- Heim
- Ressourcen
- Bloggen
- Was ist CNC-Bearbeitung?
Was ist CNC-Bearbeitung? Ein umfassender Leitfaden
- Von: HDCMFG
1952 entwickelte das Massachusetts Institute of Technology (MIT) in Zusammenarbeit mit dem Militär die erste numerisch gesteuerte Fräsmaschine mit einem Vakuumröhren-Steuerungssystem. Über 70 Jahre später, mit der Weiterentwicklung der Computertechnologie und der Weiterentwicklung des computergestützten Designs (CAD) und computergestützte Fertigung (NOCKEN) Software entwickelt sich die CNC-Bearbeitung hin zu höherer Präzision und größerer Vielfalt. Dieser Artikel nimmt Sie mit auf eine Reise, um diese bahnbrechende Bearbeitungstechnologie zu verstehen.
Was ist CNC-Bearbeitung?
CNC-Bearbeitung (kurz für Computer Numerical Control) ist eine Technologie, bei der Computer Befehle erteilen und verschiedene Systeme einer Drehbank steuern, um die Bearbeitung von Teilen automatisch abzuschließen.
Bedeutung der CNC-Bearbeitung
CNC-Technologie ermöglicht die hochpräzise Bearbeitung komplexer Designteile aus unterschiedlichen Materialien und bildet damit die Grundlage moderner Industrie und modernster wissenschaftlicher und technologischer Forschung. Moderne CNC-Werkzeugmaschinen erreichen mit hydrostatischen Führungen und Laserinterferometern höchste Präzision im Nanometerbereich und sind die einzige Möglichkeit für die Bearbeitung nanoskaliger Flachlinsen auf Gravitationswellendetektoren und EUV-Lithografiemaschinen. Auch Turbinenschaufeln in Flugzeugtriebwerken und kundenspezifische Implantate im medizinischen Bereich sind auf die Fähigkeit von CNC-Maschinen angewiesen, komplexe Profiloberflächen zu bearbeiten. Ohne CNC-Technologie steigen die Kosten für die Herstellung dieser Teile oder sie ist schlichtweg unmöglich. CNC stellt daher im Bereich der Hochpräzisionstechnik eine unüberwindbare technische Hürde dar.
Woraus besteht eine CNC-Maschine?
Eine CNC-Maschine besteht aus über 1000 Teilen, die sich grob in fünf Systeme unterteilen lassen. Als nächstes betrachten wir die standardmäßige dreiachsige Vertikalfräsmaschine als Beispiel, um einen allgemeinen Überblick über den Aufbau einer CNC-Werkzeugmaschine anhand dieser fünf Systeme zu erhalten.
1. CNC-System
Das CNC-System ist das Gehirn der CNC-Maschine und dient der Steuerung und Überwachung des gesamten Maschinenbetriebs. Es besteht aus zwei Teilen: Software und Hardware. Die Software umfasst Betriebssystem, Code-Interpreter und Steuerungsprogramm. Diese dienen zum Parsen des G-Codes, Generieren von Steueranweisungen, Steuern der Werkzeugbewegung, Anpassen der Spindeldrehzahl und Empfangen von Sensordaten wie Werkzeugposition/-temperatur in Echtzeit, zur automatischen Fehlerkorrektur und Sicherstellung der Bearbeitungsgenauigkeit. Die Hardware umfasst Prozessoren, Motortreiber und Sensoren, die für die Berechnung und Erfassung der Daten zuständig sind. Diese beiden Teile bilden die Beziehung zwischen dem Windows-System und der Computerhardware.
2. Mechanische Systeme
Das mechanische System bildet das Grundgerüst der CNC-Maschine und ist Träger der Werkzeug- und Werkstückbewegung. Das Bett dient als Basis für die stabile Lagerung von Spindel, Führungsschiene, Leitspindel, Werkbank und Getriebemechanismus und reduziert Vibrationen während der Bearbeitung. Die Spindel treibt das Werkzeug an, die Leitspindel führt es präzise entlang der Führungsschiene, um das auf dem Tisch fixierte Werkstück zu schneiden.
3. Antriebssystem
Das Antriebssystem besteht aus einem Servomotor und einem Spindelmotor, die das Herzstück von CNC-Werkzeugmaschinen bilden. Dabei wird der Servomotor zum Antrieb der Spindel verwendet, um sie in den X-, Y- und Z-Achsen nach oben zu bewegen, und der Spindelmotor wird zum Antrieb der Rotation des Werkzeugs verwendet. Die beiden arbeiten zusammen, um den Schneidvorgang abzuschließen.
4. Werkzeugsystem
Der Bearbeitungsprozess eines Teils umfasst verschiedene Arbeitsschritte, darunter Fräsen, Anfasen, Bohren und Gewindeschneiden. Jeder Arbeitsschritt erfordert ein speziell entwickeltes Werkzeug. Ein manueller Werkzeugwechsel verringert die Bearbeitungseffizienz erheblich und beeinträchtigt die Bearbeitungsgenauigkeit. Daher entwickelten die Ingenieure das Werkzeugmagazin zur Aufbewahrung und Verwaltung mehrerer Werkzeuge und das automatische Werkzeugwechselsystem (ATC) für den automatischen Werkzeugwechsel. Werkzeugsystem, Werkzeugmagazin und automatischer Werkzeugwechsler bilden das Werkzeugsystem.
5. Assistenzsysteme
Die Hauptaufgabe des Hilfssystems ist die Kühlung und Schmierung. Die Umlaufkühlung ist die am häufigsten verwendete Kühlmethode. Sie senkt die Schnitttemperatur durch Aufsprühen von Kühlmittel auf Werkzeug und Werkstück, um Genauigkeitsverluste durch Werkzeugverschleiß und Wärmestau zu vermeiden. Anschließend sammelt sie das Kühlmittel, filtert die Späne heraus und führt es dem Recycling zu. Die Schmierung erfolgt über das Zentralschmiersystem, um Schienen, Leitspindeln und andere bewegliche Teile der Ölversorgung regelmäßig zu führen.
Wie funktioniert CNC-Bearbeitung?
In diesem Abschnitt führen wir Sie durch den gesamten CNC-Bearbeitungsprozess von der Zeichnung bis zum Produkt.
Entwurf
Der erste Schritt bei der CNC-Bearbeitung von Produkten ist die Verwendung von CAD-Software (Computer Aided Design) (SolidWorks, AutoCAD, CATIA, etc.), um das 3D-Modell des Teils zu entwerfen und Form und Größe zu definieren. Beim Entwurf müssen Sie den Werkzeugtyp und die Bearbeitungskapazität der Maschine berücksichtigen, um die Machbarkeit der Bearbeitung sicherzustellen.
