Mastering Precision with Stainless Steel CNC Machining
Embark on our exploration of Precision Alloy CNC Fabrication Services, where the fusion of exactitude and ingenuity takes center stage. This comprehensive compendium demystifies the intricacies inherent in the realm of machining stainless steel, employing avant-garde CNC technology. Whether you traverse the terrain of expertise or are an initiate seeking enlightenment into the nuances of customization, this invaluable reservoir has your queries addressed.
Can Stainless Steel Be CNC Machined?
Yes, stainless steel is a material that is highly machinable, in fact, it is considered one of the best and most used types of metal because of its high versatility, ductility, and resistance. They’re already great when it comes to standard or regular manufacturing – what more if it’s CNC machined?
Types of CNC Technologies Can Be Used for Machining Stainless Steel
Machining stainless steel presents a formidable challenge due to its unyielding nature, resilience, and inclination to undergo work hardening. Nonetheless, a variety of Computer Numerical Control (CNC) technologies exhibit prowess in the art of stainless steel machining. The following elucidates some prevalent CNC manufacturing processes applied in the machining of stainless steel:
- CNC Milling: By employing elevated spindle velocities and expeditious feed rates, efficient material removal is achieved. High-Speed Machining (HSM) proves effective for stainless steel when coupled with suitable cutting tools and cooling methodologies.
- CNC Turning: Considered as one of the most common CNC machining processes, CNC turning is a process that’s used to make cylindrical parts that are off to extremely high levels of precision. This reduces the overall diameter of the workpiece to a specified measurement and dimension.
- EDM (Electrical Discharge Machining): Well-suited for intricate and pinpoint cuts in stainless steel, it utilizes a slender, electrically charged wire to erode material, ensuring heightened precision.
- Laser Cutting: Proficient in slicing through thin to thick stainless steel sheets with precision. Fiber lasers are renowned for their speed and accuracy.
- CNC Sheet Metal Punching: Punching is a manufacturing procedure that’s done to bore holes and reform/reshape sheet metal or workpiece. Don’t confuse yourself in understanding CNC sheet metal punching because it’s just the same as regular or standard punching – it’s just the way how the processing took place.
- CNC Sheet Metal Folding: Last in this list is metal folding. Sheet metal folding is typically a finishing or polishing procedure that is done by bending or folding sheet metal. These folds will be reduced to a few millimetres across the entire plain of workpiece.
- Grinding: Imparts a refined surface finish and stringent tolerances to stainless steel surfaces. Frequently enlisted for terminal machining procedures.
These are the most typical CNC machining processes done to stainless steel workpieces and materials.
NOTE: Just because these are the most common processes and methods done for stainless steel doesn’t mean that your actions and processes are limited to these. There are other CNC manufacturing and machining processes for stainless steel, but these are just the most common.
In the course of machining stainless steel, the judicious selection of cutting tools, toolpath methodologies, and cutting parameters assumes paramount significance. Furthermore, the implementation of appropriate cooling and lubrication techniques proves instrumental in managing the thermal flux generated during the machining progression. It is imperative to consistently adhere to the guidelines and exemplary practices stipulated by the manufacturer when employing CNC technologies for machining stainless steel.
Advantages of Using CNC Technology for Machining Stainless Steel Parts
Engaging Computer Numerical Control (CNC) technology in the fabrication of stainless steel components presents a paradigm shift in manufacturing. The precision excellence inherent in CNC, propelled by automated algorithms and stringent tolerances, amplifies the overall caliber of the end product. This integration also ushers in heightened operational efficiency, where automated procedures, rapid tool transitions, and refined toolpaths collaboratively curtail production timelines, fostering heightened productivity.
Moreover, CNC machining distinguishes itself in the realms of adaptability and intricacy, accommodating an array of elaborate designs for stainless steel components. The technology, through automation, secures unwavering quality by minimizing deviations in the final output—particularly critical in sectors demanding standardized components. In synopsis, CNC technology instigates a manufacturing revolution by seamlessly intertwining precision, efficiency, versatility, and steadfast quality into the production tapestry of stainless steel parts.
Challenges May Arise When Using CNC Machining for Stainless Steel
Navigating CNC machining for stainless steel introduces formidable hurdles such as tool wear stemming from the material’s unyielding nature, heat generation impacting the longevity of tools, and the imperative for effective chip control. Ensuring steadfast workpiece fixturing emerges as a critical necessity to quell vibrations, while orchestrating intricate programming becomes indispensable for the fabrication of complex components. Furthermore, the expenditure associated with stainless steel, coupled with the intricacies of achieving desired surface finishes and preserving corrosion resistance, introduces nuanced considerations for achieving machining precision and efficiency. Confronting these challenges necessitates a confluence of expertise, methodical planning, and the adept utilization of tailored tools and methodologies.
Types of Stainless Steel Suitable for CNC Machining
- 303 Stainless Steel(SUS303): Acclaimed for its notable machinability.
- 304 Stainless Steel(SUS304): Universally employed, showcasing commendable machinability, corrosion resistance, and weldability.
- 316 Stainless Steel(SUS316L): Manifesting exceptional corrosion resistance, well-suited for rigorous environments.
