas industriales sostenibles.
Además, el acero inoxidable mejora significativamente la calidad de vida. Su uso generalizado, desde instrumentos médicos hasta electrodomésticos de cocina, ha hecho que la vida cotidiana sea más saludable y cómoda. Además, su uso en estructuras de seguridad pública, como vehículos e instalaciones de transporte, ha mejorado la seguridad pública.
En conclusión, el acero inoxidable no es sólo un pilar fundamental de la industria moderna, sino también un material crucial que impulsa a la sociedad global hacia una mayor eficiencia y sostenibilidad. Con el continuo desarrollo de nuevas tecnologías, se espera que las aplicaciones y la influencia del acero inoxidable crezcan.
Descubra más con nuestras publicaciones de blog.
Mensajes recientes
-
Mecanizado CNC de acero inoxidable: tecnologías, ventajas y guía de personalización
-
Bujes de rueda de Go-Kart: funciones, materiales, selección y mantenimiento
-
Su guía completa para cortar piezas por láser personalizadas con HDC
-
Todo lo que debe saber antes de utilizar productos de titanio personalizados
-
¿Qué es la forja de metales?