- Hogar
- Capabilities
- CNC Machining Services
Ones-Stop Online CNC Machining Service
As a China-based CNC machine shop with 15+ years of aerospace-grade manufacturing expertise, HDC provides:
• 24-hour Quick Quote
• Global Shipping
• Competitive Price
HDC CNC Machining Capabilities
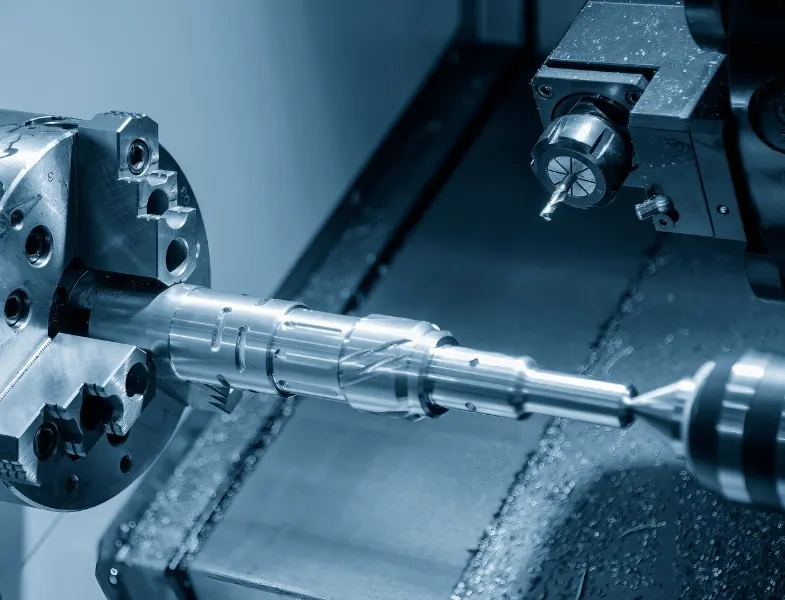
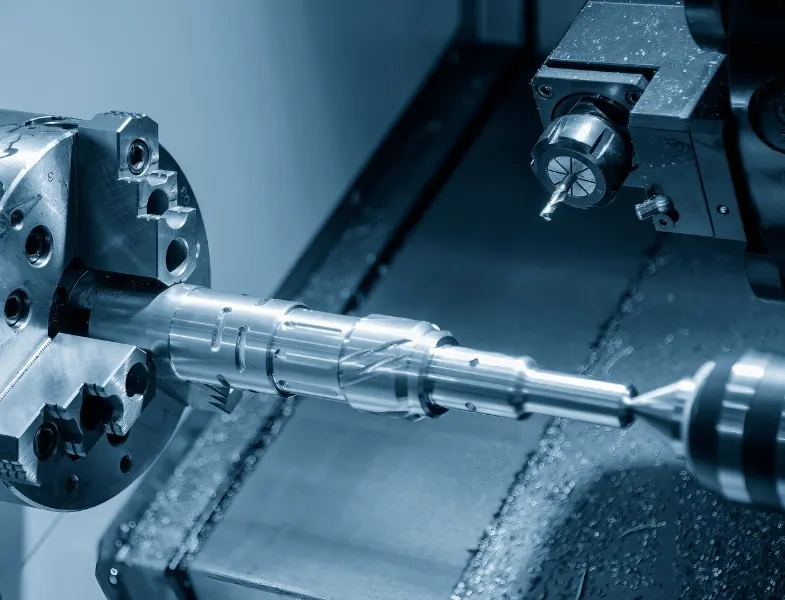
CNC Turning
CNC turning is typically used to cut rod material to shape a part with a cylindrical and symmetrical character. HDC offers the advanced milling machine, with an extra rotating axis of the cutting tool, which combines the advantages of turning and milling to produce rotating body parts like an impeller.
Learn More
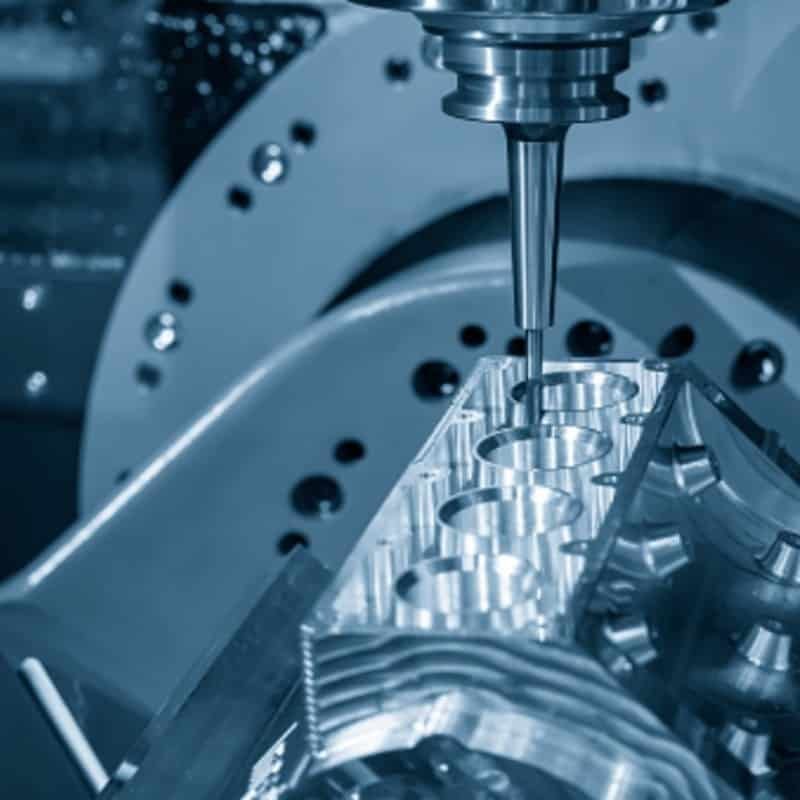
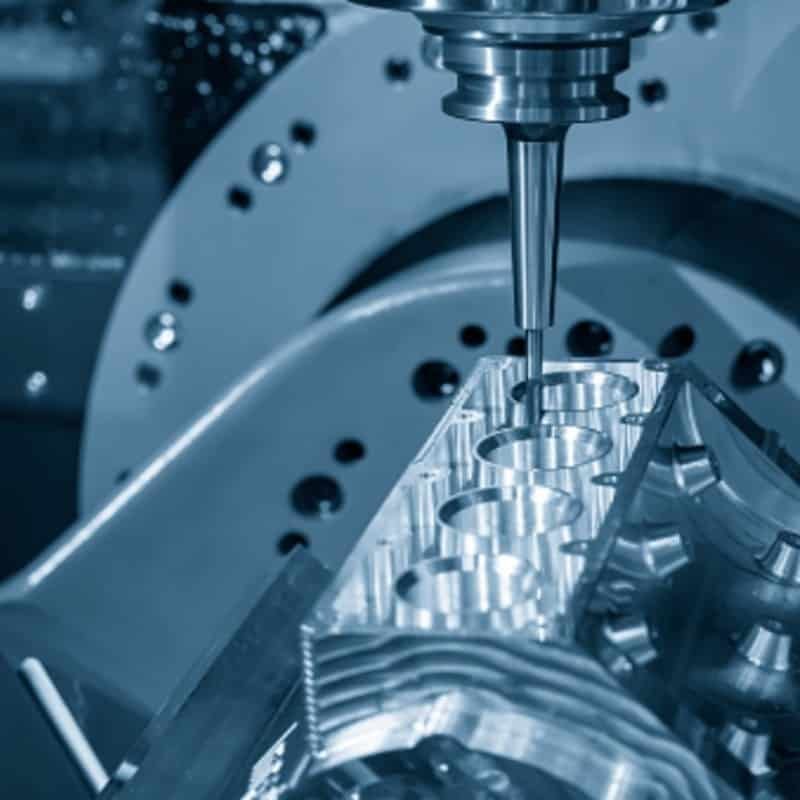
CNC Milling
CNC milling moves the cutting tool on the x, y, and z axes to cut the billet secured on the working plate. It can process complex geometries, curved surfaces, slots, and threads. With the advanced 4-axis and 5-axis milling center, which adds rotating axes for the workpiece, HDC can manufacture any parts with a ±0.005 tolerance.
Learn More


Swiss Machining
Swiss machining is a highly automated manufacturing process that features auto-feeding, machining, and tool changing. A standard version Swiss machine has 5 axes, combining the features of turning and milling, perfect for high precision small parts like medical implants, connectors, and screws.
Learn More
Advantages of HDC
Advanced Equipment
🔹State-of-the-art 5-axis CNC machining centers
🔹Handles prototypes and large-scale production
Consistent Accuracy
🔹Tight tolerances at any production volume
🔹High-precision results for all parts
Diverse Material Options
🔹Supports plastic, stainless steel, aluminum, titanium, and more
🔹Tailored solutions for unique project requirements
Expert Engineering Support
🔹Skilled design and operations team
🔹Optimized designs for enhanced performance and aesthetics
Rigorous Quality Control
🔹Advanced inspection tools (CMMs)
🔹Strict checks at each manufacturing stage
Responsive Customer Service
🔹Multi-language support
🔹FOB or door-to-door delivery
🔹Multiple payment methods
Tailored CNC Solution for Any Project.
Contact us for detailed information, get a quick quote within 24 hours for free.
CNC Machining Metal Materials




Aluminum
With the lightweight (Density: 2.6 ~ 2.9 g/cm³), high-strength-to-weight ratio (Specific Strength: 203.6 MPa/(g/cm³)), and easy to machine properties, aluminum and its alloys are the most used material in CNC machining. At HDC, we provide the best quality aluminum materials for our customers, which include grades 2024, 6061, 6063, and 7075.


Titanium
Titanium is favored due to its stable chemical and physical properties. With excellent corrosion resistance, high strength, and biocompatibility, it’s widely used in aerospace, medical, and racing industries. At HDC, we overcome the work hardening and heat generation in CNC machining titanium, bringing titanium parts with high precision.


Stainless Steel
Stainless steel is a popular metal used in CNC machining. It introduces the Cr element to increase corrosion resistance. Cr element reacts with oxygen and forms a self-healing dense Cr₂O₃ layer to resist water, oxygen, and other corrosive media. It can be divided into various types according to metallographic structure and chemical composition. The common grades include 304, 316, and 316L.
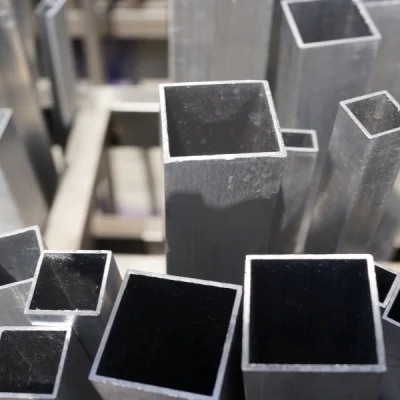
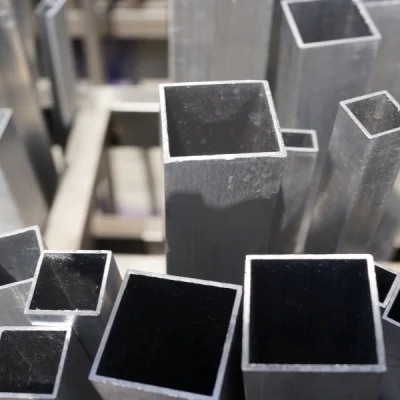
Carbon Steel
Benefit from its high machinability and affordable price, carbon steel is unanimously considered an excellent material choice for CNC machining. Based on the carbon content, carbon steel can be classified into low-carbon, medium-carbon, and high-carbon steel. A higher carbon content means higher strength but also a corresponding reduction in toughness.
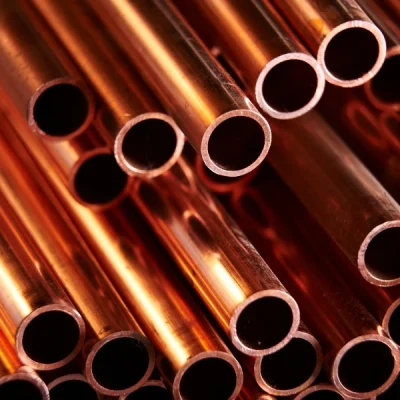
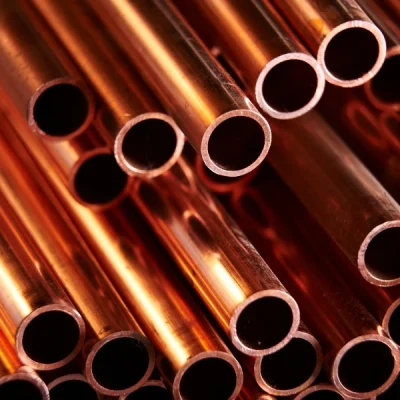
Copper
Copper has excellent thermal and electrical conductivity, making it the most important metal in the electrical and electronic field. Also, copper can be easily machined because of its free-cutting properties. But only a few common scenarios require pure copper. In most cases, copper alloys are more commonly used in CNC machining, such as brass and bronze.
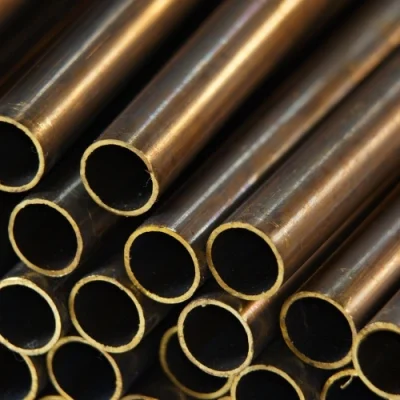
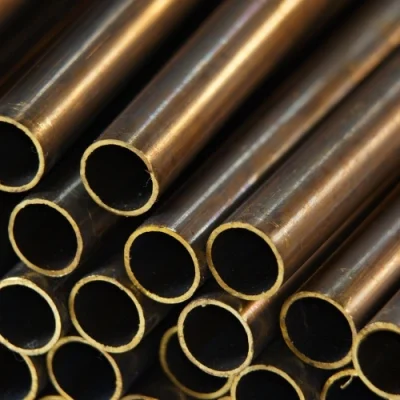
Brass
Brass is a general term for a series of copper-zinc alloys (containing 5%~45% zinc). It has a shiny golden appearance after polishing, often used in decorative, bathroom hardware, automotive electrical components, and musical instrument manufacturing. In which the grade C37700 has added Pb to enhance cutting performance and commonly in machining.
CNC Machining Plastic Materials
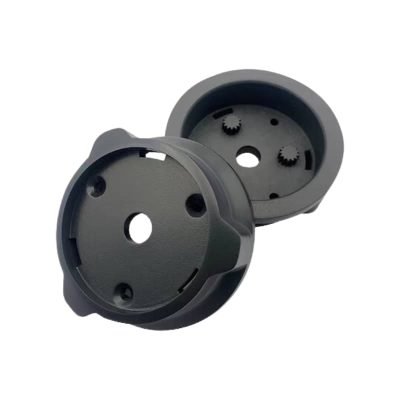
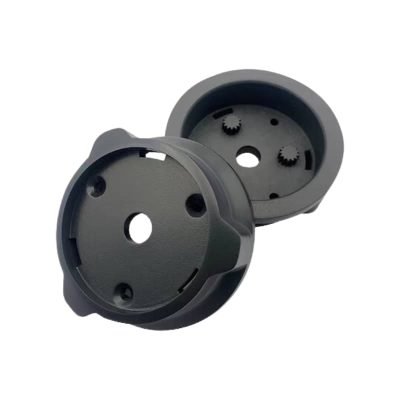
ABS
ABS is polymerized from three organic compounds, where ‘A’ stands for Acrylonitrile, ‘B’ for Butadiene, and ‘S’ for Styrene. As a thermoplastic, ABS has become a popular choice for CNC machining, injection molding, and 3D printing due to its excellent performance and ease of processing.


PVC
PVC (Polyvinyl Chloride) is a cost-effective choice for low-load applications where lightweight (1/5 the density of steel) and corrosion resistance are crucial.
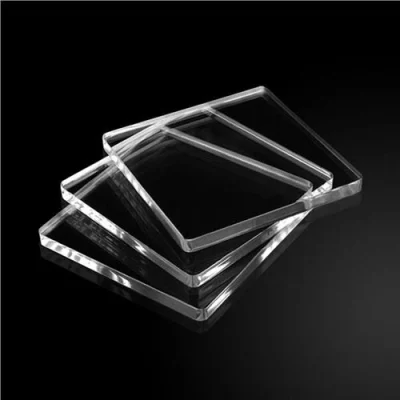
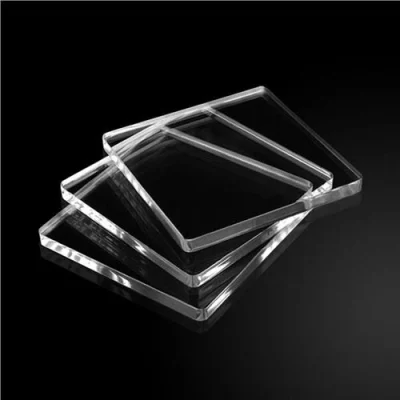
PMMA
PMMA is commonly known as acrylic or plexiglass. The light transmittance of PMMA is close to glass, but the weight is only half of glass. Because of its low price and easy processing, it has become an ideal substitute for glass in many fields. Common products include optical lenses, lamp shades, and various transparent protective shells.


UHMW
UHMW (ultra-high molecular weight polyethylene) has super wear resistance, which is 7 times that of ordinary carbon steel. At the same time, it also has good chemical stability and biocompatibility, so it is also often used in artificial joints, surgical instruments and other fields.
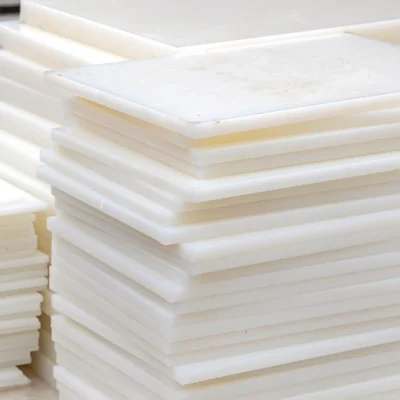
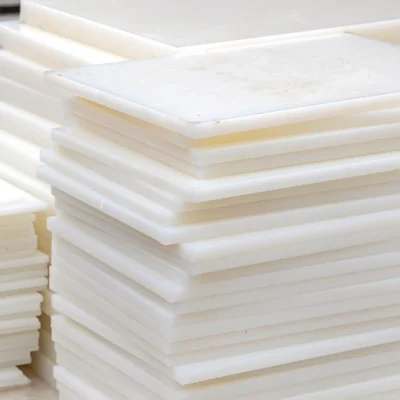
POM
POM (polyoxymethylene) is a preferred choice for precision mechanical parts in CNC machining due to its high rigidity and excellent dimensional stability. At the same time, its friction coefficient is relatively low, with certain self-lubricating properties, making it very suitable for manufacturing components such as gears and guide rails.
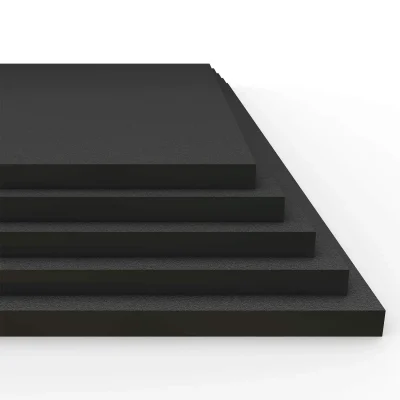
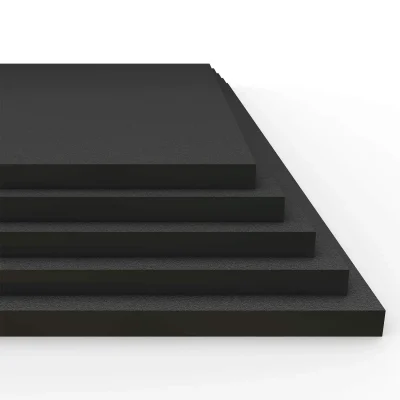
HDPE
HDPE is a type of polyethylene plastic. The “HD” stands for “High-Density” and “PE” stands for Polyethylene. It is inexpensive and adapts to various processing methods, including CNC machining. With its high chemical and impact resistance features, it’s favored by the packaging, chemical, and consumer goods industries.




PTFE
Polytetrafluoroethylene (PTFE), also known as Teflon, is famous for its applications in cookware and clothing as a coating. It has super stability, reflected in its long-term service temperature range of -200°C to +260°C, and its resistance to all strong acids, strong alkalis, and organic solvents.




Nylon
Nylon(Polyamide, PA) is a versatile plastic with a rich variety, including PA6, PA66, PA11, and PA12 etc. Nylon is widely used in a variety of fields due to its high toughness, abrasion resistance, and fatigue resistance. It’s not only a common engineering plastic in the field of machining mechanical parts, but also an important synthetic fiber material.
Surface Finishes
HDC provides various post processing and surface finish options for CNC machining parts to meet different requirements and improve performance, extend part lifespan.
- Anodizing (Hard Anodizing, Colorful Anodizing)
- Chrome Plating
- Zinc Plating (Hot-dip galvanizing, Electrogalvanizing)
- Polishing
- Powder Coating
- Painting
- Laser Etching
- Heat Treatment


More About HDC Machining Capabilities
Explore our equipment, tolerance, factory, and certifications. Learn more about how HDC can boost your business.
Walk Through Our Factory
HDC is a professional CNC service provider with over 10 years of experience. Our expertise is not limited to CNC machining. We have expanded our capabilities to sheet metal fabrication, welding, casting, and forging over the past decade. We have a facility with over 3000 square meters and over 90 employees. Now, follow the video, take a look at our factory.
What is CNC Machining
CNC machining is a highly automated machining process. Unlike a manual lathe, which relies on workers to manually control the cutting path. CNC machining uses computers to control the entire machine, including the cutting tool, cooling system control, etc. Which can effectively reduce the number of reclamping and greatly improve production efficiency while reducing manual operation errors.
How CNC Machining Works
CNC machining is not only about the machine. It complements CAD (Computer-Aided Design). Engineers use CAD software to design parts, create 3D models identical to the finished product, and conduct simulation tests with CAD software to preliminarily verify machining feasibility. Then, the CAD software automatically generates G-code, which is finally executed by the CNC machine.
FAQ
Find answers about HDC CNC machining service.
HDC offers a wide range of materials for CNC machining, including stainless steel, aluminum alloys, titanium, carbon steel, copper alloys, and various polymers. Each material is chosen for its properties to meet the specific requirements of your project.
We accept most CAD file formats, including DXF, DWG, STEP, and IGES. Providing a clear and detailed design file will help ensure the accuracy and efficiency of the manufacturing process.
Yes, HDC is equipped to handle all sizes of production runs, from single prototypes to large-scale production batches. Our facilities can adapt to your project's volume needs with the same level of precision and efficiency.
Lead times can vary based on the complexity and volume of the project. Typically, we can turn around prototypes in 4-6 weeks, while larger production runs might take 2-4 months. We always work to meet your deadline and can provide more specific timelines once we review your project details.
HDC maintains strict quality control standards throughout the CNC machining process. We use advanced measurement and inspection techniques, including CMM (Coordinate Measuring Machines) and visual inspections, to ensure every part meets your specifications and our high-quality standards.
Absolutely! Our experienced engineers are available to assist with part design and can provide input on manufacturability, material selection, and cost-efficiency to optimize your product for CNC machining.
Get an Instant Quote!
Get a quick quote for your project with just a click! Request an instant quote now!
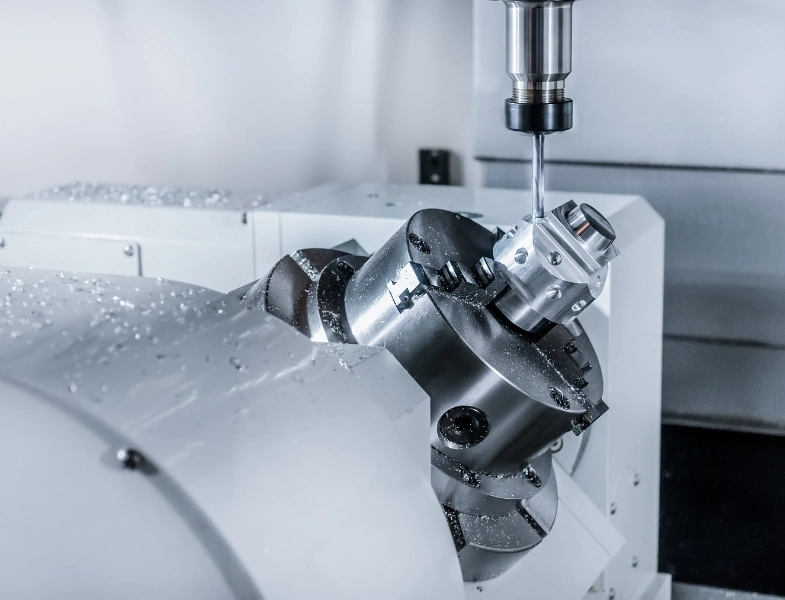
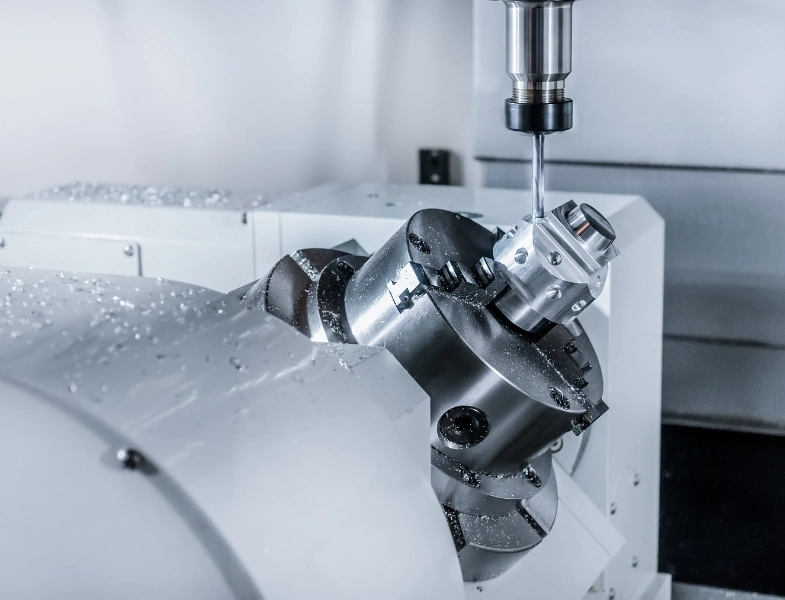
Contact With Us
for any inquiry
Other Service HDC Provide
Explore the range of additional services HDC offers, from custom design and prototyping to logistics and post-manufacturing support.






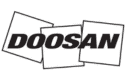
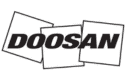
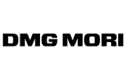
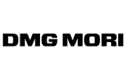