







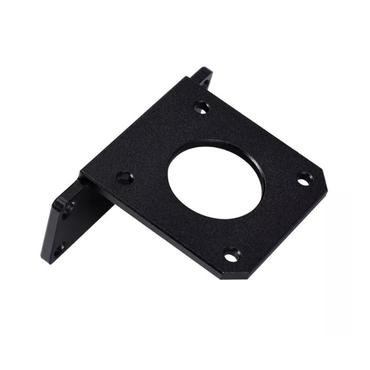
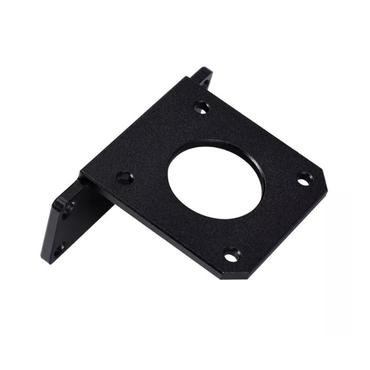
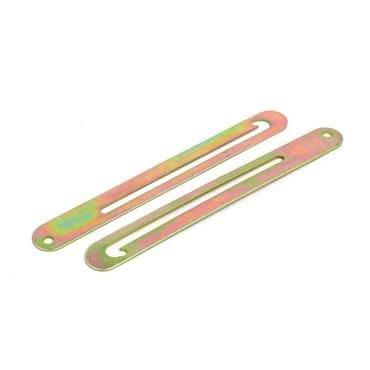
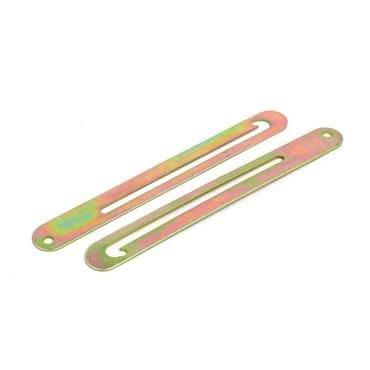
Metal Punching Service
Metal punching or sheet metal punching in which a metal is processed to get embossed with different hole sizes and shapes. Sheet metal punching production can be executed in a hand-operated punch press, however, the CNC or computer numerical controlled punching instrument is what machinists use nowadays.
Punched holes may come in different shapes like circles, squares, etc. Many also consider this process as a substitute or replacement for laser cutting as they can manufacture rapidly and punch various forms and cutouts accurately.








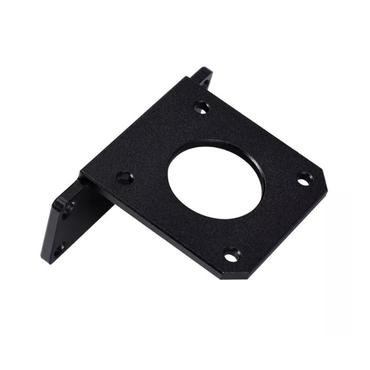
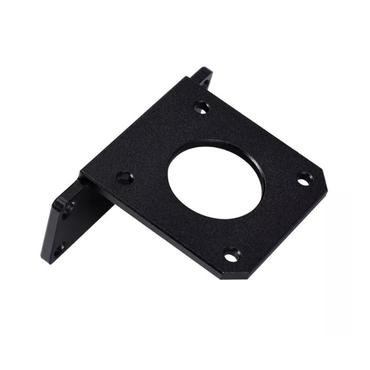
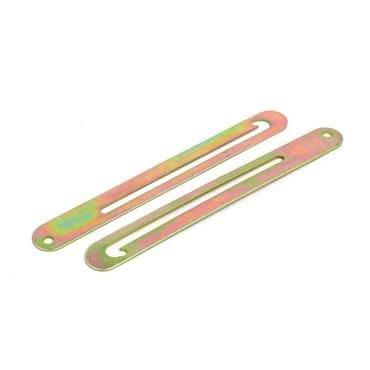
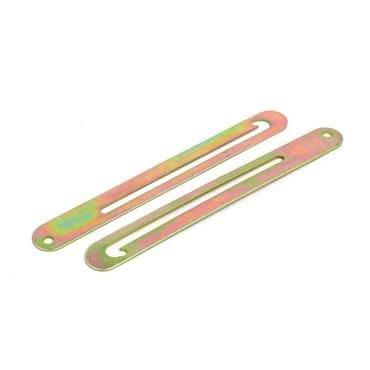
HDC Metal Punching Service
HDC’s metal punching service is where a material is placed in the middle of the punch and die. When it is already turned on, the punch press will now do its job to make its way in cutting the excess materials. The process will be repeated until the demanded shape is accomplished.
