Mastering CNC Machining for Custom Titanium Parts
Embark on a journey into the realm of precision engineering through our exploration of CNC titanium components. These artifacts, meticulously shaped by Computer Numerical Control (CNC) machining processes, exemplify the remarkable qualities of titanium—acknowledged for its extraordinary strength-to-mass ratio, resistance to corrosion, and biocompatibility. Across aerospace to medical domains, CNC machining ensures the precise crafting of intricate titanium elements, meticulously aligning with rigorous industry specifications.
Understanding CNC Titanium Parts
In the realm of precision engineering, CNC titanium parts epitomize the culmination of Computer Numerical Control (CNC) machining processes, leveraging titanium as the predominant substrate. The CNC machining modus operandi intricately utilizes exacting computer-regulated implements to incise, sculpt, and fabricate elaborate designs onto titanium reservoirs. Titanium, renowned for its elevated strength-to-mass ratio, corrosion resistance, and biocompatible attributes, is prevalent in aerospace, medical, and industrial domains. CNC machining, with its commitment to precision, ensures the meticulous creation of intricate titanium elements, adhering rigorously to the stringent specifications set by diverse industries seeking robust yet lightweight constituents.
Advantages of Titanium
Titanium emerges as a standout entity, characterized by its extraordinary attributes, notably an incomparable strength-to-weight proportion that imparts upon it a dual nature of being both ethereal and sturdy. Its noteworthy resilience against corrosive forces guarantees prolonged endurance in formidable environments, while its innate biocompatibility unveils diverse avenues for applications within the medical landscape. Furthermore, titanium’s inherent capability to withstand elevated temperatures, owing to its elevated melting point, amplifies its adaptability across a spectrum of rigorous scenarios.
Types of Parts Suitable for CNC Titanium Production
The suitability of diverse components for CNC titanium production arises from the material’s distinctive properties. In the aerospace sector, turbine blades, engine components, and structural parts are frequently fabricated using CNC titanium machining, exploiting its notable strength-to-weight ratio. Within the medical domain, titanium’s biocompatibility benefits implants like bone screws and dental prosthetics. CNC machining is also applied for the intricate crafting of components used in high-performance sports equipment and marine applications. Industrial realms employ CNC titanium production for components demanding durability in adverse conditions. Overall, CNC titanium machining showcases versatility, addressing a wide spectrum of parts across different industries.
Common Application Areas for Titanium Parts
- Aerospace:
- Medical Devices:
- Military and Defense:
- Chemical Processing:
- Automotive:
- Sports Equipment:
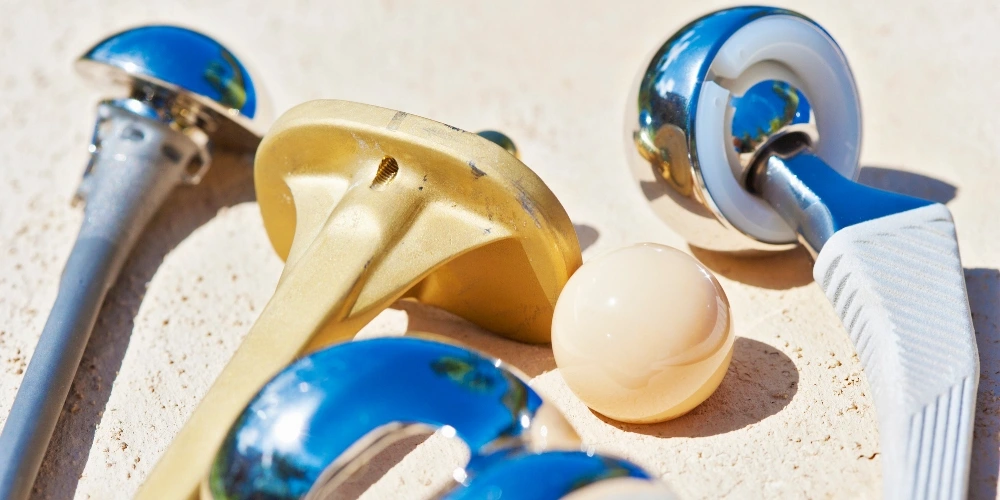
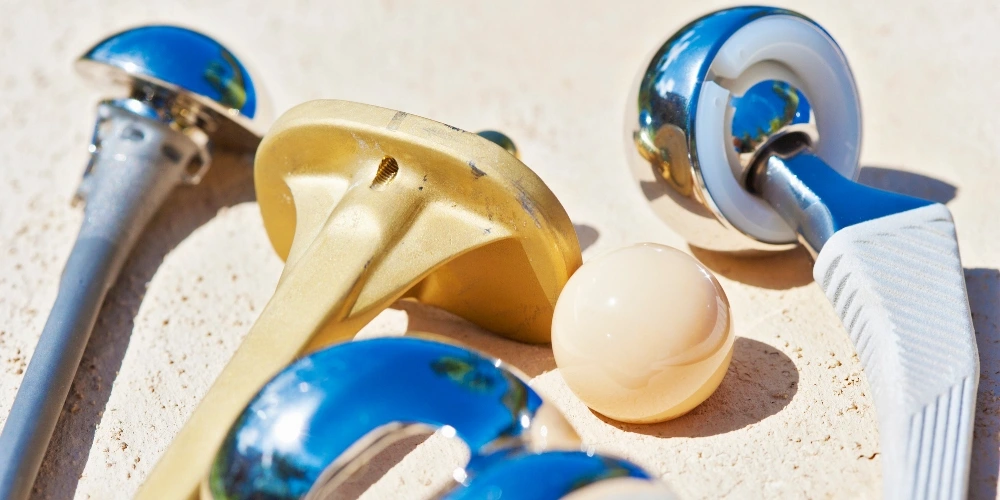
Titanium Grades for CNC Machining
- Grade 1 (Ti-CP):Commercially Pure Titanium with excellent corrosion resistance, ideal for applications requiring cold forming.
- Grade 2 (Ti-CP):Similar to Grade 1, featuring excellent corrosion resistance; widely utilized in chemical processing and marine applications.
- Grade 5 (Ti-6Al-4V):Alloyed with aluminum and vanadium, offering high strength and exceptional corrosion resistance, commonly used in aerospace and medical applications.
- Grade 7 (Ti-0.2Pd):Alloyed with palladium, provides excellent corrosion resistance, especially in reducing environments, making it suitable for chemical and marine applications.
- Grade 9 (Ti-3Al-2.5V):Alloyed with aluminum and vanadium, offers good weldability and formability, with enhanced corrosion resistance compared to Grade 5; suitable for applications requiring high strength and moderate weight.
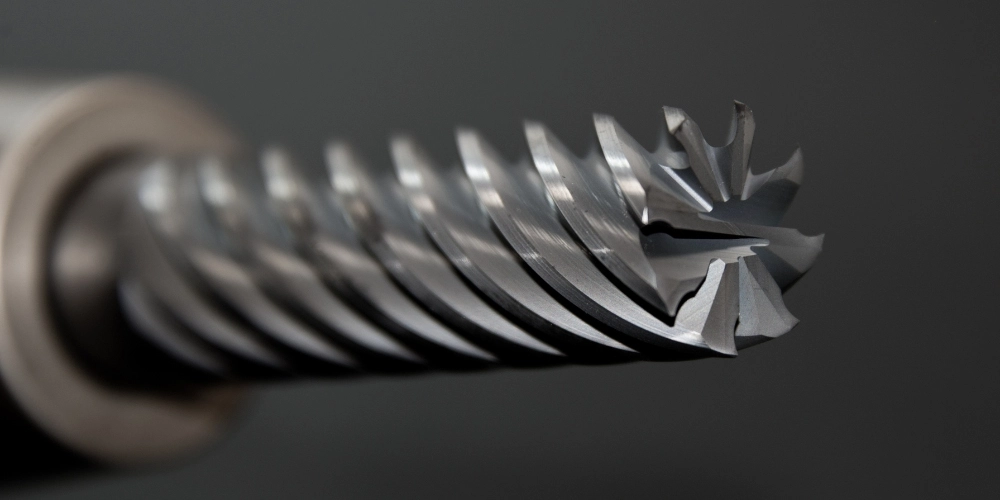
The Advantages of Producing Titanium Parts Using CNC Technology
Harnessing CNC technology for the production of titanium components yields significant merits. Paramount in this process is the meticulous interplay of precision and accuracy, where CNC machines consistently navigate stringent tolerances. The pliancy inherent in CNC machining facilitates the crafting of intricate geometries, systematically extracting material to optimize utilization, curtail wastage, and amplify overall cost-effectiveness, particularly in scenarios involving medium to high production volumes.
Moreover, the automated procedural framework guarantees reproducibility, mitigating the potential for human errors and furnishing a dependable avenue for the generation of identical titanium components. The amalgamation of CNC technology with CAD/CAM systems further refines the manufacturing trajectory, positioning it as the favored approach for the efficient realization of bespoke, high-quality titanium parts, coupled with diminished turnaround times.
