Have you wondered and asked, does aluminum rust? Does it oxidize? In this blog, we’ll be talking about aluminum in a deeper and a more microscopic level.
By the end of this blog, you will learn about aluminum’s overall principle, behavior across certain environments, potential corrosion possibilities, and many more! We’ll never short you with information about aluminum, so, stay tuned!
Does Aluminum Rust?
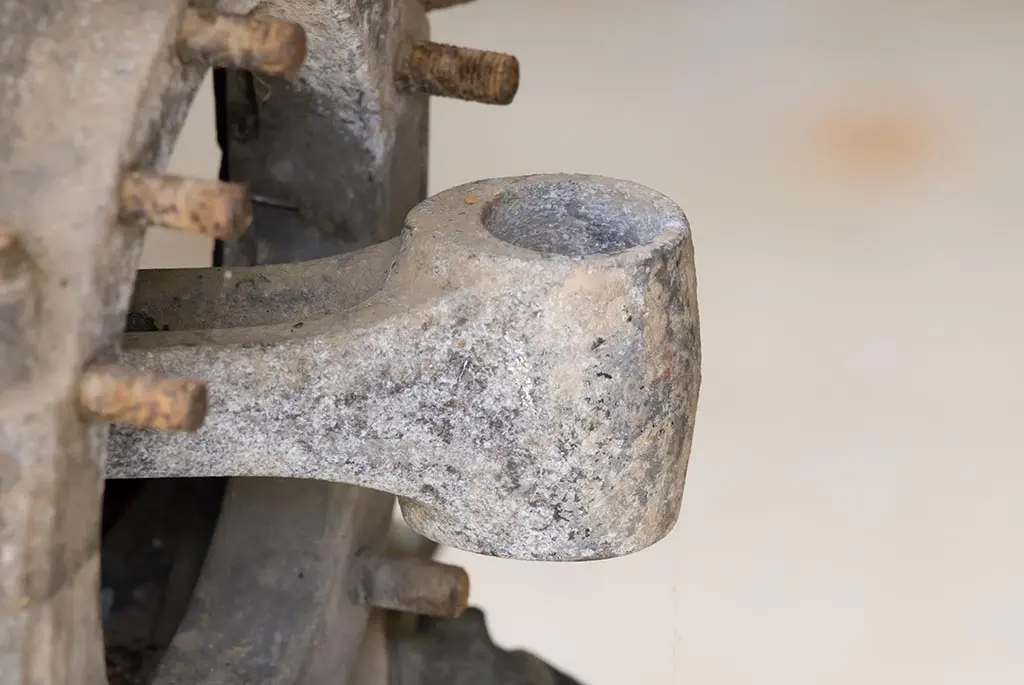
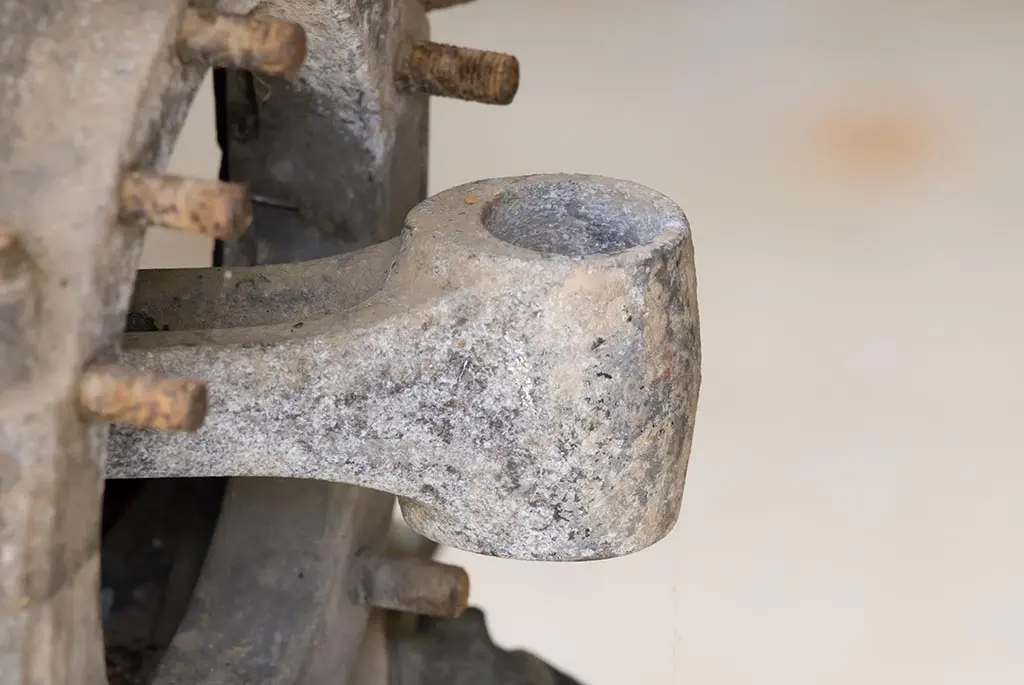
No, aluminum doesn’t rust. Aluminum is one of the few metals that have this capability. Even though it’s a highly reactive metal, you can be 100% sure that it will not rust.
It is, however, not entirely impenetrable. While it doesn’t rust, it can still corrode. The aluminum oxide coating is so robust that it can renew itself after being damaged, but certain instances can cause it to be vulnerable.
Read More: The Role of CNC Machining in Steel Fabrication
Rust vs. Corrosion
Although the terms corrosion and rust are frequently used synonymously, they are not the same. Although they both explain how materials, usually metals, deteriorate over time, their causes, manifestations, and outcomes are different.
Let’s take a look at the table below so we can further eliminate myths and hearsay about what aluminum is and vice versa.
Aspect | Rust | Corrosion |
Definition | A specific type of corrosion affecting iron and steel. | A broad term describing material degradation caused by environmental factors. |
Causing Material | Occurs exclusively in iron and iron alloys. | Can affect all metals and even non-metals. |
Appearance | Reddish-brown flaky surface. | Varies; may appear as discoloration, pitting, or tarnishing. |
Primary Cause | Reaction with oxygen and moisture (oxidation). | Chemical or electrochemical reactions, often with environmental elements. |
Material Impact | Weakens the structure and creates porous surfaces. | Can cause brittleness, structural damage, or surface wear. |
Prevention | Protective coatings, rust inhibitors, and moisture control. | Material selection, coatings, and environmental control. |
That being said, aluminum isn’t totally impenetrable because it can still be corroded. But what makes aluminum rust-proof? What is in aluminum that’s not in other metal types that protects it from rust?
A Deep Dive on Aluminum
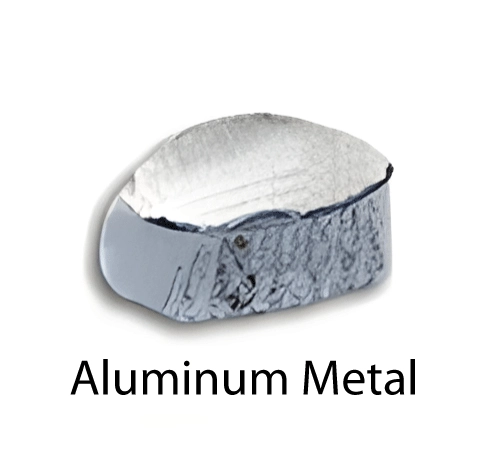
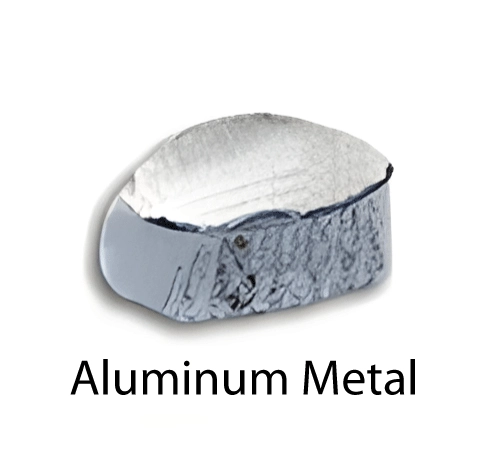
Aluminum is part of one of the most amazing metals present in the world that we live in. So, the simple explanation on why it doesn’t rust is because of its reactive. Counterintuitively, its high reactiveness is its biggest and greatest asset.
Why Iron Rusts and Aluminum Doesn’t
The reason why iron rusts is because of its oxidation principle. When exposed to oxygen, it forms iron oxide, which is rust from the metal surface. This process is called oxidation and is common among metals.
In the case of aluminum, aluminum oxide is what is formed, preventing it from rusting.
Oxide Layer Formation Principle
Microscopically, the formation of aluminum oxide involves the reaction of aluminum atoms with oxygen molecules, creating a crystalline structure that resists penetration by water or air.
While aluminum is resistant to rust, it is not entirely immune to corrosion, especially in environments containing chlorides. Chlorides can disrupt the oxide layer under extreme conditions
Aluminum’s Corrosion Resistance in Various Environments
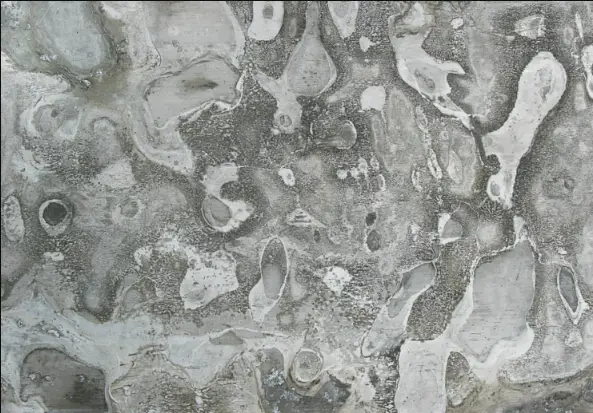
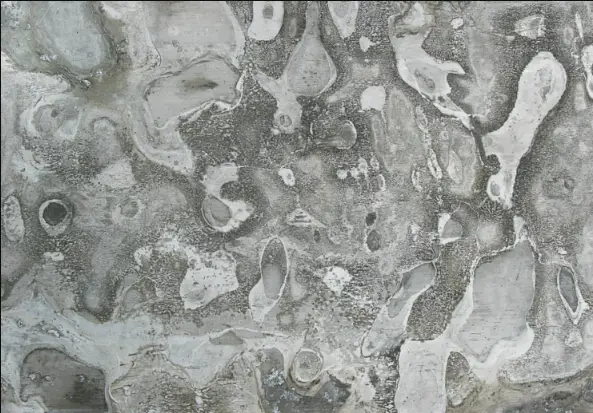
Because of its natural oxide layer, which acts as a barrier against external factors, aluminum shows exceptional corrosion resistance in a variety of situations.
Air
In air, aluminum resists corrosion effectively, even in industrial settings where pollutants are present. The oxide layer reforms quickly if damaged, maintaining its protective qualities.
However, extreme acidic or alkaline conditions can compromise this layer. This is when it can potentially lead to corrosion.
Soil
When buried in soil, on the other hand, aluminum’s performance will vary based on soil type and overall composition.
Well-drained soils are generally safe for aluminum, but environments like clay-rich or organic soils with poor drainage can accelerate corrosion. Protective treatments, such as coatings or anodization, can mitigate these effects
Water
And lastly, under H2O. Aluminum is highly resistant to both freshwater and seawater, respectively. However, it’s not perfect and indestructible.
Although it withstands natural waters, prolonged exposure to highly saline or acidic conditions may degrade the oxide film, leading to corrosion.
Alloys in Corrosion: Resistance of Different Alloys in Action


When comparing corrosion resistance between pure aluminum and its alloys like 7075, 6061, and 5052, it’s important to understand how each performs in various environments.
Pure aluminum naturally forms a protective oxide layer that gives it excellent resistance to oxidation. Aluminum alloys are useful in structural or high-strength applications, but their uses are restricted by their softness and malleability.
5052 Aluminum
Among the alloys, 5052 is particularly notable for its superior corrosion resistance, especially in marine and saltwater environments.
Alloyed with magnesium, this makes it an excellent choice for applications like boat hulls or automotive fuel tanks.
NOTE: 5052 is resistant to saltwater corrosion.
6061 Aluminum
6061 strikes a balance between corrosion resistance and strength, performing well in structural uses and general environments.
The aluminum 6061 is alloyed with silicon and magnesium. It is heat-treatable and can be hardened after forming.
Among its use would be in the structural industry, including bridge components, structural framing, valves and piping, etc.
NOTE: Better than steel in corrosion resistance. Possesses excellent strength-to-weight ratio.
Aluminum 7075
And lastly, 7075. Both 5052 and 6061 have magnesium as their primary elements, but 7075 has zinc. Because of its versatility, 7075 is often used in automotive, aerospace, military, and sporting goods applications.
NOTE: It has an average level of corrosion resistance, better than steel, but the least out of the two other alloys.
What Types of Corrosion Can Aluminum Products Experience?
Aluminum is a robust, strong, and remarkable material, but it’s not indestructible. There are situations and reactions that can cause it to corrode:
Galvanic Corrosion
The first and probably the most common is galvanic corrosion, otherwise known as contact corrosion. This occurs when aluminum comes into contact with a more noble metal, like copper or stainless steel, in the presence of an electrolyte, such as water.
The difference in electrochemical potential causes aluminum to corrode as it acts as the anode in the reaction.
Galvanic corrosion is especially common in marine or industrial environments where metals are frequently exposed to moisture or salty conditions.
TIP: To lessen the burden and risk of galvanic corrosion, you can use protective coatings or isolating dissimilar metals.
Pitting Corrosion
Pitting corrosion happens when small imperfections or breaches in aluminum’s protective oxide layer expose the bare metal to aggressive environments.
This localized attack creates tiny pits that can deepen over time. Factors like chloride ions, often found in seawater or de-icing salts, can accelerate pitting.
TIP: Preventive measures include using aluminum alloys with added corrosion resistance and applying protective finishes.
Uniform Corrosion
Lastly, general or uniform corrosion. In environments where the pH is extremely high or low, or in electrolytes loaded with chloride ions, aluminum’s protective oxide layer struggles to stay intact.
Acidic (low pH) or alkaline (high pH) solutions can destabilize the oxide coating, leaving the aluminum exposed and unable to resist corrosion effectively.
TIP: Like pitting corrosion, its preventive measures include using alloys with better and added corrosion resistance. You can either apply them as protective finishes or as cathodic protection.
Can You Powder Coat Aluminum?
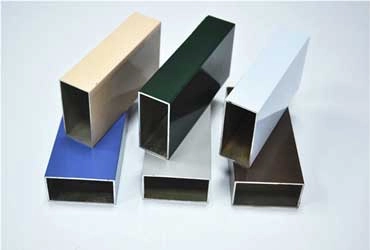
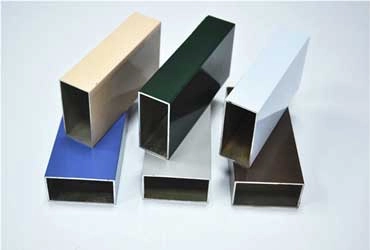
With all those solutions, one can’t help but ask – is it possible to powder coat aluminum? The short and sweet answer is yes, you can.
As a matter of fact, it’s one of the most reliable ways to ensure that your aluminum component remains safe, corrosion-free, and structured. Polishing aluminum with aluminum with better properties is the key!
Cleaning and Maintaining Aluminum Products
Aluminum, of and in itself is already an extremely robust and resistant product. But, like any other thing, it needs to be properly cared for and maintained for it to keep its pristine condition.
So, here are some of the best and most practical tips on what you can do to keep it from breaking apart:
Handling Aluminum
The handling of aluminum components requires care to maintain their quality and prevent surface damage.
- Use soft slings for heavy lifting: Soft slings protect the aluminum when lifting heavy parts, preventing damage.
- Avoid scraping: Keep aluminum from scraping against hard or sharp surfaces to avoid scratches.
- Two-person handling: Use two people when stacking or moving sheets to prevent them from sliding against each other.
- Avoid walking on sheets: Never walk on aluminum sheets to protect them from dents or deformation.
- No dragging or throwing: Always handle aluminum carefully—never drag or toss components to prevent damage.
Cleaning Aluminum
When it comes to cleaning aluminum, there’s no secret ingredient to do so. However, it’s best to make sure to use mild ingredients like mild detergent and water, solvents, abrasive waxes and cleaners, and the like to ensure that the layer wouldn’t be compromised.
NOTE: Aluminum should be washed and dried thoroughly so it doesn’t streak and mark.
Maintaining Aluminum
Again, nothing special. Just clean it regularly, remove dirt and dust buildup, and avoid subjecting it to the harshest and strongest chemicals.
Always remember to start from the mildest ingredient, working your way towards the strongest and harshest ones.
HDC For the Best Aluminums and Alloys Machining Products
For 16+ years, our business has been the same–to provide premium quality products to our clients. Developing our skillset and expertise, you can count on us for everything relating to aluminum and its alloys.
We can help you out with anything from aluminum alloys, titanium alloys, carbon steels, etc. Let us know what you need and we’ll get them for you!
Reach out to us today and get a free estimate!
Discover more with our blog posts.
Recent Posts
Discover more about our products.
Related Products
Instant Quote!