We can make metal punched parts up to 20mmthickness in any high-strength metal material, it can be aluminum, steel, stainless steel, etc. Your desired shape of holes (square, rectangle, round, etc) can be achieved with HDC in a short amount of time.
Our punching services include rolling, cutting, punching holes, developing embosses and more intricate shapes, and curving flanges. For more than thirteen years of exceeding our client’s expectations, HDC learned different methods and techniques for manufacturing parts for a certain application.
We are open and welcome to every kind of industry such as automotive, medical, military, aerospace, and so much more. HDC will always make your desired components turn into life with the use of our state-of-the-art machine and components.
We are also making it all complete by adding surface treatments for additional durability, HDC has anodizing, heat treating, bead blasting, passivating, engraving, powder coating, etc.
Looking for a supplier that is not just manufacturing highly reliable products but also giving the best customer care? HDC is the best one for you!
Why choose HDC?
Metal punching is usually accomplished using the leading and advanced machines, HDC has all of that, as well as appropriate facilities to manufacture delicate specialized components. We are using exclusive equipment produced to diminish errors and provide reliable, impressive results.
HDC can produce the exact hole shape that you desire with high speed and durability. We fabricate components for every industry, featuring precise and clean outcomes that made HDC one of the most trustworthy suppliers of metal punching services.
We can assure you that customization is attainable at HDC as we have numerous metal materials that we can use to machine your component. The punch presses from HDC are designed to make a rapid turnaround and universal cuts and shapes.
We are ISO9001 certified and IATF 16949:2016 certified manufacturer that promotes highly durable, aesthetic, and dependable parts, regardless of whether it is metal or plastic material. We also have engineering consultations for each and every client to ensure the product’s design, style, and material is appropriate for its application.
Here at HDC, we ensure your trust and peace of mind, that is why we chose to have different options when it comes to shipment, payments, and trade terms. We have courier, air shipping, and sea shipping, while Paypal, T/T, and L/C are available for payment methods. FOB, CFR, and DDP are for the trade terms.
FAQS Metal Punching Service
You know that we here at HDC Manufacturing are skilled and capable of producing metal punched materials and components, but, just recently, we developed and enhanced our capabilities and started offering metal punching services, too.
If you have a few questions about metal punching services, or if you are in the market trying to work with the best, here is a quick and easy FAQ guide that will lead you to the answers you’re looking for!
What is a Metal Punching Service?
Think about punching paper – it is the same idea, just a different set of machines and equipment. Metal punching service is a type of service in which the metal workpiece or material is “punched” or “shaped” according to the requests or needs of a client.
It’s literally just like punching paper, except that instead of paper, metal is the material being punched or cut.
How is the Metal Punching Service Done?
Metal punching is done differently by various manufacturers. Some manufacturers do a certain step first, while some go straight to the supposed first step. To help you in identifying it further, though, the general way of how metal punching is done would be by the following:
- The sketch, draft, or design is finalized and completed by the client.
- Then, it will be sent to the manufacturer for them to load it onto the software.
- The software reads the sketch or the program. An expert will check if it is attainable and applicable.