CNC Technologies Suitable for Producing Titanium Parts
A myriad of CNC technologies demonstrate unparalleled prowess in the fabrication of intricate and efficient titanium components. Multi-axis CNC Machining confers meticulous control over intricate geometries, while High-Speed CNC Machining expeditiously curtails production times. Wire EDM, leveraging electrical discharges, ensures meticulous precision. The adept craftsmanship of CNC Turning is evident in its efficient production of cylindrical components, while Waterjet Cutting proves versatile in its ability to deftly handle sheet and plate cutting tasks. The augmentation of capabilities is palpable in Abrasive Waterjet Machining. Lastly, CNC Milling stands as the vanguard of widespread precision. Manufacturers astutely amalgamate these technologies to achieve optimal outcomes, navigating the nuances of part complexity, volume considerations, and requisite tolerances with finesse.
Challenges in CNC Titanium Parts Production
CNC titanium part fabrication presents distinctive hurdles owing to the formidable hardness of the material, necessitating the application of specialized tools and methodologies to counteract wear and uphold precision. Delving into the intricacies, the management of heat generation and the implementation of efficient cooling systems stand as pivotal considerations, indispensable for averting thermal distortion. Moreover, the escalation in costs due to abrasive tool wear in titanium underscores the imperative to strike a judicious balance between durability and cost-effectiveness.
Furthermore, the exorbitant material cost of titanium propels the need for an intricate equilibrium between its utilization and economic viability. Confronting the challenge of achieving desired surface finishes in titanium components demands meticulous planning of toolpaths. Manufacturers find themselves in a perpetual process of refinement, continuously augmenting their comprehension of material characteristics and deploying advanced methodologies to adeptly navigate these challenges. The ultimate goal remains steadfast — ensuring the meticulous production of superior-quality titanium components.
Surface Finishes for CNC Titanium Parts
