- Home
- Capabilities
- Plastic Blow Molding
Professional Custom Plastic Blow Molding Services
HDC Manufacturing delivers exceptional custom plastic blow molding services for small batch production and large-scale manufacturing. With advanced technology and a professional team, we provide high-quality, precision products to help your business stand out in the market.
Benefits of Plastic Blow Molding
Discover the numerous advantages of plastic blow molding to enhance your product development.
Efficient Production
🔹Fast, High-Volume Output: Ideal for large-scale manufacturing needs.
🔹Automated Production Lines: Boost efficiency and shorten delivery times.
Design Flexibility
🔹Complex Shapes and Sizes: Meet diverse design requirements with ease.
🔹Innovative Solutions: From simple containers to intricate industrial components.
Cost Efficiency
🔹Lower Material and Production Costs: More economical than other molding processes.
🔹Reduced Per-Unit Costs: Perfect for mass production.
Lightweight Products
🔹Easy Transportation and Handling: Reduce shipping costs and improve maneuverability.
🔹Ideal for Consumer Goods: Enhance user experience with lightweight designs.
High Durability
🔹Excellent Strength: Suitable for high-stress applications.
🔹Long-Lasting Performance: Extend product lifespan with durable materials.
Consistency and Precision
🔹Uniform Quality: Ensure every product meets required standards.
🔹Reduced Defects: Maintain high precision across large production runs.
Why Choose HDC Plastic Blow Molding Service
Cutting-Edge Technology
🔹Advanced blow molding equipment and software.
🔹Precision manufacturing for complex designs and tight tolerances.
Comprehensive Services
🔹End-to-end solutions: design, prototyping, production, and post-production support.
🔹Seamless process from concept to completion.
Rigorous Quality Control
🔹Strict quality assurance measures at every stage.
🔹Consistent, high-quality products that meet your standards.
Competitive Pricing
🔹Cost-effective solutions without compromising quality.
🔹Transparent pricing with no hidden fees.
Sustainability Commitment
🔹Eco-friendly materials and practices.
🔹Support for your green initiatives and sustainability goals.
Customer-Centric Approach
🔹Exceptional service and open communication.
🔹Long-term partnerships built on trust and mutual success.
Materials HDC Offers for Blow Molding
Versatile and High-Quality Material Options Tailored to Your Specific Requirements
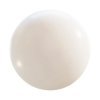
Polyethylene (PE)
Exceptional durability, flexibility, and chemical resistance.
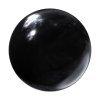
Polypropylene (PP)
Excellent stiffness, heat resistance, and chemical resistance.
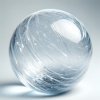
Polyethylene Terephthalate (PET)
High strength, clarity, and excellent barrier properties.
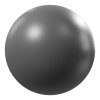
Polyvinyl Chloride (PVC)
High strength, abrasion resistance, and chemical resistance.
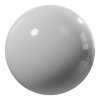
Acrylonitrile Butadiene Styrene (ABS)
Combines strength, toughness, and rigidity.
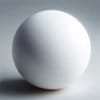
High-Density Polyethylene (HDPE)
Excellent impact resistance, strength, and environmental stress crack resistance.
Understanding Plastic Blow Molding
Explore the technology, applications, and innovations of plastic blow molding, a versatile manufacturing process for creating hollow plastic parts.
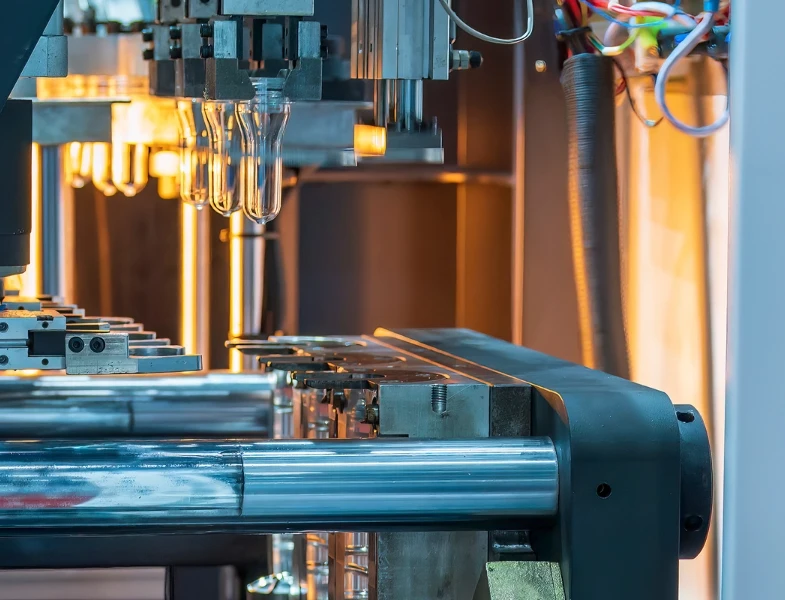
What is Plastic Blow Molding?
