Exploring the Benefits and Challenges of Custom Magnesium Parts in Modern Manufacturing
Discover the remarkable advantages and inherent challenges of using magnesium in custom parts manufacturing. From its impressive lightweight properties and high strength-to-weight ratio to its limitations in corrosion resistance and production costs, this blog delves into why magnesium is a crucial material in industries such as automotive and aerospace, and how to navigate its complexities.
Advantages of Magnesium Parts
Lightweight Properties
Magnesium’s inherent lightweight nature makes it a preferred material, especially in industries where reducing weight is critical. From automotive components to aerospace structures, the weight savings offered by magnesium parts contribute to enhanced fuel efficiency and overall performance.
High Strength-to-Weight Ratio
Despite its lightness, magnesium boasts an impressive strength-to-weight ratio. This characteristic makes it suitable for applications where durability and robustness are paramount. Manufacturers increasingly turn to magnesium to achieve structural integrity without compromising on weight.
Corrosion Resistance
Magnesium exhibits excellent corrosion resistance, a vital feature for components exposed to harsh environmental conditions. This resistance ensures the longevity of custom magnesium parts, making them reliable and cost-effective over the long term.
Limitations in Using Magnesium for Parts Manufacturing
Using magnesium alloy for parts manufacturing offers benefits such as low density and high strength-to-weight ratio, but it comes with limitations. These include susceptibility to corrosion, a low elastic modulus leading to potential deformation under load, limited temperature range, welding challenges, a restricted range of alloys, higher production costs, and limited market acceptance. Despite ongoing research, these drawbacks must be carefully considered when evaluating magnesium alloy’s suitability for specific applications, weighing its advantages against the outlined limitations.
Types of Magnesium Alloy Used for Custom Parts
- AZ31B:
- Balances strength and formability, suitable for intricate components.
- AZ91D:
- Offers improved strength but may be more challenging to form.
- AM60B:
- Provides excellent castability, making it suitable for die-casting processes.
- AE42 and AJ62:
- Preferred for applications requiring elevated temperature resistance.
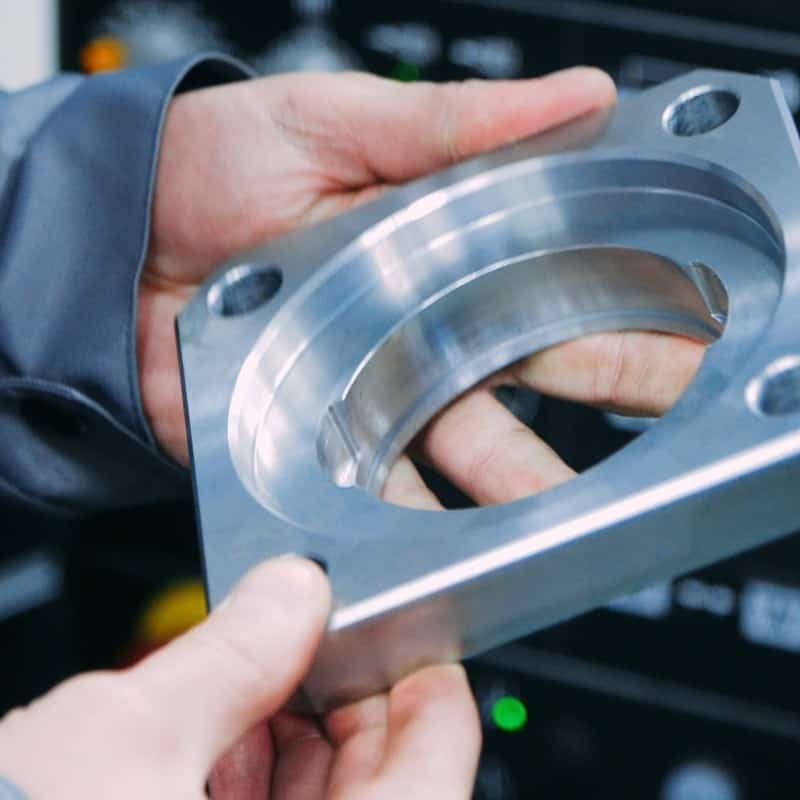
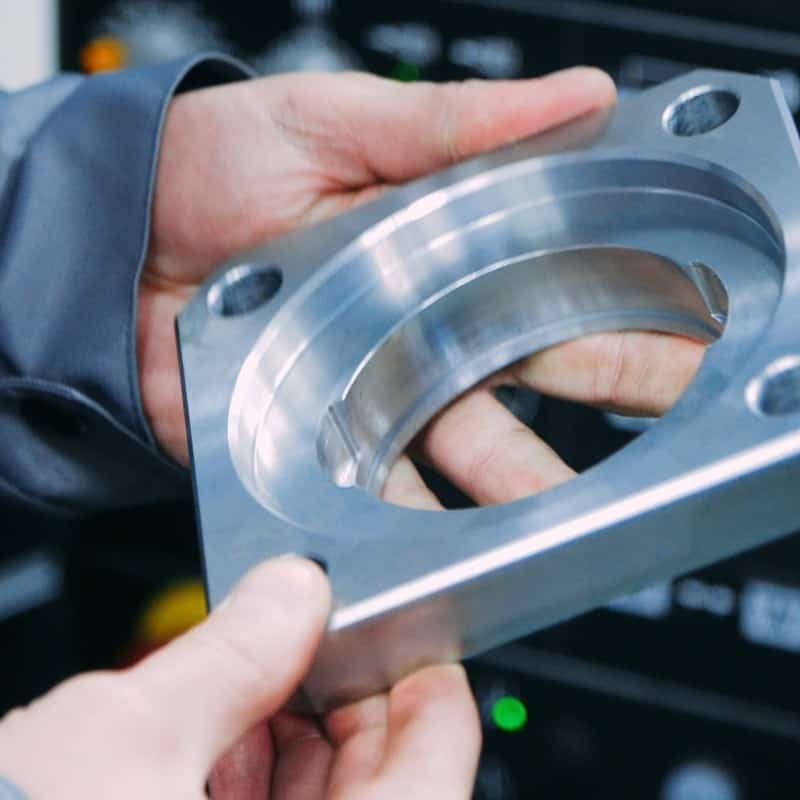
Common Finishes for Magnesium Parts
- Anodizing: Enhances corrosion resistance and provides color options.
- Painting: Adds aesthetics and a protective layer against corrosion.
- Powder Coating: Forms a durable, protective finish with various color choices.
- Chromate Conversion Coating: Improves corrosion resistance and serves as a base for other finishes.
- Electroless Nickel Plating: Increases hardness, wear resistance, and corrosion protection.
- Polishing: Creates a smooth, reflective surface for improved aesthetics.
- Shot Peening: Enhances fatigue resistance through surface compression.
- Passivation: Chemically removes free iron for improved corrosion resistance.
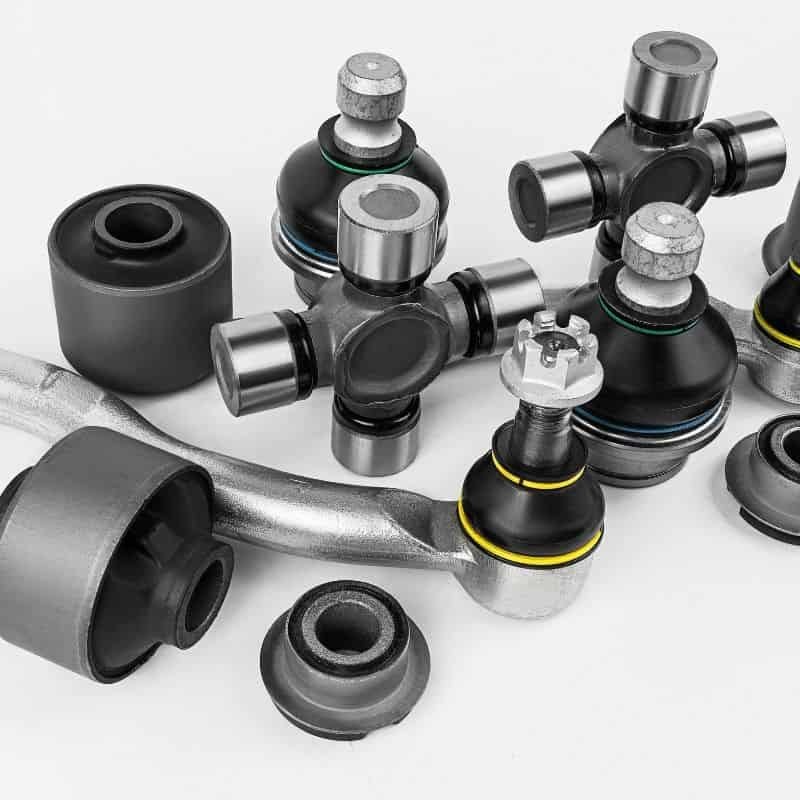
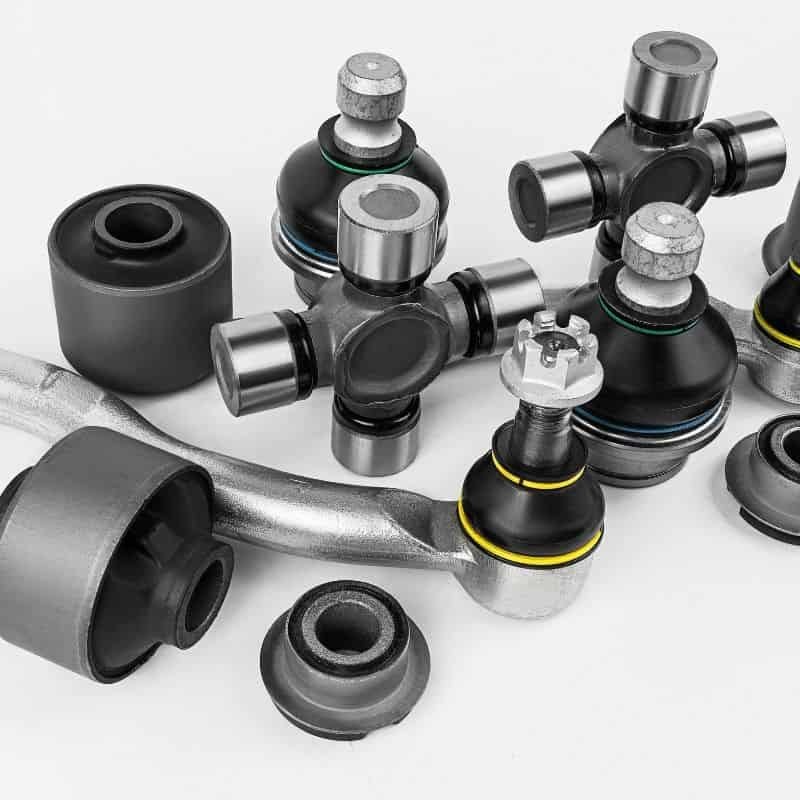
Processing Techniques for Manufacturing Magnesium Parts
- Die Casting:
- Die casting is a popular method for mass-producing intricate magnesium parts with high precision and dimensional accuracy.
- Extrusion:
- Extrusion involves forcing magnesium through a die to create profiles, tubes, or complex cross-sections, offering versatility in shaping.
- Machining:
- Forging:
- Forging involves applying pressure to shape and deform magnesium into desired forms, enhancing its mechanical properties.
- Sheet Metal Forming:
- Sheet metal forming techniques, like stamping and bending, are utilized for creating magnesium parts with specific geometries and structural characteristics.
- Powder Metallurgy:
- Powder metallurgy methods, including compaction and sintering, can be employed to manufacture magnesium parts with complex shapes and controlled porosity.
- Welding:
- Welding techniques, albeit challenging due to magnesium’s reactivity with oxygen, can be used to join magnesium components for larger assemblies.
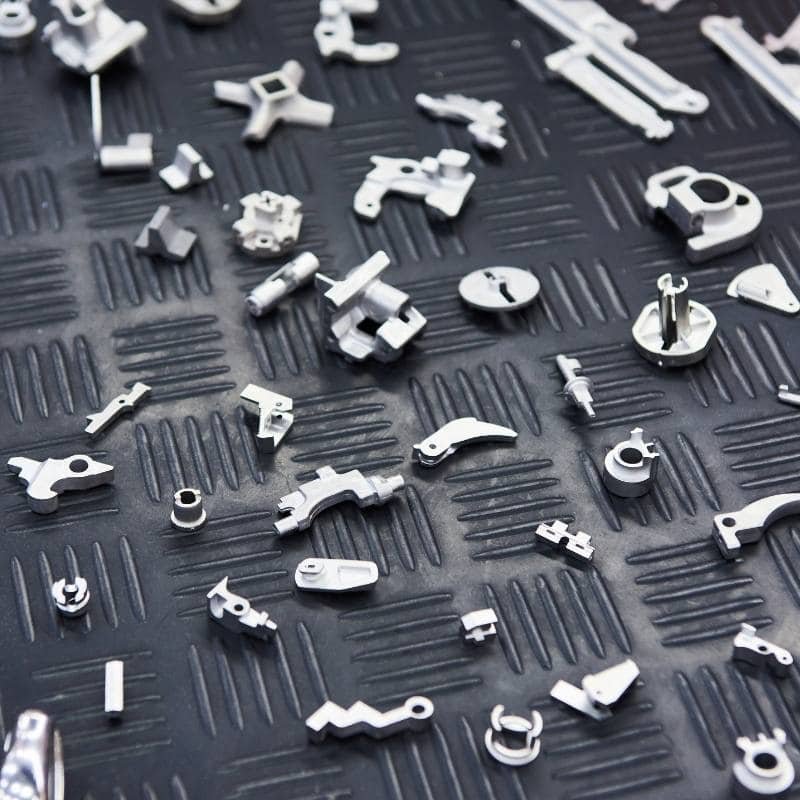
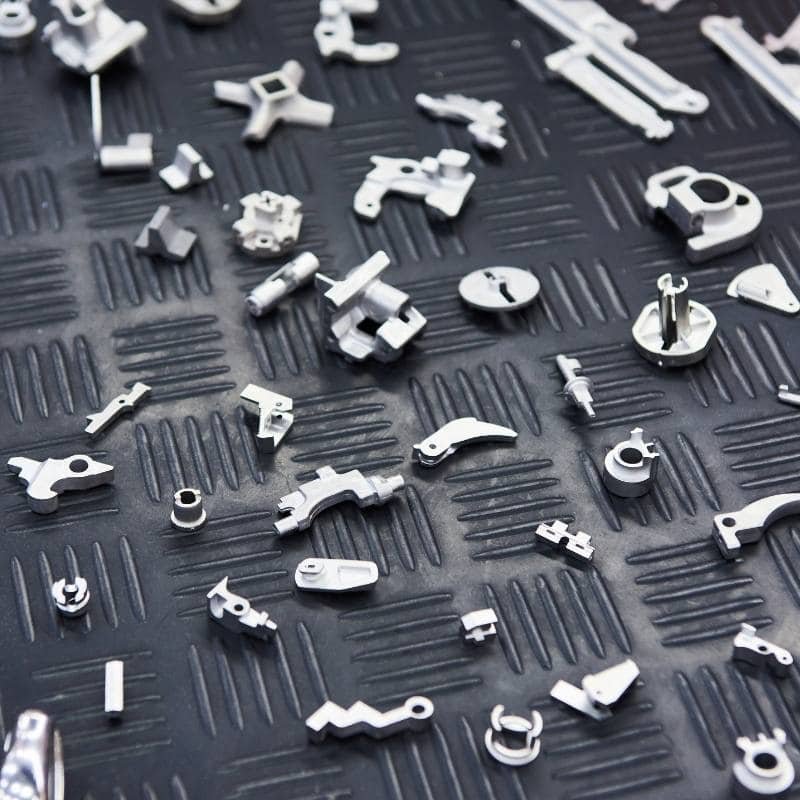
Application of Magnesium Parts
Magnesium parts are widely applied across industries due to their low density, high strength-to-weight ratio, and machinability. In the automotive sector, magnesium is used in components like steering wheels and engine parts for weight reduction and improved fuel efficiency. The aerospace industry employs magnesium in aircraft structures and engine components to enhance overall fuel efficiency. Magnesium is also utilized in electronics, medical devices, sporting goods, power tools, consumer products, military applications, and renewable energy projects, showcasing its versatility in providing lightweight, durable solutions for various engineering needs.
Maintenance Tips for Magnesium Parts
Maintaining magnesium parts for longevity involves applying corrosion-resistant coatings, regular cleaning, and avoiding harsh environments. Inspect for damage, store in dry conditions, use compatible fasteners, and refrain from abrasive cleaning. Control operating temperatures, apply proper lubrication, and follow manufacturer guidelines for specific alloy types. These practices ensure optimal performance and durability of magnesium components over time.
Cost Consideration When Custom Magnesium Parts
- Material Costs: Alloy composition impacts overall expenses.
- Manufacturing Processes: Die casting, extrusion, or machining processes have varying cost implications.
- Finishing and Coating: Additional processes like anodizing contribute to costs.
- Quality Standards: Meeting standards require additional testing, affecting expenses.
- Production Volume: Mass production reduces per-unit costs.
- Tooling and Equipment: Initial costs for specialized tools and equipment contribute.
- Customization Complexity: Elaborate designs or intricate details may increase costs.
- Market Conditions: Fluctuations in raw material costs influence expenses.
- Shipping and Logistics: Transportation considerations contribute to the final cost.
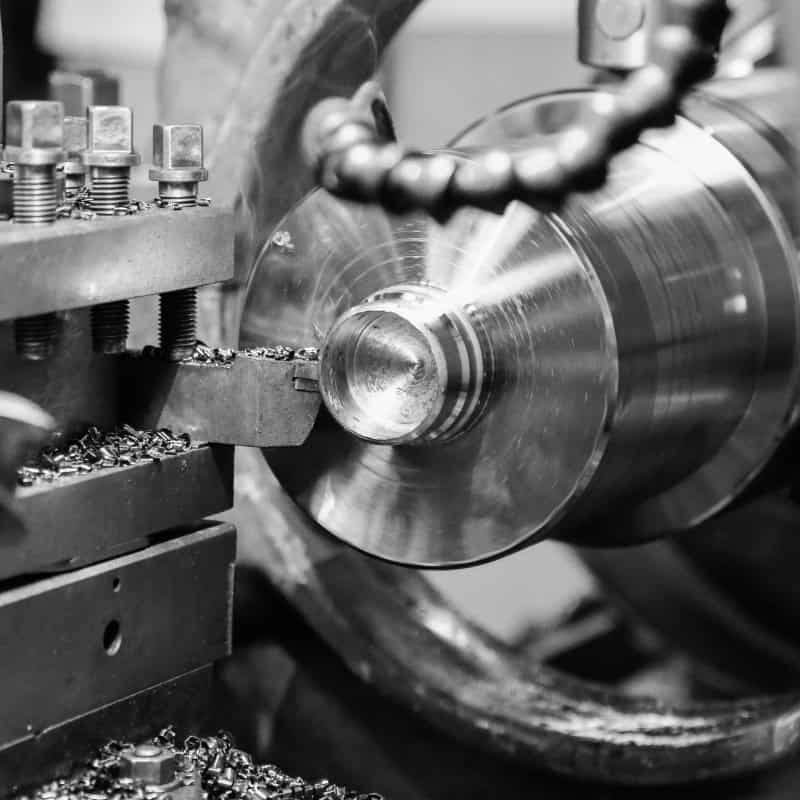
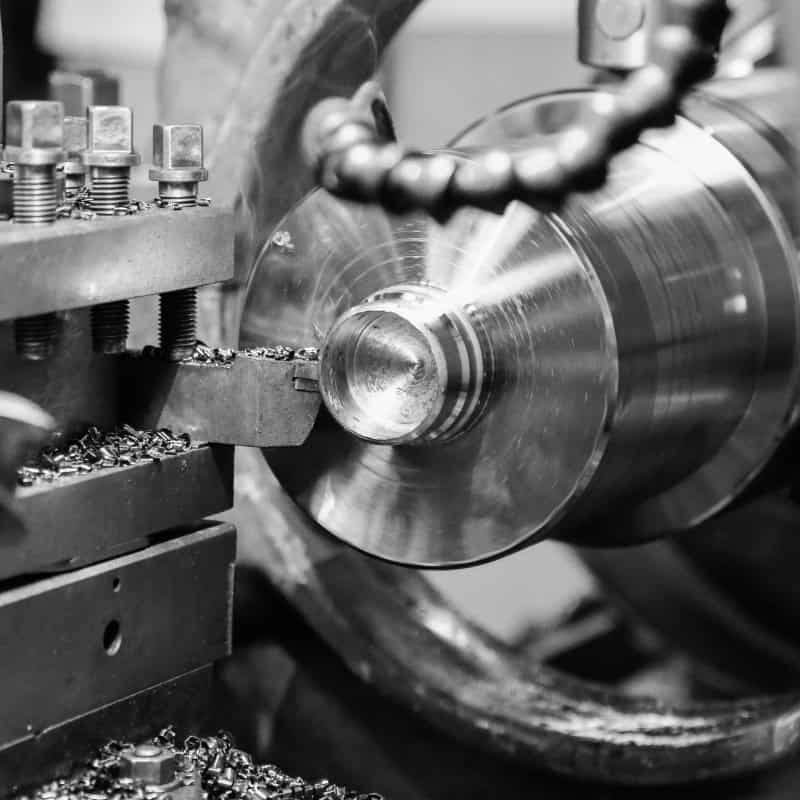
Custom Magnesium Parts From Manufacturers
Obtaining custom magnesium parts from manufacturers involves a systematic process:
- Requirement Assessment: Clearly define your specifications, including design, dimensions, and performance requirements for the custom magnesium parts.
- Material Selection: Work with the manufacturer to select the appropriate magnesium alloy based on your application needs and budget considerations.
- Design and Engineering: Collaborate with the manufacturer’s design and engineering teams to refine the specifications and ensure manufacturability.
- Quotation and Cost Evaluation: Request a detailed quotation that includes material costs, manufacturing processes, finishing, and any additional services. Evaluate costs against your budget.
- Prototype Development: If feasible, develop a prototype to test and validate the design before full-scale production.
- Quality Assurance: Discuss and establish quality control measures to ensure the final magnesium parts meet your desired standards and specifications.
- Production Planning: Work with the manufacturer to plan the production schedule, considering lead times, production volume, and any specific timelines you may have.
- Communication and Collaboration: Maintain open communication with the manufacturer throughout the process, addressing any concerns or modifications promptly.
- Inspection and Testing: Implement inspection and testing procedures during and after production to verify the quality and performance of the magnesium parts.
- Packaging and Delivery: Determine packaging requirements and coordinate the logistics for the delivery of the custom magnesium parts to your location.
By following these steps and maintaining a collaborative relationship with the manufacturer, you can ensure a smooth and efficient process for obtaining high-quality custom magnesium parts tailored to your specific needs.
Conclusion
Custom Magnesium Parts stand at the forefront of innovation in manufacturing. From their lightweight marvels to the enduring strength they bring, magnesium components have reshaped industries and pushed the boundaries of what’s possible. As we navigate challenges, embrace advancements, and explore new applications, magnesium’s enduring legacy continues to unfold.