- Home
- Capabilities
- Plastic Injection Molding
Custom Plastic Injection Molding Services
HDC Manufacturing delivers high-quality, precision plastic injection molding services for small batch production and large-scale manufacturing. With advanced technology and an expert team, we help your products stand out in the market.
Advantages of Plastic Injection Molding
Discover the Benefits of Choosing Plastic Injection Molding for Your Products.
High Precision and Consistency
Exact Specifications: Each product is manufactured to precise dimensions with minimal variation.
Consistent Quality: Ensures uniformity across large production runs.
Efficient Production
Rapid Production: Ideal for high-volume manufacturing needs.
Reduced Lead Times: Faster turnaround without compromising quality.
Design Flexibility
Complex Shapes: Create intricate designs and detailed features.
Custom Solutions: Tailored to meet diverse application requirements.
Cost-Effective
Low Material Waste: Efficient use of resources reduces costs.
Scalable Production: Economical for both small and large-scale manufacturing.
Material Variety
Wide Range of Options: Choose from ABS, PP, PC, Nylon, and more.
Tailored Properties: Match materials to specific performance needs.
Durability and Strength
Robust Products: Withstand demanding conditions and extended use.
Long-Lasting Performance: Ensures reliability and longevity.
Why Choose HDC for Plastic Injection Molding
Unmatched Expertise
🔹Decades of experience in plastic injection molding across diverse industries.
🔹A team of skilled engineers and technicians dedicated to your project’s success.
State-of-the-Art Facilities
🔹Equipped with the latest injection molding machines and automation technologies.
🔹Capable of handling projects of any scale, from prototypes to mass production.
Tailored Solutions for Every Industry
🔹Automotive: Durable components like dashboards, bumpers, and connectors.
🔹Medical: Precision parts for devices, surgical tools, and sterile packaging.
Commitment to Sustainability
🔹Use of eco-friendly materials, including recycled and bio-based plastics.
🔹Energy-efficient processes to minimize environmental impact.
Seamless End-to-End Service
🔹From initial concept design to final delivery, we handle every step.
🔹Prototyping, mold design, production, and post-processing under one roof.
Rigorous Quality Assurance
🔹Advanced inspection tools, including CMM and optical scanners.
🔹Compliance with international standards like ISO 9001 and ISO 13485.
Materials Offered for Plastic Injection Molding by HDC
Discover the diverse range of premium materials HDC uses for plastic injection molding, ensuring exceptional performance and reliability for all your custom needs.
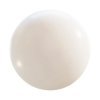
Polyethylene (PE)
Excellent flexibility, durability, and chemical resistance.
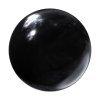
Polypropylene (PP)
Strong, flexible, and chemically resistant.
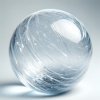
Polyethylene Terephthalate (PET)
Strong, stable, and moisture-resistant.
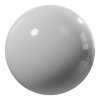
Acrylonitrile Butadiene Styrene (ABS)
Strong, tough, and rigid with good impact resistance.
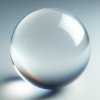
Polycarbonate (PC)
High impact resistance and optical clarity.
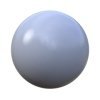
Polyamide (Nylon)
Highly durable, wear-resistant, and thermally stable.
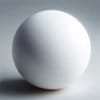
Polystyrene (PS)
Rigid, lightweight, and easy to mold.
Introduction to Plastic Injection Molding
Learn the fundamentals of plastic injection molding, a versatile and efficient manufacturing process used to produce high-quality, precision parts for various industries.
What is Plastic Injection Molding?
Plastic injection molding is a manufacturing process where molten plastic is injected into a mold cavity, cooled, and solidified into the desired shape. It’s widely used for producing high volumes of identical parts with exceptional precision and consistency.
How Does It Work?
- Material Feeding: Plastic pellets are fed into a hopper and transported to the injection unit.
- Melting and Injection: The pellets are melted and injected into a mold under high pressure.
- Cooling and Solidification: The molten plastic cools and hardens into the mold’s shape.
- Ejection: The finished part is ejected from the mold, ready for use or further processing.
Cycle Time: Typically ranges from a few seconds to minutes, depending on part size and complexity.
Challenges and Solutions
1. High Initial Costs
- Challenge: Expensive tooling and mold fabrication.
- Solution: Optimize design using CAD and simulation software to reduce trial and error.
2. Potential Defects
- Challenge: Warping, sink marks, or incomplete filling.
- Solution: Advanced quality control and real-time monitoring systems.
3. Long Lead Times
- Challenge: Time-consuming mold development.
- Solution: Use of rapid prototyping and modular molds.
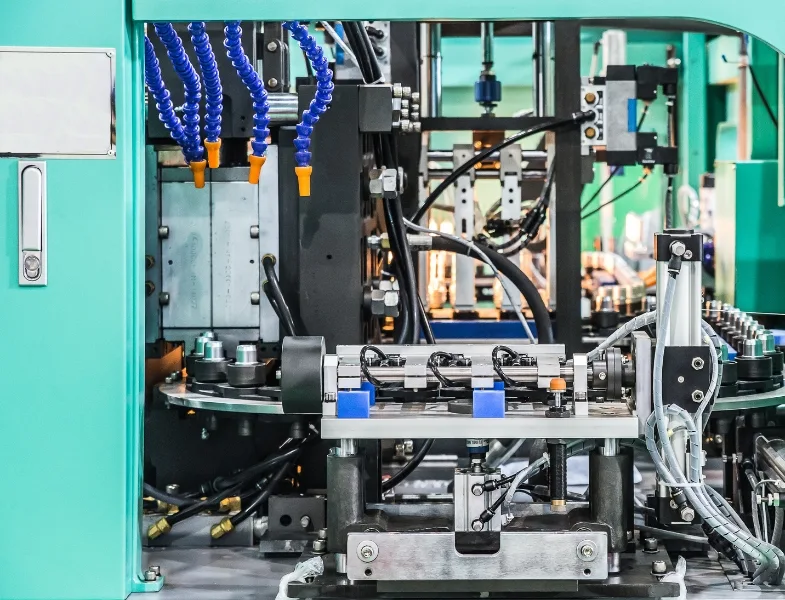
Applications of Plastic Injection Molding Across Industries
Discover how plastic injection molding is utilized across diverse industries to create high-quality, precise components tailored to specific applications.
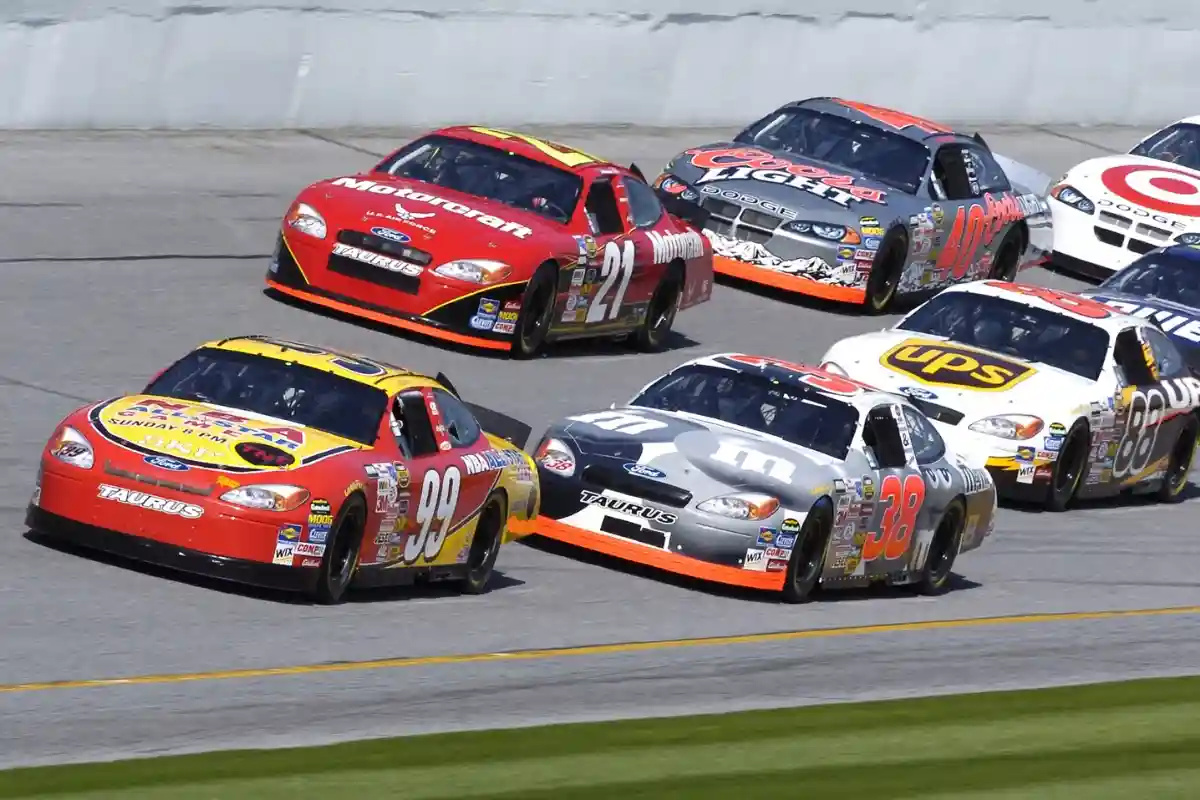
Automotive Industry
🔹Components: Dashboards, bumpers, interior trims, and engine covers.
🔹Benefits: Lightweight, durable parts that enhance vehicle safety and performance.

Aerospace Industry
🔹Components: Interior panels, ducting, and electronic system housings.
🔹Benefits: Lightweight, high-strength parts that withstand extreme conditions.
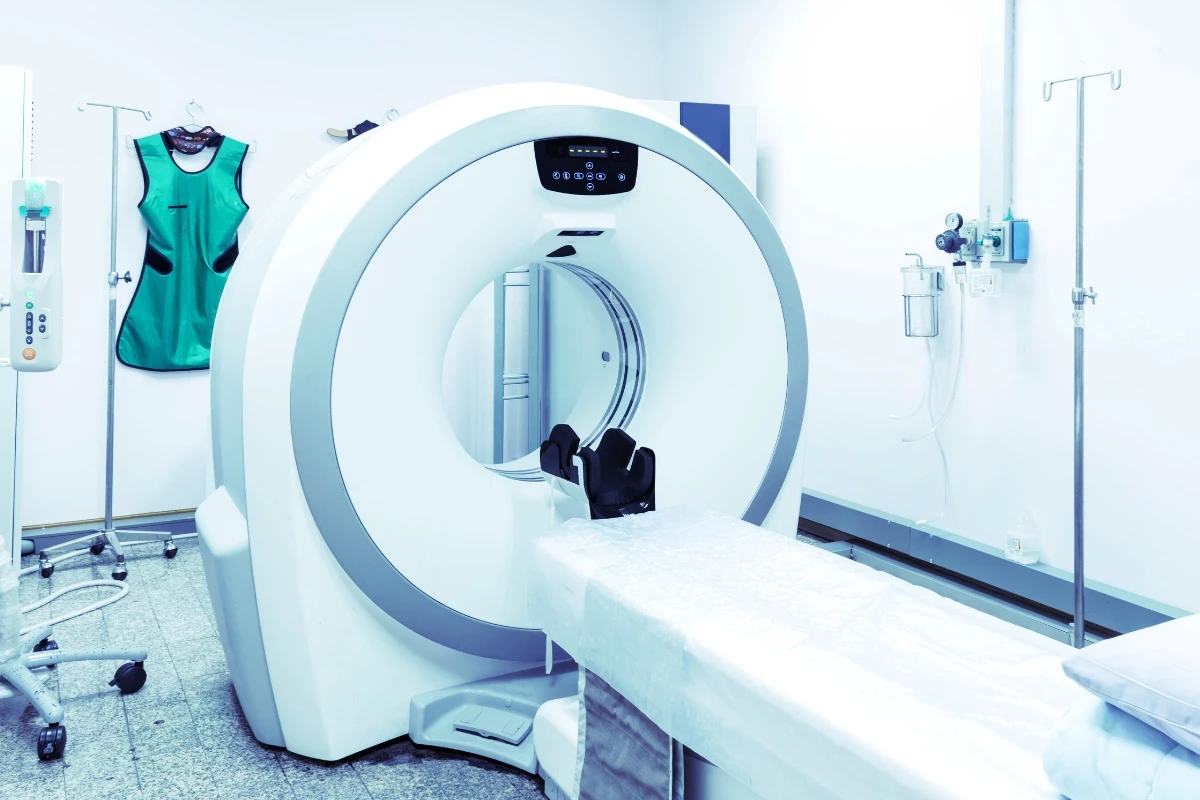
Medical Industry
🔹Components: Syringes, IV components, surgical instruments, and diagnostic device housings.
🔹Benefits: Sterile, reliable parts that meet stringent medical standards.
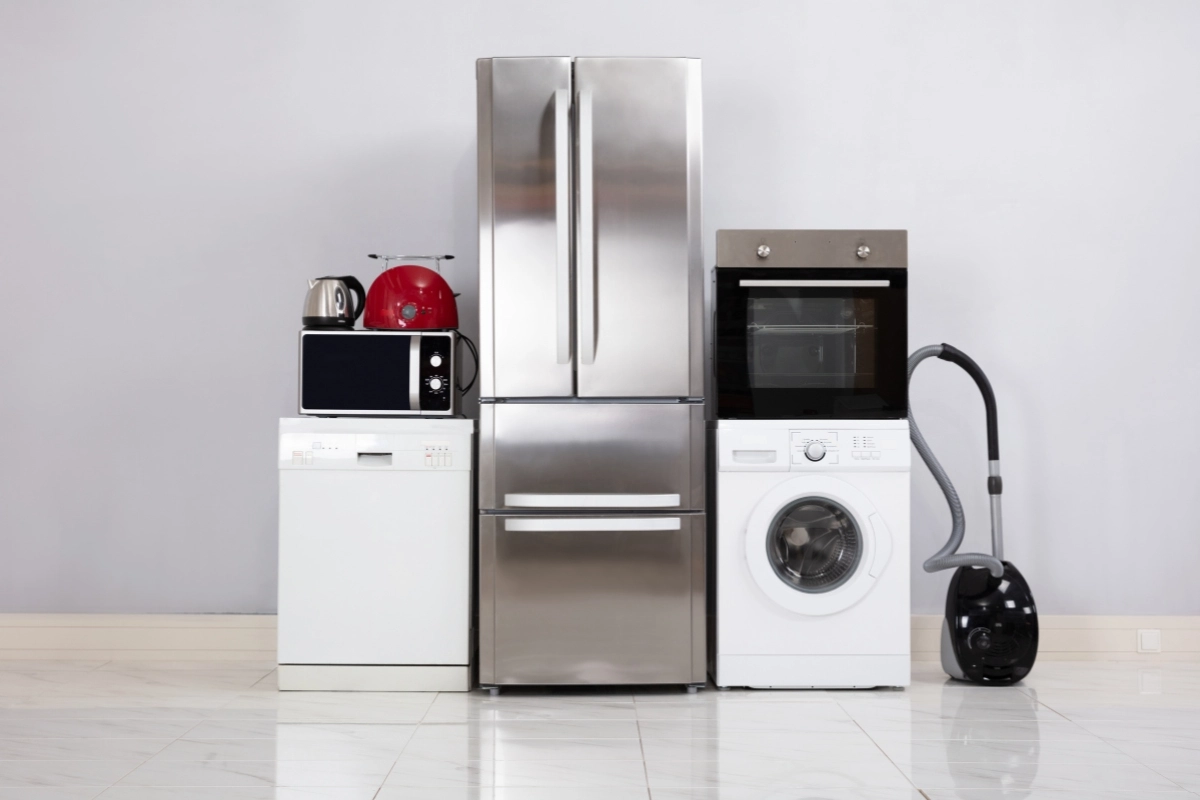
Electronics Industry
🔹Components: Housings, connectors, and enclosures.
🔹Benefits: High precision for intricate electronic assemblies and environmental protection.
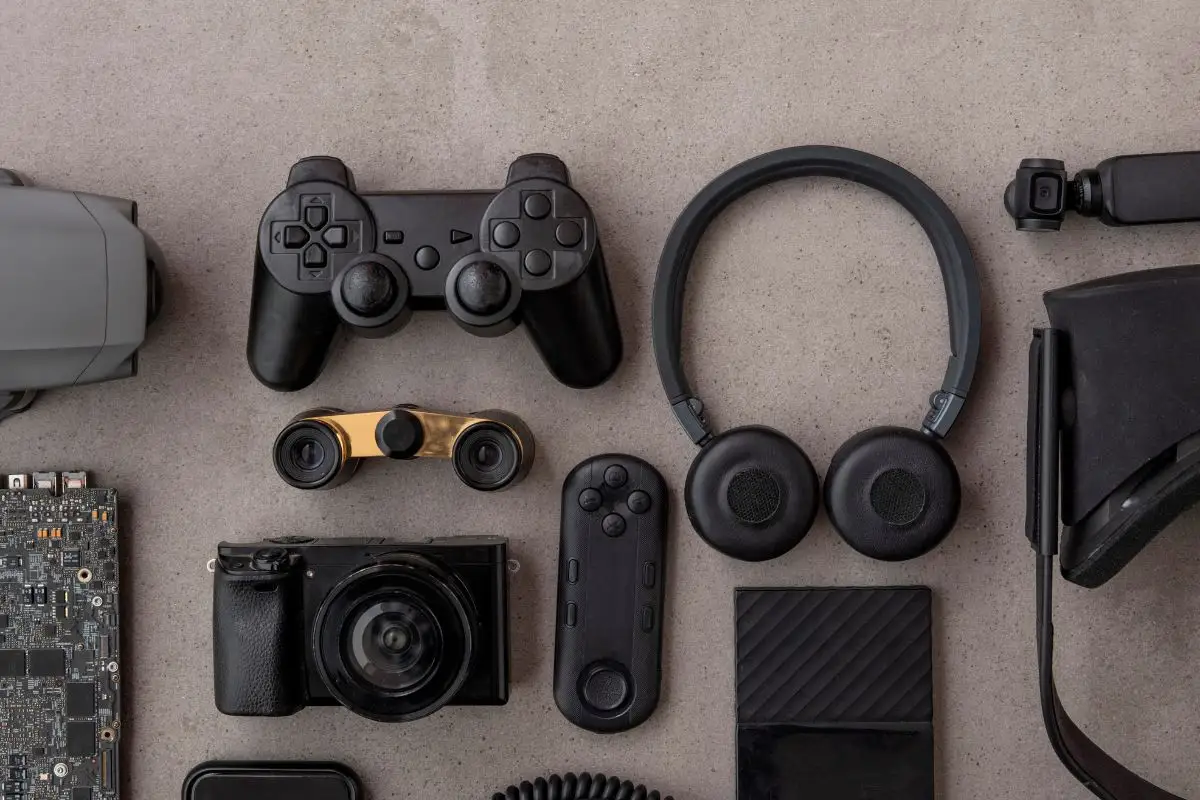
Consumer Goods
🔹Products: Kitchen utensils, storage containers, toothbrushes, and cosmetic packaging.
🔹Benefits: Uniform, high-quality parts for everyday use.

Architecture and Construction
🔹Components: Fittings, fasteners, and tools.
🔹Benefits: Durable and precise parts for structural integrity.
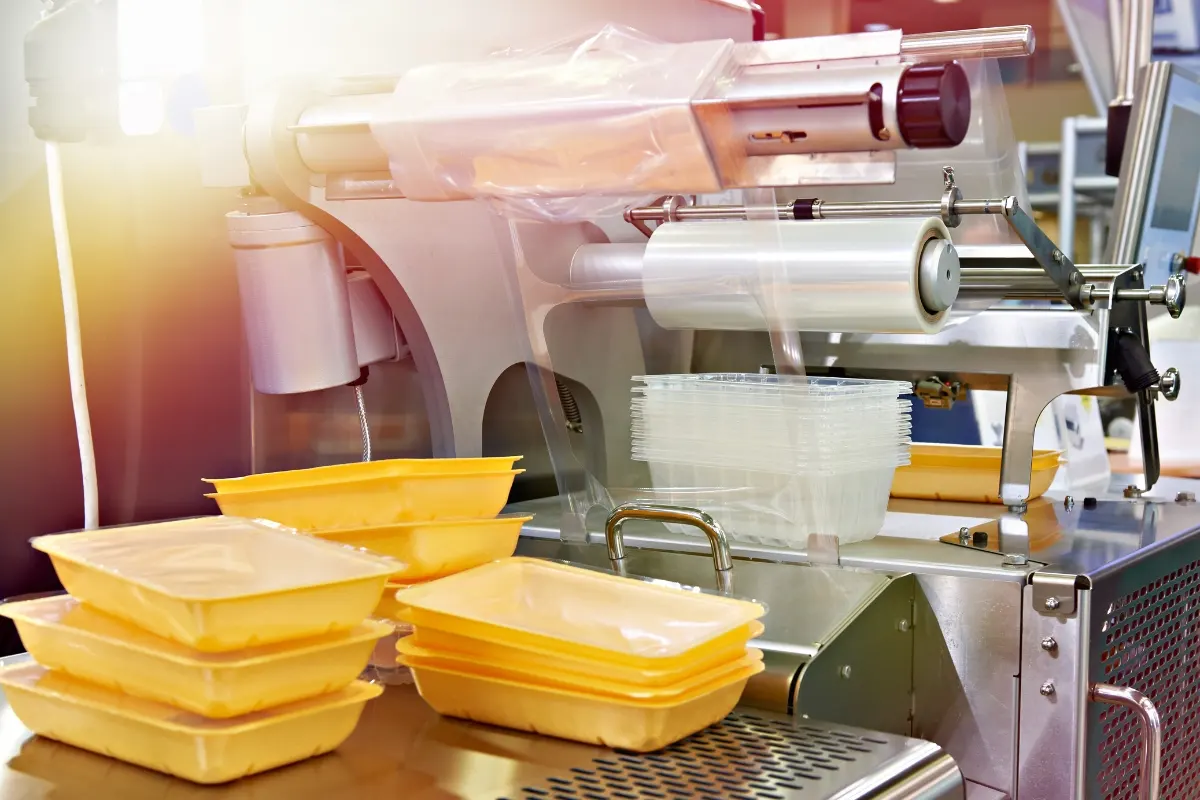
Packaging Industry
🔹Products: Bottle caps, containers, and custom packaging designs.
🔹Benefits: Robust and attractive packaging with tight tolerances.
Precision in Plastic Injection Molding
Discover the precise capabilities of plastic injection molding, delivering consistent quality and exact specifications for all your manufacturing needs.
Parameter | Typical Precision | Description |
---|---|---|
Dimensional Tolerance | ±0.1% to ±0.5% | Ensures parts meet exact size specifications. |
Wall Thickness | ±0.1 mm to ±0.25 mm | Maintains uniform wall thickness for structural integrity. |
Surface Finish | 0.1 to 0.4 µm | Achieves smooth, high-quality surfaces. |
Roundness | ±0.05 mm | Ensures cylindrical parts maintain their shape. |
Flatness | ±0.05 mm | Keeps flat surfaces within precise tolerances. |
Hole Diameter Tolerance | ±0.025 mm | Ensures accurate hole sizes for fitting and assembly. |
Part Weight Variation | ±0.5% | Controls weight variation for consistent product quality. |
HDC Plastic Injection Molding Technical Specifications
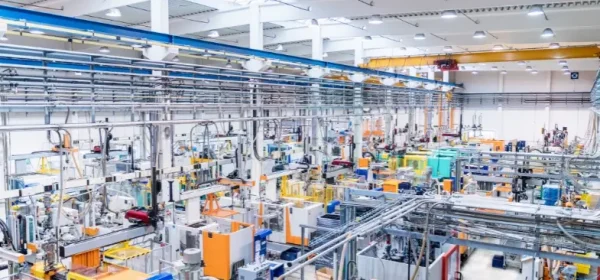
Specification | Details |
Maximum Part Size | Up to 1 meter in length |
Shot Size | Up to 3000 grams |
Clamping Force | 50 to 1000 tons |
Dimensional Tolerance | ±0.1% to ±0.5% |
Wall Thickness Range | 0.5 mm to 5 mm |
Cycle Time | 10 seconds to 3 minutes |
Materials Used | PE, PP, ABS, PC, Nylon, PET, TPE, PS |
Surface Finish Quality | 0.1 to 0.4 µm |
Color Options | Custom colors available |
Mold Cavities | Single to multi-cavity molds |
Production Volume | Prototyping to high-volume production |
Quality Control | ISO 9001-certified processes, real-time monitoring |
FAQs About Plastic Injection Molding
Find answers to common questions about HDC’s plastic injection molding services, from materials and processes to quality control and customization.
HDC works with a wide range of materials including PE, PP, ABS, PC, Nylon, PET, TPE, and PS, ensuring we can meet your specific application needs.
Lead times vary based on the complexity and volume of the order, typically ranging from 6 to 8 weeks from design finalization to production completion.
Yes, HDC can help refine and improve your design to optimize production and quality. However, we require detailed drawings or samples from you to fully understand your specific needs and ensure we meet your exact requirements.
HDC can produce parts up to 1 meter in length, accommodating a wide range of product sizes.
HDC employs ISO 9001 certified processes and real-time monitoring to ensure each part meets the highest quality standards.
Costs depend on factors such as material, complexity, size, and production volume. HDC offers competitive pricing and will provide a detailed quote based on your specific requirements.
Yes, HDC can handle everything from prototyping to high-volume production, offering flexibility to meet your production needs.
HDC offers a range of customization options including material selection, color matching, surface finishes, and specialized design features to meet your unique specifications.
Get an Instant Quote!
Get a quick quote for your project with just a click! Request an instant quote now!
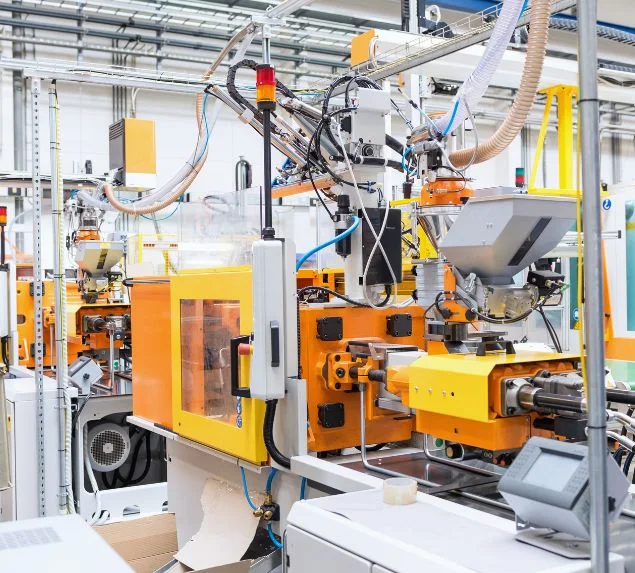
Contact With Us
for any inquiry



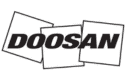
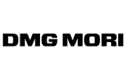