Nylon Injection Molding
HDC is Your Main Provider Of Nylon Injection Molding.
Nylon is an ideal injection molding material. HDC has been in the nylon injection molding service for thirteen years, producing highly versatile, long-lasting, moldable, yet affordable parts for every type of industry.
- Engineering grade nylon material
- Firm, adaptable, and cost-efficient nylon injection molded parts
- ISO9001 certified plastic injection molding company
- We use industry-leading machines and equipment
HDC- The Prime Nylon Injection Molding Supplier In China
The synthetic configuration of HDC’s nylon material offers a high-temperature melting point characteristic. The melted nylon plastic material is being injected into a mold and let cool and harden to be able to conduct the other processes for the part’s advancement. HDC is fabricating parts that are made with nylon through injection molding to also improve their properties.
We all know that nylon is usually available in its natural color, white, or black. With HDC’s injection molding processes, you can have your material be processed in different color pigments depending on your preferences. To boost the tensile strength of a molded product, we consider adding a needed amount of glass fibers to the nylon material. HDC doubtlessly offers its whole expertise, experiences, and mastery in developing your components.
Custom Your Nylon Injection Molding With HDC
Due to our nylon material’s high melting point capacity and high tensile strength, it is ideal to be applied in manufacturing car engine parts. We can also combine it with additional materials to enhance the component’s qualities.
HDC’s nylon is commonly used in manufacturing automotive parts because of its toughness and has lower weight compared to metal parts. Lower manufacturing cost is also an advantage in using nylon for a certain application.
Our nylon 66 material for injection molding is a semi-crystalline polyamide that has excellent fatigue resistance, stiffness, and great mechanical strength. It is used in creating industrial and consumer products, as well as other automotive and electronic parts.
HDC’s nylon 6 material has exceptional thermoplasticity with high compressive and tensile strength. It is known in injection molding to manufacture bearings and automobile components.
The nylon injection molding here in HDC is used to create wheels, bushing, housings, gears, clips, electrical components, and other applications wherein higher temperature conditions are present.
HDC ensures that our custom nylon injection molding products are 100% customer preference-based components. We will help and guide you in picking the right material, color, surface finishes for different sizes and components shapes.
Why HDC Nylon Injection Molding
HDC has varieties of plastic injection molded polyamides consisting of Nylon 612, 611, 6, and 66, strengthened, conductive, and intense melting point grades. HDC mastered the plastic injection molding nylon material components for industries ranging from motorcycle parts to intricate components for the medical industry.
This kind of extremely adaptable thermoplastic HDC injection molding material is employed in tons of applications because of its excellent electrical and mechanical properties. Our nylon material also has exceptional chemical and wear resistance, all at economical pricing. HDC’s machining services and unique customer service approach will prove to you why big industries keep on engaging with us over and over for a long time.
HDC Capabilities On Nylon Injection Molding




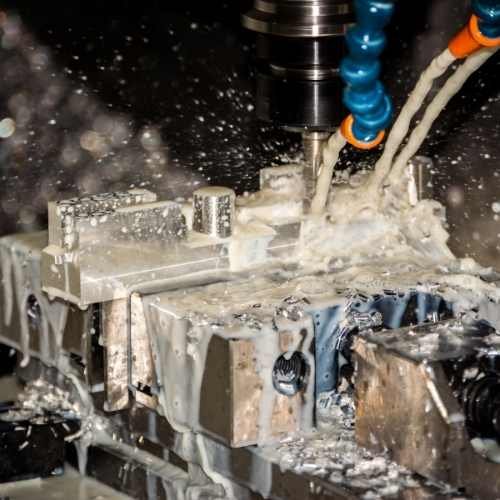
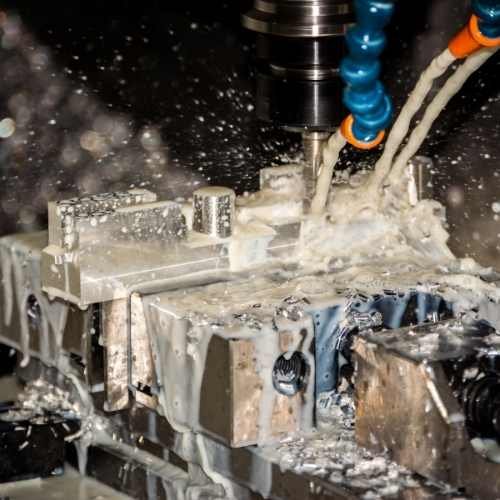
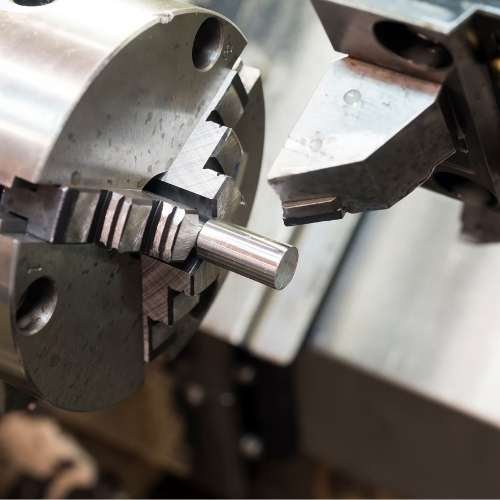
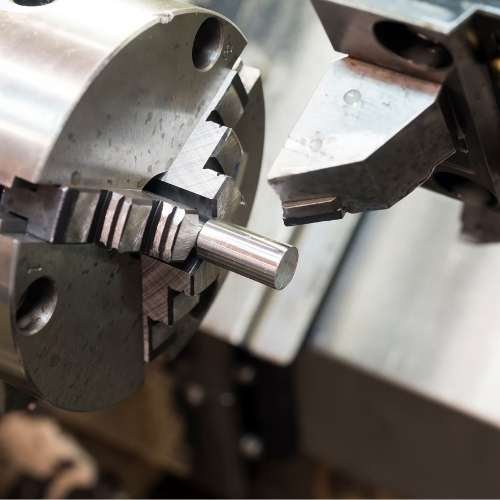


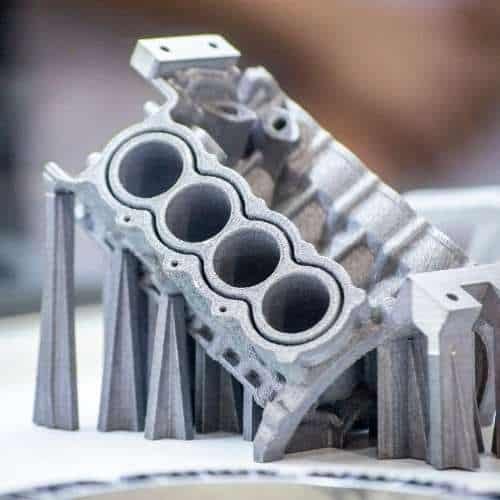
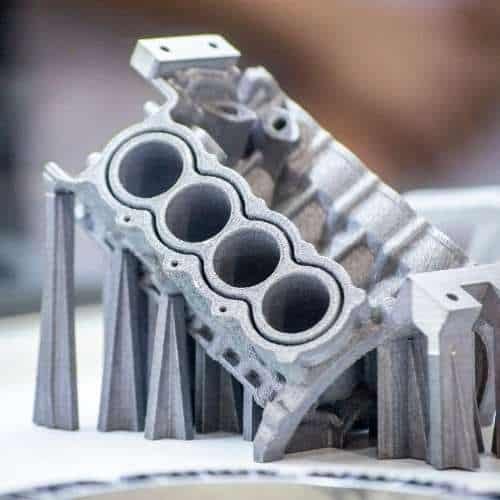
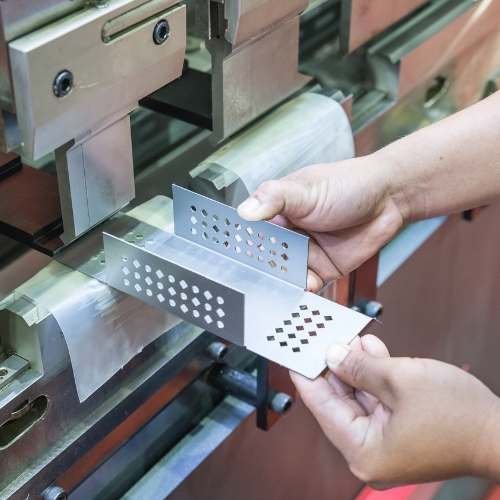
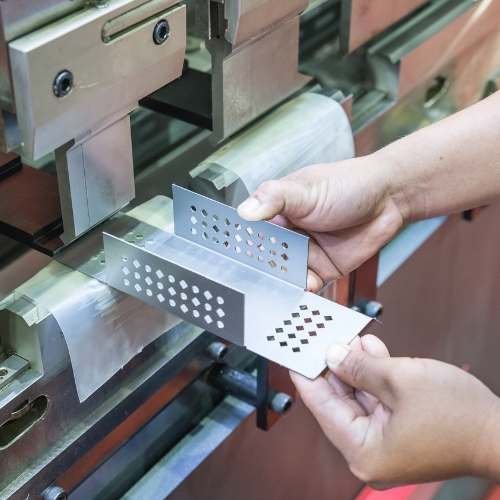


HDC Nylon Injection Molding
Dealing with different industries and components with an immense urge to serve is what made HDC the most trusted nylon injection molding manufacturer. Your desired nylon material grade is here with HDC, you can go with 6, 611, 612, or 66.
Along with providing quality products is the tools and types of machinery. HDC will accommodate your product-developing concerns using the leading CNC machines that have proved their contributions in producing ideal components.
A certain company will never be ISO9001 certified unless they have a team that ensures the quality of its products. HDC doesn’t only have the people that make it, we have the experts who produce it. Quality control is important here in HDC, we ensure that your components will give the best service for a very long time.
Surface treatments will add to your part’s ability and properties, and HDC’s finishes can be applied to your plastic or metal parts. We have anodizing, tumbling, powder coating, passivating, brushing, engraving, and so much more.
When it comes to delivering your components, HDC has courier, sea shipping, and air shipping that carries your parts with your preferred packaging. Paypal, T/T, and L/C are the payment terms we have, while FOB, CFR, and DDP are the trade terms that we offer to each client.
Aside from having CNC machining services and injection molding, HDC offers other manufacturing ways like aluminum forging, aluminum extrusion, investment casting, pressure die casting, magnesium dies casting, and blow molding.
Care to have the recommended nylon injection, molding provider? Have it a go with HDC!
Frequently Asked Questions (FAQ) – Nylon Injection Molding Parts
When it comes to manufacturing precision components and durable parts, Nylon Injection Molding has emerged as a top contender in the realm of modern engineering. In this article, we delve deep into the world of Nylon Injection Molding Parts to provide you with a comprehensive FAQ guide that not only answers your burning questions but also equips you with valuable insights into this versatile manufacturing process.
What Are Nylon Injection Molding Parts?
Nylon Injection Molding Parts are intricately designed components crafted using the injection molding process, utilizing nylon as the primary material. This method enables the production of high-quality, precise, and resilient parts, suitable for a wide range of applications.
Why Is Nylon Good for Injection Molding?
Nylon’s suitability for injection molding lies in its exceptional properties. Its impressive strength-to-weight ratio, resistance to chemicals, and high-temperature tolerance make it an ideal choice for manufacturing durable and reliable parts.
Which Nylon Materials Can Be Used for Injection Molding?
Various nylon materials are compatible with injection molding. These include Nylon 6, Nylon 66, and specialty nylons like Nylon 12. The selection depends on the specific requirements of the intended application.
How Does Nylon Compare to Other Materials for Injection Molding?
Nylon distinguishes itself by its toughness, wear resistance, and versatility. In comparison to materials like ABS, polypropylene, and polycarbonate, nylon often emerges as a preferred choice, especially for industrial and consumer products.
Are There Any Limitations to Nylon Injection Molding?
While Nylon Injection Molding offers numerous advantages, it’s essential to be aware of potential limitations. Nylon can absorb moisture, affecting its mechanical properties, so thorough drying before processing is crucial. Additionally, it may not be suitable for applications requiring high optical clarity.
What Is the Typical Production Cycle for Nylon Injection Molded Parts?
The production cycle for Nylon Injection Molded Parts encompasses several key steps, including material preparation, injection molding, cooling, ejection, and quality control. The duration varies based on factors such as part complexity and size.
What Products Are Typically Produced Using Nylon Injection Molding?
Nylon Injection Molding finds extensive use in the manufacturing of a wide array of products. These include automotive components, electrical connectors, consumer goods, and various industrial parts.
Does Nylon Get Brittle Over Time?
Nylon can become brittle when exposed to prolonged UV radiation. However, this effect can be mitigated by incorporating UV stabilizers into the material.
How Suitable Is Nylon for Anti-static Applications?
Nylon can be modified with anti-static additives, making it suitable for applications where controlling static electricity is paramount, such as in electronics packaging.
What Should Be Noted When Using Nylon Products?
Users of Nylon products should be aware of potential moisture absorption, temperature limitations, and compatibility with specific chemicals. Adhering to proper handling and maintenance guidelines is essential to ensure optimal performance.
What Are the Flame Resistance and Oil Resistance of Nylon?
Nylon is generally not highly flame-resistant, but it can be modified for improved flame resistance. It exhibits good resistance to many oils and chemicals, adding to its versatility.
Can Nylon Injection Molded Parts Be Recycled?
Yes, Nylon Injection Molded Parts can be recycled. Recycling methods may vary depending on the specific type of nylon used and the availability of recycling facilities.
Can I Customize Nylon Injection Molded Parts?
Absolutely. Nylon parts can be customized to meet specific design requirements. Customization options include altering color, texture, and mechanical properties.
What Customization Options Are Available for Nylon Injection Molded Parts?
Customization options for Nylon Injection Molded Parts are diverse. These include adding reinforcing fibers, modifying surface finishes, and adjusting the composition to achieve desired characteristics such as increased strength or flexibility.
Conclusion
In conclusion, Nylon Injection Molding Parts offer a remarkable combination of strength, versatility, and customization possibilities. Whether you are in the automotive industry, electronics, or any other sector requiring precise, durable components, Nylon Injection Molding is a solution worth exploring. With the insights provided in this FAQ guide, you are well-equipped to navigate the world of Nylon Injection Molding Parts effectively.