- Heim
- Ressourcen
- Bloggen
- Was ist Nulltoleranzbearbeitung
Zero Tolerance Machining: Revolutionizing Precision Engineering
- Von: HDCMFG
In the world of modern manufacturing, precision is everything. The demand for high-performance parts in aerospace, medical, automotive, and electronics industries continues to push the boundaries of what is possible.
One concept that has emerged as a game-changer is Zero Tolerance Machining (ZTM)—a philosophy and approach that aims to achieve near-perfect precision with minimal deviation. In this blog, we’ll explore what Zero Tolerance Machining means, its benefits, real-world applications, and how it is driving innovation in high-precision industries.
Understanding Zero Tolerance Machining
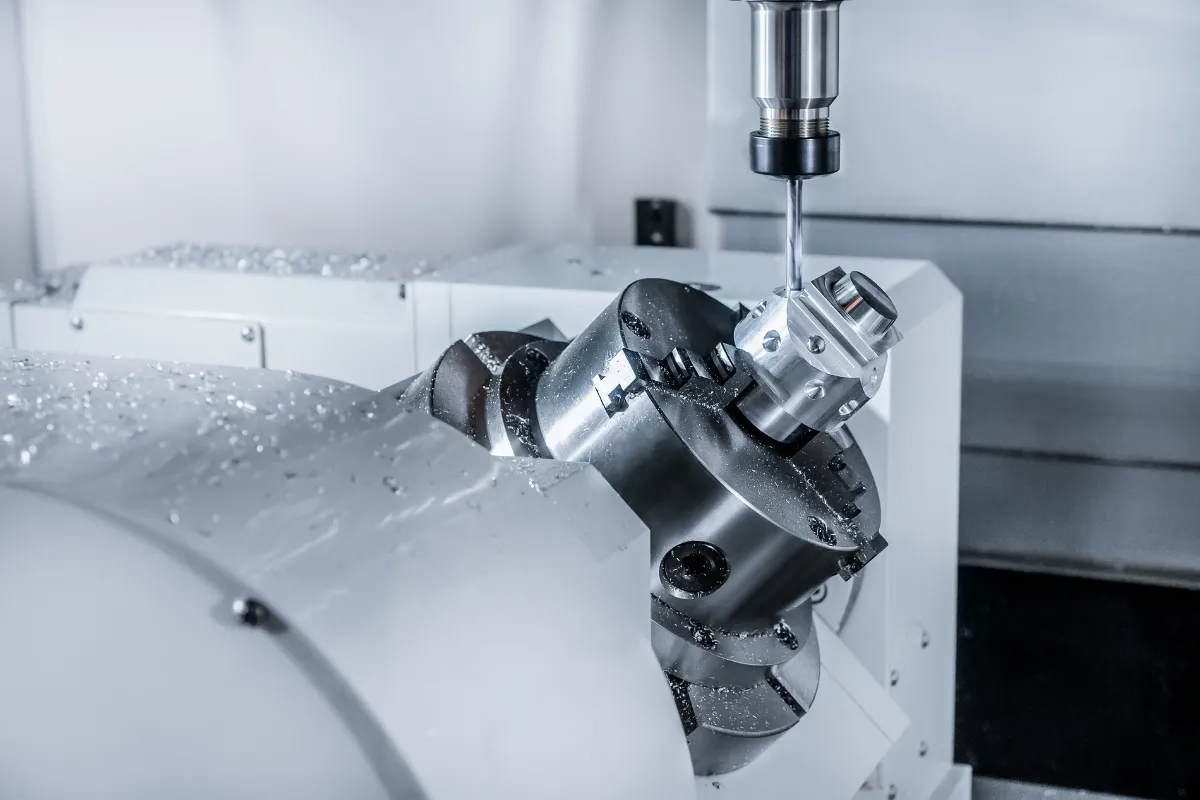
Zero Tolerance Machining does not imply achieving absolute “zero” deviations—an unattainable standard due to the laws of physics—but rather minimizing tolerances to levels that were previously thought unachievable. It is about producing parts that meet the tightest dimensional accuracy, often within a micron or less (1 micron = 0.001 millimeters). By comparison, the average human hair is about 70 microns thick, illustrating how minuscule these tolerances are.
In practical terms, Zero Tolerance Machining requires a combination of advanced CNC machinery, cutting-edge software, material science innovations, and highly skilled operators who understand the complexities of working at such precise levels.
Can Absolute Zero Tolerance Be Achieved?
Achieving absolute zero tolerance is a theoretical ideal rather than a practical reality. This is because machining processes are influenced by factors like:
- Material Properties: Materials expand or contract under temperature changes, and machining tools wear over time, introducing variations.
- Machine Limitations: Even the most advanced CNC machines are subject to slight mechanical imperfections and thermal fluctuations.
- Umweltfaktoren: Conditions such as humidity and vibrations in the machining environment can impact dimensional stability.
While absolute zero tolerance remains elusive, the advancements in CNC machining tolerances have brought manufacturers closer to achieving near-perfect precision.
The Rise of Zero Tolerance Machining
The demand for Zero Tolerance Machining is being driven by several key trends:
- Aerospace and Defense: The aerospace industry demands components that can withstand extreme environmental conditions and high loads. Precision is critical for jet engine parts, airframe components, and satellite instruments.
- Medizinische Geräte: In the medical field, implants, surgical instruments, and diagnostic equipment need to meet incredibly strict tolerances to ensure safety and reliability.
- Semiconductor Manufacturing: The electronics industry relies on highly precise components for microchips, processors, and circuit boards, where deviations at the nanometer scale can lead to failures.
For example, General Electric’s aviation division revealed that some of its turbine blade components require tolerances as tight as 2 microns to ensure optimal efficiency and prevent material fatigue. This level of precision wasn’t achievable a decade ago without significant advancements in machining technology.
Key Components of Zero Tolerance Machining
To achieve such tight tolerances, several factors must come together:
1. Advanced CNC Machines
Modern CNC (Computer Numerical Control) machines form the backbone of Zero Tolerance Machining. Five-axis CNC machines, for instance, can machine complex geometries without needing to reorient the part, minimizing errors caused by repositioning. High-speed spindles and vibration-dampening structures ensure that tools maintain consistent contact with the material for ultra-smooth finishes.
2. Metrology and Inspection Tools
Metrology—the science of measurement—is critical for verifying tolerances. Technologies such as coordinate measuring machines (CMM), laser scanners, and interferometers provide precise, real-time feedback during and after machining. For example, Zeiss CMMs can measure features with an accuracy of ±0.5 microns, ensuring every dimension is within spec.
3. Cutting Tools and Toolholders
The cutting tools used in ZTM must be capable of maintaining sharpness and form even after thousands of cuts. Innovations in carbide and diamond-coated tools have significantly enhanced tool life and precision. Additionally, ultra-precise toolholders that minimize runout (a deviation where the tool does not spin perfectly on its axis) ensure consistent cuts.
4. Thermal and Vibrational Control
Temperature fluctuations and machine vibrations can cause even the most advanced CNC machines to deviate. To counteract this, Zero Tolerance Machining setups often feature climate-controlled environments, vibration-isolated foundations, and thermal compensation software. For example, some machining centers employ cooling systems that circulate temperature-controlled oil or air to stabilize the machine’s components.
Benefits of Zero Tolerance Machining
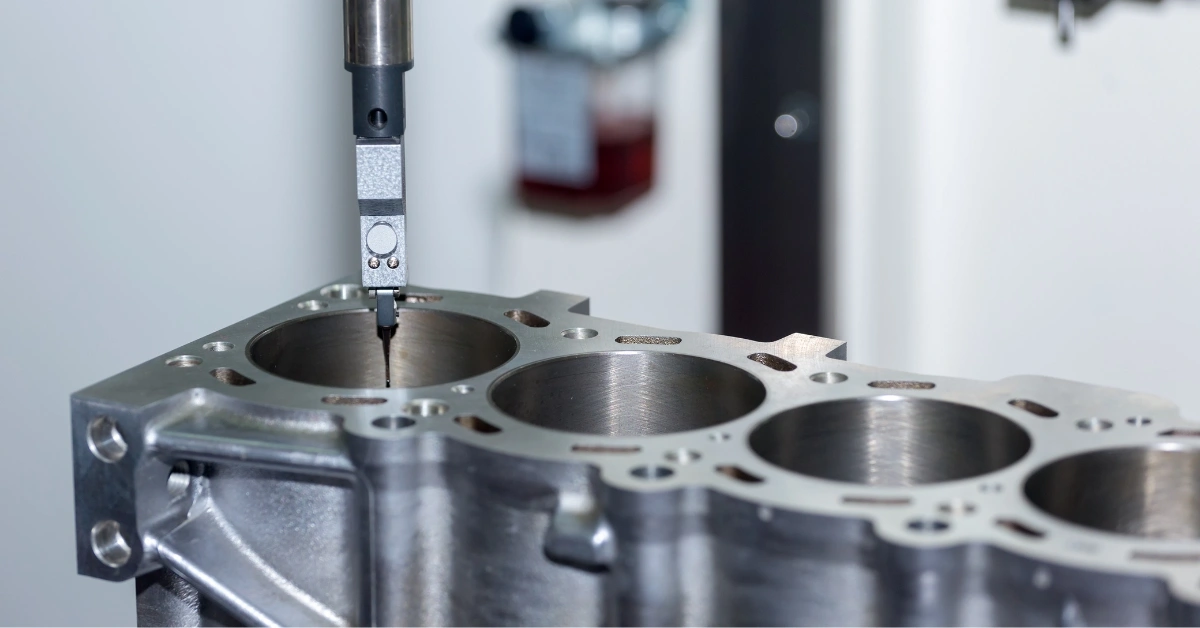
The move toward Zero Tolerance Machining offers several substantial benefits to manufacturers and end-users:
1. Improved Performance and Durability
Parts with tighter tolerances typically perform better and last longer because they fit together more precisely and experience less wear over time.
2. Reduced Waste and Rework
By achieving higher levels of precision, manufacturers can reduce scrap rates and avoid costly rework. A study by the International Academy for Production Engineering found that adopting ultra-precision machining in aerospace reduced rework costs by up to 35%.
3. Competitive Advantage
Companies that master Zero Tolerance Machining gain a significant edge in highly regulated industries. For instance, the medical device manufacturer Stryker leveraged advanced machining techniques to become a leader in producing highly accurate orthopedic implants.
Challenges in Achieving Zero Tolerance
- High Capital Costs: The initial investment in ultra-precision CNC machines, inspection equipment, and environmental controls can be substantial.
- Skill Shortages: Achieving tight tolerances requires skilled machinists who understand the nuances of high-precision manufacturing.
- Time-Intensive Setup: The setup and calibration of machines for Zero Tolerance Machining are often more complex and time-consuming than traditional machining.
Real-World Example: Precision in Aerospace

A prime example of Zero Tolerance Machining in action is SpaceX’s production of rocket components. The company’s ability to manufacture reusable rocket engines with parts machined to sub-micron tolerances has been a key factor in its success. Similarly, Rolls-Royce’s Trent XWB engines, used in Airbus A350 aircraft, rely on components that meet incredibly tight tolerances to achieve their industry-leading fuel efficiency and durability.
The Future of Zero Tolerance Machining
The future of Zero Tolerance Machining will be shaped by several exciting developments. Innovations in AI-powered CNC software, real-time machine learning-based metrology, and quantum computing for design optimization are set to push the limits even further. Additionally, additive manufacturing (3D printing) is starting to complement traditional subtractive machining, enabling complex parts with near-perfect precision.
In the next decade, we can expect to see Zero Tolerance Machining become more accessible as costs decrease and new breakthroughs emerge. This evolution will further accelerate advancements in critical fields such as aerospace, healthcare, and electronics.
Fazit
Zero Tolerance Machining represents the pinnacle of precision engineering. By pushing the boundaries of what can be achieved, this approach enables manufacturers to create components that were once thought impossible. As industries continue to demand ever tighter tolerances, the companies that embrace Zero Tolerance Machining will be the ones leading the charge in innovation, reliability, and performance.
Whether you’re producing jet engine parts, surgical implants, or semiconductor components, Zero Tolerance Machining is more than just a strategy—it’s a necessity in today’s ultra-competitive manufacturing landscape.
Entdecken Sie mehr mit unseren Blogbeiträgen.
kürzliche Posts
Erfahren Sie mehr über unsere Produkte.
Verwandte Produkte
Sofortiges Angebot!