G-Code generieren
Der nächste Schritt besteht darin, das CAD-Modell in eine CAM-Software (Computer-Aided Manufacturing) zu importieren (Mastercam, Fusion 360 CAM, PowerMill usw.) und stellt Größe, Material und Parameter der verwendeten Maschine in der CAM-Software entsprechend der tatsächlichen Produktionssituation ein, wie z. B. Verfahrweg, Steuerungssystem, Achsenanzahl, Werkzeugbibliotheksinformationen usw. Basierend auf diesen Informationen berechnet und optimiert es automatisch den Werkzeugweg und generiert den vollständigen Satz an Anweisungen, die zur Steuerung der Bearbeitung der Maschine erforderlich sind. Vor der eigentlichen Produktion kann die Simulationsfunktion der CAM-Software genutzt werden, um den Bearbeitungsprozess zu simulieren und Risiken wie Werkzeugkollisionen zu vermeiden.
Einrichten der Maschine
Dann folgt die Vorbereitungsphase vor der eigentlichen Bearbeitung, die die Installation von Werkzeug, Vorrichtung und Rohling erfordert. Hier müssen Sie sicherstellen, dass
Der Rohling hat genau die gleiche Größe wie in der CAM-Software und ist korrekt eingespannt. Verwenden Sie anschließend Werkzeuge wie Werkzeugmesstaster, um die Koordinaten jeder Bearbeitungsachse zu kalibrieren und so Bearbeitungsrisiken weiter zu vermeiden.
Anschließend wird der von der CAM-Software generierte G-Code geladen und durch Trockenlauf oder abschnittsweises Durchlaufen die Sicherheit des Pfads überprüft.
Wenn alles bereit ist, können Sie die Maschine starten und mit der formalen Verarbeitung beginnen. Zu diesem Zeitpunkt müssen Sie den Verarbeitungsstatus in Echtzeit überwachen.
Inspektion
Nach der Bearbeitung wird üblicherweise ein Koordinatenmessgerät (KMG) verwendet, um die kritischen Maßtoleranzen des Produkts zu überprüfen. Wenn dies nicht der Fall ist, muss zur CAM-Phase zurückgekehrt werden, um die Schnittparameter anzupassen und die Prüfung erneut durchzuführen. Nachdem sichergestellt wurde, dass die bearbeiteten Teile qualifiziert sind, kann die Massenproduktion offiziell beginnen.
Achsen in der CNC-Bearbeitung verstehen
Es ist bekannt, dass die Anzahl der Achsen einer CNC-Maschine ihre Fähigkeit zur Bearbeitung hochpräziser, komplexer Teile widerspiegelt. Je mehr Achsen sie hat, desto teurer wird die Maschine. Daher ist es für die Auswahl der richtigen Maschine äußerst wichtig, die Anzahl der Achsen und ihre entsprechenden Bearbeitungskapazitäten zu kennen.
3-Achsen
Die 3-Achsen-Fräsmaschine verfügt über drei lineare Achsen: X, Y und Z, und die Spindel kann sich in diesen drei Richtungen frei bewegen, was für die Bearbeitung von Ebenen, Löchern, Schlitzen und einfachen Oberflächen geeignet ist.
4 Achsen
Die 4-Achsen-Fräsmaschine verfügt zusätzlich über eine A-Achse parallel zur X-Achse zum Drehen des Werkstücks auf der Basis der 3. Achse, was sich für die Bearbeitung komplexerer zylindrischer Teile mit Spiralmerkmalen und geformten Oberflächen wie Nocken, Schrauben usw. eignet.
5 Achsen
Basierend auf der vierten Achse verfügt die fünfte Achse zusätzlich über eine zur Z-Achse parallele Rotationsachse: die C-Achse. Durch die Verbindung von A- und C-Achse lässt sich der Ablenkwinkel des Werkstücks beliebig einstellen, um den toten Winkel bei der Bearbeitung zu eliminieren. Die fünfachsige CNC-Werkzeugmaschine kann mehr als 951 TP3T Bearbeitungsanforderungen erfüllen und eignet sich für die Bearbeitung hochpräziser Turbinenschaufeln, speziell geformter Knochenimplantate usw.
6 Achsen
Im Vergleich zu den 5 Achsen verfügt die 6-Achse über eine zusätzliche Rotationsachse parallel zur Y-Achse: B-Achse, drei Linearachsen und drei Rotationsachsen sind miteinander verbunden, decken alle Bearbeitungswinkel ab und können den gesamten Bearbeitungsprozess asymmetrischer Teile mit komplex gekrümmten Oberflächen in einer Aufspannung realisieren.
Wie viel kostet eine CNC-Maschine?
Die Einstiegsmodelle mit 3 Achsen kosten in der Regel zwischen $50.000 und $150.000, während High-End-Modelle von großen Marken wie DMG und MAZAK kann bis zu $200.000 bis $400.000 betragen.
4-Achsen-Werkzeugmaschinen mit Basisfunktionen reichen von $100.000 bis $300.000, und Modelle, die eine 4-Achsen-Kopplung unterstützen, können bis zu $300.000 bis $700.000 reichen.
Die Preisspanne für 5-Achsen-Werkzeugmaschinen ist recht groß. Einstiegsmodelle aus chinesischer Produktion kosten zwischen 450.000 und 850.000 $, während deutsche oder japanische High-End-Modelle zwischen 1.200.000 und 3.000.000 $ kosten können.
6-Achsen-Werkzeugmaschinen stellen derzeit die Topkonfiguration dar, wobei die Basismodelle von $1.200.000 bis $3.500.000 reichen und einige speziell angepasste Modelle $7.000.000 übersteigen können.
Hochwertige Mehrachsen-Werkzeugmaschinen erfordern oft strengere Installationsanforderungen, müssen strengere Umweltkontrollen durchführen, haben höhere Kosten für Verbrauchsmaterial und Wartung und benötigen spezielle Software, spezielle Prüfgeräte und qualifizierte Bediener, was oft teurer sein kann als der Kauf einer Maschine selbst.
Arten von CNC-Maschinen
Wenn Sie nur die Namen der einzelnen CNC-Maschinentypen auflisten, erhalten Sie eine lange Liste. Hier ändern wir den Blickwinkel, klassifizieren nach der Verarbeitungsmethode und betrachten die Typen und Eigenschaften gängiger CNC-Maschinen.
Entsprechend der Klassifizierung der Bearbeitungsmethoden können CNC-Maschinen in zwei Typen unterteilt werden: subtraktive Bearbeitung und additive Bearbeitung.
Subtraktive Bearbeitung ähnelt dem Gravieren. Dabei wird auf verschiedene Weise Material vom Rohling entfernt, um die gewünschte Form zu erzeugen. Gängige Maschinen sind:
1. CNC-Fräsmaschine
Das Hochgeschwindigkeits-Rotationswerkzeug bewegt sich auf den drei linearen Achsen X, Y und Z, um das auf der Bearbeitungsebene fixierte Werkstück zu schneiden, und eignet sich zum Bohren, Nutenfräsen und Bearbeiten einfacher Oberflächen.
2. CNC-Drehmaschine
Das Werkstück rotiert mit hoher Geschwindigkeit und das Werkzeug wird in axialer oder radialer Richtung vorgeschoben, was häufig für die symmetrische Bearbeitung von Zylinder-, Gewinde- und Wellenteilen verwendet wird.
3. Integriertes CNC-Dreh- und Fräsbearbeitungszentrum
Durch die Kombination der Eigenschaften einer Dreh- und Fräsmaschine kann sich das Werkzeug auf den drei linearen Achsen X, Y und Z bewegen und das Werkstück wie bei einer Drehmaschine um die A-Achse rotieren. Dies eignet sich für die Bearbeitung von Teilen mit komplexeren Oberflächen und höchsten Präzisionsanforderungen. Die höherwertigen Modelle verfügen zusätzlich über zusätzliche Werkstück-Rotationsachsen: C-Achse oder B-Achse. Dadurch können alle Umformprozesse in einer Maschine durchgeführt werden. Dies ist heute die gängigste Bearbeitungsmethode.
4. CNC-Laserschneidmaschine 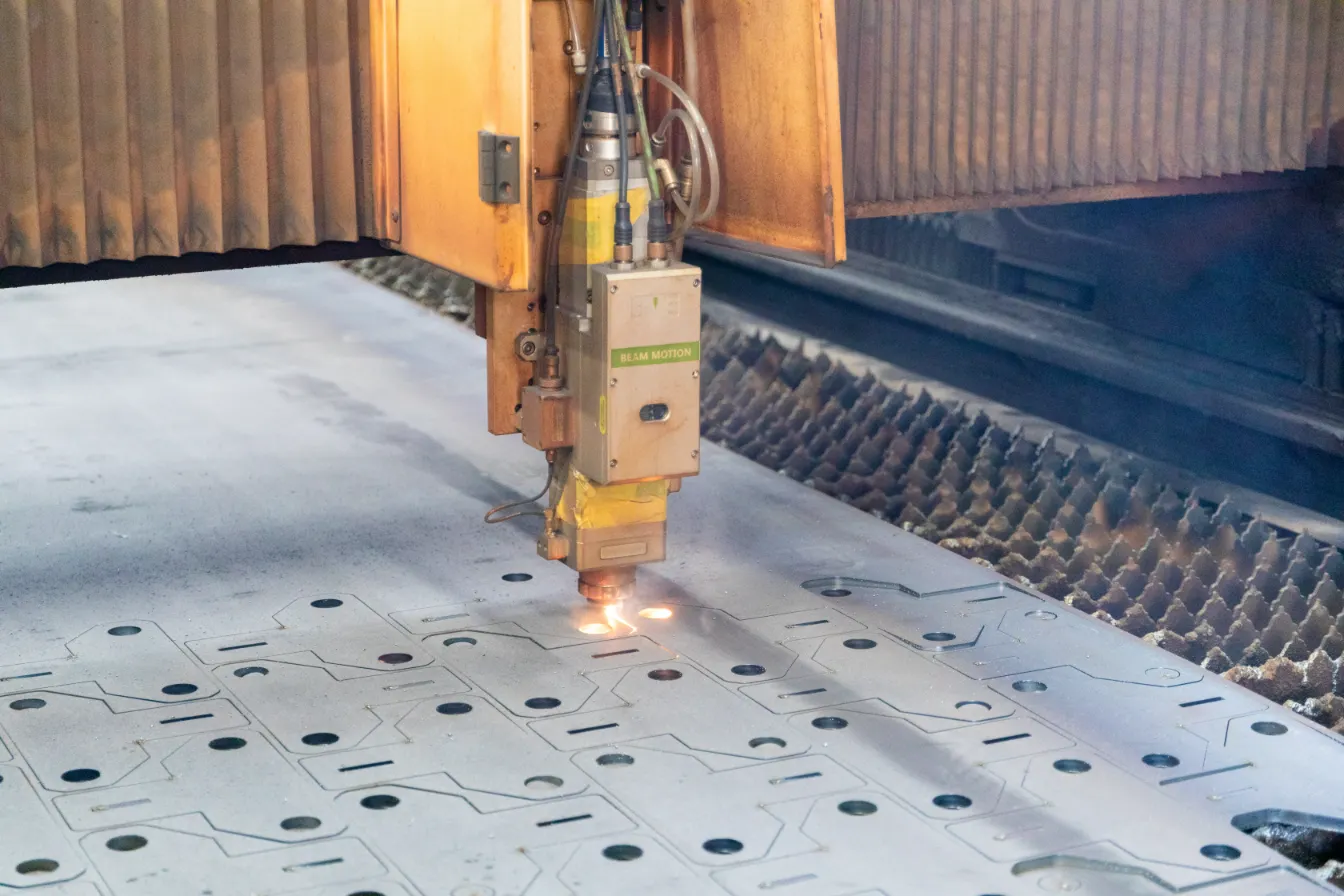
Unter der Steuerung des CNC-Systems wird der Laserstrahler präzise bewegt und das Blech mit dem Laser geschnitten. Er kann Bleche mit einer Dicke von bis zu 50 mm schneiden. Dadurch lassen sich ultrakleine, scharfe Winkel und komplexe Kurven erzielen, die mit anderen Schneidverfahren nicht erreicht werden können. Gleichzeitig kann durch die sinnvolle Anordnung des Schnittmusters der Materialabfall erheblich reduziert werden.
5. CNC-Wasserstrahlschneidemaschine
Das Prinzip entspricht dem des Laserschneidens, nur dass der Laser durch einen mit Schleifmittel versetzten Hochgeschwindigkeitswasserstrom ersetzt wird, der bis zu 300 mm dicken Stahl schneiden kann. Gleichzeitig verfügt der Wasserstrom über eine eigene Wärmeableitung und es gibt keine Wärmeeinflusszone. Daher eignet sich das Verfahren zum Schneiden von Materialien mit hohen Anforderungen an die Wärmekontrolle, wie z. B. Kunststoff, Kohlefaser usw.
6. CNC-EDM-Maschine
Der durch die Entladung extrem feiner Metallelektrodendrähte erzeugte Lichtbogen korrodiert leitfähige Materialien mit höherer Präzision als andere Schneidmethoden und eignet sich am besten zum Schneiden ultrafeiner Mikrolöcher.
Additives Verfahren ist das Gegenteil von subtraktivem Verfahren. Es ähnelt dem Bauen mit Legosteinen, bei dem Rohstoffe Schicht für Schicht zu einem Endprodukt gestapelt werden. Dies wird auch als 3D-Druck bezeichnet. Je nach Prinzip der Materialstapelung sind gängige 3D-Drucker:
1. FDM (Fused Deposition Modeling):
Durch Erhitzen und Extrudieren des Heißschmelzkunststoffs kann sich der Druckkopf in die drei Richtungen X, Y und Z bewegen und den geschmolzenen Kunststoff Schicht für Schicht auf der Druckplattform auftragen, wodurch das gewünschte Teil entsteht.
2. SLS (Selektives Lasersintern):
Jedes Mal, wenn eine Schicht Nylon- oder TPU-Pulver gleichmäßig auf die Formplattform gelegt wird, scannt der Laser diese Pulverschicht entsprechend den Schnittdaten des Modells, sodass die Pulverpartikel teilweise schmelzen und miteinander verbunden werden. Anschließend wird die Plattform abgesenkt und der Pulververteilungs-Sinterprozess wiederholt, bis das Teil geformt ist. Das ungesinterte Pulver kann das Teil selbst stützen, sodass die gedruckte Stützstruktur nicht wie beim FDM-Druck entworfen werden muss.
3. SLM (Selektives Laserschmelzen):
Das Prinzip ist dasselbe wie beim SLS, allerdings wird das Metallpulver mit einem Hochenergielaser Schicht für Schicht geschmolzen. Dadurch können innere Details und Hohlräume hergestellt werden, die mit CNC-, Guss- und anderen Verfahren nicht realisierbar sind, und gleichzeitig Festigkeit und Präzision gewährleistet werden.
Materialien, die bei der CNC-Bearbeitung verwendet werden
Von hartem Stahl bis hin zu relativ weichen Kunststoffen decken die Bearbeitungsmöglichkeiten der CNC-Technologie eine breite Palette gängiger Materialien ab:
1. Aluminiumlegierung
Wie zum Beispiel 6061 und 7075Aluminiumlegierungen sind häufig verwendete Materialien mit einer Dichte von 2,7–2,8 g/cm³ und sehr geringem Gewicht (nur etwa 40% Stahl). Sie zeichnen sich durch hohe Festigkeit, aber geringe Ermüdungsbeständigkeit und hohe Temperaturbeständigkeit aus und werden üblicherweise in verschiedenen Gehäusen oder Strukturkomponenten verwendet. Der Rahmen Ihres Telefons, Ihrer Kamera oder Ihres Computers kann aus einem einzigen CNC-gefrästen Aluminiumstück gefertigt sein. Aluminiumlegierungen weisen zudem eine gute Korrosionsbeständigkeit auf. Die dichte Aluminiumoxidschicht auf der Oberfläche isoliert Sauerstoff, Wasser und schwache Säuren/Basen wirksam vor Korrosion, erfordert jedoch zum Schutz eine Eloxierung oder Lackierung.
2. Kohlenstoffstahl
Kohlenstoffstahl wird je nach Kohlenstoffgehalt in kohlenstoffarmen Stahl (C ≤ 0,251 TP3T), mittelkohlenstoffhaltigen Stahl (C 0,251 TP3T ~ 0,61 TP3T) und kohlenstoffreichen Stahl (C ≥ 0,61 TP3T) unterteilt. Im Gegenteil, je niedriger der Gehalt, desto geringer die Härte und desto einfacher die Verarbeitung.
Kohlenstoffstahl hat eine hohe Dichte (ca. 7,8 g/cm³) und eine hohe Festigkeit. Nach Jahren der Entwicklung gibt es viele Modelle, wie z. B. Q235, A36, 1045, und so weiter, müssen Sie entsprechend der tatsächlichen Anwendung das richtige Modell auswählen. Es ist auch notwendig, die entsprechenden Probleme im Voraus während des Bearbeitungsprozesses zu berücksichtigen, beispielsweise muss beim Schneiden von kohlenstoffreichem Stahl auf den Verschleiß des Werkzeugs geachtet werden, und bei kohlenstoffarmem Stahl muss auf die scharfen Kantenrisse der Teile geachtet werden.
3. Edelstahl
Edelstahl wird durch die Zugabe von Elementen wie Chrom, Nickel, Molybdän und Stickstoff verbessert, um seine Korrosionsbeständigkeit in bestimmten Umgebungen zu erhöhen. Gemäß der metallografischen Organisation kann Edelstahl grob in drei Typen unterteilt werden: austenitischer Edelstahl (nicht magnetisch), ferritischer Edelstahl (stark magnetisch) und martensitischer Edelstahl (stark magnetisch).
Zu den austenitischen rostfreien Stählen gehören 303 Edelstahl wird aufgrund seines hohen Schwefelgehalts häufig in der CNC-Bearbeitung verwendet, was ihn leicht zu schneiden macht, aber auch zu einer geringeren Korrosionsbeständigkeit führt. Andererseits 304 und 316 Edelstahl härtet beim Schneiden stark aus und weist eine schlechte Wärmeleitfähigkeit auf. Dies führt zu einem Hitzestau während des Schneidvorgangs und erhöhtem Werkzeugverschleiß. Daher ist die Wahl des richtigen Werkzeugs und die Einstellung der richtigen Schneidparameter entscheidend.
Zu den üblichen ferritischen Edelstählen zählen 430, 439 und 444, die beim Schneiden zu Kantenausbrüchen und Spananhaftung neigen. Daher ist es notwendig, diese Probleme durch die Wahl von Werkzeugen mit TiN/TiCN-Beschichtung oder Keramikwerkzeugen zu vermeiden.
Martensitische Edelstähle sind die härtesten (HRC 50-60) und verschleißfestesten Edelstähle. Zu den gängigen Typen gehören 410, 420 und 440C, die üblicherweise bei der Herstellung von Lagern und Schneidwerkzeugen verwendet werden. Bei der Bearbeitung ist auf den Werkzeugverschleiß zu achten. Es empfiehlt sich, Werkzeuge mit hoher Härte zu wählen und eine langsame Schnittstrategie anzuwenden.
4. Titanlegierungen
Titanlegierungen haben eine geringe Dichte von 4,5 g/cm³, was etwa 601 TP3T Stahl entspricht. Ihre Festigkeit ist höher als die von Aluminiumlegierungen und Stahl. Die Zugfestigkeit kann über 1000 MPa erreichen und ist damit zwei- bis fünfmal so hoch wie die von Aluminiumlegierungen. Die Korrosions- und Temperaturbeständigkeit ist besser als die von Edelstahl und nur Platin überlegen. Zudem ist Reintitan sehr biokompatibel. Aus diesem Grund wird Titan häufig für Luft- und Raumfahrtkomponenten, medizinische Implantate und hochwertige Konsumgüter verwendet. Gängige Typen sind Reintitan (Klassen 1–4), Ti-6Al-4V (Klasse 5) und Ti-5Al-2,5Sn (Klasse 6).
Der Nachteil von Titan ist seine schwierige Zerspanung, weshalb viele bearbeitete Titanlegierungen teuer sind. Seine schlechte Wärmeleitfähigkeit kann beim Schneiden zu Hitzestaus führen, was die Werkzeugstandzeit verkürzt. Außerdem neigt Titan bei hohen Temperaturen zu chemischen Reaktionen mit dem Werkzeug, was zu Spanbildung führt und die Werkzeugstandzeit weiter verkürzt. Daher werden bei der Zerspanung in der Regel Spezialwerkzeuge, niedrige Drehzahlen und hohe Vorschübe eingesetzt.
