Understanding the Fundamentals and Benefits of CNC Machining
Explore the comprehensive guide to CNC machining, a high-tech manufacturing process driven by computer software for precision and efficiency. Learn about various CNC machining technologies, materials used, working principles, and the significant advantages and challenges faced in the industry. This guide also covers essential tips for selecting custom CNC machining services and highlights the importance of CNC in modern manufacturing.
The Meaning of CNC Machining
CNC, short for computer numerically controlled, is a type of methodology where it entails the use of cutting-edge and highly advanced machinery and equipment to perform certain tasks without the intervention of human skill, in short, it’s carried out by software engineered to carry out tasks required.
CNC machining is a manufacturing procedure that makes use of machines such as laser cutters, lathes, mills, turning machines, routers, and many other types of equipment without the need for workers.
Importance of CNC Machining
Besides the fact that CNC is high-tech and advanced, there are a ton of important benefits and factors that make it extraordinary. One of the best factors would be the accuracy and precision of the products manufactured.
Since it’s run by software, errors are minimal, and a lot of times, there’s no need for further processes, unless of course the software hasn’t been programmed to be 100% accurate to the end result that is wanted to achieve.
Types of CNC Machining Technology
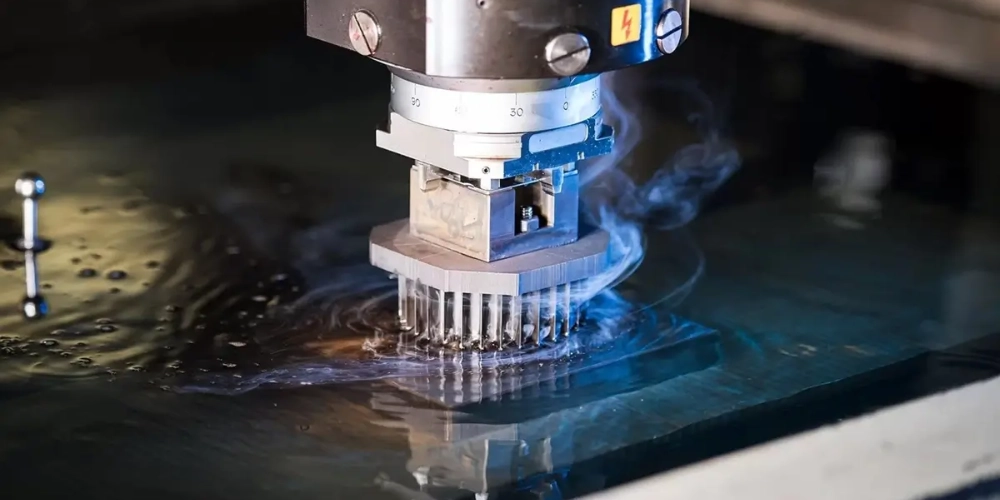
- Milling: Includes cutting material out of a workpiece with rotating knives.
- Turning: Turns the workpiece as a cutting tool forms it.
- Drilling: It uses a rotating drill bit to make holes in the workpiece.
- Electrical Discharge Machining (EDM): Cuts through the material with electrical discharges using a fine wire.
- Waterjet Cutting: Uses a pressurized stream of water to cut through materials.
- Laser Cutting: It uses a laser to cut or engrave materials.
- Grinding
- Routing: Uses a rotary cutting tool and is widely applied to woodworking.
Materials Used in CNC Machining
CNC machining involves the use of various materials to manufacture high precision components. Usual metals include aluminium, stainless steel and alloys as well as plastics like ABS or polycarbonate. Further wood, composites including carbon fiber among others, ceramics foam rubber and specialist materials such as glass stone are used. The selection of an appropriate material is based on certain properties needed for the part work, such as strength or resistance to heat etc. With the adaptability, CNC machining makes it possible to produce accurate component components across different sectors while working with a wide range of materials.
Understanding CNC Machining Services
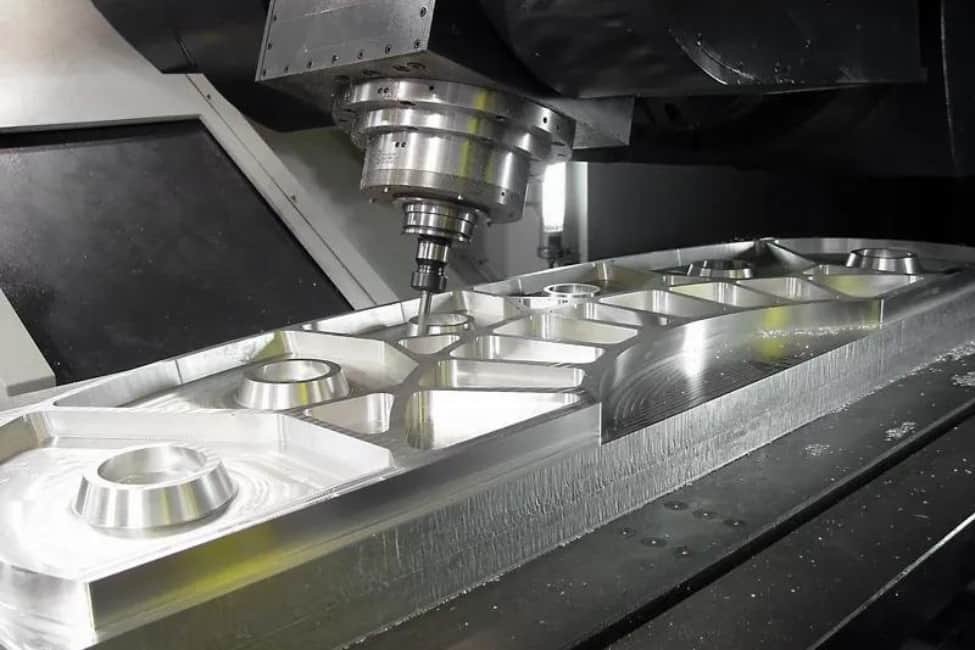
- Laser Cutting
- Milling
- Plasma Cutting
- Lathes and Turning
The Parts of CNC Machines
- Headstock
- Spindle
- Carriage
- Monitor
- Computer (CNC)
- Tailstock
- Bed
- Drive Motor
- Foot Pedals
- And Many More!
Working Principle of CNC Machining
CNC machining is a manufacturing process that is typically categorized as a subtractive process or a process that’s primary goal is to remove material from a workpiece to achieve the desired form and measurement.
There are many different categories of CNC machining but the most common are laser cutting, CNC turning and milling, CNC grinding, and others.
The typical process of CNC machining is simple:
- The material or workpiece is loaded and mounted to the machine.
- Then, the program or pattern is programmed and set.
- Once done, the entire system will undergo a dry run to test out the program and materials.
- Lastly, the process is pursued.
- Depending on the manufacturer, they can have assessors and inspectors to check if there are any adjustments needed.
The Parts You Can Manufacture Using CNC
You can produce and manufacture many, if not all types of parts and components of machines using CNC processing. Here at HDC Manufacturing, we produce anything from CNC motorcycle parts, bike parts, automotive parts, and even stainless steel, brass, aluminum, titanium, plastic, and others for machinery and equipment!
The overall effect of CNC machining is widespread, and there are tons of products you can make using it, thanks to its heightened advantages!
Pros and Cons of CNC Machining
Continuity
Usually, CNC machines are designed and engineered to run more than 18 hours per day. The longer they run, the better. The only time you have to shut them off would be during maintenance.Consistency
Another advantage would be the consistency and quality of the parts and components. The products will 99.99% be identical, especially since it will depend on the software programmed.Flexibility and Adaptability
CNC machines can also easily be adjusted. What we mean by this is that they can be reprogrammed to perform a different style, structure, and type of product. It’ll just need a little tweaking on the software or program part.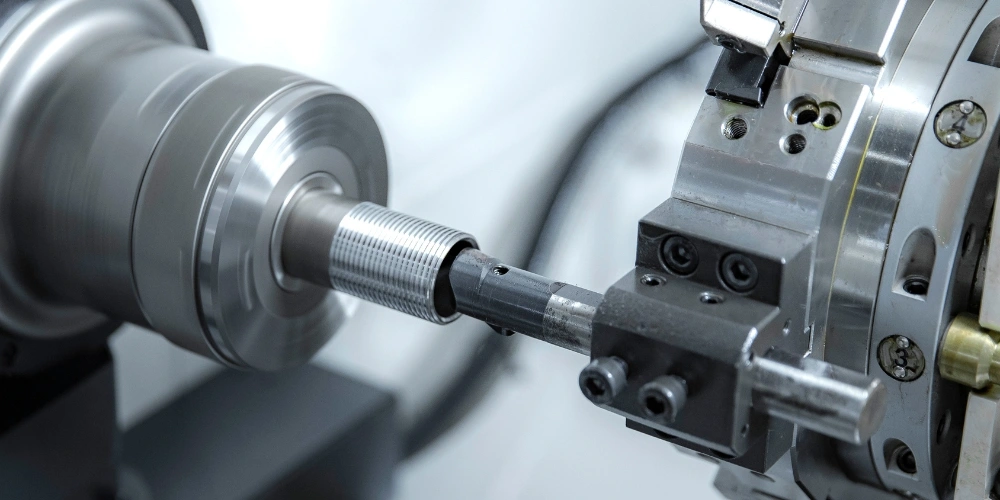
Less Staffing
Last and most definitely not least would be the savings on labor costs. The more CNC machines, the fewer staff, and workers are needed in a plant. Although many people think that CNC machines are expensive – that is only for the rates and/or prices upfront. If you think long-term, it’ll give you a lot of savings. There are many more pros and advantages to using CNC machines, and in fact, you’ll notice them when you start using them. Of course, though, there are cons and drawbacks to it as well, and these include:- Higher Upfront Costs (When Purchasing or Renting the Machines)
- Unemployment
- Loss of Skills
Challenges Faced in CNC Machining
CNC machining may be considered a technology characterized by its numerous applications and high precision but with some challenges in application. One of the major problems is achieving perfect toolpaths and cutting rates for various materials taking into account their hardness, thermoconductivity as well as some other factors. Losing a tight tolerance is another challenge in that it requires constant calibration and monitoring. Deformation and breakage of tools can affect the level of efficiency, as well as quality for product output; maintenance therefore must be routinely carried out. Complex geometries can be a problem to program and so it requires an expert operator. Furthermore design of fixture and material selection play an important role in addressing stability issues on workpiece during machining. The process of overcoming these challenges requires knowledge, sophisticated technologies and careful production preparation in the CNC machining area.
Get High-Quality CNC Machining Services
There will never be a shortage of where you can get the best CNC machining services in the industry, especially now since most organizations and companies are slowly leveraging it to their advantage.
But, if you are trying to get the best quality of services from a Chinese company, you can never go wrong in choosing us here at HDC Manufacturing. For more than a decade, we have produced the best CNC machining parts our clients ever asked for – that made them want to work with us more and more!
Other than our CNC machining parts, we are also considered the best when it comes to CNC rapid prototyping, metal stamping, 5-axis CNC machining, and many more!
Reach out to us and we’ll send a free estimate over to you!
Custom CNC Machining Parts From Manufacturers
- Define Specifications: State the cut material, tolerances and quantity needed for CNC machining parts.
- Research Manufacturers: Search and find a high-quality CNC machining manufacturer with a record of accuracy and dependability.
- Communication: It is also crucial that your specifications and requirements are clearly communicated to the manufacturer in order for there to be an understanding.
- Verify Capabilities: Firmly establish the manufacturing capability, not only their capacity and equipment used but also their quality control measures.
- Request Prototypes/Samples: Prior to starting full production, order prototypes or samples of the manufacturer’s workmanship so that you can evaluate it and ensure its fulfillment corresponds with your expectations.
- Discuss Pricing and Lead Times: Have conversations about pricing, lead times and any other factors to ensure there’s a mutual understanding of the agreement.
- Prioritize Communication: Provide ongoing and productive dialogue between the manufacturer to guarantee an effective collaboration.
Conclusion
CNC machining is a highly advanced and accurate manufacturing process that has several benefits such as precision, uniformity, adaptability, and minimized workforce expenses. This technology encompasses different kinds of machining and materials as well as service which makes it a flexible means for making a variety of components. Although CNC machining poses some challenges, surmounting them demands the expertise, sophisticated technologies and detailed arrangements.