Exploring CNC Machining for Metals: Key Techniques & Benefits
Dive into the world of CNC machining for metal components. This guide covers everything from types of metals and their applications to the cost factors and quality control measures crucial for achieving precision in manufactured parts.
Types of Parts That CNC Machines Can Produce
- Fittings
- Housings
- Ball Joints
- Suspension Arms
- Brackets
- Rollers
- Spacers
- Valves etc.,
Applied Industry of CNC Metal Parts
Applications of CNC metal parts are huge and wide ranging from the aerospace, automotive to medical devices, electronics industry even across oil & gas manufactures products defense instrument super communication mixed energy constructing water vehicles consumer resources as well guy food manufacturing mining environmental connected ongoing lines. CNC, precision machined metal parts play essential functions across various industries such as aircraft and medical devices to motor vehicles electronics apsemblers anf heavy machinery because of their accuracy flexibility toughness many among others.
Costs of Using a CNC Machine for a Metal Material
- Aluminum 6061– $25
- Aluminum 7075– $80
- Stainless Steel 304– $90
CNC Machine Can Be Used for Metals
A CNC machine can truly slice and dice a metal, it is known for its exceptional precision and exactness. CNC machining can develop various outcomes and finishes depending on certain metal materials and their toughness and rigidity.
Lots of things around us are metals that are manufactured by using a CNC machine. For example, aluminum is used to create auto parts and other sports equipment. Stainless Steel for utensils, gears, nuts, and cooking accessories. Brass is a great material when fabricating food containers.
Types of Metals That Can Be Used in CNC
- Aluminum- its 6061 and 7075 grades are the most popular ones.
- Steel- this one has 303,304, 316L, 410, and 416 that are often used with CNC.
- Brass- C3604 and C3602 have great machinability and mechanical attributes.
- Copper- is used to machine electronic instruments.
- Titanium- is the most known material for biomedical applications.
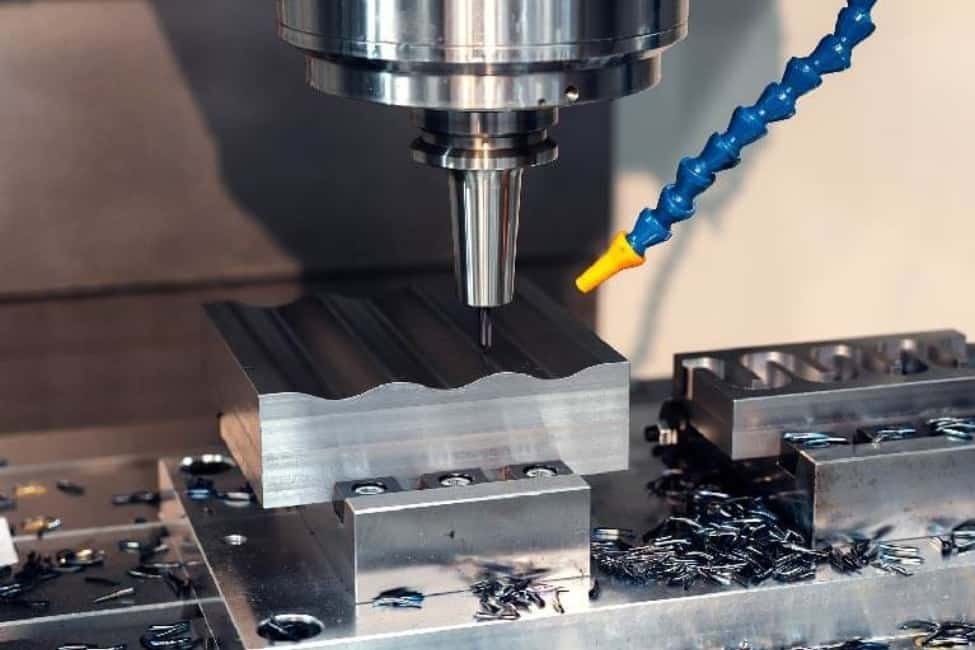
Surface Finishes and Coatings Available for CNC Metal Parts
CNC metal parts can be beautified with different surface finishes and coatings like anodizing for the aluminum, powdering paint: a combination of aesthetic texturing that also provides basic protection. On-site plating such as chrome nickel state or zinc is used decorative corrosion and resistance having fabricate stainless passivated to polishing blue chemical film br Besides, coatings such as ceramic plates or Teflon materials to PVD and CCD can improve the performance of processes in addition light etching for branding proofs that are permanent plus electropolishing surface improvement. The decision made regarding fitting collaborates with material, utilization intention required and designed looks that meet specific standards as well requirements for the CNC metal parts.
CNC Machining Accommodates Intricate Designs for Metal Components
Intricate designs for metal components are efficiently much adapted to CNC machining. Its high precision and cutting capacity enables precise creation of various geometrical shapes, shape details as well as patterns on metallic materials. With a correctly programmed toolpath that is easy to follow, CNC machines are capable of executing even the most complex designs with relative ease. This function renders CNC machining a perfect option for fields of use like the aviation, automobile, medical equipment and electromechanical products that involve complex configuration fitted with submicron accuracy. Whether it is the manufacture of intricate prototypes or, more complex production parts, CNC machine tools provide both high precision and the ability to adjust tool cutting speeds in order to bring designs for complex metal components into reality.
Quality Control Measures To Ensure Precision and Accuracy in CNC Metal Parts
The quality control process for CNC metal parts entails the use of sophisticated inspection equipment such as optical comparators, in-process checks regularly to verify dimensional accuracy through periodic first article certification. The use of such quality assurance tools as tool calibration, statistical process control and material verification eliminates inconsistency. In an attempt to acquire surface quality and defects, visual checks as well as surface finish inspections are undertaken. Special emphasis must be put on tight tolerances, and full traceability is established through detailed documentation. While the former is a feedback loop between quality control and machine operators that addresses issues as they arise, root cause analysis does not only reveal defects to work on with continuous improvement upholding overall precision and accuracy in CNC metal part manufacture maintaining designs specifications standards.
Cost Factors Associated With CNC Machining for Metal Components
Issues relating cost in CNC machining for metal components include material costs, efforts made to control wastages, setting up of the machine tools and equipment thereby creating tooling expenses among other factors that correspond with labor inputs into work stations along these lines which also increase as machines gain time both in operations besides quality demands related thereto concerning surface finishes together with resources invested upon controls exercised upon These elements of cost control include material selection, effective programming and economizing on the waste generation while complex designs together with tight tolerances tend to enhance expenses. Striking a balance in the foregoing elements is vital for ensuring cost-effective CNC machining projects, which guarantees quality even as production costs are kept under check.
Guidance for Custom CNC Metal Parts From Manufacturers
In ordering custom CNC metal parts from the manufacturers, there should be a clear specification defining material type and tolerances. Coordinate with the supplier to choose an appropriate metal substrate and request prototypes in case available. Make sure that the manufacturer observes strict quality measures and certifications, along with surface finishes … It is crucial to provide transparent communication and documentation all over the project process.
Remember that the volume of production, cost estimates and post-production services should be taken into consideration as well costs may have to be negotiated with payment terms too. Besides, ask about the manufacturer’s quality control processes and request copies of any information related to guarantees or warranties. If you obey the above rules and keep in touch with your manufacturing partner, it is possible to establish a fruitful collaboration that will ensure accurate custom assemblies of CNC metal components specific for your project.
Conclusion
In conclusion, CNC machining is a vital technology with a wide range of applications in diverse industries, offering the ability to create precise and complex metal components. It plays a crucial role in modern manufacturing, enabling customization and accuracy. While it provides numerous benefits, including the ability to work with various metals and intricate designs, it’s important to consider cost factors and collaborate effectively with manufacturers to ensure successful projects and accurate custom assemblies.
Resources: