- Home
- Finishes
HDC Offers a Variety of Finishes for Your Custom Parts
Discover the diverse range of custom finishes HDC offers to enhance the durability, aesthetics, and performance of your precision components. Explore our advanced finishing techniques tailored to meet the unique requirements of various industries.
The Role of Finishes in Custom Part Manufacturing
Finishes are critical components of the manufacturing process, providing both protective and aesthetic enhancements to custom parts. Applied at the final stages of production, finishes improve the product’s appearance, making it more appealing to customers. But the benefits of finishes extend far beyond just good looks. They also play a vital role in enhancing the durability and performance of the parts, making them capable of withstanding harsh environments and prolonged use.
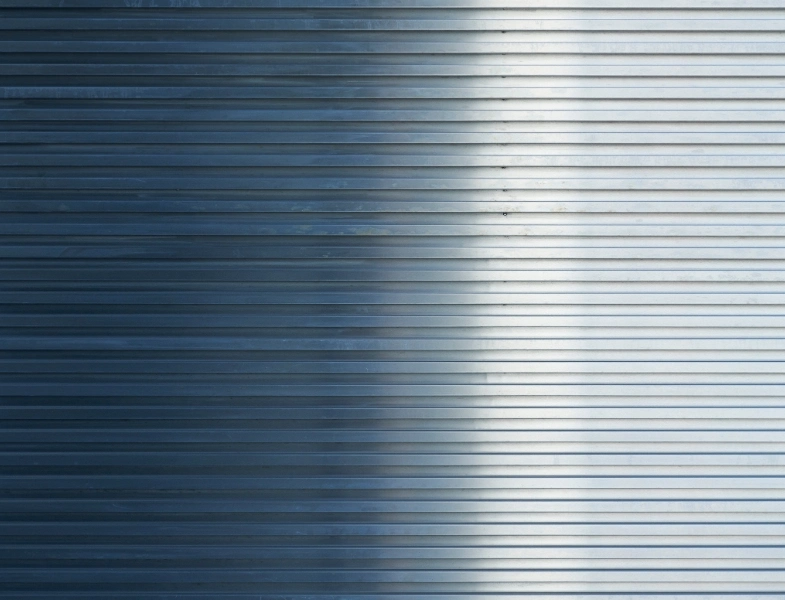
The primary functional benefits of applying finishes to custom parts include:
- Corrosion Resistance: Finishes form a barrier against environmental factors that can lead to corrosion, thus prolonging the lifespan of the part.
- Improved Wear Resistance: Certain finishes increase the surface hardness of the part, making it more resistant to wear and tear from physical contact.
- Aesthetic Enhancement: Finishes can be used to add color, gloss, or texture to parts, enhancing their visual appeal and aligning with brand aesthetics.
- Environmental Protection: By protecting the underlying material from harsh conditions, finishes help prevent material degradation and maintain the part’s integrity over time.
Each type of finish brings its own set of advantages, allowing manufacturers to select the one most suited to their specific needs, thereby ensuring that the final product not only meets but exceeds customer expectations.
Unmatched Benefits of HDC's Finishing Services
Find Out Diverse Finishes We Provide For Metal Parts
Explore the range of finishes HDC offers to enhance and protect your custom parts with both functionality and flair.
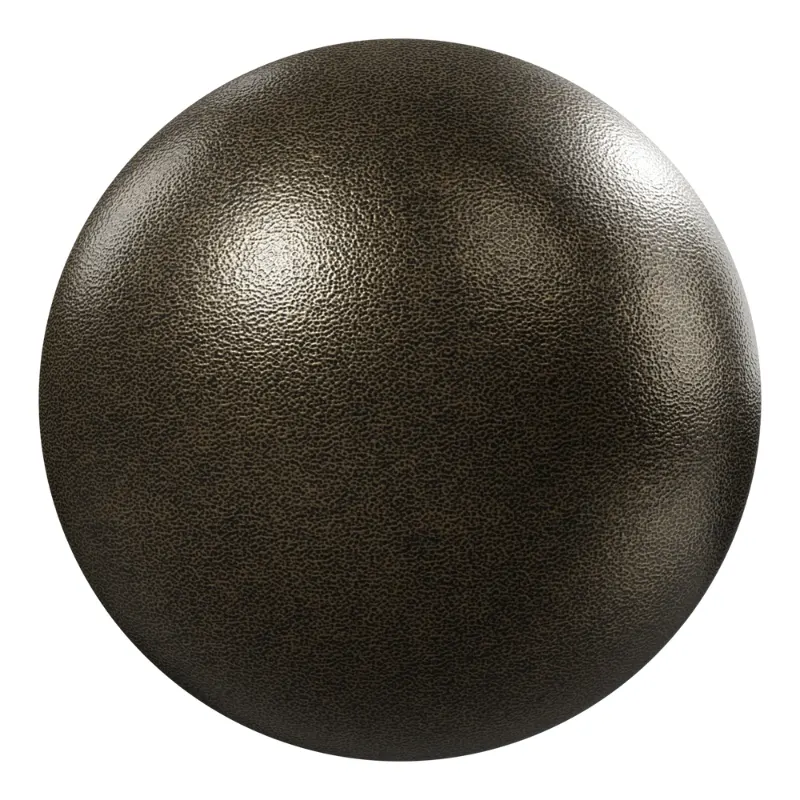
Powder Coating
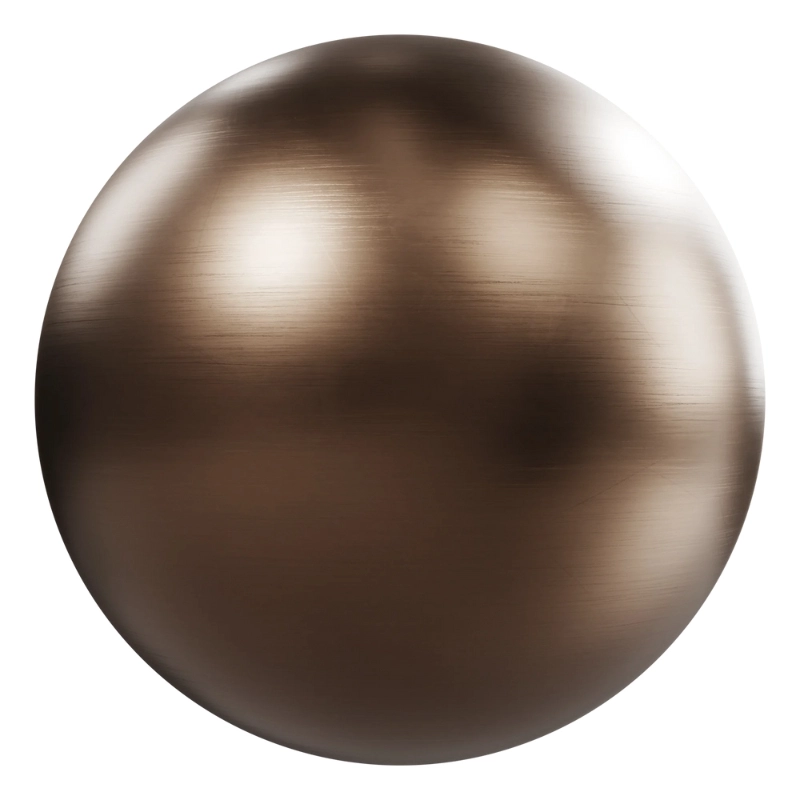
Anodizing
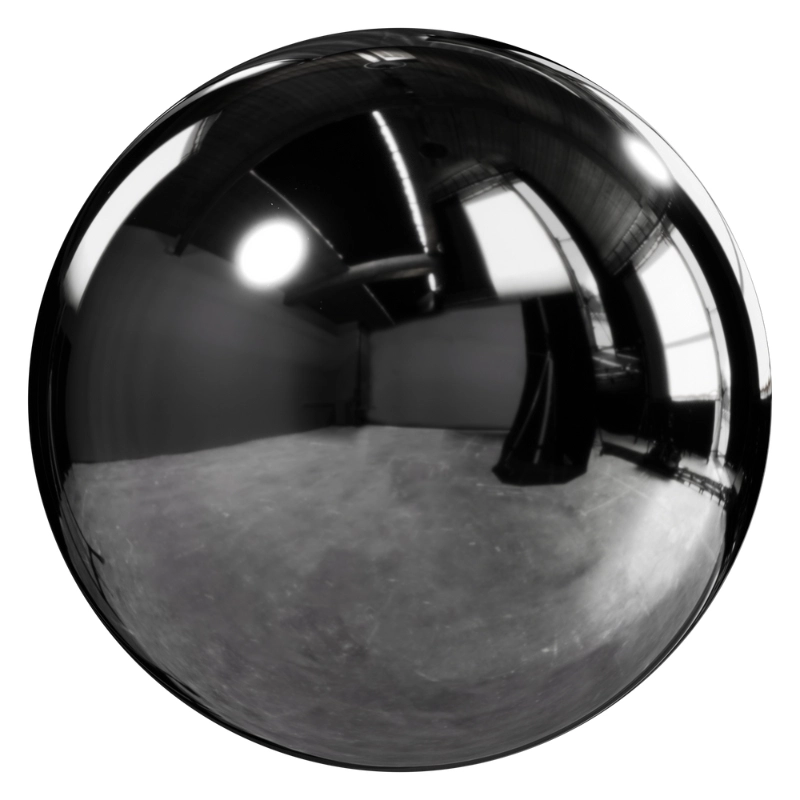
Chrome Plating

Nickel Plating
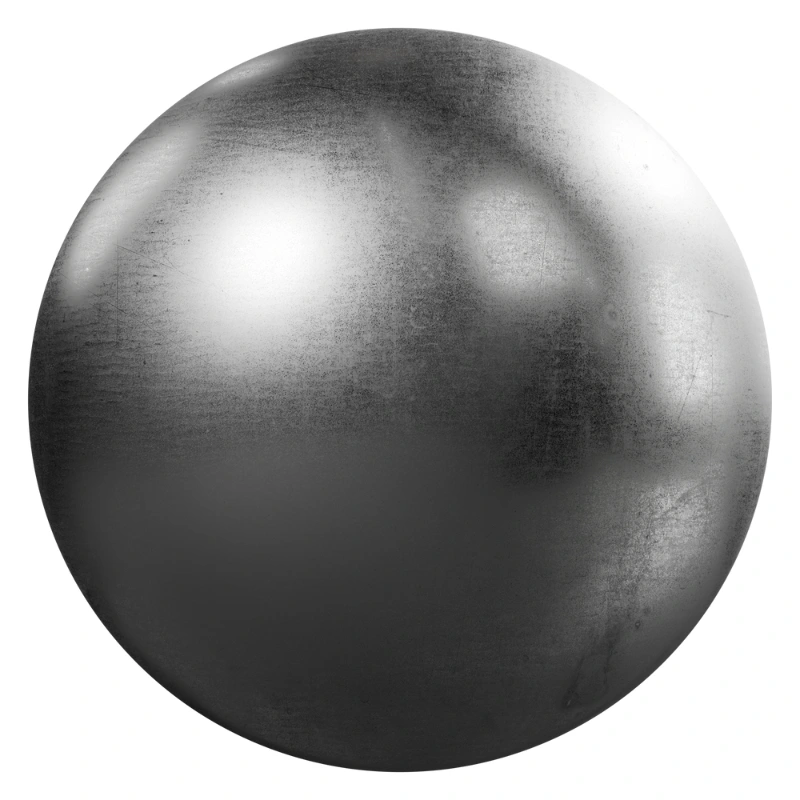
Zinc Plating
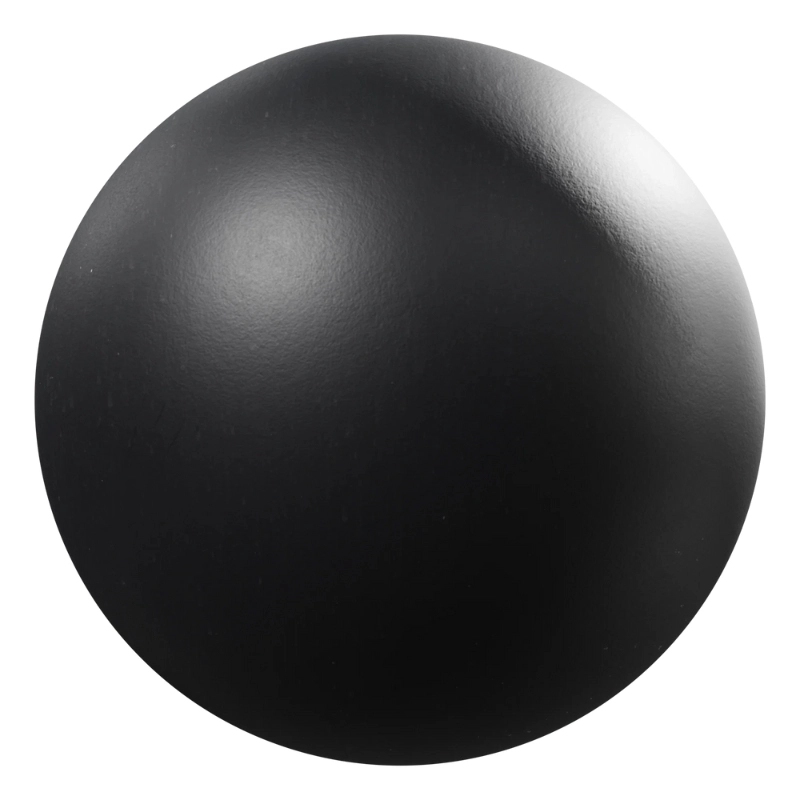
Painting
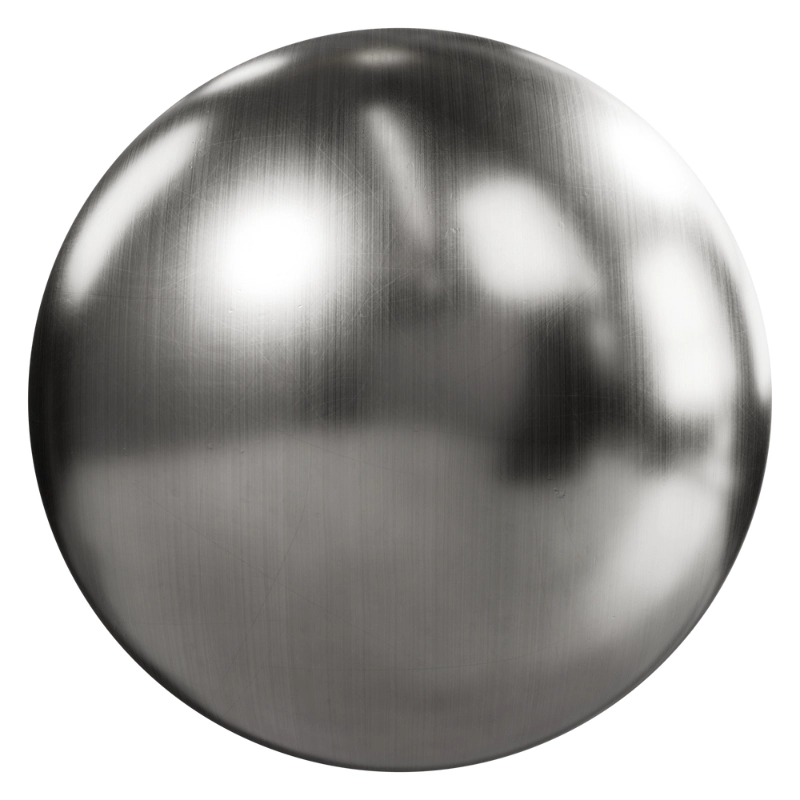
Polishing
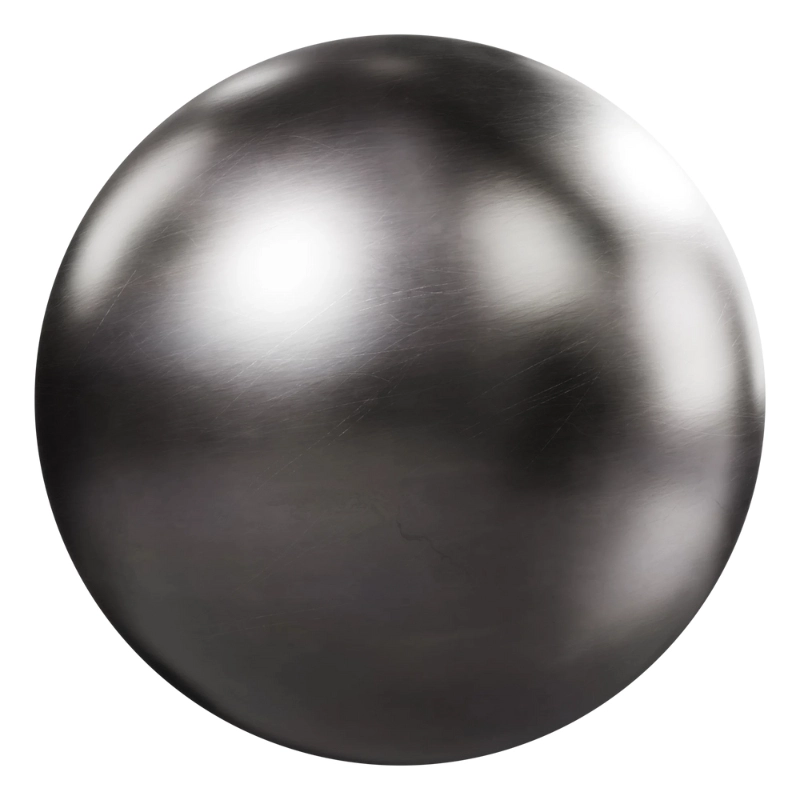
As Machined
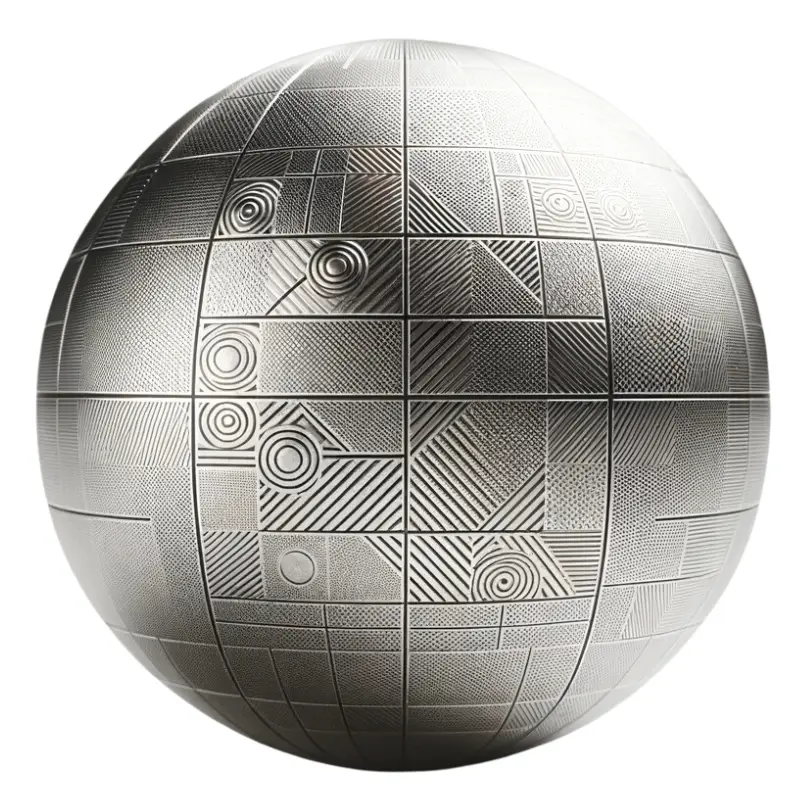
Laser Engraving
Showcase of Product Finishes
Explore our photo gallery to see the diverse and high-quality finishes we can provide for your custom products.
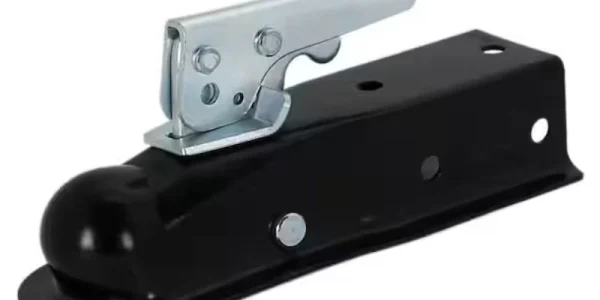
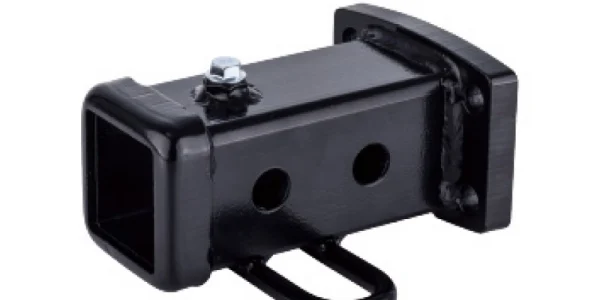
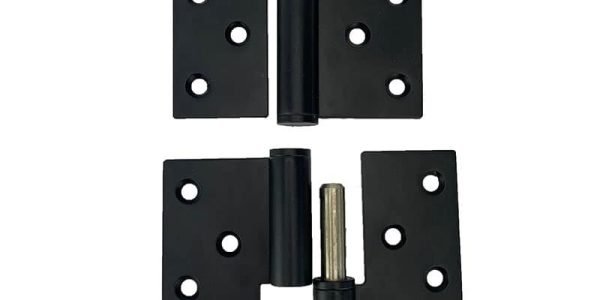
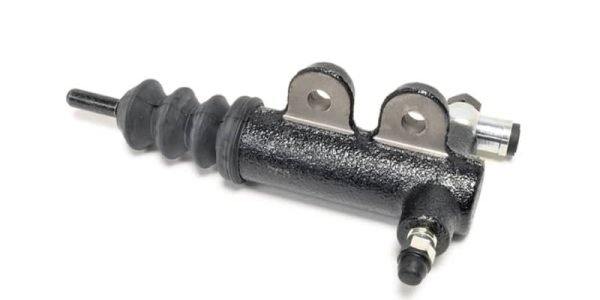

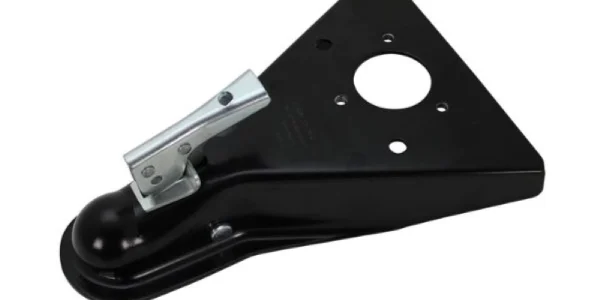
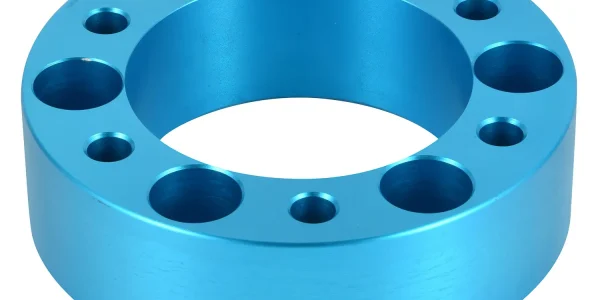
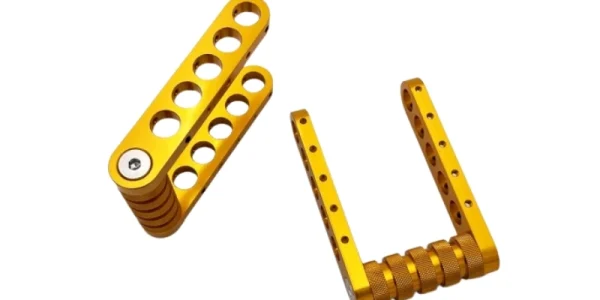

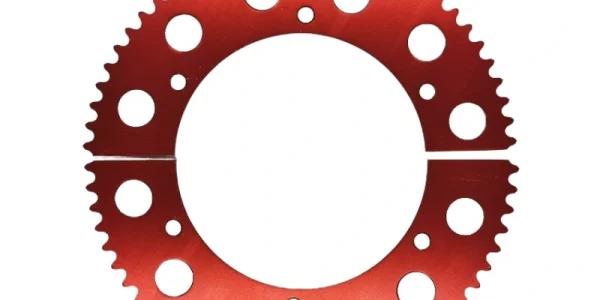
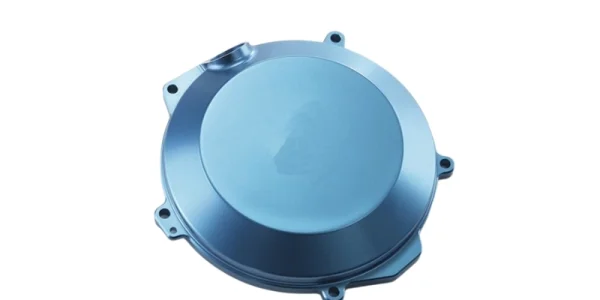
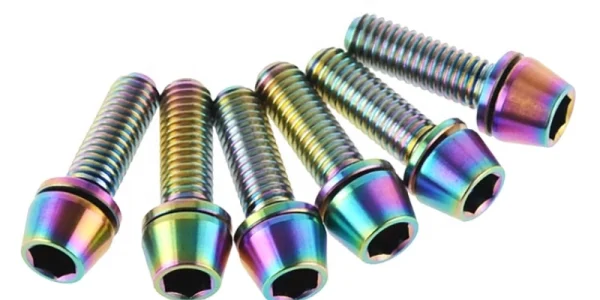
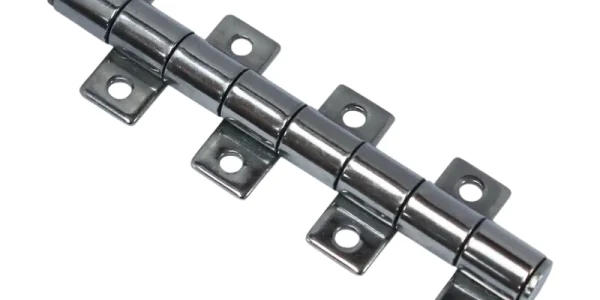
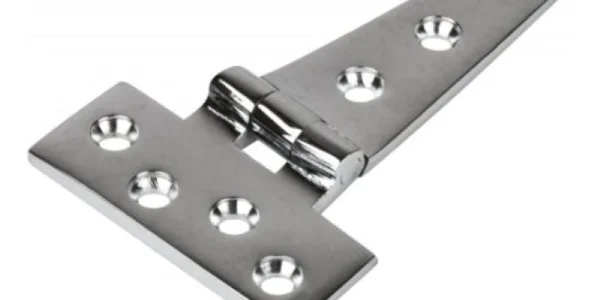
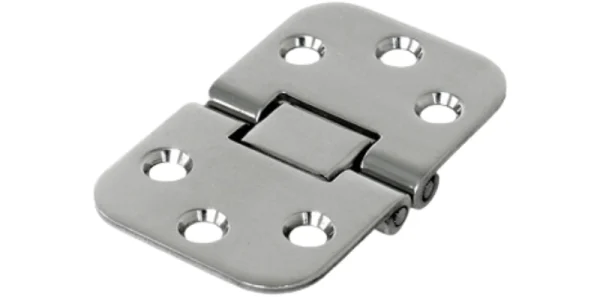
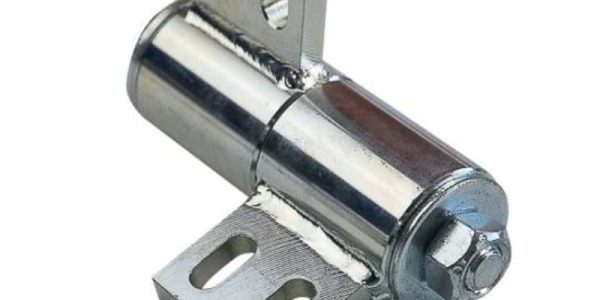
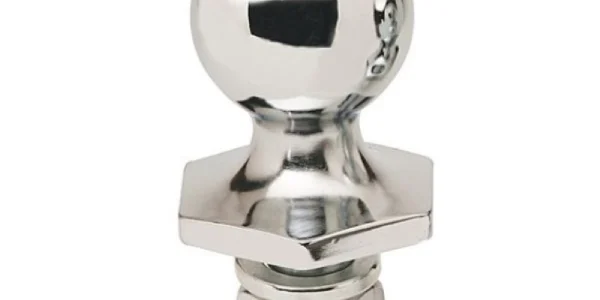
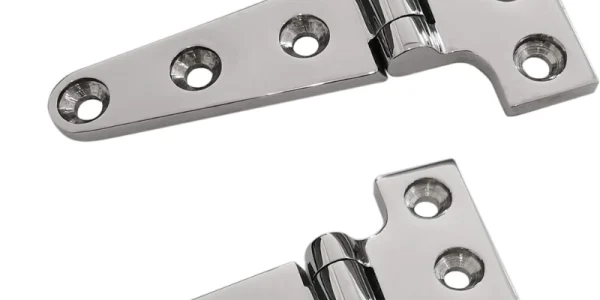
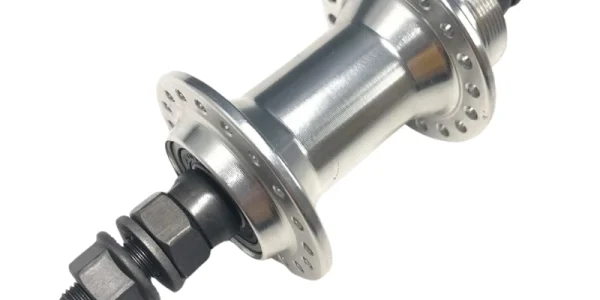
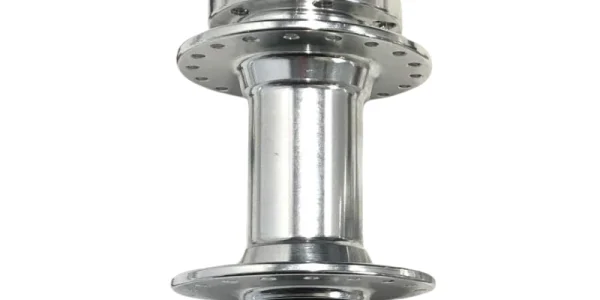
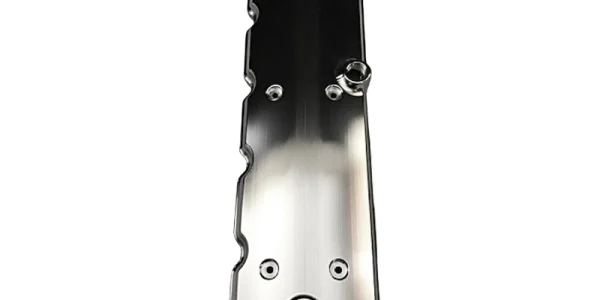
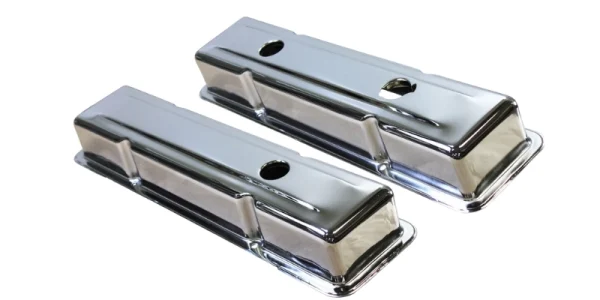




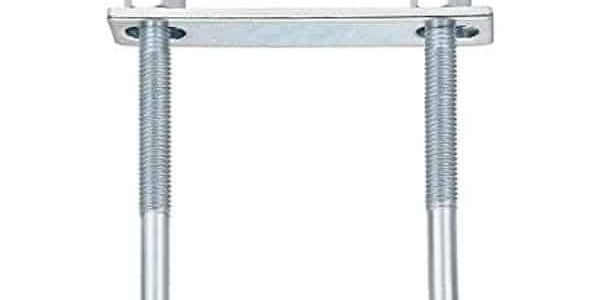
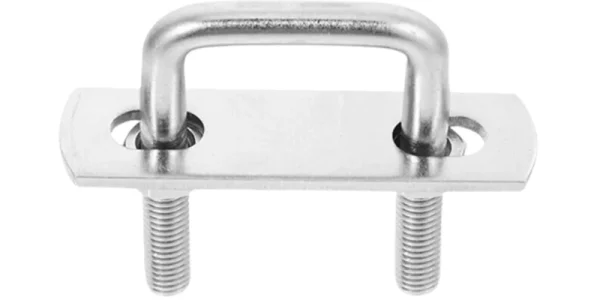
Technical Specifications of HDC's Finishes
Explore the precise thickness, durability, maintenance, and compliance details of our finishes to choose the best option for your project needs.
Thickness Specifications
- Powder Coating: Typically applied at 60-80 microns to ensure optimal coverage and durability.
- Anodizing: Ranges from 5 microns for type II decorative finishes to 25 microns for type III hard anodizing used in harsh environments.
- Chrome Plating: Usually applied between 0.5 to 20 microns, depending on the required resistance to wear and corrosion.
Durability and Performance
- Painting: Tested for up to 500 hours of salt spray resistance, ensuring long-term performance in corrosive environments.
- Zinc Plating: Offers cathodic protection, with lifespan assessments showing effectiveness for up to 96 hours in salt spray tests without red rust.
Maintenance Recommendations
- Nickel Plating: Requires regular cleaning with non-abrasive, pH-neutral cleaners to maintain its luster and prevent tarnishing.
- Polymeric Coatings: Simple maintenance involving routine washing with mild detergents; resistant to most chemical solvents, ensuring easy upkeep.
Standards and Compliance
- All finishes are applied in accordance with ISO 9001 quality standards, ensuring consistent quality management and process control.
- Environmental compliance with EPA regulations for VOC emissions in finishes, ensuring sustainability and safety.
FAQ
Find answers to common questions about our finishing processes and their benefits in our comprehensive FAQ section.
Powder coating offers excellent durability, impact resistance, and corrosion protection. It also provides a wide range of color options with a uniform finish that is more environmentally friendly compared to traditional liquid paints.
Anodizing enhances the natural oxide layer on aluminum, increasing its corrosion and wear resistance. It also allows for dyeing the metal in various colors, improving both cosmetic and mechanical properties.
Yes, plastics can be plated with metals such as chrome or nickel. This process enhances the aesthetic appeal of plastic parts, making them look metallic and more durable. It also improves wear resistance and electrical conductivity.
Laser engraving uses a high-powered laser beam to etch designs or text into the surface of a metal, creating precise and permanent markings. It is commonly used for serialization, branding, and decorative purposes.
For outdoor metal furniture, finishes that provide excellent UV resistance and weatherproofing are ideal. Powder coating and UV protective paints are highly recommended due to their durability and resistance to fading and weather conditions.
UV coating on plastic parts adds a protective layer that resists sun damage, prolonging the part's lifespan and maintaining its appearance by preventing fading and brittleness.
Pad printing can transfer 2D images onto 3D objects, making it ideal for printing on irregular surfaces like appliances and electronics. Screen printing, however, is better suited for larger, flatter surfaces and allows for thicker ink application, which can be more durable.
Our Products With Various Finishes
Explore our products to see how HDC's advanced finishing techniques enhance both the performance and aesthetics of our products, providing a closer look at the quality we deliver.
Request a Instant Quote!
Get a personalized quote for your project instantly—simply enter your specifications and requirements to see how we can meet your needs.
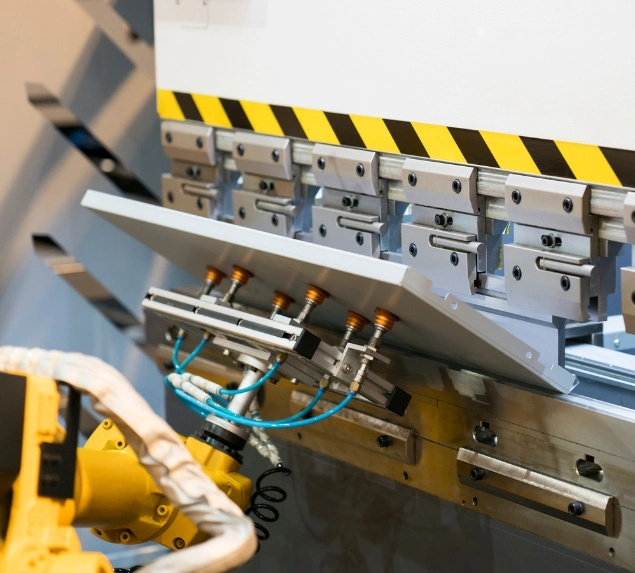
Contact With Us
for any inquiry



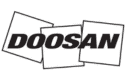
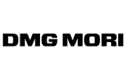