- Heim
- Ressourcen
- Bloggen
- Präzisionsdruckgusstechniken
Fortschrittliches Druckgussverfahren: Schlüssel zu hochpräzisen Komponenten
Entdecken Sie die Präzision und Vielseitigkeit des Druckgusses, einer beliebten Fertigungstechnik, bei der geschmolzenes Metall in hochwertige Teile gegossen wird, die in verschiedenen Branchen verwendet werden. Dieser Artikel beleuchtet die Prozesse, Vorteile und Materialien des Druckgusses.
Druckguss verstehen
Beim Druckguss handelt es sich um eine Fertigungstechnik, bei der geschmolzenes Metall mit Kraft in eine Form eingespritzt wird, wodurch sorgfältig geformte Komponenten entstehen. Druckguss ist bekannt für seine Fähigkeit, komplizierte Designs mit unübertroffener Präzision zu realisieren, und erweist sich als bevorzugte Option für Branchen, die höchste Qualität bei ihren Produkten anstreben.
Vorteile von Druckguss
Die Verbreitung des Druckgusses in verschiedenen Branchen lässt sich auf eine Vielzahl von Vorteilen zurückführen, die er mit sich bringt. Zu den entscheidenden Vorteilen gehören:
- Hohe Präzision und Maßhaltigkeit:Ermöglicht die Herstellung komplexer Komponenten mit außergewöhnlicher Präzision und strengen Toleranzen.
- Hervorragende Oberflächenqualität:Erzeugt glatte Oberflächen und minimiert die Notwendigkeit zusätzlicher Nachbearbeitungsverfahren.
- Robustheit und Langlebigkeit: Ergibt Komponenten mit hervorragenden mechanischen Eigenschaften, ideal für Anwendungen mit anspruchsvollen Leistungsanforderungen.
- Hohe Produktionsraten: Schnelle Produktion großer Mengen durch schnelle Erstarrung der Metallschmelze.
- Kostengünstig für große Auflagen: Kosteneffizient für die Massenproduktion, nachdem die anfänglichen Werkzeug- und Formkosten abgedeckt sind.
- Vielseitige Legierungsoptionen: Unterstützt eine breite Palette von Metalllegierungen und ermöglicht so eine maßgeschneiderte Materialauswahl.
- Reduzierter Materialabfall:Präzision minimiert Materialverschwendung und trägt so zu Umwelt- und Kostenvorteilen bei.
- Konsistenz und Wiederholbarkeit:Gewährleistet Einheitlichkeit und Zuverlässigkeit innerhalb der Produktionsläufe.
- Komplexe Geometrien: Geeignet für komplizierte Teile mit komplexen Formen und Merkmalen.
Arten von Druckguss
Druckgussverfahren werden hauptsächlich in zwei Typen eingeteilt: Warmkammer-Druckguss und Kaltkammer-Druckguss, die sich durch ihre Ansätze zum Schmelzen und Übertragen von Metall in die Druckgussmaschine unterscheiden.
Warmkammer-Druckguss:
Beim Warmkammer-Druckguss wird das Einspritzsystem in ein Bad aus geschmolzenem Metall getaucht. Diese Methode wird üblicherweise für Legierungen mit niedrigeren Schmelzpunkten wie Zink, Zinn und Blei eingesetzt. Der Einspritzmechanismus oder Kolben wird in geschmolzenes Metall eingetaucht und beim Zurückziehen wird geschmolzenes Metall in die Kammer gesaugt. Dieses Verfahren zeichnet sich durch seine Schnelligkeit aus und eignet sich gut für kleinere Bauteile, die von kurzen Zykluszeiten profitieren.
Kaltkammer-Druckguss:
Kaltkammer-Druckguss ist auf Legierungen mit höheren Schmelzpunkten zugeschnitten, darunter Aluminium, Messing und Magnesium. Im Gegensatz zum Warmkammer-Druckguss unterscheidet sich das Einspritzsystem beim Kaltkammer-Druckguss vom geschmolzenen Metallbad. Geschmolzenes Metall wird in die Kaltkammer gegossen und dann unter hohem Druck in den Formhohlraum gedrückt. Dieses Verfahren ist besonders vorteilhaft für größere und komplexere Teile, die die Verwendung von Legierungen mit hohem Schmelzpunkt erfordern.
Druckguss im Vergleich zu anderen Gießverfahren
Hier ein Vergleich des Druckgusses mit anderen gängigen Gießverfahren:
Druckguss:
Vorteile: Hohe Präzision, hervorragende Oberflächengüte, kürzere Zykluszeiten, ideal für die Massenproduktion.
Nachteile: Höhere Werkzeugkosten, begrenzte Legierungsoptionen, weniger flexibel für kleine Serien.
Sandguss:
Vorteile: Geringere Werkzeugkosten, vielseitig für Legierungen und Teilegrößen, geeignet für Prototypen und Kleinserienfertigung.
Nachteile: Geringere Präzision, rauere Oberflächenbeschaffenheit, längere Zykluszeiten, arbeitsintensiver.
Vorteile: Hervorragende Oberflächengüte, gute Maßhaltigkeit, geeignet für komplexe und detaillierte Teile.
Nachteile: Langsamere Produktionsraten, höhere Werkzeugkosten, weniger kosteneffektiv für die Produktion in großem Maßstab.
Schwerkraftguss:
Vorteile: Geringere Werkzeugkosten, geeignet für verschiedene Legierungen, gut für die Produktion mittlerer bis hoher Stückzahlen.
Nachteile: Langsamere Produktionsraten, geringere Präzision als beim Druckguss, möglicherweise eine zusätzliche Nachbearbeitung erforderlich.
Schleuderguss:
Vorteile: Geeignet für zylindrische Teile, gute metallurgische Eigenschaften, kann eine dichte Struktur erreichen.
Nachteile: Beschränkt auf bestimmte Geometrien, längere Zykluszeiten, weniger präzise als Druckguss.
Die Wahl zwischen Druckguss und anderen Gussverfahren hängt von den spezifischen Anforderungen der Anwendung ab, einschließlich Materialeigenschaften, Teilekomplexität, Produktionsvolumen und Budgetbeschränkungen. Jede Methode hat ihre Stärken und Grenzen, sodass sie für verschiedene Fertigungsszenarien geeignet ist.
Materialien, die beim Druckguss verwendet werden
Druckguss ist ein vielseitiger Prozess, der verschiedene Materialien verarbeiten kann. Aufgrund ihrer spezifischen Eigenschaften und ihrer Eignung für den Druckgussprozess werden jedoch bestimmte Legierungen häufiger verwendet. Zu den gängigsten Materialien für den Druckguss gehören:
Aluminiumlegierungen:
Aufgrund seiner geringen Dichte, seines hohen Festigkeits-Gewichts-Verhältnisses, seiner Korrosionsbeständigkeit und seiner Wärmeleitfähigkeit wird es häufig verwendet.
Gängige Legierungen: A380, A383, A360, ADC12.
Zinklegierungen:
Beliebt für kleinere Bauteile, bietet es hohe Präzision, hervorragende Gusseigenschaften und eine gute Oberflächengüte.
Gängige Legierungen: Zamak 3, Zamak 5, Zamak 7.
Magnesiumlegierungen:
Wird für leichte Komponenten verwendet, die eine hohe Festigkeit erfordern, mit Vorteilen wie geringer Dichte und guter Bearbeitbarkeit.
Gängige Legierungen: AZ91D, AM60B.
Kupferlegierungen
Wird im Druckgussverfahren für hervorragende Leitfähigkeit und Korrosionsbeständigkeit verwendet.
Gängige Legierungen: C87500, C95800.
Blei- und Zinnlegierungen:
Wird in spezifischen Anwendungen eingesetzt, bei denen niedrige Schmelzpunkte von Vorteil sind.
Beispiele hierfür sind Pb-Sn-Legierungen (Blei-Zinn).
Druckgussverfahren erklärt
Hier ein Überblick über den Druckgussprozess:
- Formvorbereitung:Beginnen Sie mit einer präzise gefertigten Form, bestehend aus feststehenden und beweglichen Hälften aus gehärtetem Stahl.
- Klemmung: Bringen Sie die Formhälften sicher zusammen und klemmen Sie sie fest, um ihre Position während des Gießens beizubehalten.
- Einspritzen von geschmolzenem Metall: Erhitzen Sie geschmolzenes Metall (Aluminium-, Zink- oder Magnesiumlegierungen) in einem Ofen. Spritzen Sie das geschmolzene Metall unter hohem Druck in den Formhohlraum.
- Erstarrung: Lassen Sie das geschmolzene Metall in der Form schnell erstarren, um seine Form anzunehmen. Kontrollieren Sie die Abkühlzeit für die gewünschten Eigenschaften.
- Öffnen der Form:Öffnen Sie die Formhälften und werfen Sie das Gussstück in der gewünschten Form aus.
- Zuschneiden und Endbearbeitung: Schneiden Sie überschüssiges Material (Flansch) ab und stellen Sie das Teil fertig. Fügen Sie bei Bedarf Features hinzu.
- Rückgewinnung und Recycling:Recyceln Sie überschüssiges Material und Angüsse für Nachhaltigkeit und Effizienz.
Postprozess für Druckgussteile
Nach Abschluss des Druckgussprozesses werden häufig weitere Nachbearbeitungsschritte durchgeführt, um besondere Anforderungen zu erfüllen, die Qualität des Endprodukts zu verbessern und die Übereinstimmung mit den gewünschten Spezifikationen sicherzustellen. Die Nachbearbeitungsschritte für Druckgussteile können Folgendes umfassen:
- Beschneiden und Entgraten:Entfernen Sie überschüssiges Material („Flansch“) und glätten Sie die beim Gussvorgang entstandenen rauen Kanten.
- Bearbeitung: Zusätzlich ausführen Mahlen, Bohren oder Gewindeschneiden für präzise Abmessungen oder zum Erstellen spezifischer Merkmale.
- Oberflächenveredelung:Verbessern Sie das Erscheinungsbild und die Korrosionsbeständigkeit durch Methoden wie Kugelstrahlen, Gleitschleifen oder Galvanisieren.
- Wärmebehandlung:Verbessern Sie mechanische Eigenschaften wie Festigkeit und Härte durch Wärmebehandlungsprozesse.
- Qualitätskontrolle: Stellen Sie durch Maßprüfungen, Sichtprüfungen und zerstörungsfreie Prüfungen sicher, dass Druckgussteile die festgelegten Toleranzen und Qualitätsstandards einhalten.
- Montage:Fügen, schweißen oder befestigen Sie Druckgussteile mit anderen Komponenten, um fertige Produkte zu erstellen.
- Oberflächenbeschichtung oder Lackierung: Tragen Sie Beschichtungen oder Farben auf, um Farbe, Textur oder zusätzlichen Schutz vor Umwelteinflüssen zu erzielen.
Anwendungen des Druckgusses
- Unterhaltungselektronik: Gehäuse und Strukturkomponenten für Smartphones, Laptops, Kameras und Audiogeräte
- Haushaltsgeräte:Teile von Waschmaschinen, Kühlschränken und Öfen, Leuchten und Lampengehäusen
- Automobil:Motorkomponenten, Getriebegehäuse und Bremssystemteile
- Industrielle Ausrüstung:Getriebe, Pumpengehäuse und Ventilkomponenten
- Luft- und Raumfahrt:Flugzeugkomponenten, einschließlich Triebwerksteile
- Militär und Verteidigung:Waffensysteme und Fahrzeugteile
- Sportwaren:Fahrradkomponenten und Golfschläger
- Telekommunikation
- Medizinische Ausrüstung
- Möbel
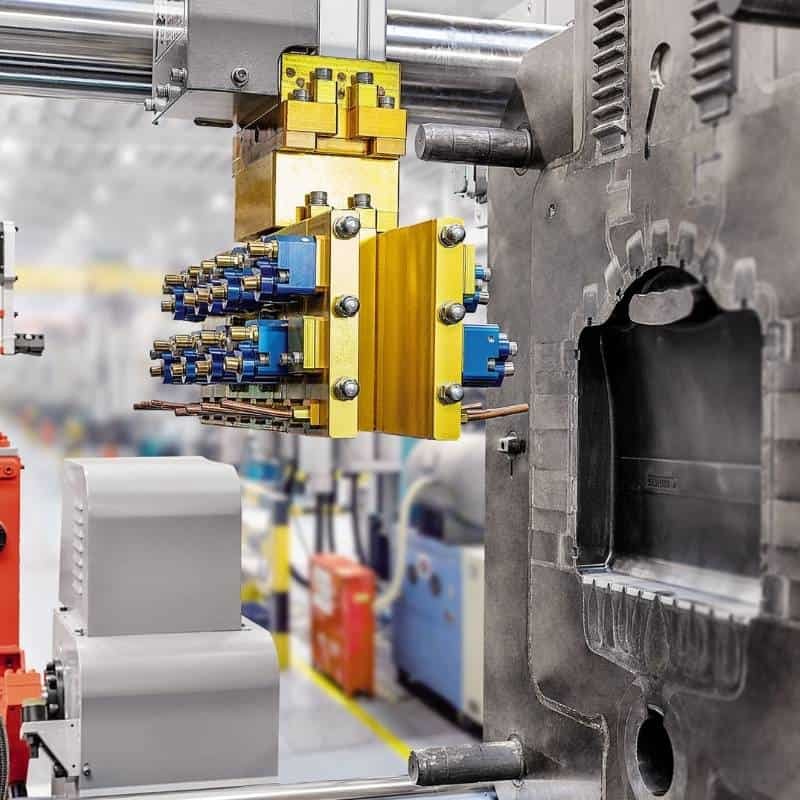
Innovationen in der Druckgusstechnik
In der Druckgusstechnik gab es in den letzten Jahren zahlreiche Innovationen mit dem Ziel, Effizienz, Präzision, Nachhaltigkeit zu verbessern und das Anwendungsspektrum zu erweitern. Einige bemerkenswerte Innovationen in der Druckgusstechnologie:
- Fortschritte beim Hochdruck-Druckguss (HPDC): Kontinuierliche Verbesserungen der Maschinen, höhere Einspritzdrücke, schnellere Zyklen und fortschrittliche Steuerungssysteme steigern die Effizienz.
- Dünnwandiger Druckguss: Innovationen bei Werkzeugen und Prozesssteuerung ermöglichen die Herstellung dünnwandigerer Komponenten, was für die Gewichtsreduzierung in Automobil- und Luft- und Raumfahrtanwendungen von entscheidender Bedeutung ist.
- Vakuumunterstützter Druckguss:Reduziert die Porosität durch die Entfernung von Gasen vor der Erstarrung, was zu verbesserten mechanischen Eigenschaften und einer besseren Oberflächenbeschaffenheit führt.
- Halbfester Druckguss:Verwendet teilweise erstarrtes Metall zur Verbesserung der mechanischen Eigenschaften, besonders vorteilhaft für Anwendungen, die Festigkeit und Präzision erfordern.
- Fortschrittliche Matrizenmaterialien: Hochleistungs-Werkzeugstähle und -Beschichtungen verbessern die Haltbarkeit der Matrizen und reduzieren so Wartungs- und Ausfallzeiten.
- Fortschrittliche Materialien und Legierungen: Die laufende Forschung wird Legierungen mit verbesserten Eigenschaften einführen, um den sich entwickelnden Anforderungen der Industrie gerecht zu werden.
- Echtzeitüberwachung und -steuerung: Durch die Integration von Sensoren und Überwachungssystemen wird der Druckguss optimiert, indem durch Echtzeitsteuerung eine gleichbleibende Teilequalität sichergestellt wird.
- 3D-Druck für die Werkzeugherstellung: Erforschung von 3d Drucken für komplizierte und komplexe Formen und bietet kostengünstige Lösungen für die Werkzeugherstellung.
- Simulationssoftware: Fortschrittliche Simulationen prognostizieren den Fluss geschmolzenen Metalls, identifizieren Fehler und simulieren den Herstellungszyklus, wodurch der Bedarf an physischen Prototypen reduziert wird.
- Legierungsentwicklung: Laufende Forschung führt neue Materialien mit verbesserten Eigenschaften ein, darunter verbesserte Festigkeit, Hitzebeständigkeit und Recyclingfähigkeit.
- Verbesserungen der Energieeffizienz: Innovationen bei energieeffizienten Ofentechnologien und nachhaltigen Praktiken tragen dazu bei, die Umweltauswirkungen des Druckgusses zu reduzieren.
- Robotik und Automatisierung:Der verstärkte Einsatz von Robotik steigert die Effizienz, senkt die Arbeitskosten und verbessert die Sicherheit bei Aufgaben wie der Teileentnahme, dem Beschneiden und der Qualitätskontrolle.
- Individualisierung und Kleinserienfertigung:Wir entwickeln uns weiter, um flexiblere und agilere Produktionsprozesse zu ermöglichen und den steigenden Anforderungen an die individuelle Anpassung gerecht zu werden.
Diese Innovationen tragen gemeinsam dazu bei, den Druckguss zu einem vielseitigeren, präziseren und nachhaltigeren Herstellungsprozess zu machen. Da die Technologie weiter voranschreitet, wird erwartet, dass weitere Entwicklungen die Zukunft des Druckgusses in verschiedenen Branchen prägen werden.
Umweltauswirkungen von Druckguss
Der Druckgussprozess hat wie jeder industrielle Herstellungsprozess Auswirkungen auf die Umwelt. Druckguss bietet zwar Vorteile hinsichtlich Effizienz und Materialausnutzung, bringt aber auch bestimmte Umweltaspekte mit sich. Es ist wichtig zu beachten, dass Fortschritte in Technologie und Branchenpraktiken sowie regulatorische Rahmenbedingungen dazu beitragen, die Umweltauswirkungen des Druckgusses zu verringern. Viele Druckgussbetriebe arbeiten aktiv an der Einführung nachhaltigerer Praktiken, wie z. B. der Verwendung energieeffizienter Geräte, der Umsetzung von Recyclingprogrammen und der Einhaltung von Umweltstandards und Zertifizierungen. Hier sind einige Aspekte der Umweltauswirkungen des Druckgusses:
- Energieverbrauch: Das Schmelzen von Metall beim Druckguss erfordert erhebliche Energie, die von Faktoren wie der Legierungsart und der Anlageneffizienz beeinflusst wird.
- Emissionen:Beim Betrieb von Hochöfen können Schadstoffe freigesetzt werden, die zur Luftverschmutzung beitragen. Moderne Anlagen nutzen jedoch Technologien, um Emissionen zu minimieren und Vorschriften einzuhalten.
- Wassernutzung: Beim Druckguss wird zum Kühlen ein gewisser Anteil an Wasser verbraucht, weshalb ein verantwortungsvolles Management erforderlich ist, um Auswirkungen auf die Umwelt zu vermeiden.
- Abfallaufkommen:Beim Druckguss entsteht Abfall, einschließlich überschüssigem Material und Ausschussteilen.
- Chemikalienverbrauch: Beim Druckguss werden Schmierstoffe und Trennmittel verwendet, deren Auswahl und Handhabung sich bei unsachgemäßer Handhabung auf die Umwelt auswirken kann.
- Recyclingfähigkeit: Druckgussmaterialien wie Aluminium und Zink sind in hohem Maße recycelbar, unterstützen eine Kreislaufwirtschaft und reduzieren die Umweltbelastung.
Tipps für hochwertigen Druckguss
Die Sicherstellung der Qualität im Druckgussprozess ist für die Herstellung zuverlässiger und präziser Bauteile von entscheidender Bedeutung. Durch die Einbeziehung der folgenden Tipps können Hersteller die Qualität ihrer Druckgussteile verbessern, Fehler reduzieren und die Gesamtproduktionseffizienz optimieren:
- Optimales Werkzeugdesign: Investieren Sie in gut konzipierte Druckgusswerkzeuge, um eine präzise Teilegeometrie zu erreichen, Fehler zu reduzieren und eine gleichmäßige Kühlung und Entlüftung sicherzustellen.
- Materialauswahl: Wählen Sie Legierungen basierend auf mechanischen Eigenschaften, Korrosionsbeständigkeit und Wärmeleitfähigkeit.
- Wartung und Schmierung der Form: Überprüfen und warten Sie die Formen regelmäßig, um Verschleiß vorzubeugen. Tragen Sie geeignete Formschmiermittel auf, um die Reibung zu reduzieren, die Teilefreigabe zu erleichtern und zur Langlebigkeit der Form beizutragen.
- Prozessoptimierung: Passen Sie die Prozessparameter für Einspritzdruck, Temperatur und Zykluszeit genau an, um die Teilequalität und Produktionseffizienz zu optimieren.
- Echtzeitüberwachung:Implementieren Sie Überwachungssysteme, um wichtige Prozessparameter zu verfolgen, Probleme frühzeitig zu erkennen und fehlerhafte Teile zu verhindern.
- Qualitätskontrollprüfungen:Führen Sie regelmäßige Kontrollen durch, einschließlich Maßkontrollen, visuelle Beurteilungen und Testmethoden, um festgelegte Toleranzen und Qualitätsstandards einzuhalten.
- Optimiertes Angusssystem: Entwerfen Sie ein effizientes Angusssystem für einen kontrollierten Metallfluss, das Turbulenzen minimiert und das Risiko von Fehlern verringert.
- Schulung und Kompetenzentwicklung: Bieten Sie den Bedienern eine angemessene Schulung, um durch qualifiziertes und sachkundiges Personal eine gleichbleibende Qualität aufrechtzuerhalten.
Kundenspezifische Druckgussteile
Wenn Sie maßgeschneiderte Druckgussteile von Herstellern beziehen möchten, finden Sie hier einige Schritte und Überlegungen, die Sie durch den Prozess führen:
- Spezifizieren Sie Ihre Anforderungen:Definieren Sie klar Ihre Anforderungen, einschließlich Material, Abmessungen, Oberflächenbeschaffenheit, Menge und etwaiger spezifischer Merkmale oder Toleranzen.
- Forschungshersteller:Identifizieren Sie seriöse Druckgusshersteller mit einschlägiger Erfahrung und Zertifizierungen in den von Ihnen gewünschten Legierungen und Prozessen.
- Angebote anfordern: Senden Sie eine detaillierte Angebotsanfrage (RFQ) an ausgewählte Hersteller und geben Sie Projektdetails für genaue Angebote an.
- Angebote bewerten: Prüfen Sie Angebote unter Berücksichtigung von Kosten, Lieferzeiten, Qualitätssicherungsmaßnahmen und Zusatzleistungen.
- Fähigkeiten bewerten: Bewerten Sie die Fähigkeiten, Erfahrungen und Erfolgsbilanz jedes Herstellers bei der Herstellung ähnlicher Komponenten.
- Qualitätskontrolle:Erkundigen Sie sich nach Qualitätssicherungsprozessen und Zertifizierungen, um die Einhaltung von Industriestandards sicherzustellen.
- Besuchseinrichtungen (falls möglich): Erwägen Sie einen Besuch in Produktionsstätten, um sich die Ausrüstung, Prozesse und Gesamtfähigkeiten aus erster Hand anzusehen.
- Kommunikation: Stellen Sie eine klare Kommunikation her, besprechen Sie Anforderungen und potenzielle Herausforderungen und sorgen Sie für gegenseitiges Verständnis.
- Prototyp entwickeln:Fordern Sie Prototypen oder Muster an, um die Qualität zu beurteilen und Anpassungen vor der Serienproduktion vorzunehmen.
- Konditionen aushandeln: Verhandeln Sie Bedingungen, einschließlich Preise, Lieferzeiten, Zahlungsbedingungen und andere Vertragsaspekte.
- Vertragliche Vereinbarung:Formulieren Sie die Vereinbarung mit einem Vertrag und dokumentieren Sie Spezifikationen, Lieferpläne und Qualitätsstandards.
- Überwachung der Produktion: Bleiben Sie während der gesamten Produktion engagiert und erhalten Sie regelmäßige Updates, um etwaige Probleme umgehend zu beheben.
- Qualitätskontrolle:Führen Sie beim Erhalt der Teile gründliche Qualitätsprüfungen durch, einschließlich Maßprüfungen und visueller Beurteilungen.
- Feedback und Verbesserung: Geben Sie den Herstellern Feedback, um zukünftige Kooperationen und kontinuierliche Verbesserungen zu verbessern.
Wenn Sie diese Schritte befolgen und eine offene Kommunikation mit dem ausgewählten Hersteller pflegen, können Sie die Wahrscheinlichkeit erhöhen, qualitativ hochwertige, maßgeschneiderte Druckgussteile zu erhalten, die Ihren spezifischen Anforderungen entsprechen.
Fazit
Druckguss ist ein Eckpfeiler der modernen Fertigung und bietet Präzision, Effizienz und Haltbarkeit. Seine Auswirkungen wirken sich branchenübergreifend aus und prägen die Produkte, auf die wir uns täglich verlassen. Mit dem technologischen Fortschritt werden auch die Möglichkeiten des Druckgusses zunehmen, was seine anhaltende Relevanz in der sich ständig weiterentwickelnden Landschaft der Präzisionsfertigung sicherstellt.