Plastic blow molding is a manufacturing process used to create hollow plastic parts by inflating a heated plastic tube until it fills a mold and forms the desired shape. Developed in the 1930s, this technique has evolved significantly and is now a cornerstone of modern manufacturing.
Key Features of Blow Molding
- Tight Tolerances: Typically within ±0.25% to ±1% of specified dimensions.
- Consistency: Ensures uniform quality across large production runs.
- High-Volume Output: Ideal for mass production needs.
- Automation: Modern systems enhance efficiency and quality control.
Challenges and Solutions
1. Uniform Wall Thickness
- Challenge: Maintaining consistent thickness in complex designs.
- Solution: Advanced mold design and real-time monitoring systems.
2. Complex Shapes
- Challenge: Producing intricate geometries.
- Solution: Innovations in mold cooling and material flow control.
3. Material Shrinkage
- Challenge: Managing shrinkage during cooling.
- Solution: Optimized cooling technologies and material selection.
Applications of Blow Molding Across Various Industries
Exploring the Versatile Uses of Blow Molding Technology in Different Sectors
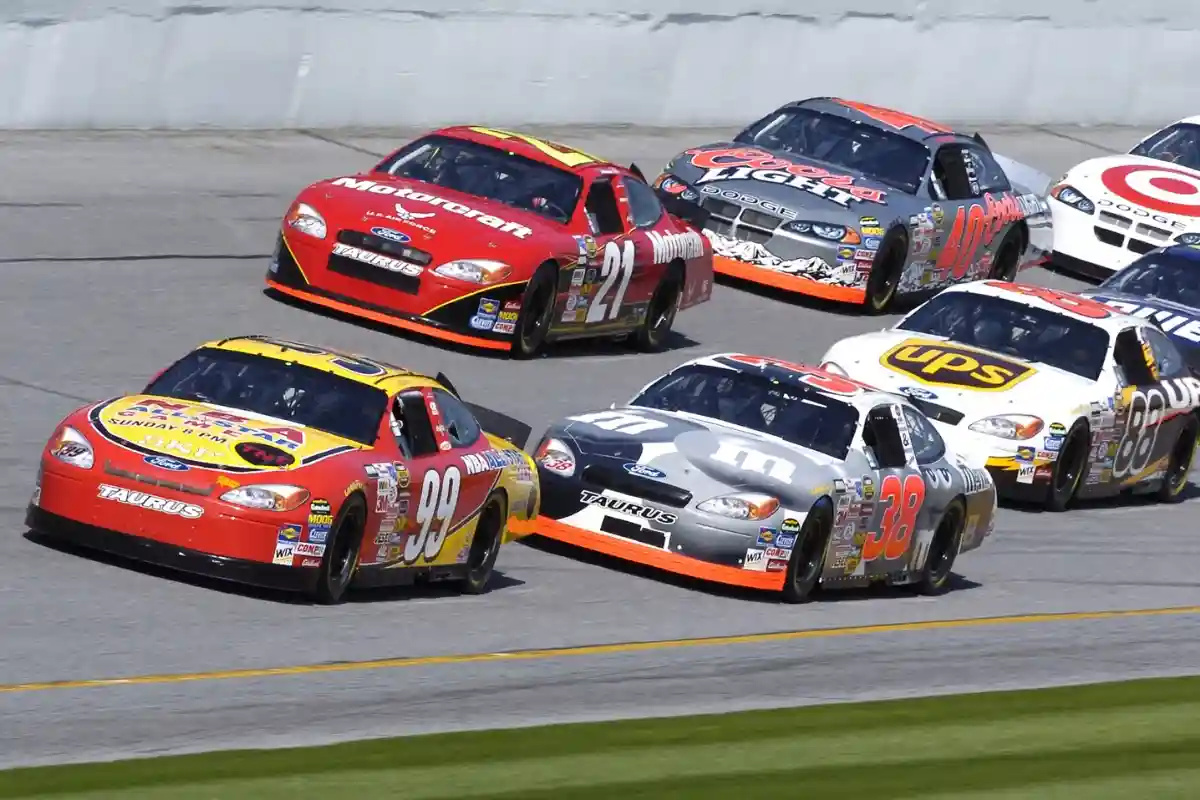
Automotive Industry
🔹Components: Fuel tanks, air ducts, coolant reservoirs, and intake manifolds.
🔹Benefits: Precise dimensions, intricate shapes, and durability for enhanced vehicle performance.
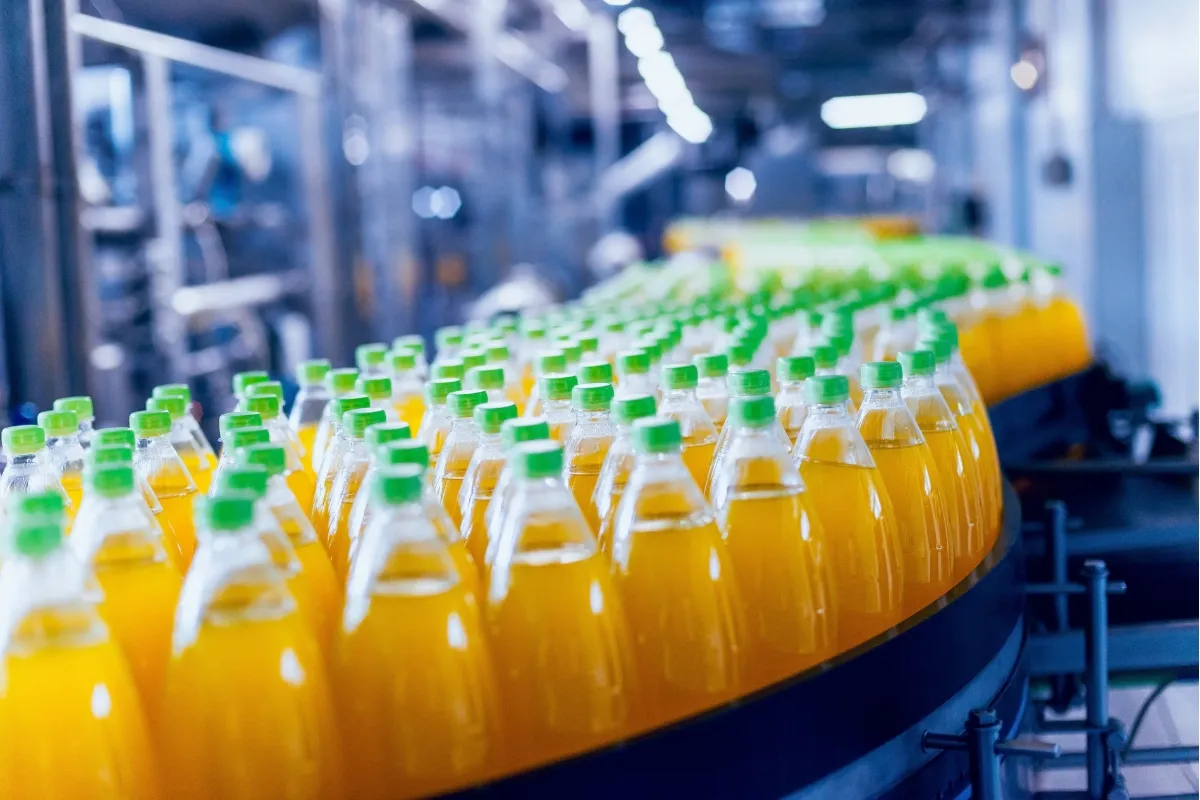
Food Industry
🔹Products: Bottles and containers for water, soda, juices, and milk.
🔹Examples: PET bottles for soft drinks, HDPE milk jugs, and PP juice containers.
🔹Benefits: Durability, safety, and chemical resistance for food-grade applications.
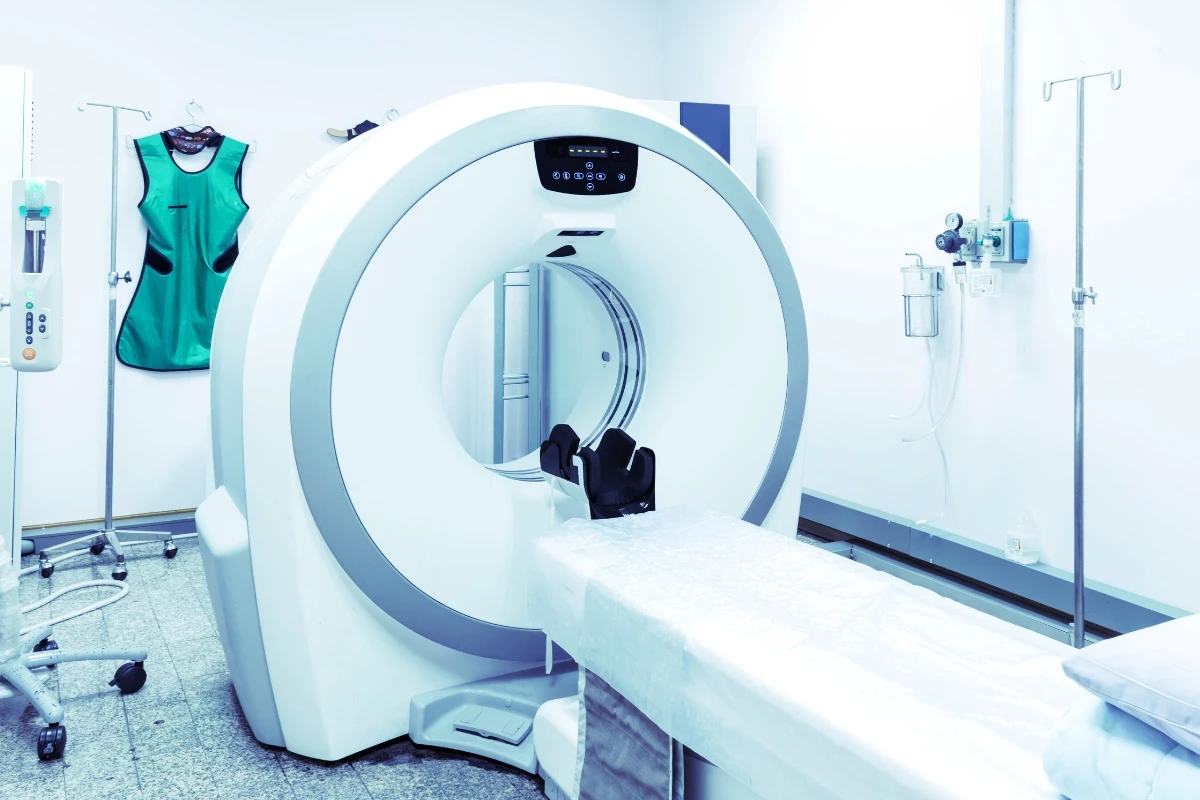
Medical Industry
🔹Products: Medical containers, IV bottles, and pharmaceutical packaging.
🔹Examples: Sterile medical containers, IV solution bottles, and secure medication packaging.
🔹Benefits: High hygiene standards and safety for healthcare applications.
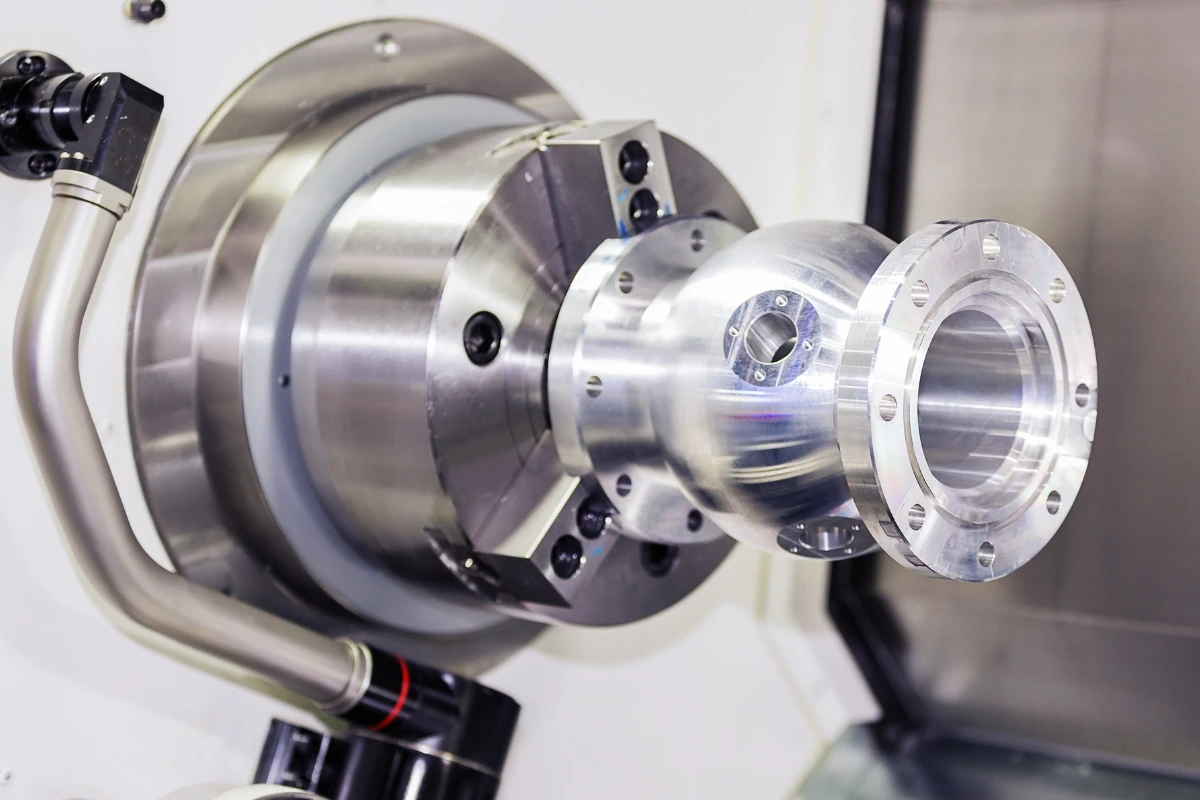
Industrial Applications
🔹Products: Large containers, industrial drums, and chemical storage tanks.
🔹Examples: 55-gallon chemical drums, HDPE liquid containment tanks, and custom industrial parts.
🔹Benefits: Robust designs meeting specific engineering requirements.
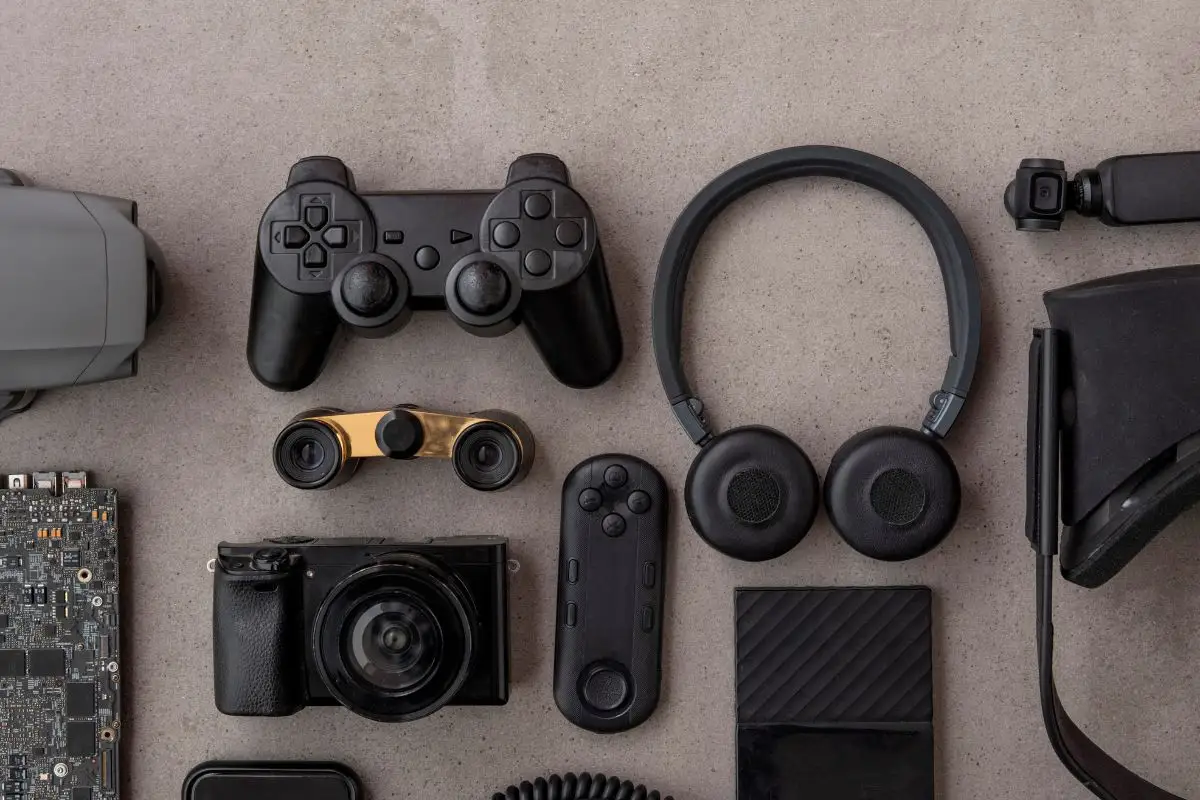
Consumer Goods
🔹Products: Household items and personal care packaging.
🔹Examples: HDPE detergent bottles, PET shampoo bottles, and lotion dispensers.
🔹Benefits: Durability, transparency, and user convenience for everyday use.
Precision in Blow Molding
Blow molding technology achieves high precision, ensuring each product meets strict dimensional and quality standards.
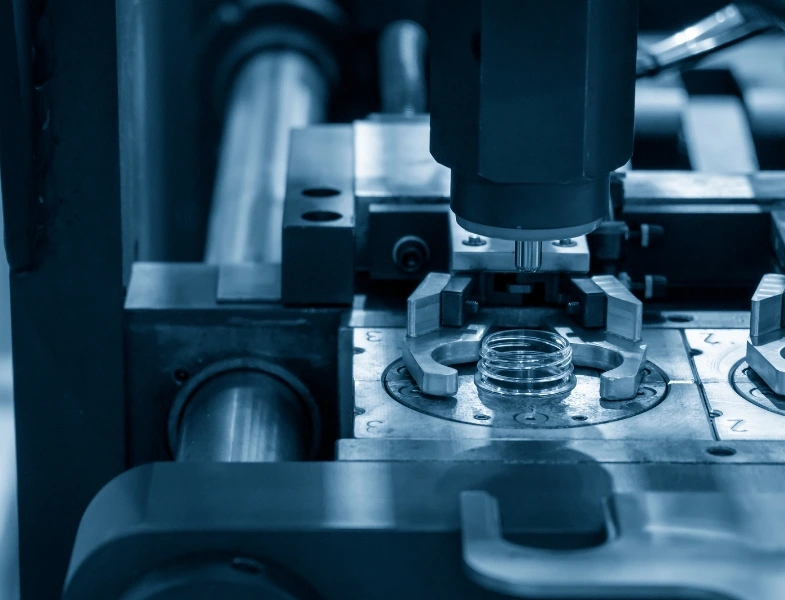
Parameter | Typical Precision |
Dimensional Tolerance | ±0.25% to ±1% |
Wall Thickness | ±0.1 mm to ±0.5 mm |
Weight Variation | ±1% to ±5% |
Surface Finish | Ra 0.8 to Ra 1.6 μm |
Roundness | ±0.5% |
Concentricity | ±0.5% |
Blow Molding Technical Specifications
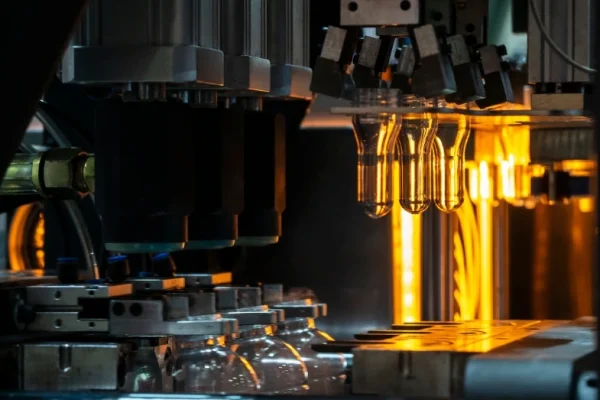
Specification | Details |
Wall Thickness Range | 0.5 mm to 2 mm |
Material Compatibility | PE, PP, PET, PVC, ABS, HDPE |
Mold Clamping Force | Up to 500 kN |
Blow Pressure | 2 to 6 bar |
Production Speed | Up to 1500 units per hour (varies with product size) |
Tolerance | Dimensional tolerance: ±0.25% to ±1% |
Surface Finish | Ra 0.8 to Ra 1.6 μm |
Automation Level | Fully automated with real-time monitoring and control |
Max Part Size | Up to 1 meter in length and 0.7 meters in diameter |
FAQs About HDC Plastic Blow Molding Service
Find answers to common questions about HDC’s plastic blow molding services, from customization to quality assurance, and ensure your project meets exact specifications.