- 17-4 PH Stainless Steel: Possessing heightened strength, corrosion resilience, and favorable machinability.
- 416 Stainless Steel(SUS416): Exhibiting enhanced machinability, particularly apt for intricate geometries.
- 420 Stainless Steel(SUS420): Displaying heightened hardness and corrosion resistance, notably suitable for wear-resistant components.
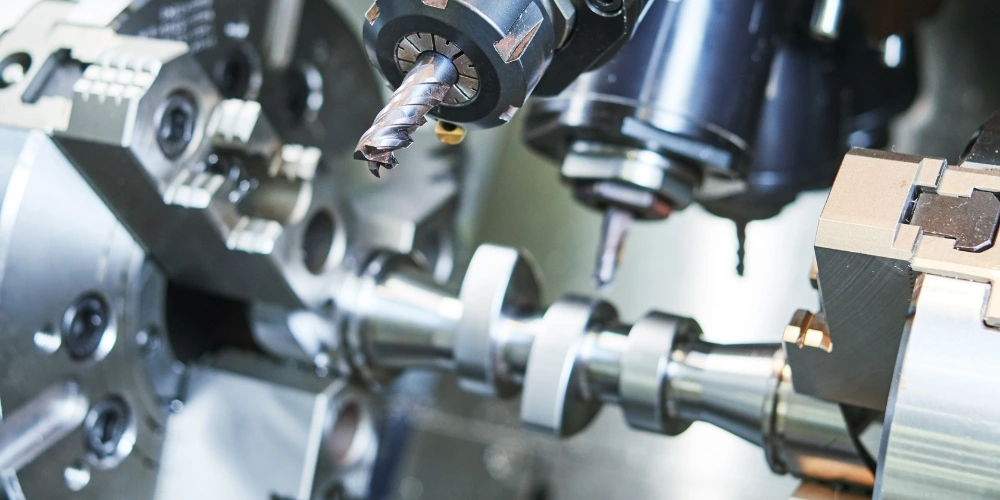
SUS303 vs. SUS304 Stainless Steels
SUS303 and 304 are two (2) of the most common types of stainless steel types that are used for CNC machining. Here are a few of the differences between these grades:
Durability
SUS304 is a type of austenitic stainless steel that is non-magnetic, which calls for lower electrical and thermal conductivity. It’s also exceptionally tough and corrosion resistant.
Usability
SUS303 is one of the few types of stainless steel that is easy and convenient to use because of its free-cutting capability. On the contrary, SUS303 is considered not weldable and less susceptible to machining. SUS304 is a stainless steel type that is weldable; it’s also the best and ideal stainless steel type for machining. It does not harden with heat treatment – it is not a free-cutting material.
Cost
Last and most definitely not least would be the cost and price of these types. The regular costs change every now and then, so, you can’t be too sure which one is cheaper and more affordable. Generally speaking, SUS304 is cheaper in comparison to its properties against SUS303.
These are the primary differences between SUS303 and SUS304 in stainless steel machining.
NOTE: SUS and SS are the same – SUS is just the Japanese variation (Japanese Industrial Standards or JIS) while SS is the American way of listing it.
Types of Stainless Steel Parts Suitable for CNC Technology
- Gutters
- Nuts & Bolts
- Fasteners
- Kitchen Appliances
- Automotive, Motorcycle, and Aerospace Parts
- Surgical Instruments
- Pressure Vessel
- Precision components like gears,
- Complex geometries such as turbine blades,
- Medical components like surgical instruments,
- Aerospace parts
- Automotive components
- Electronic components
- Tool and die components
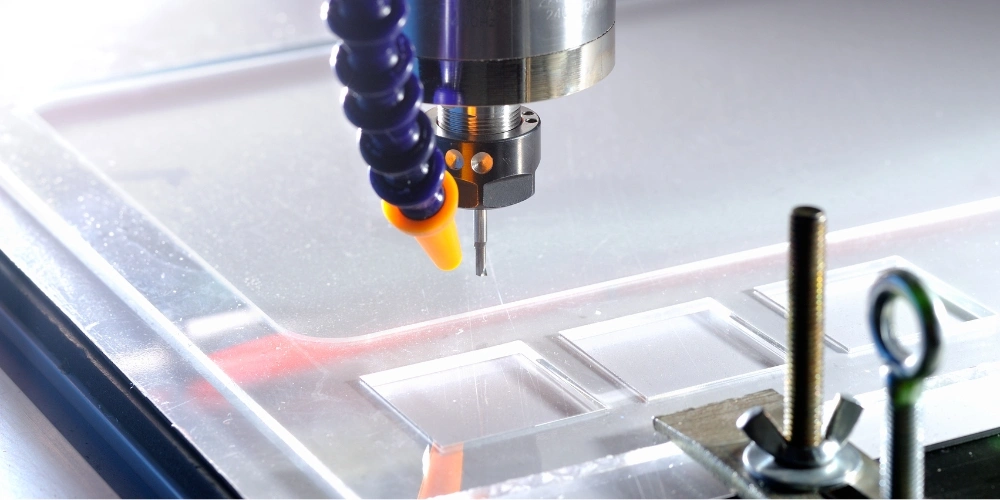
Factors Should Be Considered When Customizing CNC Stainless Steel Parts
- Material Grade: Opt for the apt stainless steel classification contingent on sought-after attributes like resistance to corrosion and hardness.
- Design Complexity: Scrutinize the intricacy of the component’s design to ascertain CNC machining’s efficacy in achieving the desired forms.
- Precision and Tolerances: Articulate with precision the requisite tolerances and exactitude levels for the meticulous manufacturing of the component.
- Surface Finish Requirements: Clearly outline the necessary surface finish, contemplating the spectrum achievable through CNC machining.
- Batch Size: Ascertain the volume of components required, striking a balance between cost-effectiveness for both diminutive and extensive production series.
- Tooling and Fixturing: Meticulously opt for cutting implements and fixturing methods for a streamlined and accurate machining process, factoring in tool compositions and coatings.
- Cost Considerations: Rigorously assess the overall customization costs, encompassing material expenses, machining duration, and any supplementary processes or embellishments.
- Lead Time: Delve into the temporal dynamics of production, integrating machining and any subsequent procedures into the overarching timeline.
- Quality Assurance: Enforce stringent quality control measures, entailing meticulous inspections and testing protocols, to uphold the specified benchmarks.
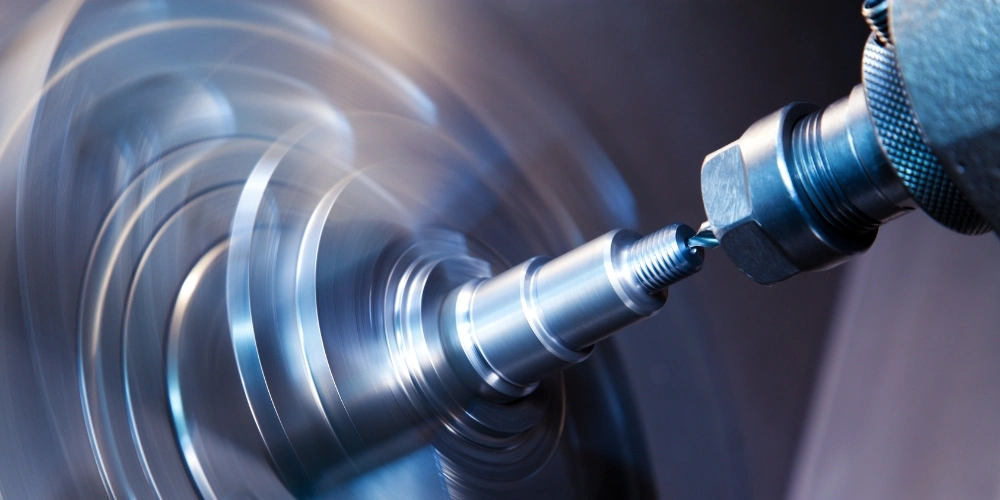
How to Custom Stainless Steel CNC Machining Parts?
Custom ordering stainless steel CNC machining parts involves a straightforward process. Firstly, clearly define the specifications, including material grade and dimensions. Following this, identify reputable manufacturers with specialized expertise in stainless steel CNC machining. Reach out to these manufacturers, providing them with detailed requirements and requesting quotations.
Collaborate with the chosen manufacturer to select the appropriate stainless steel grade and optimize the design for efficient CNC machining. Clearly communicate the required tolerances and surface finish expectations. During discussions, address batch size considerations, confirm production quantities, and establish lead times for timely delivery.
Inquire about the manufacturer’s quality control measures and testing processes to ensure the final parts meet your specified standards. Maintain open communication throughout the process, promptly addressing any concerns that may arise. Finally, review the quotations, confirm all details, and finalize the order with the chosen manufacturer. This streamlined approach ensures an efficient and successful custom order for stainless steel CNC machining parts.
CNC Machining Stainless Steel Materials Supplier You Can Trust
Out of the many manufacturers and suppliers you can trust when it comes to CNC machining stainless steels, HDC Manufacturing is the best you can get! You’ll never be able to find another supplier or manufacturer as talented and experienced as us!
For 12+ years, we have produced a vast library of stainless steel materials, parts, and components via CNC machining. We were able to manufacture many different types and kinds of materials and parts using a whole wide range of stainless steel types and kinds!
If you need CNC machining stainless steel automotive, motorcycle, aerospace, industrial, or any other type of industry that heeds stainless steel materials, you can count and bank on us!
Aside from CNC machining stainless steel materials, we here at HDC Manufacturing are also experts and professionals when it comes to CNC rapid prototyping, laser cutting services, metal stamping services, 5-axis CNC machining services, and many more!
Reach out to us and we’ll be more than happy to send a free quotation over!
Conclusion
In wrapping up our exploration, the fusion of technology and metallurgy showcased in CNC machining for stainless steel emerges as a game-changer. Despite challenges, the rewards of durable, high-performance parts make the journey worthwhile. This FAQ guide serves as your beacon, empowering you to navigate the complexities and embrace a future where precision and reliability seamlessly converge.
Resources: