A Comprehensive Understanding of Stainless Steel: Past, Present, and Future
The Origins and History of Stainless Steel: A Timeline
- In 1794: French chemist Louis Nicolas Vauquelin, while studying crocoite ore (lead chromate), successfully produced chromium trioxide (CrO3) by mixing the ore with hydrochloric acid. In 1797, he managed to isolate metallic chromium by heating this oxide in a charcoal furnace. For this, Vauquelin is credited as the true discoverer of the element chromium.
- In the early 1800s: British scientists James Stoddart, Michael Faraday, and Robert Mallet observed the resistance of chromium-iron alloys to oxidizing agents.
- 1821: Pierre Berthier discovered the corrosion resistance of chromium-iron alloys to certain acids and suggested their use in cutlery manufacturing.
- 1840s: Steel manufacturers in Sheffield, England, and Krupp in Germany were both producing chromium steel, with the latter using it to manufacture cannons in the 1850s.
- 1869: J. Baur of the Chrome Steel Works in Brooklyn produced chromium-containing steel for the construction of bridges in the United States for the first time, and obtained a US patent for chromium steel in 1869. Subsequently, the British scientists John T. Woods and John Clark recognized the importance of chromium content for the corrosion resistance of chromium alloys, noting that the chromium content should be within 5-30%.
- Late 1890s: German chemist Hans Goldschmidt developed an aluminothermic (thermite) process for producing carbon-free chromium.
- 1904 ~1911:Some researchers, particularly Leon Guillet of France, prepared alloys that are considered to be stainless steel today.
- 1911: Philip Monnartz reported on the relationship between chromium content and corrosion resistance.
- 1912: Krupp engineers Benno Strauss and Eduard Maurer patented austenitic stainless steel (known today as 18/8 or AISI type 304).
- 1912: While seeking a corrosion-resistant alloy for gun barrels, Harry Brearley in Sheffield, England, discovered what is now known as AISI type 420 martensitic stainless steel.
- 1915: Harry Brearley’s discovery was announced in The New York Times. He later collaborated with Haynes and, with a group of investors, founded the American Stainless Steel Corporation in Pittsburgh, Pennsylvania.
Stainless Steel Elemental Composition: The Key to Rust Prevention
Stainless steel is primarily composed of iron, chromium, nickel, molybdenum, vanadium, and other common alloying elements. Iron generally constitutes about 70% to 80% of stainless steel, providing the necessary structural strength. Chromium is crucial for rust resistance in stainless steel; at least 10.5% chromium is required for steel to be considered stainless, as it is essential for forming a stable, dense layer of chromium oxide on the surface. This layer is very stable and impermeable, effectively preventing the penetration of oxygen and moisture when exposed to air or water, significantly enhancing the steel’s corrosion resistance.
Nickel content is usually between 8% to 10%, enhancing the corrosion resistance, formability, and strength of stainless steel, and helping to maintain the non-magnetic qualities of austenitic stainless steel at low temperatures. The typical content of molybdenum ranges from 2% to 3%, which enhances resistance to pitting and crevice corrosion, particularly beneficial in chlorinated conditions. Elements such as vanadium and titanium are usually present in very low amounts, typically not exceeding 0.5%. They strengthen stainless steel by forming fine carbides, such as vanadium carbide (VC) and titanium carbide (TiC), which stabilize the structure and enhance hardness and strength. These carbides are critically important for improving the overall performance of stainless steel due to their high hardness and wear resistance. By carefully adjusting the proportions of these elements, stainless steel can perform optimally in a variety of harsh environments.
In-depth Analysis of the Most Commonly Used 304 Stainless Steel: Composition and Properties
304 Stainless Steel is one of the most versatile and widely used austenitic stainless steel, known for its excellent corrosion resistance and formability.
Composition of 304 Stainless Steel:
% | 304 | 304L | 304H |
C | 0.0 – 0.07 | 0.0 – 0.03 | 0.04 – 0.08 |
Mn | 0.0 – 2.0 | 0.0 – 2.00 | 0.0 – 2.0 |
Si | 0.0 – 1.00 | 0.0 – 1.00 | 0.0 – 1.0 |
P | 0.0 – 0.05 | 0.0 – 0.05 | 0.0 – 0.04 |
S | 0.0 – 0.03 | 0.0 – 0.02 | 0.0 – 0.02 |
Cr | 17.50 – 19.50 | 17.50 – 19.50 | 17.00 – 19.00 |
Ni | 8.00 – 10.50 | 8.00 – 10.50 | 8.00 – 11.00 |
Fe | Balance | Balance | Balance |
N | 0.0-0.11 | 0.0-0.11 | 0.0 – 0.10 |
Properties of 304 Stainless Steel
Grade | 304 |
Tensile Strength (MPa) | 500 – 700 |
Proof Stress (MPa) | 190 |
Elongation A50 mm | 45 Min % |
Hardness Brinell | 215 Max HB |
Property | Value |
Density | 8.00 g/cm3 |
Melting Point | 1450 °C |
Modulus of Elasticity | 193 GPa |
Electrical Resistivity | 0.72 x 10-6 Ω.m |
Thermal Conductivity | 16.2 W/m.K |
Thermal Expansion | 17.2 x 10-6/K |
Microscopic Perspective: The Rust Prevention Mechanism of Stainless Steel
Metal corrosion refers to the damage caused by the combined effects of chemical, physical, mechanical, or biological factors in its environment. Atmospheric corrosion, which is the deterioration of metal materials or structures due to chemical or electrochemical reactions under atmospheric conditions, is the most common type of corrosion. Globally, over 60% of steel is used in atmospheric conditions, including steel beams, rails, various mechanical equipment, and vehicles. The metal loss due to atmospheric corrosion typically accounts for more than 50% of the total corrosion damage.
In standard metal corrosion, iron loses electrons (oxidizes) and is transformed into iron ions, which then react with water to form hydrated ferric oxides (rust).
In stainless steel, which contains a high content of chromium, the chromium reacts with oxygen in the environment (either air or water) to form a thin and stable chromium oxide layer on the metal surface. This chromium oxide layer is incredibly thin yet highly adherent, effectively preventing the migration of electrons necessary for iron oxidation and physically isolating the iron from environmental oxidants.
Should the oxide layer be mechanically damaged or chemically disrupted temporarily, the chromium in the stainless steel can spontaneously regenerate the oxide film and repassivate the surface. This self-healing characteristic is crucial in environments where the metal is frequently subjected to wear or severe chemical exposure.
The alloy composition of stainless steel typically includes nickel and molybdenum, which enhance the stability of the oxide film, particularly in chloride-containing environments (such as coastal areas or de-icing salt conditions), reducing the risk of pitting and crevice corrosion. The stability of the oxide layer is maintained even in acidic or highly oxidizing conditions, making stainless steel suitable for a wide range of atmospheric conditions.
Limitations of Stainless Steel: When Does It Corrode?
- Chlorides: Chlorides, especially at high temperatures, can compromise the passivation layer of stainless steel, leading to localized corrosion and pitting. This is commonly seen in marine environments and with de-icing salts used on roads during winter.
- Strong Acids: While stainless steel can withstand corrosion from weak acids, strong acids such as sulfuric and hydrochloric acid can rapidly penetrate its passivation layer, causing significant corrosion.
- Strong Oxidizers: Strong oxidizers like peroxides and certain acids (e.g., nitric acid) can accelerate the corrosion process in stainless steel.
- Low Oxygen Environments: In environments with insufficient oxygen supply, such as soil and sludge, the passivation layer of stainless steel cannot regenerate effectively, increasing the risk of corrosion.
- High-Temperature Conditions: At high temperatures, the passivation layer of stainless steel may crack or become unstable, accelerating the corrosion process, particularly in the presence of corrosive substances.
- Mechanical Stress: Stress corrosion cracking can occur when stainless steel is subjected to tensile stress and corrosive environments simultaneously, especially in the presence of chlorides.
- Microbial Activity: In some cases, the metabolic processes of microorganisms (such as bacteria) can produce corrosive substances. This phenomenon, known as microbiologically induced corrosion (MIC), can lead to the formation of biofilms on the surface of stainless steel, promoting corrosion.
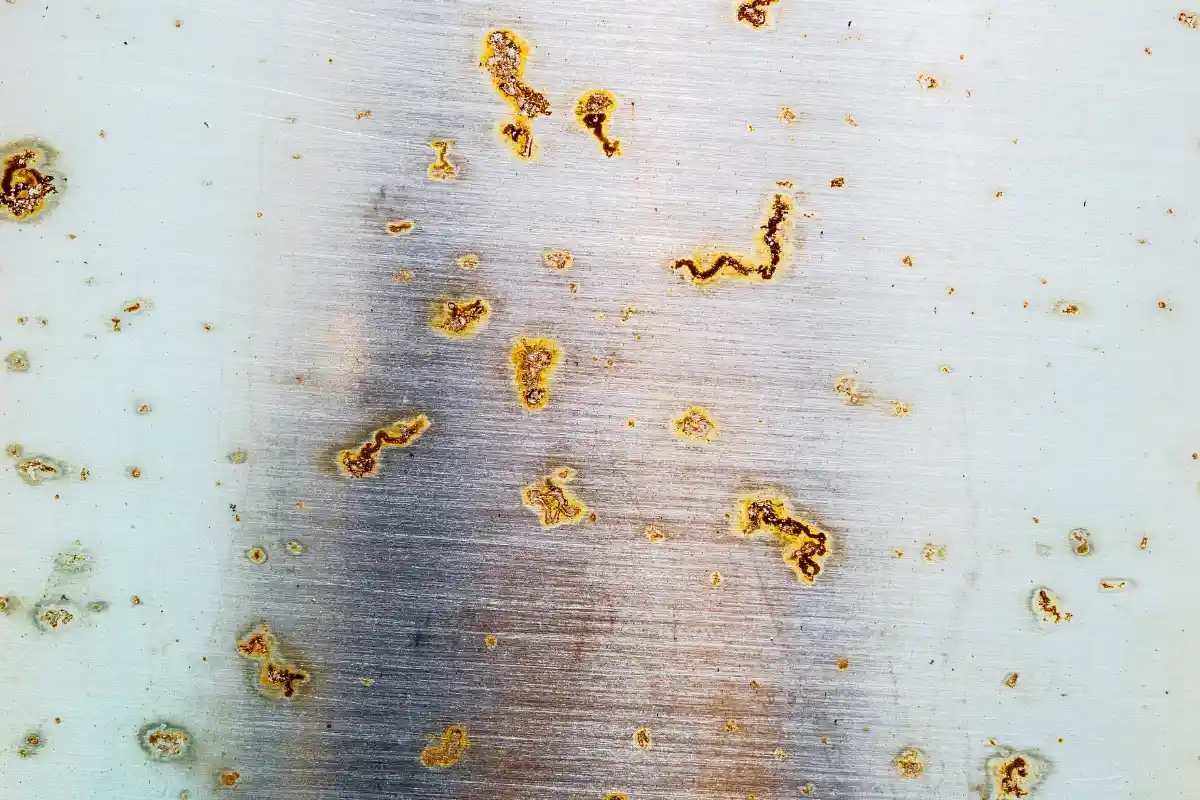
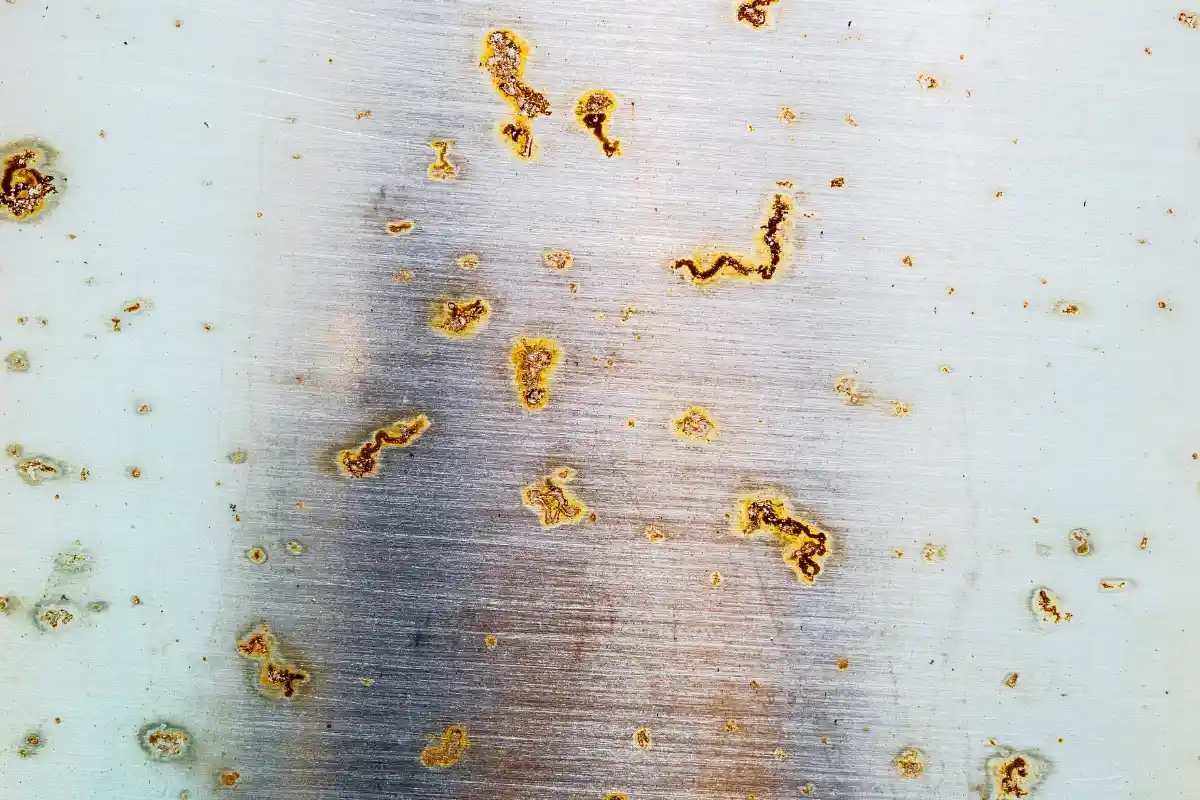
Stainless Steel Standards: Grading Stainless Steel
There are several mainstream stainless steel grading standards worldwide, established by different standardization organizations to meet the needs of various industrial and commercial applications.
- United States Standards (AISI/ASTM): AISI (American Iron and Steel Institute) and ASTM (American Society for Testing and Materials) are common stainless steel classifications that include the 300 series (such as 304, 316), 400 series, and more. These standards are widely used across the United States and globally.
- European Standards (EN/ISO): EN (European Norm) standards are issued by the European Committee for Standardization, covering various aspects of stainless steel, such as 1.4301 for 304, 1.4401 for 316, etc. Additionally, ISO (International Organization for Standardization) also publishes widely influential stainless steel standards.
- German Standards (DIN): German Industrial Standards (DIN) are well-known internationally, especially within the engineering and manufacturing sectors in Europe and Asia.
- Japanese Standards (JIS): JIS (Japanese Industrial Standards) are particularly popular in Asia, especially in the electronics and automotive manufacturing industries.
- British Standards (BS): British Standards (BS) are developed by the British Standards Institution. Although their direct global impact may not be as extensive as ASTM or EN, they still hold significant relevance in the UK and many Commonwealth countries.
- Chinese Standards (GB): China’s National Standards (GB) are frequently used in products manufactured and exported from China, often aligning with and referencing international standards.
Here are some comparisons of stainless steel grades according to different standards:
China(GB) | Russi(GOST) | American(ASTM) | German(DIN) | ISO |
1Cr17Mn6Ni5N | – | 201 | X12CrMnNiN 17-7-5 | A-2 |
1Cr18Mn8Ni5N | 12KH17G9AH4 | 202 | X12CrMnNiN 18-9-5 | A-3 |
1Cr17Ni7 | – | 301 | – | 14 |
1Cr18Ni9 | 12KH18H9 | 302 | DIN17440-96 X12CrNi18-9 | 12 |
Y1Cr18Ni9 | – | 303 | X12CrNiS18-9 | 17 |
0Cr18Ni9 | 08KH18H10 | 304 | X5CrNi18-10 | 11 |
00Cr19Ni11 | 03KH18H11 | 304L | X2CrNi19-11 | 10 |
1Cr18Ni12 | 12KH18H12T | 305 | X4CrNi18-12 | 13 |
0Cr17Ni12Mo2 | 08KH17H13M2T | 316 | X5CrNiMo17-12-2 | 20/20a |
0Cr18Ni12Mo2Ti | 08KH17H13M2T | 316Ti S31635 | X6CrNiMoTi17-12-2 | 21 |
00Cr17Ni14Mo2 | 03KH17H14M2 | 316L | X2CrNiMo18-14-3 | 19/19a |
0Cr19Ni13Mo3 | 08KH17H15M3T | 317 | X5CrNiMo17-13-3 | – |
1Cr18Ni9Ti | 12KH18H10T | 321 | X6CrNitI18-10 | 11 |
0Cr18Ni10Ti | 08KH18H10T | 321 | X6CrNiTi18-10 | 15 |
0Cr18Ni11Nb | 08KH18H12B | 347 | X6CrNiNb18-10 | 16 |
0Cr13Al | – | 405 | X6CrAl13 | 5 |
1Cr17 | 12KH17 | 430 | X6Cr17 | 8 |
1Cr12 | 403 | X6Cr13 | 3 | |
1Cr13 | 12KH13 | 410 | X12Cr13 | 3 |
0Cr13Ae | 405 | X6Cr13 | 1 | |
2Cr13 | 20KH13 | 420 | X20Cr13 | 4 |
3Cr13 | 30KH13 | 420 | X30Cr13 | 5 |
1Cr17Ni2 | 14KH17H2 | 431 | X17CrNi16-2 | 96 |
Stainless Steel Testing Methods
- Magnetic Testing: Most stainless steels, especially austenitic types like 304 and 316, are non-magnetic under normal conditions. Testing with a magnet to see if the material is attracted can preliminarily indicate if it is austenitic stainless steel. This method is simple and quick, suitable for rapid on-site identification. However, it should be noted that cold working can induce a slight martensitic structure in some stainless steels, causing mild magnetism.
- Reagent Testing: This involves using specific chemical reagents that react with metal ions in stainless steel to observe changes in color for component identification. For example, iron ion tests turn blue, nickel-specific reagents react to show pink to red, and chromium-specific reagents turn yellow to green upon reaction. This method is low-cost, easy to operate, and suitable for rapid field applications.
- Spectrometer Testing: Spectrometers analyze the specific wavelengths of light emitted or absorbed by a material to accurately determine its chemical composition. For instance, using the Olympus handheld XRF analyzer to test stainless steel accurately identifies elements like iron, chromium, and nickel. This technology is suited for high-precision applications requiring detailed compositional analysis.
It is important to note that the above testing methods can only analyze the composition of the metal surface. For thicker or solid stainless steel products, these methods are not capable of accurately detecting the internal composition. Therefore, the best strategy to prevent purchasing counterfeit stainless steel materials or products is to choose reliable suppliers who provide material certifications.
Stainless Steel Advantages and Challenges
Stainless steel is renowned for its exceptional corrosion resistance, high strength, and aesthetic appeal, making it suitable for a variety of applications, from architectural designs to industrial equipment. It also offers excellent heat resistance and is 100% recyclable, aligning well with sustainable practices.
Despite its benefits, stainless steel can be cost-prohibitive, especially for large-scale projects, and its high strength often necessitates specialized machining tools and techniques. Additionally, its poor thermal conductivity and susceptibility to stress corrosion cracking in specific environments like those containing chlorides can limit its use in certain applications.
How Various Elements Are Combined to Form Stainless Steel


- Melting and Alloying: Stainless steel production begins with the melting process. Raw materials typically include steel from ore smelting directly used for stainless steel production, recycled stainless steel, and ferroalloys such as ferronickel. These materials are heated in an electric furnace until they melt at high temperatures, during which alloying elements like chromium and nickel are added to ensure the molten steel achieves the specified chemical composition.
- Removing Excess Carbon: An Argon Oxygen Decarburization (AOD) furnace is typically used to blow oxygen into the molten steel under standard atmospheric pressure while also injecting inert gases (Ar, N2). This process refines and decarburizes by adjusting the argon/oxygen ratio, reducing the CO partial pressure, thereby lowering the carbon content to a very low level and preventing the oxidation of chromium in the steel.
- Casting: After conditioning and Stirring, the molten steel is poured into molds to solidify into slabs or ingots.
- Hot and Cold Rolling:
- Starting with slabs, which are heated and then processed through roughing and finishing rolling mills to form strip steel.
- The hot steel strip is cooled to a preset temperature in a laminar flow and then coiled by a coiler.
- The cooled coil has an oxidized surface, which is removed by annealing and pickling.
- Some hot-rolled products are used directly, while others are processed further into cold-rolled products.
- Cold rolling involves using hot-rolled products with a thickness of 3.0-5.5mm, which are then rolled using cold rolling equipment.
- After cold rolling, the stainless steel is annealed to eliminate work hardening caused by rolling.
- Pickling removes the oxide layer formed during annealing and carries out passivation treatment to improve the corrosion resistance of the steel plate.
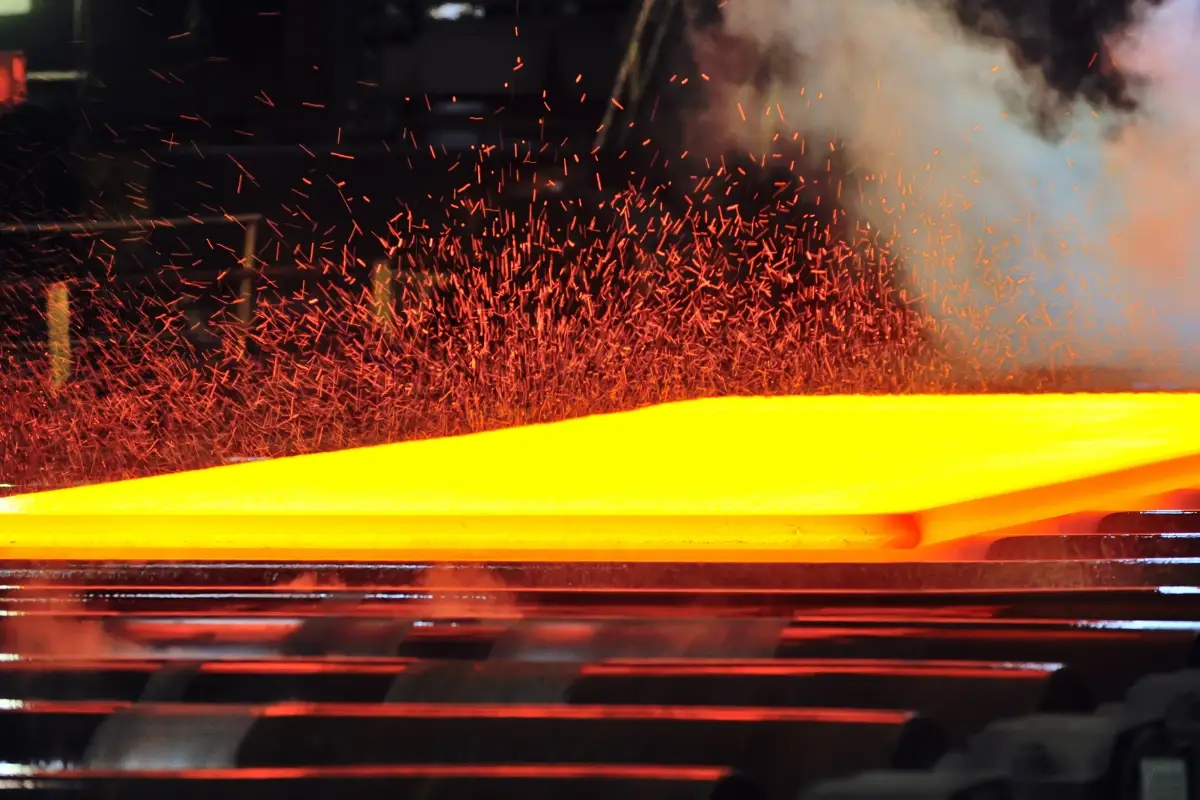
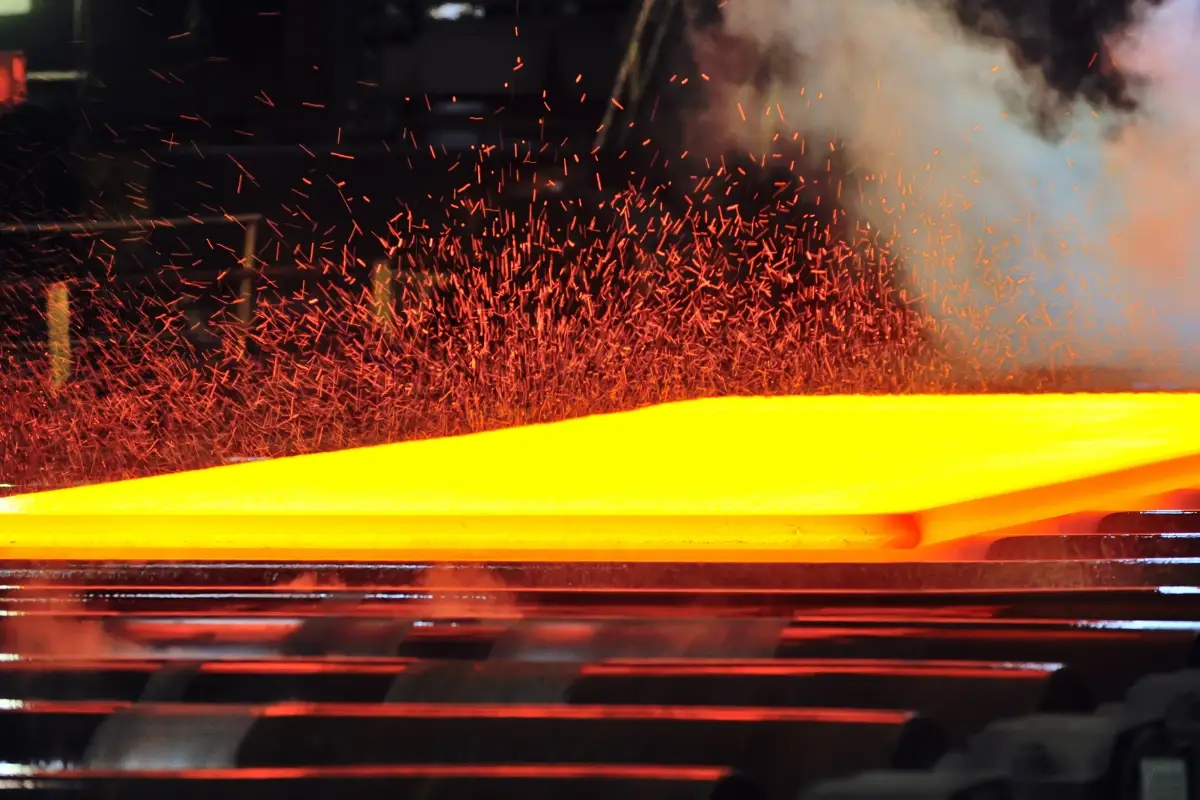
Innovative Development of Stainless Steel Alloys
Innovating Stainless Steel Alloys Through Elemental Ratio Adjustment
The performance of stainless steel alloys can be optimized and innovated by adjusting the ratios of elements in their chemical composition. By increasing or decreasing the content of key elements such as chromium, nickel, molybdenum, and titanium, significant changes can be made to the mechanical properties, corrosion resistance, and thermal stability of stainless steel. For example, increasing the content of chromium enhances the oxidation resistance and corrosion resistance; adding more nickel improves low-temperature impact resistance and overall toughness; and for applications in high-temperature environments, increasing molybdenum content might be necessary.
This fine-tuning of elements not only addresses specific industrial needs but also leads to the creation of new types of stainless steel designed for specific applications.
Example: Stainless Steel Used in Musk’s Starship
Elon Musk’s SpaceX has adopted an innovative stainless steel alloy—30X stainless steel—for its Starship project. SpaceX claims that 30X stainless steel is a new type of 300 series stainless steel designed specifically for the Starship, which offers better toughness at low temperatures compared to traditional 304L stainless steel, while maintaining strength and stability at high temperatures.
SpaceX’s innovative application not only demonstrates the potential of adjusting chemical compositions to optimize stainless steel properties but also highlights the importance of advanced materials in the modern aerospace industry. Through such advancements, the development of stainless steel alloys is gradually pushing the boundaries of industrial materials, providing more possibilities for applications under extreme conditions.
Advanced Manufacturing Technologies: The Future Direction of Stainless Steel
High-Efficiency, Energy-Saving Melting Techniques:
Modern stainless steel production utilizes Electric Arc Furnaces (EAFs) and induction furnaces equipped with advanced control systems. These technologies enhance the precision of melting, improve the purity of materials, and reduce energy consumption and environmental impact.
Advancements in Refining and Impurity Removal Techniques:
Argon Oxygen Decarburization (AOD) and Vacuum Oxygen Decarburization (VOD) technologies effectively remove impurities from stainless steel, optimize its chemical composition, and enhance its mechanical properties and corrosion resistance.
Precise Control of Microstructural Phases:
By controlling the cooling rates and annealing temperatures during heat treatment, the ratio of austenite to ferrite can be adjusted to achieve optimal mechanical properties and corrosion resistance.
Continuous Casting Technology:
Continuous casting transforms stainless steel production by automating the casting of molten steel into billets and slabs. This method improves yield, reduces energy consumption, and ensures product consistency, minimizing the defects associated with traditional ingot casting.
Laser 3D Printing and Other Additive Manufacturing Technologies:
Additive manufacturing, including selective laser melting (SLM) and electron beam melting (EBM), enables the production of complex stainless steel components with customized properties.
These sections outline the innovative techniques and technologies that are shaping the future of stainless steel production, focusing on sustainability, efficiency, and advanced material properties.
Conclusion
The utilization of stainless steel has markedly boosted industrial efficiency and prolonged the lifespan of products, also yielding positive environmental effects. Due to its recyclability, stainless steel aids in reducing industrial waste and the demand for raw materials, supporting sustainable industrial practices.
Furthermore, stainless steel significantly enhances the quality of life. Its widespread use from medical instruments to kitchen appliances has made everyday life healthier and more convenient. Additionally, its use in public safety structures, such as transportation vehicles and facilities, has improved public safety.
In conclusion, stainless steel is not just a fundamental pillar of modern industry but also a crucial material driving global society towards greater efficiency and sustainability. With the continuous development of new technologies, the applications and influence of stainless steel are only expected to grow.