We work with a wide range of materials including PE, PP, PET, PVC, ABS, and HDPE. Each material offers unique properties suited for different applications, ensuring we can meet your specific needs.
The lead time varies depending on the complexity and volume of the order. Typically, it ranges from 6 to 8 weeks from the finalization of the design to the completion of production.
We offer assistance with design and prototyping, but we require customers to provide detailed drawings or samples. While we can guide and support the design process, understanding your specific needs fully necessitates your input and initial designs.
We can produce products up to 1 meter in length and 0.7 meters in diameter.
We implement rigorous quality control measures at every stage of production, including real-time monitoring, precise dimensional checks, and thorough inspections to ensure each product meets our high standards.
While blow molding is highly versatile and can create complex shapes, there are some limitations with extremely intricate designs and very small details. Our team can help optimize your design for the best results.
Costs vary based on material, complexity, size, and volume of the order. We provide competitive pricing and will work with you to find cost-effective solutions that meet your budget.
Get an Instant Quote!
Get a quick quote for your project with just a click! Request an instant quote now!
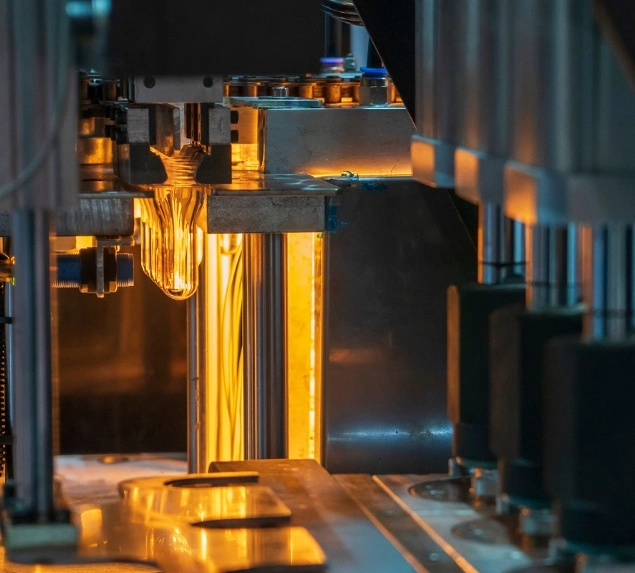
Contact With Us
for any inquiry



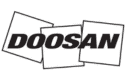
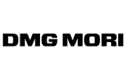