Your Stainless Steel Manufacturing Partner
Our vertically integrated capabilities transform raw stainless steel into high-performance components. Using SUS303/SUS304/SUS316 series materials, we combine multiple manufacturing process to make the best stainless parts for you.


Why Choose Stainless Steel
Superior Corrosion Resistance
✅316L (AISI 316L) offers 5x higher chloride resistance vs carbon steels
✅Ideal for: Marine hardware components, chemical processing pipelines
Food-Grade Safety
✅SUS304 meets FDA 21 CFR 177.2600 food contact standards
✅Common applications: Dairy processing equipment, commercial kitchen fixtures
Biocompatibility Certified
✅Medical-grade 316L complies with ISO 13485 biocompatibility requirements
✅Specifically used in: Surgical instrument manufacturing, orthopedic implant systems
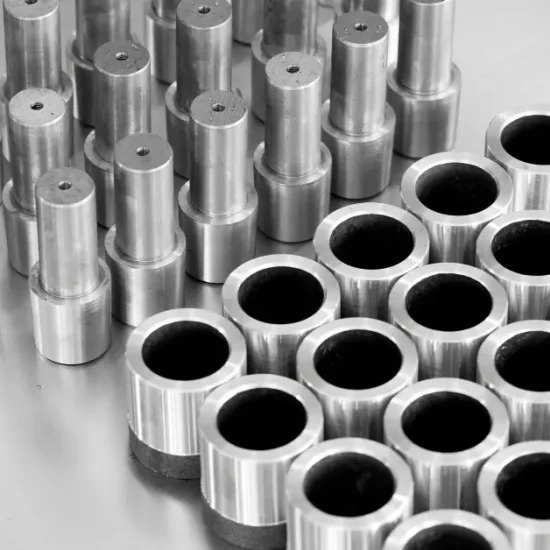
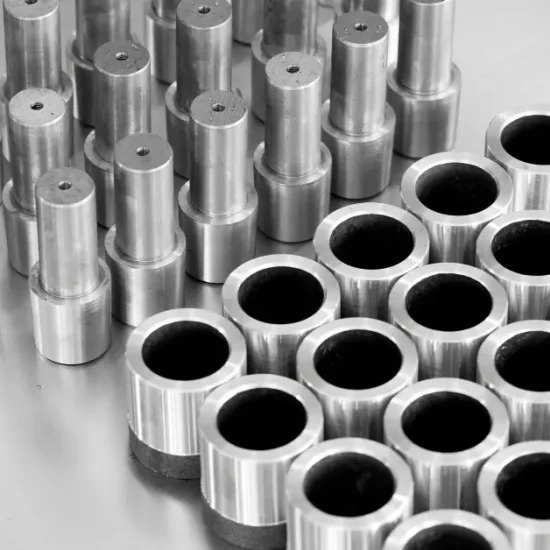
Why Choose HDC for Custom Stainless Steel Parts
We are Investment Casting Expertise
✅Complex geometries with ±0.15mm tolerance for high-volume production
We Provide Multi-Process Integration
✅Hybrid manufacturing combining casting with CNC machining (±0.005mm)
We Provide Medical-Grade Finishing
✅7 surface options including electropolishing (Ra 0.2μm) and passivation
Multi-Material Capability
✅6+ stainless grades: SUS303 / SUS304 / SUS316L / SUS410 / SUS416 / SUS316F
Agile Production Scaling
✅We can handle different size orders, from 50pcs prototypes to 50,000+ batch orders.
All Material Certified
✅All Materials are certified before processing. we provide certifications upon request.
Stainless Steel Selection Guide
Engineered for Extreme Performance
Discover our 6 essential stainless steel grades (SUS303/304/316L/316F/410/416), precision-tuned for:
✅ Strength-to-Corrosion Balance
✅ Zero-Compromise Machinability
✅ Certified Consistency
Need help matching materials to your application?
Precision-Crafted Stainless Steel Fabrication
Mastering CNC machining, sheet metal forming, investment casting, and certified welding to transform raw stainless alloys into high-performance components with micron-level accuracy and industry-leading surface finishes.
CNC Machining
✅5-axis simultaneous milling (±0.01mm)
✅Swiss-type turning for Ø0.5-32mm components
✅Custom toolpath programming
Investment Casting
✅0.6mm minimum wall thickness control
✅Dual-certified materials (316L/17-4PH/2205)
✅CT scan inspection for internal defects
Welding
✅Laser/TIG welding with ≤0.1mm seam width
✅Full-penetration welding for pressure vessels
✅Post-weld solution annealing
Sheet Metal Fabrication
✅Fiber laser cutting(0.5-12mm thickness)
✅Sheet Metal Bending
✅CNC Auto Sheet Metal Punching
Custom Stainless Steel Products by HDC
Delivering Precision-Engineered Custom Stainless Steel Solutions Designed to Enhance Functionality and Performance Across Various Industries
FAQ
Addressing Your Concerns: Get Answers to Common Questions on Customizing Stainless Steel Solutions with HDC
HDC offers a wide range of stainless steel grades, including 201, 304, 316, 416, and more specialized alloys like 17-4 PH and 2205 Duplex, catering to diverse industry requirements and applications.
Yes, HDC is equipped to handle all sizes of production runs, from small custom batches to large-scale manufacturing, ensuring consistency and quality across all products.
We utilize advanced manufacturing processes such as CNC machining, laser cutting, welding, and metal stamping to create precise and durable stainless steel components tailored to your specifications.
Quality is paramount at HDC. We employ rigorous testing and quality control measures throughout the fabrication process to ensure each product meets our high standards and your specific requirements.
Lead times can vary depending on the complexity and volume of your project. We work closely with you to establish timelines that meet your project deadlines while maintaining our quality standards. Generally, 30-40 days is our typical lead time.
Absolutely, HDC encourages prototyping as a critical step in the development process to ensure the final product meets your specifications before full-scale production.
HDC offers a variety of finishes for stainless steel, including brushed, polished, and matte finishes, to meet aesthetic and functional requirements.
Get an Instant Quote!
Get a quick quote for your project with just a click! Request an instant quote now!
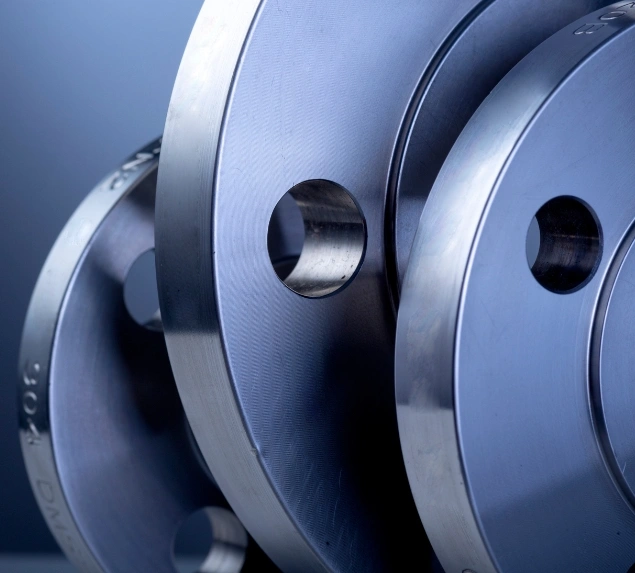
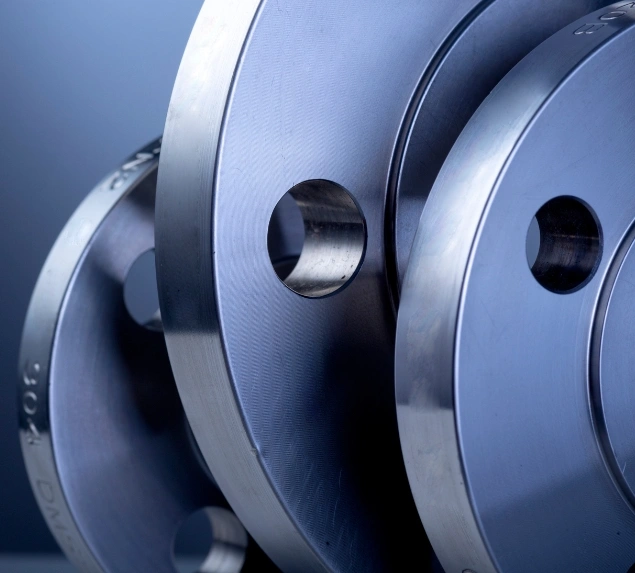
Contact With Us
for any inquiry
Explore More Materials Offered by HDC
Beyond stainless steel – specialized metals and composites
for demanding applications






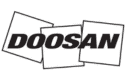
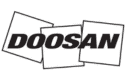
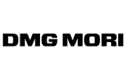
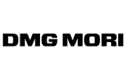