- After that, the machine undergoes a dry run to see if it will follow the program precisely and accurately.
- Once done, the punch tooling is positioned properly along with the workpiece.
- Then, the CAD file will be run and the CNC metal puncher will move in both the X and Y directions.
NOTE: This is just a general process of how it’s done. Not all manufacturers follow it like this.
Can All Metals Be Punched?
Before, manufacturers only have a few selected types of steels and metals they punch due to the lack of material and resources. However, in today’s time, engineers and manufacturers reveal that they’re able to punch and machine all types and kinds of steel and metal.
Whether it’s stainless steel, aluminum steel, carbon steel, mild steel – literally everything, it can be machined and punched properly.
Is Metal Punching and Metal Stamping the Same?
Yes and no – let me explain.
Metal punching and metal stamping are two (2) machining processes done to workpieces. Their goal is the same – and that is to ensure that the workpiece will be reformed, reshaped, and reworked, so, how are they the same?
Well, metal punching is done if the manufacturer wants a specific size or shape punched out of the metal. Typically, this punched area will just be a small part.
On the contrary, metal stamping is done to an entire piece. For instance, if you have a sheet metal and you need a large round-shaped metal, a metal stamp will be used in order to produce the shape needed.
Think of it like this, for small punched parts and components, metal punching is done. If you need the larger area, you’ll need to do metal stamping instead.
Which Industries Make Use of Metal Punching Services?
Precision metal machining (which includes metal punching) is widely used across a variety of business sectors and industries. To help you with it, the industries that are capitalizing on CNC metal punching services include:
- Agriculture and Farming Industry
- Construction and Structural Industry
- Military and Defense Industry
- Automotive and Aerospace Sectors
- Commercial Display Industries
- Electrical and Equipment Industry
- Electronics and Telecommunications Industry
- And Many More!
What Are the Capabilities of Metal Punching Services?
Now that we know about the industries that use it, let us now divert our attention to the capabilities or the specific applications metal punching has. Based on the list of industries that need it, the following are the most-known applications and capabilities of metal punching services:
- Aircraft Assembles and Components
- Building and Structural Products
- Doors, Drawers, and Compartments
- Steel Panels
- Enclosures
- Fixtures and Lighting
- Electronic Subcomponents
- And Many More!
What Are the Advantages of Metal Punching?
Metal punching – or even metal stamping has its own breed of benefits and advantages. These include, but are not limited to:
Accuracy and Precision
In machining, precision is the number one priority of a manufacturer. The more precise a workpiece is the better and the higher the value will be. Metal punching usually requires maximum accuracy even in the smallest of products and components.
Speed and Urgency
Another advantageous factor metal punching has is that it is fast and urgent. The combination of speed + accuracy is a lethal combination especially for businesses that are looking for short and long-term success.
Flexibility and Adaptability
If you were surprised that metal punching can be done to all types of metals, then you need to know about this. Metal punching is unlike the type of punching you know – it is not restricted to a single type of material because the pressure, force, distance, and even the weight can be changed all according to the needs of the client.
Where Can You Get the Best and Highest Quality Metal Punching Services?
Metal punching is a complex procedure that is not as simple as punching a piece of paper. Here at HDC Manufacturing, we’ve garnered more than 3 decades worth of metal punching service through our experts, engineers, and operators.
We have produced a whole wide range of products and merchandise to clients in and out of the country by performing metal punching. HDC Manufacturing is such an excellent provider of metal punching services that when you take our service, you can expect us to punch and puncture various types of steels and metals – even plastics, too!
Our metal punching service is one of the best services we are known for, but, other than that, you can also find us reliable and trustworthy if you ever need help with CNC rapid prototyping, 5-axis CNC machining, aluminum forging, and many more!
Don’t think twice about our overall capabilities! Work with us and we will give you the best and highest quality of metal punching services you will ever find in this part of the world!
[toc]