5. Kupfer
Kupfer wird aufgrund seiner hervorragenden Duktilität, elektrischen Leitfähigkeit und Wärmeleitfähigkeit häufig in der Elektronik und im Maschinenbau eingesetzt. Häufig verwendete Modelle sind: C11000 (Reinkupfer), H62 (Cu-Zn-Legierung, Messing), QSn6.5-0.1 (Bronze).
Reines Kupfer weist eine gute Plastizität auf, was jedoch auch zu starkem Festkleben beim Schneiden führt, da Späne nicht leicht brechen und das Problem des Aufwickelns von Werkzeugen besteht, was den Einsatz von Spezialwerkzeugen und Schneidflüssigkeiten erfordert.
Messing weist aufgrund des enthaltenen Bleis die beste Schneidleistung auf, führt jedoch auch zu mehr gebrochenen Spänen und belastet leicht die Umwelt.
Zinn in Bronze führt bei der Bearbeitung zu einer Verhärtung und neigt zur Gratbildung.
6. Kunststoffe
Herkömmliche Kunststoffverarbeitungsverfahren wie Spritzguss und Blasformen erfordern hohe Kosten für die Formenherstellung. CNC-Bearbeitung eignet sich ideal für die Verifizierung von Kunststoffprototypenteilen oder die Produktion kleiner Stückzahlen. CNC-Technologie kann jedoch nur Kunststoffe mit einer bestimmten Härte verarbeiten und ist bei weicheren Materialien wie Silikon wirkungslos. Gängige CNC-bearbeitete Kunststoffe sind:
- Abs: Günstig und einfach zu verarbeiten, gute Schlagfestigkeit, wird häufig in Gehäusen elektronischer Produkte und Autoinnenräumen verwendet.
- Nylon (PA): Die Leistung der Verschleißfestigkeit und Ermüdungsbeständigkeit ist sehr gut, mit selbstschmierenden Eigenschaften, kann es in Zahnräder und Lager und andere verarbeitet werden
- Polycarbonat (PC): transparent und beständig gegen hohe Temperaturen unter 120 Grad, kann transparente Schutzhüllen und optische Linsen herstellen.
- POM(Delrin): Hohe Festigkeit, hohe Dichte, niedriger Oberflächenreibungskoeffizient, geeignet für die Herstellung von Präzisionsteilen wie Zahnrädern.
- SPÄHEN: Hohe Temperatur Widerstand von 260 °C, chemische Korrosionsbeständigkeit, bessere Festigkeit als POM, Zugfestigkeit kann mehr als 90 MPa erreichen.
- HDPE: Lebensmittelechtes Material, weiche Textur.
- PTFE: Es ist hitzebeständig bis 260 °C, hat eine antihaftbeschichtete und isolierende Wirkung und wird häufig für verschiedene Beschichtungen verwendet, beispielsweise für Pfannen und Backöfen.
Aufgrund der Eigenschaften von Kunststoffen muss auf die Kontrolle der Schnitttemperatur geachtet werden, um ein Schmelzen während des Schneidvorgangs zu verhindern. Verwenden Sie scharfe Messer, um Kantengrate zu vermeiden. Erhöhen Sie die Drehzahl und verringern Sie die Schnitttiefe, um eine Materialverformung zu verhindern.
Bei der Auswahl des richtigen Materials sollten Sie nicht nur die Leistung berücksichtigen, sondern auch den Preis. Titanlegierungen sind unter den Metallen am teuersten und etwa 10- bis 15-mal teurer als Aluminiumlegierungen. Aluminium ist zwar die optimale Lösung für leichte Anforderungen, aber der Preis ist relativ günstig und liegt etwas unter dem von Edelstahl. Viele denken, Kunststoff sei günstiger als Metall. Tatsächlich ist ABS unter den gängigen Kunststoffen sogar teurer als Kohlenstoffstahl, Teflon, POM und andere Materialien sind sogar teurer als Edelstahl, PEEK hingegen am teuersten und preislich vergleichbar mit Titanlegierungen.
CNC-Bearbeitungstoleranz
Die Genauigkeit der CNC-Bearbeitung wird auf verschiedene Arten gemessen: Maßgenauigkeit (IT-Toleranzgrade), geometrische Genauigkeit (Form-/Lagetoleranzen) und Oberflächenqualität (Ra-Wert der Rauheit).
1. Maßgenauigkeit
Unter Maßgenauigkeit versteht man den Abweichungsbereich zwischen den tatsächlich gemessenen Abmessungen eines bearbeiteten Teils und den in der Zeichnung angegebenen Abmessungen. Sie wird üblicherweise in Toleranzklassen (IT) ausgedrückt, wobei kleinere Werte eine höhere Genauigkeit bedeuten.
Toleranzklassen werden von der Internationalen Organisation für Normung (ISO) definiert. Sie unterteilt Abmessungen von 0 bis 3150 mm in verschiedene Größenklassen, die jeweils einen bestimmten Maßgenauigkeitswert von IT01 bis IT18 definieren. Detaillierte Informationen finden Sie auf Seite 26 des ISO 286-1-Dokuments: ISO 286-1
Bei der Bearbeitung wird die Maßgenauigkeit von verschiedenen Faktoren beeinflusst, wie z. B. der Leistungsfähigkeit der Werkzeugmaschine, der CNC-Steuerung und den Prozessparametern. Die mit einer normalen CNC-Maschine erreichbare Maßgenauigkeit liegt zwischen IT7 und IT8. In der Praxis liegt die Genauigkeit der Grobbearbeitung üblicherweise bei IT12–IT18, die Genauigkeit allgemeiner mechanischer Teile bei IT8–IT11 und die Genauigkeit von Präzisionsteilen bei IT5–IT7. IT01–IT4 gehört zur Nanoebene der Ultrapräzisionsbearbeitung, die sehr kostspielig ist.
2. Geometrische Genauigkeit
Die geometrische Genauigkeit, auch bekannt als Form- und Lagetoleranz (GD&T), ist ein wichtiges Maß dafür, wie gut Form, Ausrichtung und Lage eines Teils mit den gewünschten geometrischen Merkmalen der Konstruktionszeichnung übereinstimmen. Sie hat direkten Einfluss auf die Montagegenauigkeit und Lebensdauer eines Teils. Im Gegensatz zur Maßgenauigkeit, die sich auf die Größe des Teils konzentriert, konzentriert sich die geometrische Genauigkeit auf die Genauigkeit von Form und Lage. Beide Messwerte können mit einer Koordinatenmessmaschine (KMG) gemessen werden.
Es gibt vier Kernkonzepte der geometrischen Genauigkeit: Form, Ausrichtung, Position und Rundlauf.
- Bilden: Die Abweichung der tatsächlichen Form von der entworfenen Form, zB Ebenheit, Rundheit.
- Standort: Koaxialität und Symmetrie axialer oder rotierender Teile.
- Orientierungsgenauigkeit (Orientierung): Ob die verschiedenen Ebenen des Teils parallel oder senkrecht zueinander sind.
- Auslaufen: Der Grad der Abweichung der Oberfläche oder Achse eines rotierenden Teils von der Konstruktionszeichnung, der sich direkt auf die Balance des rotierenden Teils auswirkt.
Der ISO 1101-Standard definiert eine Reihe von Symbolen für jeden Typ geometrischer Genauigkeit, von denen einige aus dem Standard extrahiert wurden.
Eigenschaften | Symbol |
Geradheit | ▭ |
Rundheit | ○ |
Zylindrizität | ⌭ |
Parallelität | ∥ |
Rechtwinkligkeit | ⊥ |
Koaxialität (für Achsen) | ◎ |
Rundlauf | ↗ |
Wenn Sie wissen möchten, wie man geometrische Genauigkeit misst oder weitere Informationen zu geometrischen Genauigkeitssymbolen benötigen, lesen Sie bitte unsere Seite über geometrische Genauigkeit oder zum ISO-1101 Standarddokument.
3. Oberflächenrauheit
Die Oberflächenrauheit ist ein Maß für die Glätte der Oberfläche eines Teils und beeinflusst direkt Reibung, Verschleiß, Dichtheit und Dauerfestigkeit. Die wichtigsten Parameter und Messmethoden für die Oberflächenrauheit folgen derzeit den ISO 21920 Standard.
Die am häufigsten verwendeten Rauheitsindikatoren sind Ra (arithmetischer Mittenrauwert) und Rz (maximale Höhenrauheit) in µm.
Die Messung von Ra erfolgt durch Abtasten der Werkstückoberfläche mit einem Tastschnittgerät oder Laserscanner und Messen des Absolutwerts der höchsten und niedrigsten Punkte innerhalb einer einzigen Messstrecke relativ zur im Design gewünschten absoluten glatten Ebene (Bezugsebene). Aus den Werten mehrerer Messstrecken wird ein arithmetischer Mittelwert berechnet. Die Messstrecke ist in der ISO-Norm festgelegt. Beispielsweise ist für eine Zielrauheit Ra ≥ 10 eine Messstrecke von 2,5 mm vorgeschrieben. Dies spiegelt die Gesamtrauheit des Werkstücks wider und ist in 90% für industrielle Szenarien anwendbar.
Rz wird durch direkte Messung des Höhenunterschieds zwischen dem höchsten und dem niedrigsten Punkt innerhalb der Probenlänge ermittelt und dient zur Messung der Rauheit kritischer Bereiche.
Diese drei Maßnahmen bestimmen die Genauigkeit eines Teils von der Makro- bis zur Mikroebene. Maßgenauigkeit bildet die Grundlage, geometrische Genauigkeit sichert die Funktion des Teils und die Oberflächenrauheit bestimmt Leistung und Lebensdauer. Während des Konstruktions- und Produktionsprozesses sollten diese drei Maßnahmen für jedes Teil priorisiert werden, um eine Überkonstruktion zu vermeiden, die zu hohen Bearbeitungskosten führen kann.
Anwendungen der CNC-Bearbeitung
Die CNC-Bearbeitung ist eine sehr flexible und weit verbreitete Bearbeitungstechnologie. Seit ihrer Einführung, nach mehr als 70 Jahren Entwicklung, hat die CNC-Technologie ein komplettes Set an Verarbeitungssystemen gebildet, das alle Aspekte unseres Lebens abdeckt.
Luft- und Raumfahrt
Die CNC-Technologie hat die rasante Entwicklung der Luft- und Raumfahrt vorangetrieben. Um den rauen Bedingungen in großen Höhen und im Weltraum gerecht zu werden, erfordert der Flugzeugbau die Verwendung hochfester Materialien. Alle Teile müssen eng aneinandergefügt sein, da jeder kleinste Spalt schwerwiegende Folgen haben kann. Die präzise 5-Achsen-Werkzeugmaschine kann Titanlegierungen, Nickelbasislegierungen und verschiedene Speziallegierungen der Luft- und Raumfahrt verarbeiten und erreicht dabei eine Genauigkeit im Mikrometerbereich. Damit erfüllt sie perfekt die Anforderungen der Luft- und Raumfahrtindustrie an Teilegenauigkeit, Festigkeit und schnelle Prototyping-Iteration.
Automobilindustrie
Stanzformen für Automobilkarosserien, Spritzgussformen für Kunststoffinnenausstattungen, Kurbelwellen, Zahnräder, Achsschenkel, Motorgehäuse, Rotoren, Spindeln für Fahrzeuge mit alternativer Antriebstechnik usw. 90% – viele Autoteile basieren direkt oder indirekt auf CNC-Technologie. Darüber hinaus ermöglicht die intelligente CNC-Bearbeitungslinie eine vollautomatische Produktion und Prüfung und passt die Bearbeitungsparameter in Echtzeit an die jeweiligen Teile an. Dies steigert die Ausbeute und Produktionseffizienz deutlich und legt den Grundstein für die rasante Entwicklung der Automobilindustrie.
Medizinische Industrie
Die größte Revolution, die die CNC-Technologie in der Medizinbranche gebracht hat, ist die Möglichkeit, medizinische Lösungen individuell anzupassen. Ärzte können nun den gebrochenen Knochen durch 3D-Scannen modellieren, dann mithilfe professioneller Software das passende Implantat entwerfen und schließlich 5-Achsen-CNC Technologie zur Bearbeitung des geformten Implantats. Der Behandlungszyklus wird verkürzt und der Komfort des Patienten verbessert.
Elektronik und Konsumgüter
Heutzutage ist die Fülle an Elektronik- und Konsumgütern untrennbar mit der CNC-Technologie verbunden. Im Bereich Mobiltelefone und Computer erscheinen jährlich weltweit Tausende neuer Produkte. Die Gehäuse und Rahmen dieser Produkte basieren auf Präzisionsformen, die von CNC-Werkzeugmaschinen hergestellt werden. Einige Marken verwenden auch direkt CNC-gefräste Gehäuse aus Aluminiumlegierungen, wie beispielsweise Apples iPad und Mac.
Prototyping und kundenspezifische Produkte
Prototyping und die Herstellung kundenspezifischer Produkte sind Bereiche, in denen CNC-Maschinen herausragend sind. Sie können komplexe gekrümmte Oberflächen mit höchster Präzision bearbeiten. Ob es darum geht, die Harmonie dekorativer Komponenten oder die Zuverlässigkeit des Designs funktionaler Teile zu überprüfen – auf CNC-Technologie ist Verlass.
Vorteile und Einschränkungen der CNC-Bearbeitung
Vorteile: Präzision und Genauigkeit
CNC-Bearbeitung ist hochpräzise und erreicht Genauigkeiten im Mikrometerbereich. Sie eignet sich für die Bearbeitung von Präzisionsteilen und bietet auch bei wiederholter Produktion eine stabile Qualität. Die maßgeschneiderte CNC-Produktionslinie ermöglicht eine automatische, kontinuierliche Bearbeitung und automatische Erkennung mit weniger manuellen Eingriffen und eignet sich daher hervorragend für die Produktion von Großserienteilen. Die Mehrachsen-Kopplung ermöglicht die Bearbeitung komplexer gekrümmter Oberflächen und Hohlstrukturen, die mit herkömmlichen Methoden nur schwer zu erreichen sind. Besonders hervorzuheben ist die Flexibilität der CNC-Bearbeitung: Durch einfaches Wechseln der Programme können Sie unterschiedliche Produkte bearbeiten. Durch Werkzeugwechsel und Anpassung der Bearbeitungsparameter können Sie eine Vielzahl von Materialien wie Metalle, Kunststoffe und Verbundwerkstoffe bearbeiten.
Einschränkungen: Hohe Maschinenkosten, professioneller Bediener erforderlich
In Bezug auf die Bearbeitungskapazität sind extrem tiefe Hohlräume, interne Details und spezielle Winkel mit CNC-Technologie schwer zu bearbeiten, was hauptsächlich auf die physikalischen Einschränkungen des Werkzeugs zurückzuführen ist. Beispielsweise wird das interne Wärmeableitungsrohr des Motors hauptsächlich durch integriertes Gussteil bearbeitet.
Darüber hinaus sind die Anfangsinvestitionen für CNC-Maschinen sehr hoch. Der Kauf von Maschinen ist nur der erste Schritt. Sie müssen auch Prüfgeräte ausrüsten und professionelles Programmier- und Bedienpersonal einstellen. Diese Anfangsinvestitionen schrecken viele ab und führen dazu, dass sie sich stattdessen für CNC-Fabriken entscheiden, die Bearbeitungsdienstleistungen anbieten.
Kurz gesagt: Die CNC-Bearbeitung bietet herausragende Vorteile bei der Herstellung präziser, effizienter und komplexer Teile, hat aber auch ihre Grenzen, und wir müssen je nach den tatsächlichen Anforderungen die geeignete Bearbeitungsmethode wählen.
CNC-Bearbeitungskosten
Viele Faktoren beeinflussen die Kosten der CNC-Bearbeitung. Im Folgenden analysieren wir die Kosten der CNC-Bearbeitung unter verschiedenen Gesichtspunkten.
- Ausstattung: Die Kosten für Nutzung, Wartung und Arbeitsaufwand moderner Werkzeugmaschinen sind höher. Die stündlichen Bearbeitungskosten einer 5-Achs-Maschine sind in der Regel zwei- bis dreimal so hoch wie die einer 3-Achs-Maschine. Dies bedeutet jedoch nicht, dass die Kosten für eine 3-Achs-Maschine am niedrigsten sind. 5-Achs-Maschinen bearbeiten komplexe Teile effizienter und weisen einen geringeren Materialverlust auf. Je komplexer die Teile, desto kostengünstiger ist die 5-Achs-Bearbeitung.
- Materialien: Der Materialpreis wirkt sich direkt auf den Produktpreis aus. Auch die Schwierigkeit der Verarbeitung verschiedener Materialien ist ein Faktor, der berücksichtigt werden muss. Beispielsweise erfordert die Verarbeitung von Titanlegierungen den Einsatz von Spezialwerkzeugen. Die Verarbeitungszeit ist länger als bei Aluminiumlegierungen, was naturgemäß zu höheren Kosten führt.
- Menge: Durch die Massenproduktion werden die Kosten für Vorentwurf und Inbetriebnahme reduziert. Gleichzeitig können Hersteller den Prozess kontinuierlich optimieren und die Stückkosten in der Großserienproduktion senken.
- Komplexität der Teile: Ähnlich wie komplexe und schwer zu bearbeitende Formen wie gekrümmte Oberflächen, dünne Wände, tiefe Hohlräume usw. erfordern sie mehr Prozesse und Zeit.
- Bearbeitungsgenauigkeit: Strenge Anforderungen an Toleranzen und Oberflächenrauheit erhöhen unmittelbar die Bearbeitungszeit und die Kosten nach der Prüfung. Darüber hinaus ist auch die Ausschussrate höher, was zu einem starken Kostenanstieg führt.
Um Kosten effektiv zu senken, sollten wir bereits in der Entwurfsphase dem Konzept des Design for Manufacturing (DFM) folgen und die Bearbeitbarkeit umfassend berücksichtigen. Achten Sie auf die Funktionalität der Teile, reduzieren Sie die Genauigkeitsanforderungen in unkritischen Bereichen, während Sie gleichzeitig die funktionalen Anforderungen erfüllen, und vermeiden Sie eine Überkonstruktion.
CNC-Bearbeitung vs. traditionelle Bearbeitung
Im Vergleich zu herkömmlichen Bearbeitungsverfahren liegen die Vorteile der CNC-Bearbeitung vor allem in der Präzision und Flexibilität.
CNC-Bearbeitung vs. Gießen
Das Gussverfahren wird hauptsächlich in drei Typen unterteilt. Sandguss ist kostengünstig und eignet sich für die Herstellung großer Teile mit geringen Anforderungen an die Präzision. Feinguss erfordert die Herstellung von Formen zur Herstellung von Wachsmodellen, und der Prozess ist relativ komplex, was für die Massenproduktion von Teilen mit komplexen Strukturen geeignet ist. Druckguss erfordert auch zunächst die Entwicklung von Formen, die für die Herstellung hochpräziser Teile geeignet sind.
Der erste Nachteil des Gießens im Vergleich zur CNC-Bearbeitung ist die mangelnde Flexibilität. Gießen eignet sich nur zur Herstellung von Metallteilen (z. B. Aluminium, Edelstahl, Inconel usw.), und jede Form kann nur ein bestimmtes Produkt produzieren. Der zweite Nachteil ist, dass die Gussteile oft nachbearbeitet werden müssen. In der Massenproduktion ist Gießen jedoch die bessere Wahl. Bei der Massenproduktion können die anfänglichen Kosten für die Formenherstellung vernachlässigt werden.
CNC vs. Schmieden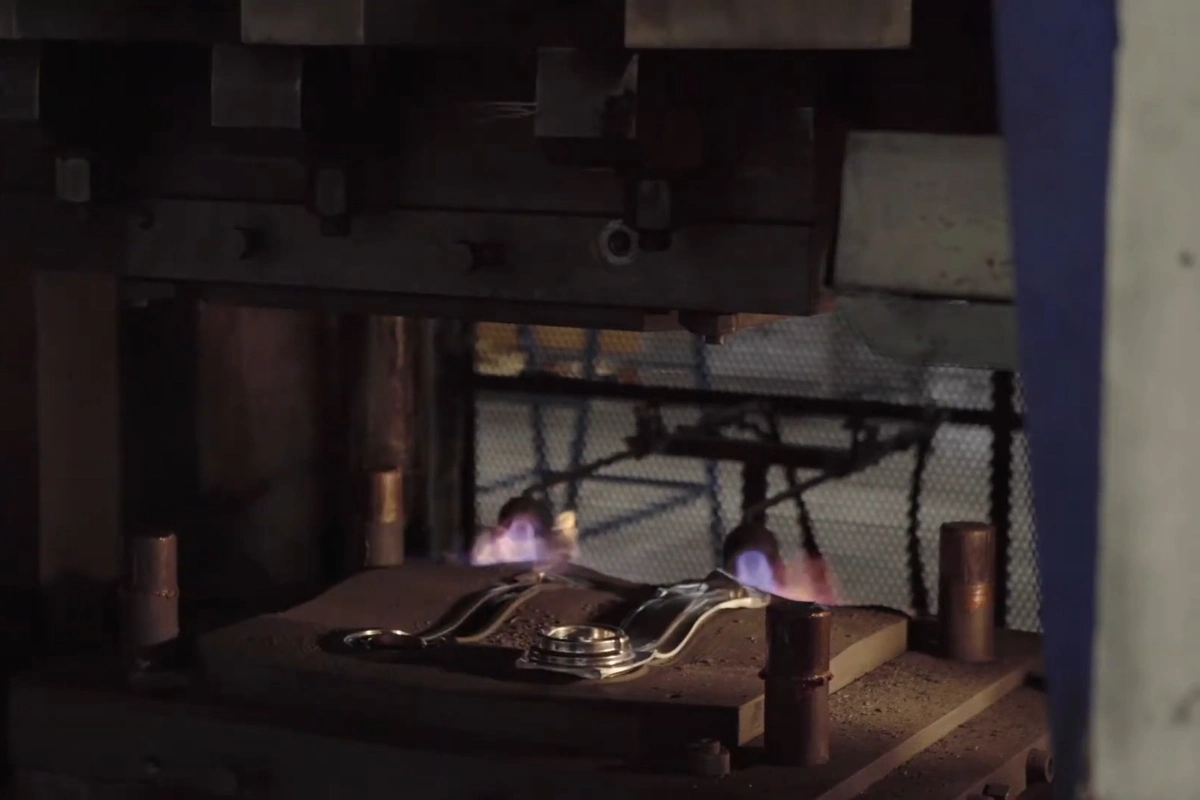
Beim Schmieden unterscheidet man hauptsächlich zwischen Freiformschmieden und Gesenkschmieden. Freiformschmieden erfordert keine Formen, weist eine geringe Präzision auf, erfordert eine Nachbearbeitung und eignet sich für die Kleinserienfertigung großer Teile. Gesenkschmieden Schmieden erfordert den Einsatz von Formen, mit denen Teile mit hoher Präzision und komplexen Formen hergestellt werden können.
Im Vergleich zur CNC-Bearbeitung liegt der Nachteil des Schmiedens in der mangelnden Flexibilität. Die Vorteile des Schmiedens liegen jedoch auf der Hand: Durch hohe Temperaturen und hohen Druck verändert sich die innere Gitterstruktur des Metalls, wodurch Teile mit höherer Festigkeit als bei anderen Verarbeitungsverfahren hergestellt werden können. Schmieden ist die bessere Wahl für die Massenproduktion von Schlüsselkomponenten, die eine hohe Festigkeit erfordern (wie Pleuelstangen, Zahnräder, Wellen usw.).
Im eigentlichen Produktionsprozess sind häufig verschiedene Prozesse erforderlich, um bei der Herstellung eines Produkts zusammenzuarbeiten. Die CNC-Bearbeitung wird hauptsächlich im Nachbearbeitungsprozess von Schmiede- und Gussteilen eingesetzt.
Trends in der CNC-Bearbeitung
Mit der Entwicklung von Wissenschaft und Technologie entwickelt sich die CNC-Bearbeitung in Richtung hochpräziser, intelligenter, automatisierter und multitechnologischer Integration.
1. Intelligenz und Automatisierung
Künstliche Intelligenz hat in den letzten zwei Jahren ein explosionsartiges Wachstum erlebt. Immer mehr Pioniere versuchen, KI in ihre eigenen Branchen zu integrieren und so der Entwicklung der Branche neuen Schwung zu verleihen. Die CNC-Bearbeitung bildet da keine Ausnahme. Viele Werkzeugmaschinenhersteller versuchen, KI gezielt zu trainieren und kombinieren KI mit CNC-Maschinen und Robotern, um mannlose intelligente Werkstätten (Lights-out Manufacturing) zu realisieren.
2. Hohe Präzision
Hohe Präzision war schon immer unser Ziel, denn hochpräzise Instrumente und Geräte fördern die Entwicklung von Wissenschaft und Technologie. Durchbrüche bei Linearmotoren, Gitterlinealen und anderen Technologien haben die Präzision der CNC-Bearbeitung auf den Nanometerbereich gebracht.
3. Multi-Technologie-Integration
Multitechnologie-Fusion ist nicht einfach die Nutzung mehrerer Technologien bei der Bearbeitung eines Teils, sondern die Integration mehrerer Technologien in ein Gerät. Beispielsweise führt dieselbe Maschine beim 3D-Druck + CNC den 3D-Druck und die CNC-Bearbeitung durch. Dadurch können Fehler, die durch den Wechsel zwischen mehreren Geräten entstehen, effektiv reduziert und die Verarbeitungseffizienz verbessert werden.
4. Neue Materialien
Schneidwerkzeuge wirken sich direkt auf die Bearbeitungsmöglichkeiten aus und die Forschung und Entwicklung einer Vielzahl neuer Materialwerkzeuge, wie polykristalliner Diamant (PCD) und kubisches Bornitrid (CBN), entwickelt die Bearbeitungsmöglichkeiten der CNC-Technologie ständig weiter.
Fazit
CNC-Bearbeitung ist die Kerntechnologie der modernen Fertigung. Sie integriert Informatik, Maschinenbau, Automatisierung und Werkstofftechnik und fördert so kontinuierlich die Entwicklung verschiedener Branchen. Durch die Integration von KI und die Erforschung der Multitechnologie-Integration erweitert die CNC-Bearbeitung kontinuierlich die Grenzen der Fertigung und lässt komplexe Designs Wirklichkeit werden.
FAQ
Wenn Sie G-Code lesen möchten und viel Zeit zum Lernen benötigen, empfehlen wir Ihnen, die G-Code-Tutorial des CNC Cook Book oder lesen Sie unser G-Code-Seite um schnell die Bedeutung häufig verwendeter G-Codes herauszufinden.
GD&T ist die Abkürzung für Geometric Dimensioning and Tolerancing (Geometrische Bemaßung und Toleranz), ein System zur Quantifizierung und Messung der Bearbeitungsgenauigkeit.
Wir bieten alle CNC-Bearbeitungsdienste an, einschließlich 5-Achsen-CNC-Bearbeitung, Laserschneiden, Wasserstrahlschneiden, 3D-Druck und so weiter.
Entdecken Sie mehr mit unseren Blogbeiträgen.
kürzliche Posts
Erfahren Sie mehr über unsere Produkte.
Produkte
Sofortiges Angebot!