CNC titanium components present a myriad of surface finish possibilities, addressing both aesthetic and functional requisites. Diverse alternatives encompass the refined Polished Finish, the textured Brushed Finish, the uniformly matte Bead-Blasted Finish, the chromatically varied Anodized Finish, and the smoothly subtle Satin Finish. The discerning choice among these relies on multifaceted considerations, encompassing application nuances, intricate design elements, and the nuanced interplay between aesthetic allure and utilitarian purposes. This discretion enables manufacturers to intricately harmonize surface finishes with the precise demands of distinct end-use scenarios.
A Guide for Customize Titanium Parts


- Specification of Requirements:
- Clearly delineate dimensions, tolerances, material grade, and requisite features.
- Design Articulation :
- Express design intent through intricate drawings or immersive 3D models.
- Material Selection :
- Discern the apt titanium grade with sagacious guidance from manufacturers.
- Surface Finish :
- Clearly articulate the desired surface finish, balancing aesthetic allure and functional requisites.
- Precision Guidelines :
- Unambiguously enunciate the required tolerances and precision levels.
- Batch Size and Volume Determination :
- Discern judiciously the batch size and production volume.
- Quality Assurance :
- Establish testing standards and quality certifications.
- Lead Time and Delivery :
- Engage in dialogue regarding production lead times and delivery schedules.
- Cost Consideration :
- Deliberate on cost factors, encompassing materials and machining expenses.
- Collaboration :
- Foster open collaboration with the manufacturing team, fostering a symbiotic partnership.
- Prototyping for Complex Designs :
- Delve into iterative prototyping, particularly for intricate and convoluted designs.
- Thorough Review and Approval Process :
- Institute a comprehensive review process culminating in final approval before mass production initiation.
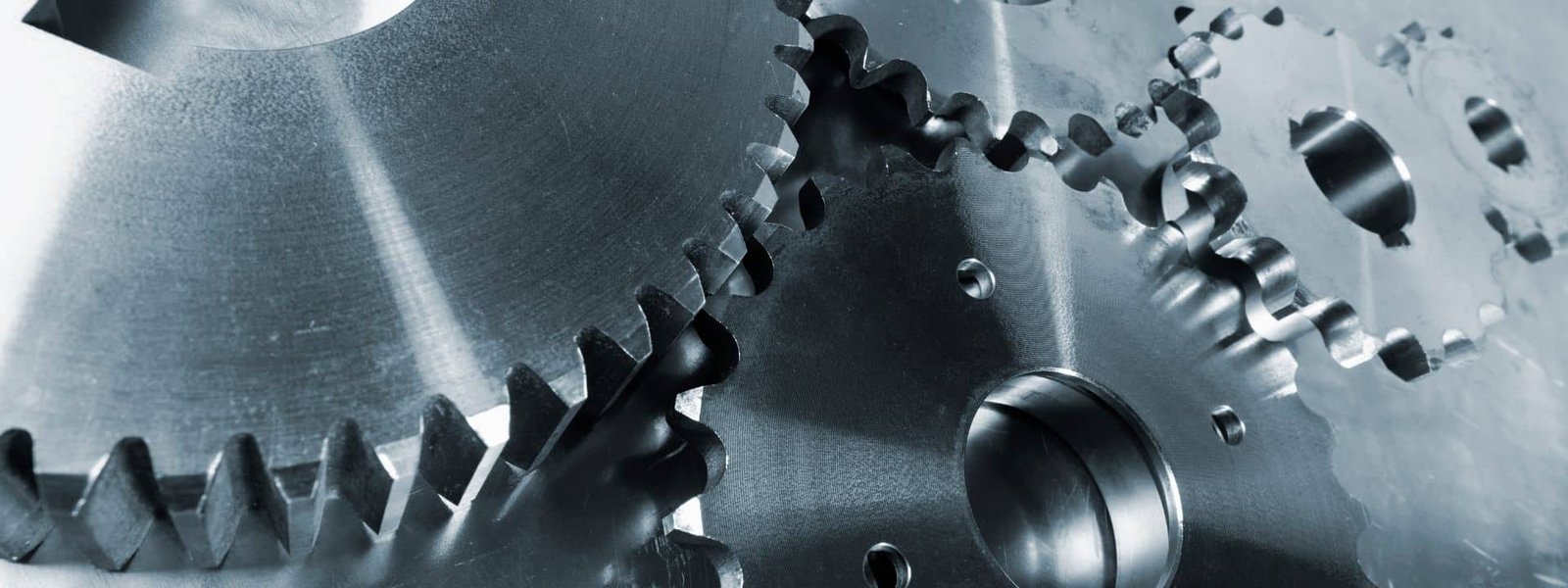
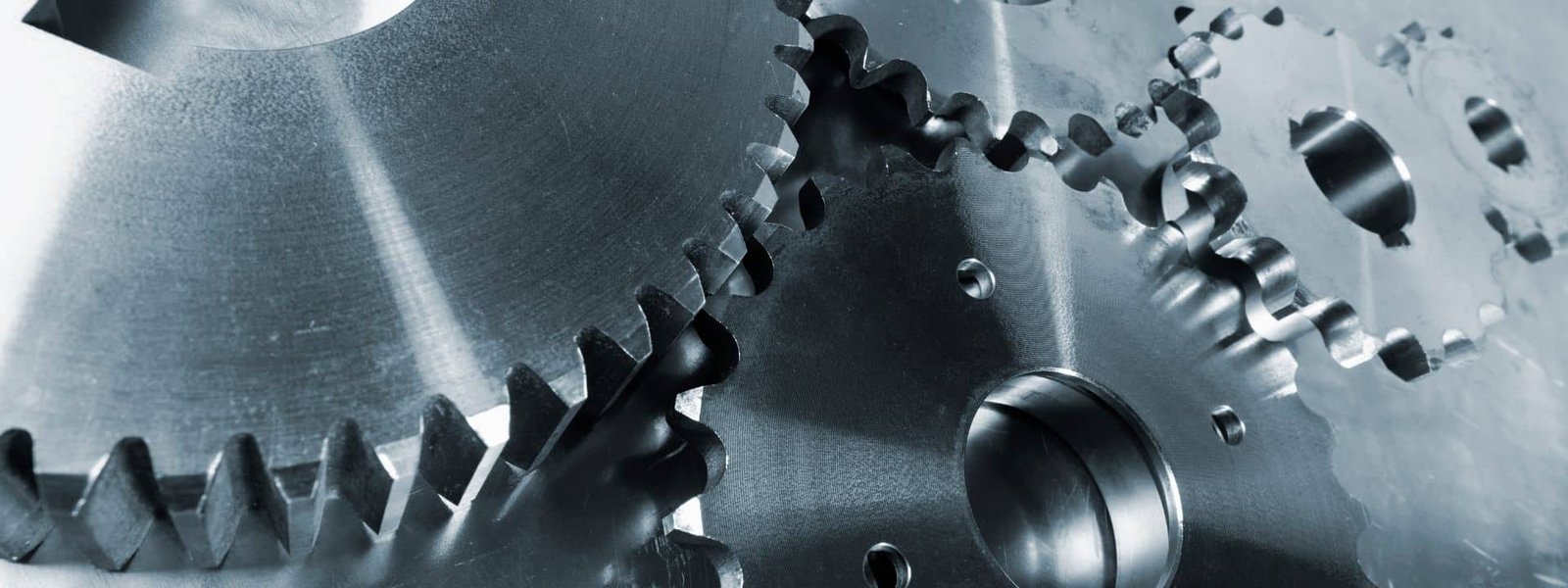
Conclusion
As we conclude, this exploration highlights the pivotal role of CNC titanium machining in shaping industries. The synergy of strength, precision, and innovation defines a future where customized titanium components meet unique requirements with unparalleled efficiency.
Resources: