













Table of Contents
Stainless Steel Casting Exhaust Manifold
Stainless steel casting for exhaust manifolds offers several advantages over other materials and manufacturing processes. Here are some key advantages:
Corrosion Resistance: Due to its exceptional capacity to withstand corrosive gases and high temperatures, stainless steel is an optimal material for exhaust manifolds. It can withstand the corrosive effects of exhaust gases, moisture, and road salt, prolonging the life of the manifold.
High-Temperature Performance: Stainless steel can withstand the high temperatures generated by the exhaust system without significant deformation or degradation. It maintains its strength and structural integrity even under extreme heat, ensuring long-lasting performance.
Design Flexibility: Casting allows for complex shapes and intricate designs that are difficult or costly to achieve with other manufacturing methods. Stainless steel casting enables the production of exhaust manifolds with optimized flow characteristics, improved exhaust gas scavenging, and reduced backpressure, leading to enhanced engine performance.
Strength and Durability: Stainless steel castings stand out with their outstanding mechanical strength that results in high durability and resistance to cracking or fracturing under stress. They can withstand the vibrations, thermal cycling, and pressure fluctuations commonly experienced in exhaust systems.
Weight Reduction: Stainless steel casting allows for the production of lightweight exhaust manifolds without compromising strength or performance. This weight reduction can contribute to improved fuel efficiency and vehicle handling.
Corrosion Fatigue Resistance: Stainless steel castings exhibit excellent resistance to corrosion fatigue, which is the combination of cyclic loading and corrosive environments. This property ensures the longevity and reliability of the exhaust manifold, even in harsh conditions.
Cost-Effectiveness: Stainless steel casting can provide cost advantages compared to other manufacturing processes, especially for complex shapes and low to medium production volumes. It offers a cost-effective solution for producing high-quality exhaust manifolds.
These advantages make stainless steel casting an attractive choice for manufacturing exhaust manifolds. They provide a balance of performance, durability, corrosion resistance, and design flexibility, contributing to improved engine efficiency and reliability.
The Function of an Exhaust Manifold
Exhaust manifold is mainly an integral part of the exhaust system in a vehicle fitted with internal combustion engine by collecting and guiding away all exhausted gases. Their functions include collecting the high-temperature exhaust gases from individual engine cylinders, equalizing of pressure in all the 4 engines to ensure smooth drainage as well routing it towards catalytic converter and passages beyond. It is also the work of an exhaust manifold to let off heat created by hot gases. Functionally, it is crucial in ensuring that the engine remains efficient while minimizing emissions with respect to an engine’s temperature and pressure.
Benefits of Using Casting for Exhaust Manifold Production
Casting is one of such best preferred ways to produce the exhaust manifolds popular owing to several benefits. It enables the formation of complex constructions eliminating material waste in production, and therefore, providing greater flexibility when it comes with choosing a type of materials to ensure long-life products. Due to its heat and corrosion-resistant properties, the cast type of exhaust manifold is highly durable. Additionally, the procedure is usually a situation where relatively little machining goes into something that saves time and resources in equal measure resulting to consistently uniform results. Design flexibility allows you to be customized for improved engine efficiency, and light-weight materials are used to reduce the total weight of vehicles that will in turn help improve fuel economy and handling.
Benefits of Using Stainless Steel for Casting Exhaust Manifold Production
Stainless steel considerably simplifies the casting of exhaust grate manufacturing. Stainless steel is very corrosion resistant which provides the high strength performance of seam welded manifolds to guarantee its durability in harsh automotive surroundings and also withstands all temperatures. It provides the required rigidity to hold up under prolonged engine tensions and enables uniquely complex designs that steer exhaust gas streamlines, improving on performance. Stainless steel manifolds are easy to maintain, produce cleaner emissions and possess an attractive design finish that is either polished or brushed. Moreover, stainless steel is a non toxic as well recyclable material which promotes sustainability in manufacturing.
Comparison Between Casting and CNC Machining for Exhaust Manifold Production
Casting and CNC machining are two distinct methods used for exhaust manifold production, each with its own advantages and considerations:
Casting:
- Cost-Effective: Casting is in many cases more economical than forming for mass production because of lower tool and set-up costs.
- Complex Shapes: Casting enables the elaboration of sophisticated and intricate patterns that can be difficult to develop with machining.
- Material Efficiency: Casting eliminates material waste since surplus can be recycled.
- Surface Finish: However, cast manifolds may need other finishing processes for better surface quality.
CNC Machining: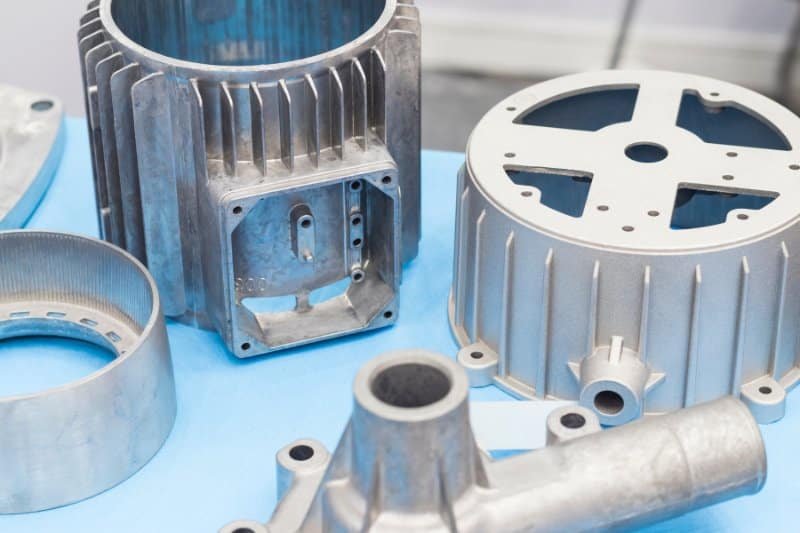
- Precision: With CNC machining, components of exhaust manifolds are produced with extreme level accuracy and high tolerance.
- Material Versatility: It is compatible different materials, such as stainless steel , giving an opportunity to choose of the material.
- Low Setup Time: CNC machining set up is less time-consuming, and therefore it favours small production runsand prototyping.
- Surface Finish: With the use of CNC machining, surface finish is usually higher and does not require any further processes.
Types of Stainless Steel Used for Casting Exhaust Manifold
Stainless steel casting is widely applied to the manufacturing of exhaust manifolds because it stands up well, has high corrosion resistance and other properties that outperform those offered by most metals. For this purpose, several types of stainless steel are available. The first type is an austenitic grade for excellent corrosion (e.g., the 304 and 316). Besides that there’s ferritic due to heat resistance( e . g , in both cases use of items like i925 separators ) ass The selection of type within the stainless steel is based upon variable factors such as application specifics, operating mode conditions and cost aspects; therefore making it possible for exhaust manifold performance optimization.
Challenges of Using Stainless Steel for Casting Exhaust Manifolds
When using stainless steel for the casting of exhaust manifolds, several challenges arise including expensive materials prices when compared to other options as well as more difficult casting operations with smaller design possibilities and higher tool wear during machining which could provide little protection against high temperatures that may be problematic at extremely high levels together with corrosion effects under extreme circumstances while also increasing weight. However, such issues notwithstanding; stainless steel has an advantage because it does not rust or corrode easily, is durable and put up with heat making it most sought after In instances where the application of exhaust manifold in car manufacturing to name but a few must be hardy. These variables should be taken into account when manufacturers manufacture this product using stainless steel.
Post-Processing Techniques for Stainless Steel Casting Exhaust Manifolds
After the casting of stainless steel, there are post-processing techniques such as surface finishing methods that include shot blasting and sandblasting to make a better appearance manifold by polishing it to remove any extra marks. Precision and dimensional accuracy can be reached by some machining processes – CNC machineing and drilling. Mechanical properties may be enhanced through heat treatment while welding and assembly are required for linking different components. Different types of control methods such as visual, dimensional and non-destructive testing is also used. Other protective coatings such as ceramic and thermal barrier coatings can be applied for further enhancement of protection and performance. Such post-processing methods are important since they allow us to make stainless steel casting exhaust manifolds of good quality.
Custom Stainless Steel Casting Exhaust Manifolds From Manufacturers
Manufacturers produce custom stainless steel casting exhaust manifolds that serve as specialized solutions for different fields. While searching for these components, certain points must be observed to achieve the expected outcomes. To begin with, have a thorough specification meeting with an experienced manufacturer stating your accurate requirements that include design, material selection, measurements and the quantity. With its high durability and corrosion resistance properties, stainless steel should be chosen; however, considerations about the most convenient alloy for you application will also have to take place.
The design of the manifold can be customized by manufacturers according to your performance and space limitations, as well as tuned for better flow dynamics in order to enhance overall engine performance. It is therefore important that different precision casting techniques are used to ensure the accuracy and high quality in production of manifolds. Use treatment options like machining, heat treatment, surface finishing and coatings to meet the specifications.
Therefore, quality control and testing should be an integral part ofthe process; agencies with reputable manufacturers have some standards which they follow to the letter for dimensional checks nd non-destructive testings. Costmgmt should work closely with manufacturer to provide cost sensitive solutions that match your specification requirements. Delivery lead times are essential, thus talk about the delivery time and see that it conforms to meeting project deadlines.
During the implementation of this project make periodic contact with manufacturer to revise designs or adaptations suggested. In brief, custom stainless steel casting exhaust manifolds relationship between specifications; material selection design customization precisioncasting post-processing quality control cost management delivery and ongoing the work to fulfill your particular needs indeed satisfactory.